Thermal cutting in metalworking
By Staff Report | August 16, 2024 2:12 pm SHARE
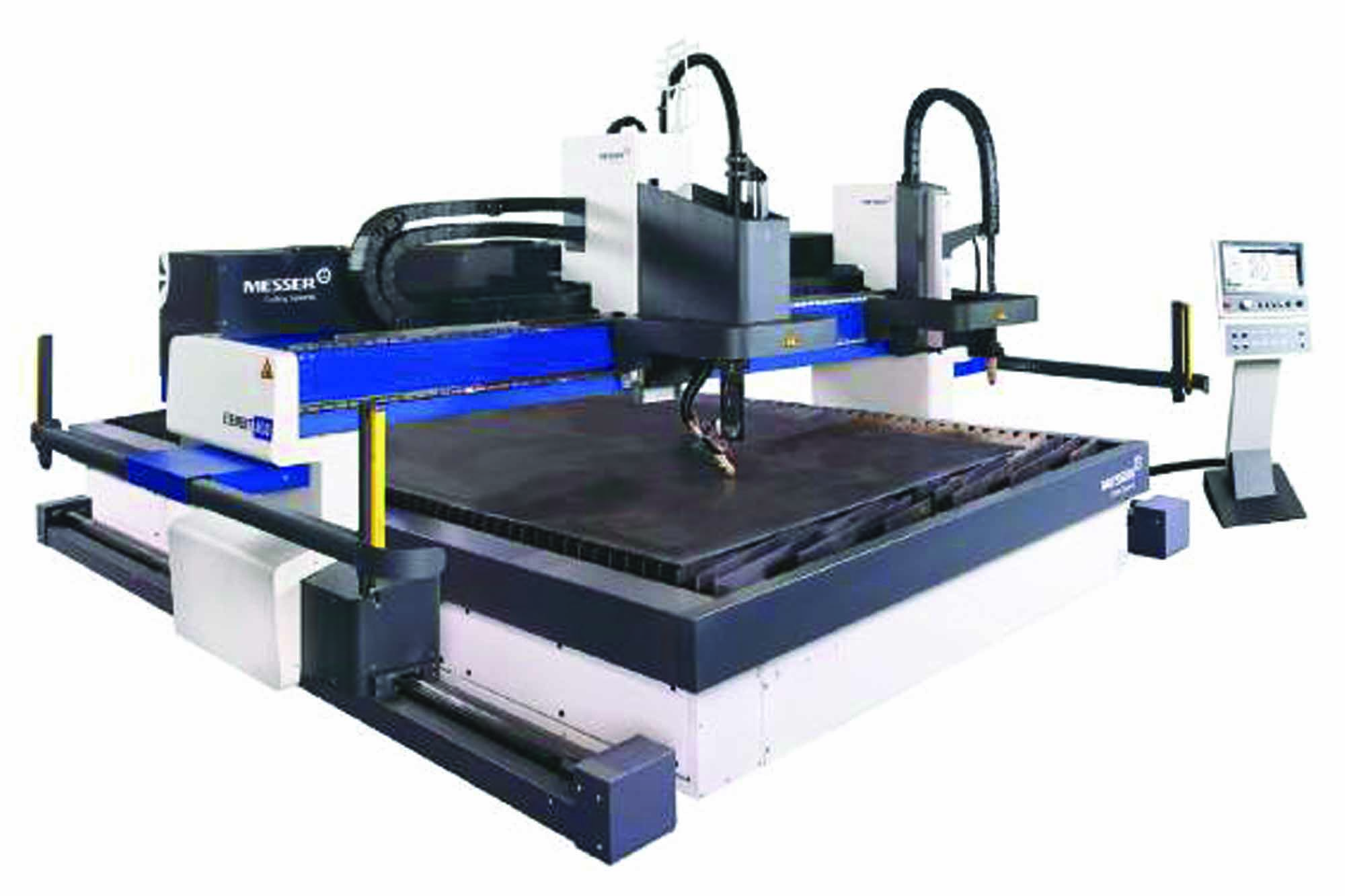
In the fast-paced world of metal production, thermal cutting stands out as a critical process, enabling industries to sculpt materials with unparalleled precision. This article explores the various cutting techniques, the role of energy carriers, and the importance of bevel cutting, highlighting how each step contributes to the final product’s quality and durability.
Thermal cutting is a vital production process within the metal production and metalworking sectors, covering areas such as structural engineering, machine fabrication, energy equipment manufacturing, shipbuilding, and plant manufacturing. Essentially, this process harnesses energy in various forms to shape a wide range of ferrous and non-ferrous materials, whether sheets or hefty slabs. These materials, commonly called “Flats” in the metal processing realm, encompass different grades. Conversely, other metal types like angles, channels, beams, pipes, and rods are collectively known as “Longs.”
Classification of thermal cutting processes
Thermal cutting can be classified based on several criteria. First, material type and thickness play a crucial role, as the choice of thermal cutting process depends primarily on whether the material is ferrous or non-ferrous and its thickness. Precision is another critical factor, as each thermal cutting process maintains specific tolerances related to basic process fundamentals, quality, and dimensional accuracy. Quality attributes such as perpendicularity, angularity tolerances, and permissible roughness depth are defined for different cutting methods. The physics of the cutting process and material effects are also significant, with cutting processes categorised by their underlying physics, such as burning via oxidation, melting, and vaporization (sublimation). The process selection influences material type, tolerances, and the chemical and physical reactions post-cutting.
The type of production also affects the selection process, ranging from manual tools to fully automated systems across various industries. Production volume and location—on-site, enclosed areas, or typical factory settings—are critical considerations. Desired post-cutting operations also influence the choice, as thermally cut parts often undergo fitting, welding, grinding, bending, or heat treatment after cutting. The energy carrier used in the process, such as hot gases, electric gas discharge, or light beams, directly impacts the physical and mechanical properties of the cut parts. Finally, considering factors like mechanical stress, chemical reactions, and fatigue, applying the cut part determines the appropriate thermal cutting process based on the intended use.
Primary thermal cutting technologies
Plates can be cut through three primary processes: oxyfuel, plasma, and laser. Each technology allows plates to be cut straight or with a bevel.
Bevel cutting is essential in fabrication units for several reasons. Proper edge preparation for welding is crucial for achieving high-quality results, maintaining productivity, and minimising costs associated with rework and downtime. Preparing metal for welding typically involves cutting and beveling the base material, and the level of care and preparation invested in the initial cut can significantly reduce the need for extensive post-processing later on. Various tools can be used for edge preparation, including torches, plasma cutters, shears, manual tools like wheels, and mechanical bevel cutters. However, each edge preparation method has its own advantages and disadvantages. Ensuring proper metal preparation for welding is essential for consistently producing high-quality results, maintaining productivity, and minimising costs.
In industrial settings, bevel cutting is required in various sectors and applications where precise and angled cuts are necessary for welding or joining metal components. Common industries and applications include structural steel fabrication, shipbuilding, automotive manufacturing, aerospace, oil and gas, heavy equipment manufacturing, power generation, and metalworking and fabrication shops. Bevel cutting is essential wherever precise and angled cuts are required to facilitate these diverse industries’ welding, assembly, and fabrication processes.
Messer’s role in plate cutting
Messer plays a significant role in plate cutting by offering comprehensive solutions tailored to the diverse needs of industries ranging from automotive and aerospace to construction and energy. Their cutting-edge technologies and equipment ensure precision, efficiency, and cost-effectiveness in plate-cutting processes. Messer’s offerings include oxyfuel cutting systems for thick carbon steel plates, plasma cutting systems for a wide range of materials, fibre laser cutting systems for unmatched precision, and hybrid cutting solutions that combine multiple technologies to maximise efficiency and versatility. Messer’s plate-cutting solutions are designed for seamless integration into automated production environments, enabling increased productivity, reduced labour costs, and improved workflow efficiency. Their range of bevel tools, from manual to automated, ensures that all preparatory work is completed efficiently, enhancing the overall cutting process.
Overall, Messer’s plate-cutting solutions provide industry-leading performance, reliability, and versatility, empowering manufacturers to achieve superior cutting results while optimising their production processes.
Why is bevel cutting necessary in fabrication units?
Proper edge preparation for welding is crucial in any application for achieving high-quality results, maintaining productivity, and minimising costs associated with rework and downtime. Preparing metal for welding typically involves cutting and beveling the base material. The level of care and preparation invested in the initial cut can significantly reduce the need for extensive post-processing later on. Various tools can be used for edge preparation, including torches, plasma cutters, shears, manual tools like wheels, and mechanical bevel cutters. However, each edge preparation method comes with its own advantages and disadvantages.
Ensuring proper metal preparation for welding is essential for consistently producing high-quality results, maintaining productivity, and minimising costs.
For instance, cutting with a right-angle grinder is cost-effective, portable, and requires minimal setup and maintenance compared to other options. However, achieving clean, straight cuts with this method demands significant practice and skill. Therefore, making the initial cut as clean, straight, and consistent as possible facilitates the production of quality results.
A clean and consistent gap between the two pieces to be welded results in a stronger and more consistent weld, requiring less filler metal. This not only reduces costs but also saves time in the welding process.
Where is bevel cutting required?
Industrial bevel cutting is required in various sectors and applications where precise and angled cuts are necessary for welding or joining metal components. Some common industries and applications where industrial bevel cutting is essential include:
Structural Steel Fabrication: Bevel cutting is crucial for preparing structural steel components such as beams, columns, and plates for welding in construction projects.
Shipbuilding: Shipbuilding requires precise bevel cutting of metal plates and sections to ensure proper fit-up and welding of hulls, decks, and other structural components.
Automotive Manufacturing: Bevel cutting fabricates automotive frames, chassis, and body panels, ensuring accurate assembly and welding of vehicle structures.
Aerospace Industry: Aerospace applications require bevel cutting to fabricate aircraft components such as fuselages, wings, and engine parts to meet strict performance and safety standards.
Oil and Gas Sector: Bevel cutting is essential for preparing pipes, valves, and other components used in oil and gas pipelines, refineries, and processing plants.
Heavy Equipment Manufacturing: Industrial machinery and equipment manufacturers use bevel cutting to fabricate components such as frames, booms, and brackets, ensuring precise assembly and structural integrity.
Power Generation: Bevel cutting is employed to fabricate components for power plants, including turbine blades, boiler parts, and heat exchangers, to ensure efficient operation and reliability.
Metalworking and Fabrication Shops: Bevel cutting is commonly used in metalworking and fabrication shops for various applications, including custom fabrication projects, repair work, and prototype development.
Overall, industrial bevel cutting is essential wherever precise and angled cuts are required to facilitate welding, assembly, and fabrication processes in diverse industries and applications.
Messer’s Role in Plate Cutting:
Messer offers comprehensive plate-cutting solutions tailored to the diverse needs of industries ranging from automotive and aerospace to construction and energy. Their cutting-edge technologies and equipment ensure precision, efficiency, and cost-effectiveness in plate-cutting processes. Here’s an overview of Messer’s plate-cutting solutions:
Oxyfuel Cutting: Messer’s oxyfuel cutting systems provide robust and reliable cutting solutions for thick carbon steel plates. Oxyfuel cutting achieves high-quality cuts with minimal dross and excellent edge squareness using oxygen and fuel gas, such as acetylene or propane.
Plasma Cutting: Messer’s plasma cutting systems utilise advanced plasma technology to cut a wide range of materials, including carbon steel, stainless steel, aluminium, and non-ferrous metals. With high cutting speeds, precision, and versatility, Messer’s plasma cutting solutions are ideal for various applications, from thin gauge to thick plate cutting.
Fibre Laser Cutting: Messer’s fibre laser cutting systems deliver exceptional speed, accuracy, and flexibility for cutting various materials with unmatched precision. With fibre laser technology, Messer’s cutting solutions offer superior edge quality, minimal heat-affected zones, and reduced operating costs compared to traditional cutting methods.
Combination Cutting: Messer offers hybrid cutting solutions that combine oxyfuel, plasma, and fibre laser technologies to maximise cutting efficiency and versatility. These integrated systems allow users to optimise cutting processes for different material types, thicknesses, and applications, achieving optimal results with minimal setup time and material waste.
Automation and Integration: Messer’s plate-cutting solutions are designed for seamless integration into automated production environments, enabling increased productivity, reduced labour costs, and improved workflow efficiency. From robotic cutting systems to advanced software solutions, Messer offers a range of automation options to streamline plate-cutting operations and maximise throughput.
Bevel solutions: Messer has a range of bevel tools, from manually positioned tools for simple beveling to automated bevel tools in oxyfuel, plasma, and Laser processes for complicated contour beveling and to produce all preparatory work in next to no time.
Overall, Messer’s plate-cutting solutions provide industry-leading performance, reliability, and versatility, empowering manufacturers to achieve superior cutting results while optimising their production processes.
For more information, visit: https://in.messer-cutting.com/
Cookie Consent
We use cookies to personalize your experience. By continuing to visit this website you agree to our Terms & Conditions, Privacy Policy and Cookie Policy.