Time for a change
By Edit Team | July 28, 2015 11:53 am SHARE
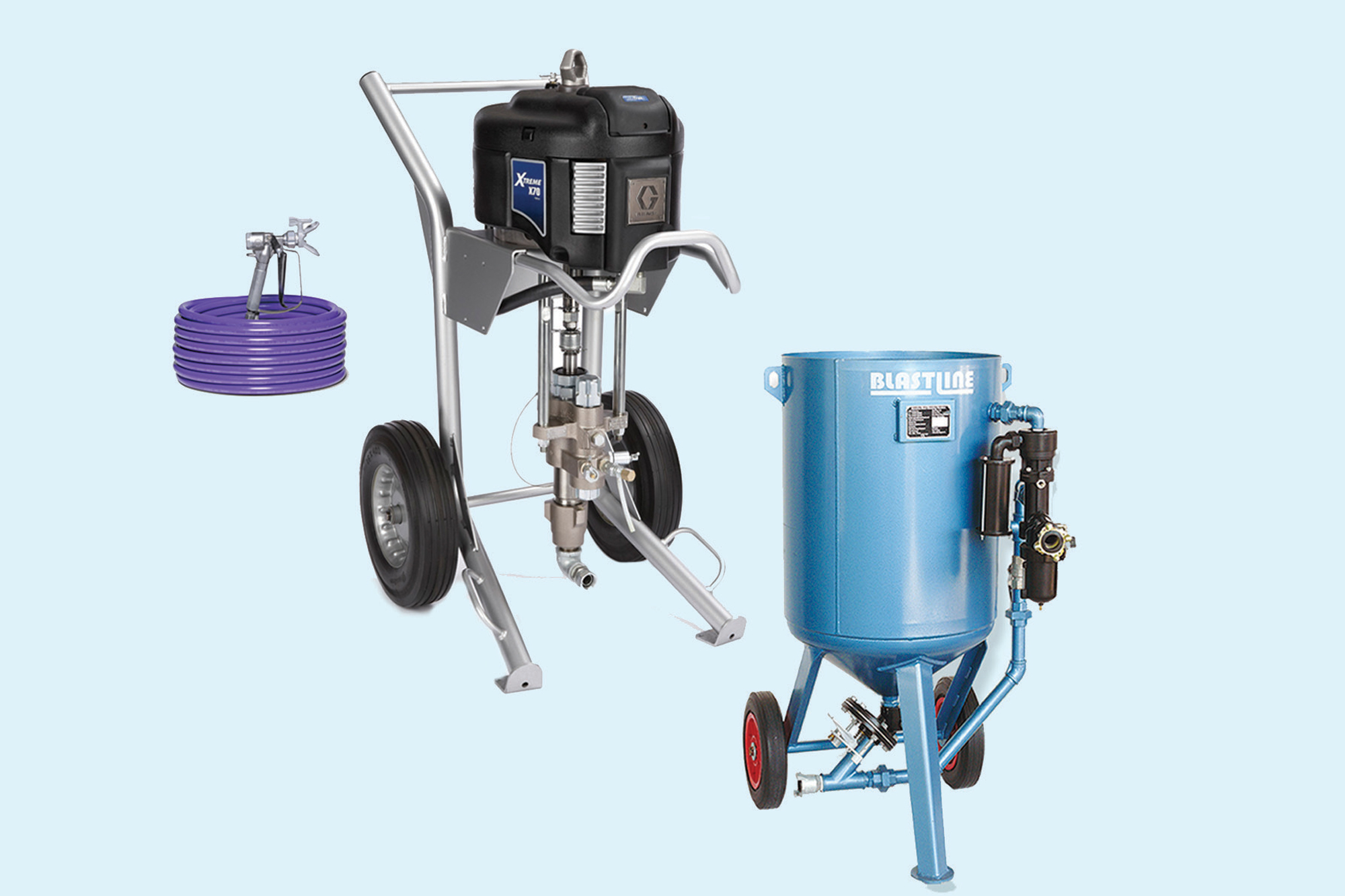
Jolly Lonappan, Managing Director, Blastline India explains why it is required to phase out ‘cheap’ blasting equipment and adopt the ‘efficient’ one
Abrasive blast cleaning equipment available in India may be broadly classified into two major categories:
• Air or dry blasting type used for open blasting applications
• Airless or wheel blasting type used for blasting in controlled environments.
The former type is simple, low cost equipment that is trouble free, portable and versatile. It uses compressed air as the propelling media for the blasting grit delivery. The first of its kind was made by a company called “Clemco” located in San Francisco Bay, USA. Over a period of time this basic machine evolved with modifications and innovations to its present form. Now it is being made by many manufacturers. One good thing is that the basic design is more or less the same and therefore many parts of these machines are interchangeable or compatible irrespective of the brand or make.
Earlier, not many industrial coating contractors in India were conscious about quality nor there were serious manufacturers catering to this industry. Till recent times, blast machine manufactures were typically run-of-the-mill welding workshops that produced low cost blast machines with no concern for quality or safety standards whatsoever.
Actually a good amount of science need to be applied behind design and production of these machines to ensure one strikes the right balance to achieve the best productivity, lowest machine down-time, availability of spare parts, safety features and cost effective pricing. Moreover, these need to be quality tested based on well defined specifications including ability to withstand very high pressures and ability to satisfy various other safety parameters based on international norms.
Also, the end-user had to be provided with proper training, a clear instruction manual, and suitably sized machines to match his requirement and business model. The productivity and machine up-time is proportional to the quality of the equipment, abrasives used and the operator. Every penny spent on equipment should be paid back 100-fold in production by a reliable machine.
Blastline India, in collaboration with Blastline of UK, manufactures such high quality blast machines in India. Blastline India’s manufacturing process meets international standards and its machines come with a pressure test certificate, instruction manual, free operator training, detailed drawings and spare parts list supported by prompt after-sales service. Machines of different sizes are available with various capacities like 300, 200, 100, 50 or 25 litres blast pots. Its machines are currently available in India, Far East and the Middle East.
Growth drivers
The major growth driver of this industry is population. The people are the market. Where there are more people there will be more opportunities. The large population in India coupled with the developing stage of the country makes it a gold mine for the manufactures. The other growth drivers are India’s vast coastal areas and the heavy monsoon rains that appear every year without fail. The saline and moist environment is an ideal catalyst for very high corrosion rates. The most efficient method to protect steel from corrosion is by coating. All coatings need surface preparation and hence the blast machines for surface cleaning and profiling is a necessity that should be in high demand. Further, the “Make in India” campaign should attract many new entrepreneurs into this field.
Demand-supply scenario
At present, 60 per cent of machines in the market are supplied by the unorganised sector where a welding work shop becomes a manufacturer who is least bothered about quality or safety standards. But, such products should get phased out as competitively priced machines start rolling out to every contractor, who hopefully will realise the effect of good equipment and its productivity on his bottom-lines in terms of blasting efficiency, down-time and safety.
Authored by__
Jolly Lonappan,
Managing Director,
Blastline India Pvt. Ltd.
Cookie Consent
We use cookies to personalize your experience. By continuing to visit this website you agree to our Terms & Conditions, Privacy Policy and Cookie Policy.