TMT bars dominating construction projects
By Staff Report | September 12, 2024 1:57 pm SHARE
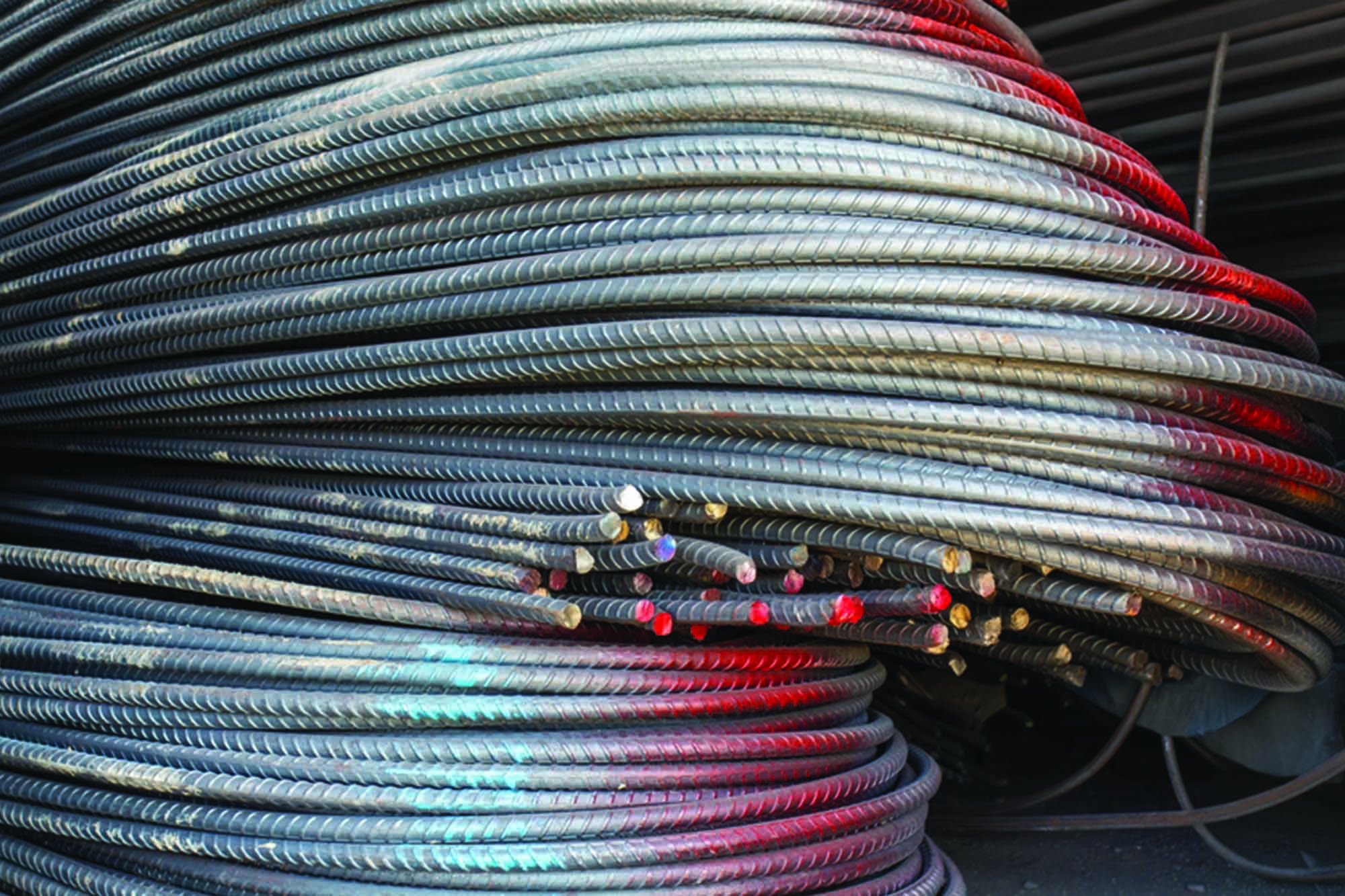
The demand for TMT bars is soaring, reaching new heights, with trends such as eco-friendly practices and the incorporation of micro-alloying elements leading the way. This article provides an overview of the booming TMT market in India and explores the promising opportunities it presents for construction professionals.
Choosing premium TMT bars is essential for guaranteeing the durability and strength of any project, be it residential or commercial construction. Given the varied climate and difficult topography, it is imperative to select TMT bars that can withstand the test of time to protect investment for years to come.
TMT bars offer additional safety and stability in regions prone to seismic activity or extreme weather conditions. Their superior ductility allows them to absorb and dissipate seismic energy, reducing the risk of structural failure during earthquakes. Additionally, their resistance to corrosion and high-temperature performance ensures that structures remain robust and reliable under challenging environmental conditions.
The need for TMT bars in India is growing due to private sector investments and the government’s emphasis on building high-quality earthquake-resistant structures. As the best option for reinforcing concrete structures, TMT bars are renowned for their exceptional strength and longevity. Beyond maintaining structural integrity, they improve safety, offer superior corrosion resistance, remarkable ductility and elongation, and are reasonably priced and dependable over the long run.
Market trends
The consumption of TMT bars in India saw a notable rise, with 50.3 million tonnes (MT) used in FY23 compared to 46 MT in the previous fiscal year. This growth is attributed to increased government-backed infrastructure projects, housing schemes, and urbanisation. During the same period, domestic production of TMT bars also increased to 51 MT from 47.2 MT in FY22. This uptick underscores the steel industry’s capability to meet rising demand, with TMT bars constituting a significant portion of total steel production. In FY23, out of 123 MT of steel produced, 52 MT were TMT bars and rods.
As Er. Abinash Mishra, Chief Marketing Officer at Captain Steel India Limited, says, TMT bars offer a blend of strength and flexibility crucial for earthquake-prone regions. The 600 EQR rebars provide superior protection against seismic forces, while FBE-coated rebars address corrosion challenges, significantly extending the lifespan of steel structures.
One of the significant trends reshaping the TMT bar industry is the use of micro-alloying elements. These trace elements, such as vanadium, titanium, niobium, zirconium, boron, molybdenum, and rare-earth metals, enhance TMT bars’ strength, durability, and performance. For instance, vanadium improves strength by forming robust carbide compounds, while titanium refines the grain structure, promoting uniformity. Niobium enhances toughness and weldability, and zirconium controls grain size during heat treatment. Boron increases hardenability, molybdenum improves strength and corrosion resistance, and rare-earth metals contribute to grain structure and impurity removal. Incorporating these elements makes TMT bars suitable for high-stress environments, extreme weather conditions, and seismic zones.
Precision in rolling and quenching processes is essential for TMT bar production. Automated technologies have significantly improved control over pressure and temperature, resulting in uniform cooling and superior mechanical properties. Automated quenching systems prevent internal stress and enhance the overall quality of the bars, contributing to their durability and performance.
Another important trend is the application of corrosion-resistant coatings. Fusion-bonded Epoxy (FBE) coatings provide a protective layer that shields TMT bars from rust and corrosion, particularly in humid or coastal regions. This uniform application ensures extended durability and reduced maintenance costs, making TMT bars more reliable in challenging environments.
Automating material handling, including conveyor systems and robotic arms, has revolutionised manufacturing. These innovations enhance load capacity, reduce manual errors, and improve productivity, setting a new standard for efficiency and accuracy in TMT bar production.
The integration of smart sensors with TMT bars represents a cutting-edge trend. These sensors provide real-time data on load distribution, temperature, and structural stress, allowing for better monitoring and maintenance. This technology helps ensure construction projects’ long-term performance and safety, offering valuable insights for engineers and builders.
The environmental impact of steel production has led to a growing focus on sustainability. Leading TMT bar manufacturers are adopting greener practices to mitigate their environmental footprint. Recycling steel is a significant initiative, reducing reliance on new raw materials and minimising waste. Using renewable energy sources in production processes helps lower greenhouse gas emissions. Optimising production processes to reduce waste and treating by-products before release also contribute to a more sustainable industry.
Demand drivers
Urbanisation is a major driver for the increased demand for TMT bars. The expanding urban population and the development of smart cities are fueling the need for high-quality construction materials. Government initiatives such as the Smart Cities Mission and Pradhan Mantri Awas Yojana (PMAY) are also contributing to this demand, particularly in large-scale infrastructure and housing projects. Furthermore, the booming real estate sector is significantly increasing the use of TMT bars in construction.
Key properties of TMT bars
TMT bars are known for their exceptional strength, which is attributed to the hardened martensite layer formed during the thermomechanical treatment. This strength allows them to support heavy loads and withstand significant external forces, making them suitable for high-stress applications in construction.
Their impressive ductility enables them to deform under stress without fracturing, preventing sudden failures and ensuring structural safety under bending, twisting, or seismic forces. The self-tempering process further enhances ductility by refining the bars’ microstructure, allowing them to bend and stretch without compromising integrity.
Corrosion resistance is a major consideration in construction, and TMT bars are designed to resist corrosion effectively, extending their service life even in harsh environments. The controlled cooling process reduces internal stresses, minimising the likelihood of corrosion.
TMT bars are highly weldable and bendable, making them versatile for various structural configurations. Their refined microstructure ensures that welding does not compromise strength or ductility, and their bendability allows them to be shaped according to design requirements.
In terms of fire resistance, TMT bars maintain their strength at elevated temperatures, which is crucial for ensuring structural integrity during fires and contributing to safer evacuation and firefighting efforts. Their enhanced seismic resistance makes them effective in absorbing and dissipating seismic energy, reducing structural damage during earthquakes and improving safety.
The ribbed surface of TMT bars provides excellent bond strength with concrete, ensuring effective load transfer and contributing to overall structural stability. Additionally, the high tensile strength of TMT bars allows for fewer bars than traditional mild steel reinforcement, resulting in reduced material and labour costs and faster construction timelines.
Challenges
Despite their benefits, TMT bars face several challenges. Variations in raw material costs, such as iron ore and coal, can impact production costs and profitability. Manufacturers also face regulatory compliance with diverse standards and certifications. Additionally, intense market competition among numerous players puts pressure on pricing and profit margins.
Testing, standards, and certifications
Several tests are conducted to ensure the quality and performance of TMT bars. The tensile strength test measures the maximum load a TMT bar can withstand before breaking, assessing its suitability for construction. The elongation test determines the bar’s deformability without fracturing, indicating its ductility. The bend test evaluates the bar’s flexibility and ability to withstand bending forces without cracking. The corrosion resistance test assesses the bar’s resistance to corrosion from environmental elements, ensuring long-term durability.
TMT bars in India are governed by specific standards set by the Bureau of Indian Standards (BIS) and international organisations. IS 1786 specifies requirements for high-strength deformed steel bars and wires used in concrete reinforcement, outlining mechanical properties, chemical composition, dimensions, and tolerances. The revised version, IS 1786-2008, establishes requirements for hot-rolled steel bars for concrete reinforcement. International standards such as ASTM A615 and BS 4449 cover deformed and plain carbon steel bars for concrete reinforcement, specifying mechanical properties and dimensions. By understanding the advantages, properties, and challenges associated with TMT bars, stakeholders can make informed decisions to enhance construction projects’ durability, safety, and efficiency.
Cookie Consent
We use cookies to personalize your experience. By continuing to visit this website you agree to our Terms & Conditions, Privacy Policy and Cookie Policy.