Torqueing technology to secure mining, construction heavy machinery
By Edit Team | September 23, 2019 5:54 am SHARE
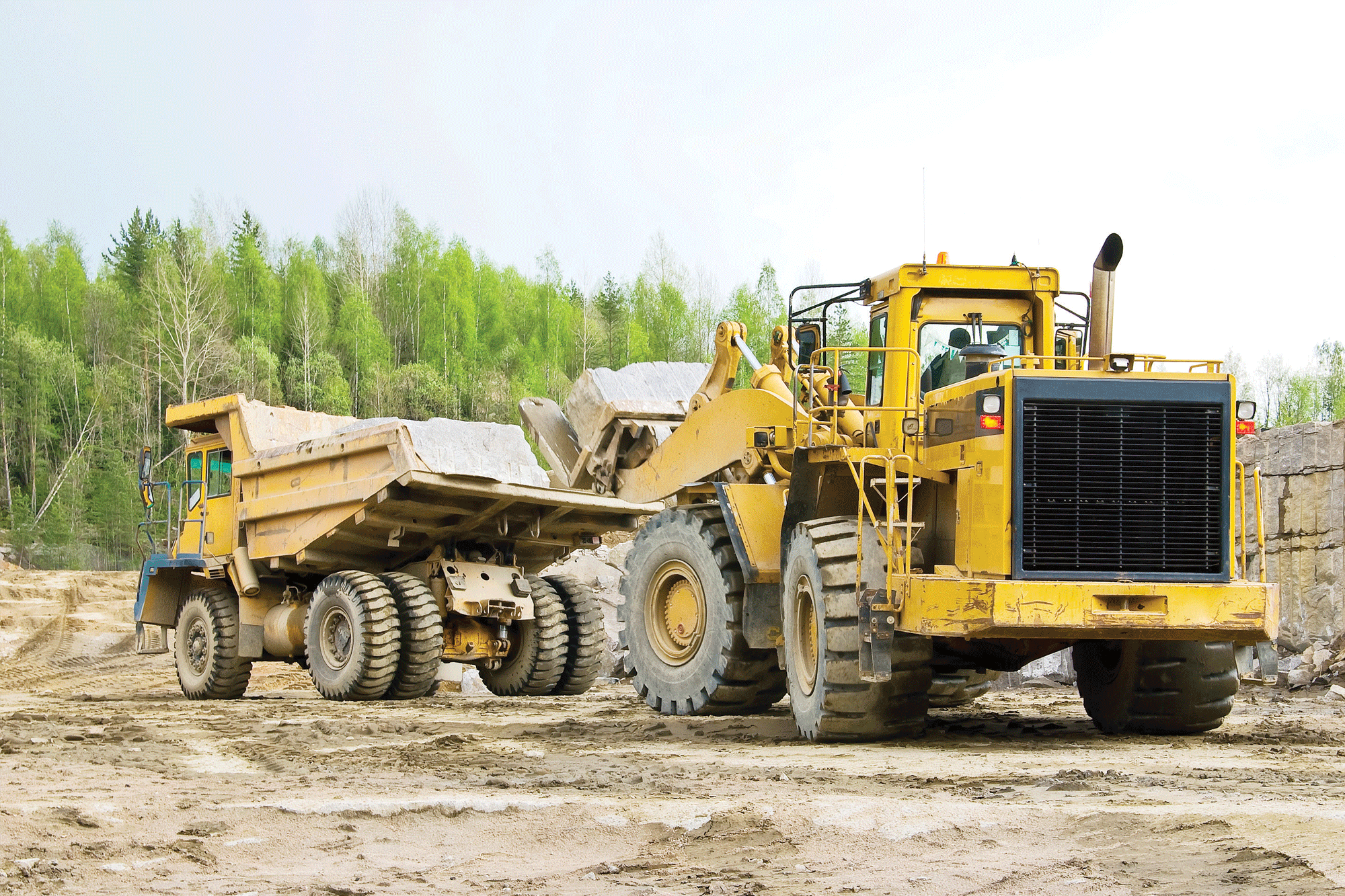
Excavators, loaders, bulldozers, graders, trenchers, scrapers and all other mining and construction equipment have one thing in common – most of their joints are held together by bolts and nuts. The advantages of using bolts are that they are removable, reusable and secure the joints under tension.
Bolts act as a spring and can be stretched within the elastic limit or the yield point of the bolt material. This load applied using torque is retained when tightening the nut. It is important to ensure that the bolts are tightened to the required or specified torque values as these bolts are constantly exposed to high vibrations, rough terrain and heavy loads carried by this equipment in extreme environmental conditions.
Some of the top heavy machinery plants (OEMs) use Direct Current (DC) controlled bolting tools during production for sake of repeatability, speed and traceability. These tools aren’t portable enough to be used onsite and are normally meant to be used in a controlled environment.
Bolting operations at a job site are a different ball game. High loads would be required to tighten or loosen the bolts due to rough operational environmental factors like dust, debris or other foreign material. Besides there might be clearance issues around the bolt to place the tool, which may be non-existent in the assembly shop environment.
Common methods of bolting at site include impact wrenches and manual methods. These methods mostly result in inefficiencies due to uncontrolled torque, workers fatigue, noise pollution and no traceability mechanisms. Common health hazards include HAVS (hand arm vibration syndrome).
New generation battery operated cordless torque wrenches offer the most portable, repeatable and accurate alternative in modern day site conditions with practically no vibration or noise levels. The battery torque tools come in 36V and 18V battery variants with maximum torque outputs of up to 6500 Nm and added documentation features to keep track of torque applied on all the bolts.
Another popular tool with a proven track record in use on mining and construction equipment is the pneumatic torque wrench. These tools provide higher torque output, speed and accuracy without the noise and vibrations of pneumatic impact wrenches. Extensions may be used to access bolts in wheels and tight pockets.
Latest methods in bolting include use of patented products such as the HYTORC developed “reaction-free” washers and “back-up” washers on the bolts. These washers help to lock the torque tools to the nut, eliminating reaction forces, which is a huge safety factor that also eliminates “pinch points” during operations.
Advanced bolting solutions (HYTORC India) offers a complete range of hydraulic, pneumatic, electric and battery operated torque tool systems, along with fasteners for reaction-free bolting.
Cookie Consent
We use cookies to personalize your experience. By continuing to visit this website you agree to our Terms & Conditions, Privacy Policy and Cookie Policy.