Two ways to increase productivity of mining equipment
By Edit Team | March 1, 2016 12:31 pm SHARE
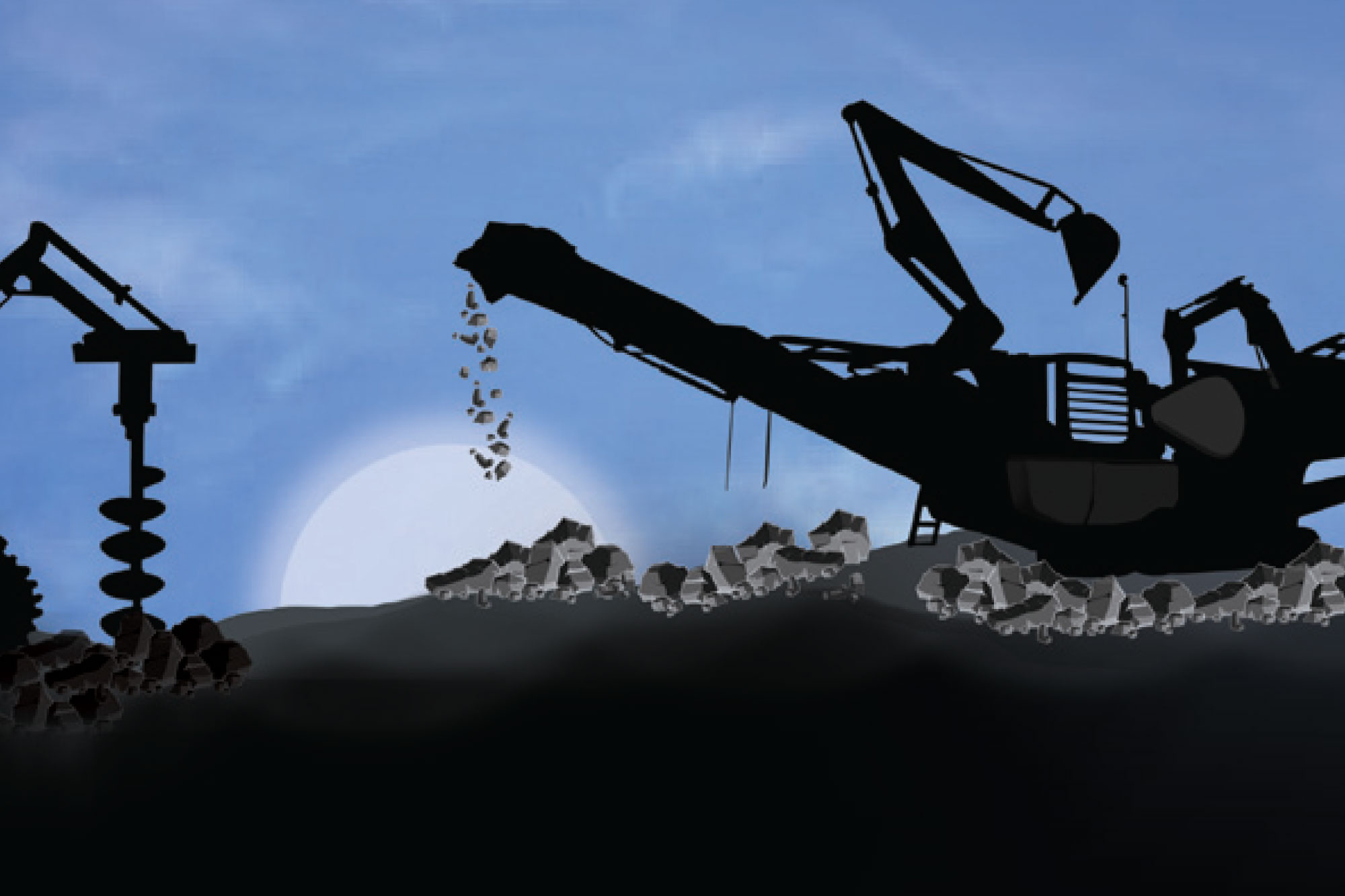
Discussion on different ways to increase the productivity of mining equipment
All industries are dependent on their assets and so are mining companies. The increase in automation, compounded by the increase in the size and capacity of equipment over the years has drastically changed the consequences of equipment ineffectiveness. Current economic conditions, severe global competition, environmental regulations and a continually improving focus on safety are also causing mine managers to consider creative and proven methods to determine effectiveness of their equipment so they can take necessary precautions to increase the effectiveness of their equipment and to reduce the total production cost.
1. Overall Equipment Effectiveness (OEE)
“Mining is a very capital-intensive industry, and it is known fact that the equipment utilisation and accurate estimation of this utilisation are important since mine managers want to utilise their equipment as effectively as possible to get an early return on their investments as well reducing total production cost,” says Pankaj Kumar, Vice President – Equipment Sales, DOZCO (India) Pvt Ltd.
Many studies have been carried out on selection of mining equipments. But there has been a little attention on the measurement of effectiveness of those equipments. Only maintenance policies have been studied and implemented in order to improve availability of these equipments. Therefore the aim of this study is to introduce a method, which is widely accepted in manufacturing industries, used in measuring overall effectiveness of equipments known as Overall Equipment Effectiveness (OEE).
Overall equipment effectiveness (OEE) = Availability (A) × Performance Rate (P) × Utilisation (U)
According to Kumar, mining contractors can take the following six steps to improve both labor and equipment productivity:
• Keep track of productive, standby and non-productive time.
• Consider the hourly cost of owning or renting equipment.
• Monitor variable vs. fixed costs.
• Manage equipment maintenance and repair.
• Schedule equipment efficiently.
• Select the right equipment for the job.
2. Scheduled repair and maintenance
Unscheduled repair and maintenance of mining production can have a direct impact on the productivity and increase the opex of the mine. “In addition to scheduled maintenance program which the OEMs advise, we also suggest our clients to use a cloud based condition management software (CMS),” says Loknath Director and Co-founder, Geovale Services.
The new process, which in a nutshell, involves:
• Continuous gathering of critical component’s health conditions
• Analysis of the information by experts using customised algorithm
• Creation of a maintenance schedule which is just in time and cheaper
Such a CMS system has multiple benefits like lowering the overall maintenance cost, improving productivity and lifecycle of the mining equipment.
Cookie Consent
We use cookies to personalize your experience. By continuing to visit this website you agree to our Terms & Conditions, Privacy Policy and Cookie Policy.