Welding and Cutting need skill development
By Edit Team | August 9, 2022 4:25 pm SHARE
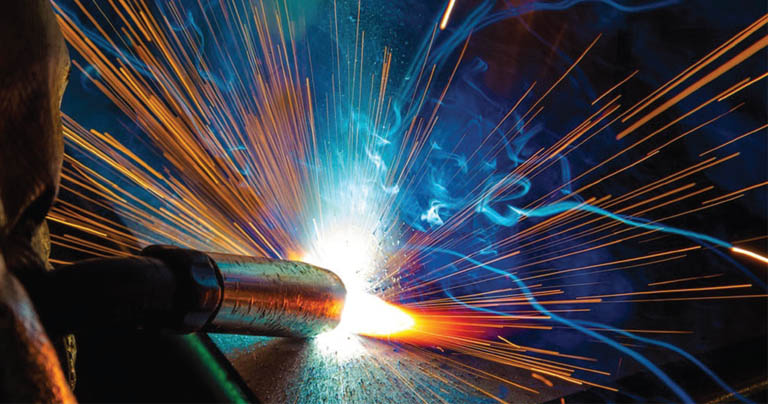
Discussing the technological advancements in the welding and cutting segment, welding experts and leading welding equipment providers stress the need to create training for skill development and welding safety to increase the quality of welders across the welding and cutting industry.
By 2025, India hopes to have a million-person, $5 trillion-dollar economy. The construction infrastructure sector in India is growing in importance as the number of pre-engineered buildings increases. Due to increased PEB buildings and related activities across construction projects, preengineered buildings are expected to revolutionise construction patterns. This transformative trend opens up new opportunities for industrial welding and welding practices across the country. The discussion below highlights the requirement for a skilled workforce to manage automated and robotic welding, training and development, and safety imperatives in welding processes.
Infrastructure-based projects require greater productivity for their beams, columns, foam work structures, and other
structural components. Taking this opportunity, Nimesh Chinoy, Marketing Director, Electronics Devices Worldwide Pvt. Ltd., highlights, “We have specialised Thin Wire SAW systems that help with I Beam, H Beam, and Pre- Fabrication Structure manufacturing. This enables the exploitation of the benefits of submerged arc welding for materials with modest thicknesses ranging from 5 to 15 mm. The typical submerged arc technique performs perfectly above 15mm. Additionally, switching from the traditional SMAW to GMAW or FCAW aids in raising production in this sector. To help them enhance their throughput, SigmaWeld offers semi automated solutions, including magnetic trolleys, weaves, and unique carriages.
Robotic welding applications in construction equipment to obtain accuracy
Robotics in welding is a critical yet efficient application because it allows one to reduce machine downtime and overall production time. Changing industrial requirements, project timelines, and design expectations to achieve precision Robotic welding is very efficient, and we can also reduce production time. According to Anil Kumar,
Robotic Welding System Design Engineer, Panasonic Smart Factory Solutions India, “I am seeing increasing application and productivity growth through robotic welding.” The precision obtained through robotic welding is more efficient, quick, and accurate than manual welding. It improves the welding quality even more. Surprisingly, robots can repeat the same process for several hours.
Adding precision and speed to projects
WAAM, also known as metallic 3D printing, is still in its early stages, with many applications being developed. They are currently helpful in producing sophisticated parts that require extensive machining or material removal from a block. WAAM can save a significant amount of material and the time necessary to construct the part in this case. “SigmaWeld works closely with a few research facilities across the country to develop a variety of WAAM and 3D printing technologies,” Nimish adds.
Skill development in welding and Cutting
Welding engineering and technology are the backbones of industries like construction, infrastructure, and pre-engineered buildings. With the changing infrastructure trends in the construction and pre-engineered building
sectors, welding technology and its requirements are constantly changing. This transformation is primarily seen in quality, speed, precision, and efficiency. This indicates a dire need to have quality welders and increase skill development activities to obtain precision in welding processes.
We still lack skilled welding labour in India. Most welders in India are neither educated nor adequately trained. Welders are not subject to any specific regulations. As a result, it is critical to provide appropriate skill development
on-the-job training to improve their welding skills and educate them on the most recent available welding processes and technologies and advanced welding systems and technologies.
Antree K. A.,Project Manager,Don Bosco Vocational emphasises that some formal institutes in cities such as Pune and Kochi, among others, provide training and development in robotic and skilled welding. Fronius lead the Pune centre, and we also have the Don Bosco Training Centre in Kurla and the Don Bosco Tech in Delhi, both of which
offer robotic welding training.
Satish Sawant, Chief Inspector and Surveyor, Indian Institute of Welding Technology, appreciates Antree’s assessment that we require skilled welders. Welders are not required to have any qualifications. The majority of welders today are not even 10th-class passers. This further adds complications to enrolling them at technical institutes. As a result, they moved towards manual welding. This again adds safety risks to their onsite activities. We
must educate them on the importance of safety through training sessions, modules, and physical workshops. They work from various construction sites and must work at heights in multiple climates and temperatures. They must receive the appropriate training following different welding standards in the automotive, shipping, construction, infrastructure, and machine building industries.
The discussion underlines the value of welding engineering as a viable career option. Because of the increased emphasis on infrastructure addition and construction activities, there is a parallel demand for quality welders. As a
result, welding as a career would produce quality welding engineers capable of handling automated welding processes and robotic welding equipment to ensure optimal precision in the end product.
Welding is already playing a significant role in this manufacturing sector. Moving forward, welding automation and robotics will play a vital role in improving productivity and maintaining world-class quality. Skill development for welding can also be a focus area. As such, there is a real shortage in the availability of welding professionals.
“I am seeing increasing application and productivity growth through robotic welding.” – Anil Kumar, Robotic Welding System Design Engineer, Panasonic Smart Factory Solutions India
“The availability of skilled welders remains to be a challenge for Indian industries.” – Antree K. A., Project Manager, Don Bosco Vocational Training Institute
“WAAM can save a significant amount of material and time required to construct.” – Nimesh Chinoy, Marketing Director, Electronics Devices Worldwide Pvt. Ltd
“Including industry-specific training modules and sessions for manual, automated, and robotic welding processes is critical.” – Satish Sawant, Head Inspector & Surveyor, Institute of Welding & Testing Technology
Cookie Consent
We use cookies to personalize your experience. By continuing to visit this website you agree to our Terms & Conditions, Privacy Policy and Cookie Policy.