Welding automation plays a critical role in increasing productivity
By Edit Team | March 9, 2021 7:26 pm SHARE
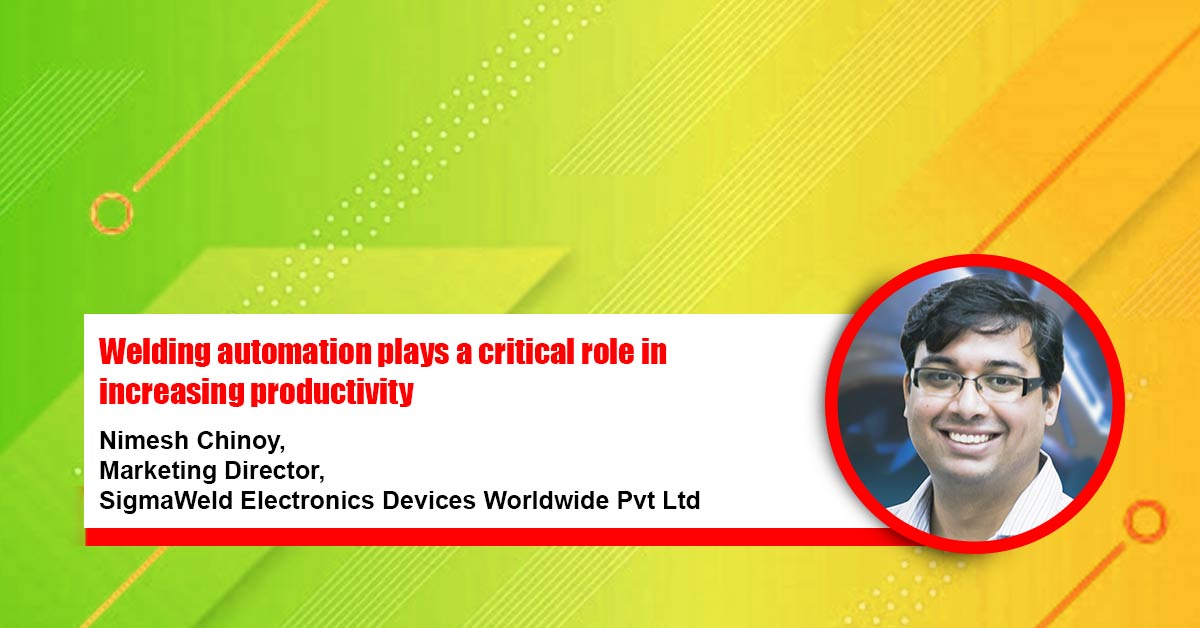
Automation improves quality and ensures repeatability at lower costs. It de-skills the role of the welder and helps them upskill to the role of an operator, says Nimesh Chinoy, Marketing Director, SigmaWeld Electronics Devices Worldwide Pvt Ltd.
With the rise in automation, what is the role do you see AI and IoT playing in the welding sector?
Artificial Intelligence (AI) and the Internet of Things (IoT) technologies are inevitable in any field going forward. The art of welding is very much skill-driven. However, with the help of expert systems and AI, the machines are becoming smarter and can help get desired weld quality with lower-skilled welders. The synergic lines help set the parameters directly based on material thickness, gas combination, wire diameter etc. This also helps the welder understand and learn quicker. Further, programs developed such as JetArc, DAC MD, Root, Pulse or Super Pulse help welder weld specific runs with ease. Also, when we couple these equipment with automation, it helps upskill the welder to an operator. DataData is the next gold, everyone who has the right set of data can analyse and optimise. If you have all the data recorded during welding, it would be very easy to know if there were any possibilities of repair or faults. It would also show the utility of the resource (welding equipment or welder) during the day, month or year. It would help decide how much capacity expansion is required during the peak periods, or simply increasing the number of shifts would be the solution.
With the correct set of data, its analysis can help derive many conclusions and save money, time and resources. It also boosts the confidence of the customer as he knows that the welding done on his job is as per the WPS set by them, any deviations will be reflected in the reports. Welding automation plays a critical role in increasing productivity, improving quality and ensuring repeatability at lower costs. It also de-skills the role of the welder and helps them upskill to the role of an operator. Automation along with IoT helps capture the runtime data and can be visualised from anywhere. A single QC person could be looking at the desktop and monitor more than 40 stations at any given point in time. The system could also send out alerts in case of any abnormalities.
What are the steps and precautions to be taken when it comes to the safety of the welding workers?
When planning any automation, the movements of the robot or SPM arms can be at very high speed and also dangerous if they are in striking distance of the operator. It can be fatal. So, first and foremost, the sensors used for safety must-have redundancy (if one fails other is still in place). When planning automation simulation of all movements, human presence around it must be taken into consideration for both working (in operation) and maintenance (in-service). Light curtains, safety fences, welding curtains, safety locks and multiple interlocks must be used. Another critical parameter is shock sensors, which ensure the system stalls, in case of any collision. One must not choose cost over safety as lives cannot be measured in money.
In the post-Covid situation, how is the costing of welding consumables expected to differ?
Prices of most raw materials have shot up, and there is also a very steep increase in container prices and freight costs. All these will lead to increased pricing of the welding consumables
Cookie Consent
We use cookies to personalize your experience. By continuing to visit this website you agree to our Terms & Conditions, Privacy Policy and Cookie Policy.