Welding automation to play big in green construction
By Edit Team | August 9, 2023 2:43 pm SHARE
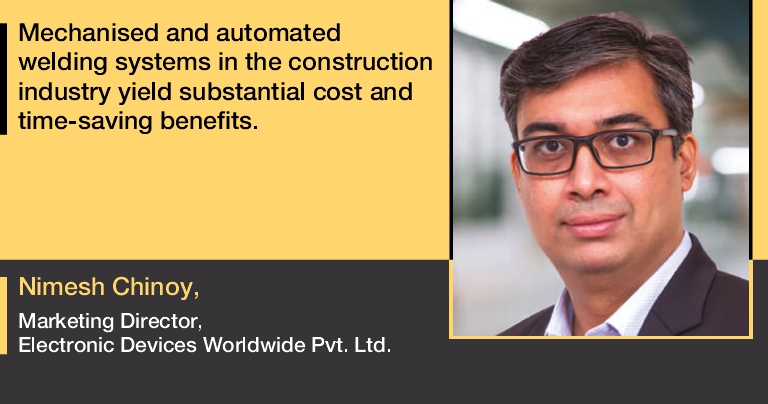
Mechanised and automated welding systems in the construction industry yield substantial cost and time-saving benefits.
Nimesh Chinoy, Managing Director, Electronic Devices, in an interview with B2B Purchase discusses how welding is driving sustainable construction with eco-friendly innovations and adapting to new technologies to ensure safety and efficiency.
How do advanced welding technologies empower construction professionals to overcome complex challenges and achieve higher levels of precision and efficiency?
Advanced welding technologies play a pivotal role in empowering construction professionals to navigate intricate challenges and attain heightened precision and efficiency. By facilitating precise control over welding processes, advanced technologies enhance the precision of intricate joint configurations and critical weld positions. This results in reduced rework and enhanced weld quality. Furthermore, the integration of real-time monitoring and data analytics optimises resource allocation, minimises downtime, and enhances overall workflow efficiency, contributing to elevated project timelines.
What role do skill development and training play in ensuring the safe and proficient use of welding techniques in construction projects?
Skill development and training are paramount in guaranteeing the secure and adept application of welding techniques within construction projects. As a welding machine manufacturer, we recognise that advanced technologies alone are insufficient without a skilled workforce capable of harnessing their potential. Rigorous training equips construction professionals with the necessary expertise to operate complex machinery safely and efficiently, mitigating potential hazards and ensuring compliance with stringent safety regulations.
How are your welding products and solutions like SigmaWeld Accelerated TIG (S.W.A.T) technology revolutionising construction processes and pushing the boundaries of design possibilities?
Introducing our groundbreaking SigmaWeld Accelerated TIG (S.W.A.T) technology, spearheading innovation with a transformative approach. S.W.A.T redefines welding, boasting an intuitive process and a concentrated arc that rapidly permeates materials, achieving seamless welding three times faster than conventional GTAW methods. S.W.A.T’s prowess lies in its focused arc, ensuring deep penetration and minimal heat impact, a leap beyond GTAW. This low-energy process maximises efficiency without compromising performance. Remarkably, S.W.A.T minimises distortion, crucial for intricate designs. Versatility shines as it adapts to various needs, accommodating filler wires or not. SigmaWeld’s S.W.A.T reflects our dedication to advancing construction, empowering professionals for heightened efficiency, creativity, and precision.
What are the cost and time-saving benefits of adopting mechanised and automated welding systems in the construction industry?
The adoption of mechanised and automated welding systems in the construction industry yields substantial cost and time-saving benefits that are impossible to overlook. Data comparison for a 10mm Austenitic stainless steel plate joint reveals a transformational impact.
Taking into consideration all the factors, including weld edge preparation cost, filler metal cost, labour expenses for cleaning and welding, and gas expenditure, a substantial 90-95 percent reduction in rental costs is realised. This comprehensive cost reduction, alongside a 30-40 percent reduction in heat-affected zone (HAZ), ensures minimised distortion in plates, enhancing structural integrity. In embracing mechanised and automated welding systems, the construction industry aligns itself with a paradigm of efficiency, precision, and economic prudence, fostering unprecedented advancements in project outcomes.
How are welding processes adapting to meet the evolving demands of sustainable construction practices, including the use of eco-friendly materials and reducing carbon emissions?
Welding processes are diligently evolving to align with the demands of sustainable construction practices, reflecting a commitment to eco-friendly methodologies. Embracing sustainable materials and reducing carbon emissions, our welding solutions play a vital role. Innovative technologies optimise energy usage, reducing the carbon footprint.Processes like pulsed MIG and SWAT welding contribute to minimal heat-affected zones, conserving material and energy. Automated systems enhance precision, minimising rework and wastage. These advancements synergise with the industry’s shift towards sustainable construction, forging a greener future without compromising structural integrity or efficiency.
Cookie Consent
We use cookies to personalize your experience. By continuing to visit this website you agree to our Terms & Conditions, Privacy Policy and Cookie Policy.