What makes concrete stronger
By Edit Team | February 14, 2018 10:41 am SHARE
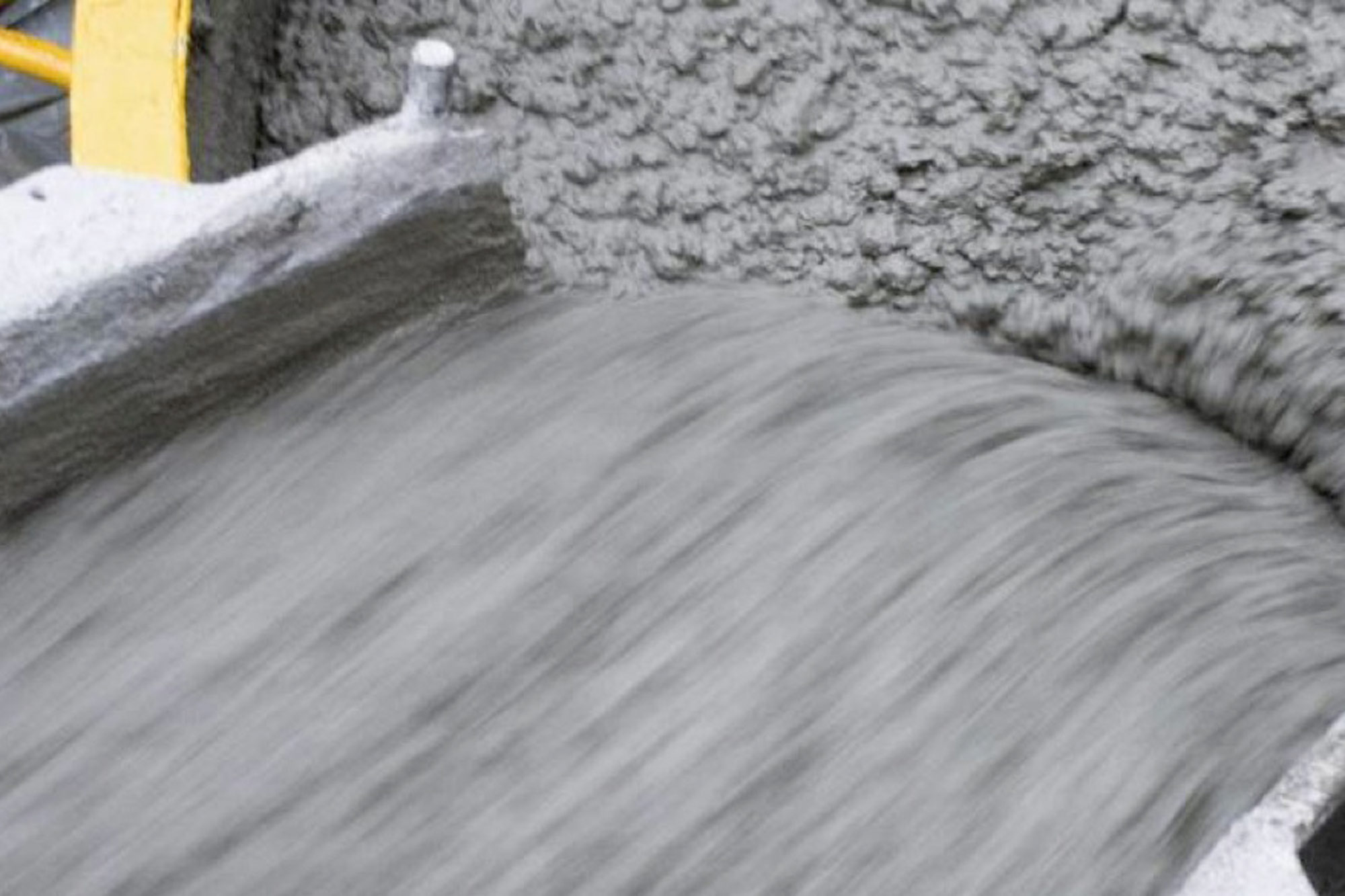
An in-depth analysis on how concrete admixtures, epoxy and grouts help in enhancing concrete strength.
Many of you might be aware of as concrete is the most common building material which is being used for a long time. Cement concrete mainly consist of cement, coarse aggregate, fine aggregate and water. Out of all the above ingredients, cement and water are the most venerable materials which cause the maximum damage to the strength and durability of concrete. These two materials mainly contribute to higher heat of hydration, creep, shrinkage, alkali-aggregate-reaction, etc.
The production process of cement emits around 400 Kg of CO2 per tonne of cement, and if the greenhouse gas emitted due to the electricity required for production of one tonne cement is included, then the figure goes up-to nearly 800 Kg per tonne of cement production which is a frightening figure as far as the environment is concerned. Here we take you through how concrete admixtures, epoxy and grouts help in enhancing concrete strength:-
Factors affecting the workability of concrete
“Admixtures, epoxy and grouts are construction chemicals that are designed to improve structural as well as durability performance of concrete, says, Sunny Surlaker, Head of Admixture Division, MC-Bauchemie India Pvt Ltd. “Admixtures play an important role in enhancing properties of the concrete both in the fresh as well as hardened state. Epoxy and Grouts are materials that are used post construction to improve performance of concrete.”
Admixtures (superplasticisers) help achieve high workability using a minimal amount of water, which helps in achieving excellent mechanical properties in concrete. Accelerators and retarders help control setting time, which ensure concrete develops optimal mechanical properties in the correct time frame. There are other admixtures that help improve overall durability of concrete.
Epoxies are a class of compounds that have multiple post construction applications. Ultra-low viscosity epoxy injections can be used to fill up cracks and voids in concrete, improving the load distribution in the body of the concrete and thereby improving the structural strength of deteriorated concrete. Epoxy mortars are used to patch damaged concrete, again improving the structural capacity of damaged concrete. Epoxy coatings and floorings help provide excess cover to the concrete and help maintain its durability over its intended service life.
Grouts can be structural grouts or injection grouts and can be based on cement, epoxy or a combination of cement and epoxy as a binder. Surlaker adds, “These material help fill voids in concrete. The loads in concrete are distributed in a better manner and thus helps improve the overall strength and load carrying capacity of concrete.”
Water-reducing admixtures
“Concrete admixture plays a vital role in reducing the porosity, capillary pores; shrinkage cracks etc. thus preventing ingress of water, chloride, sulphate, acids and other harmful chemicals which are detrimental for the durability of concrete structure,” says Sukanta Mallik, Assistant Vice President – BDG, CICO Technologies Ltd. “For hydration process, cement consumes 20 to 25 per cent of water and the balance water creates shrinkage and forms capillary pores inside the concrete’s body. Water-reducing admixture reduces the water requirement to achieve the desired workability for a particular mix of concrete and makes the concrete dense, strong and durable.”
The other uses of admixture are to reduce cement content for a particular mix and hence reduce the carbon footprint.
Epoxy grout – low viscosity epoxy materials are used for the purpose of strengthening and making impervious of faulty structures, which mainly occurs due to shrinkage, honeycombing, foundation settlement, dense reinforcement causing voids inside the structures etc. He informs, “There are different processes of epoxy grouting but the basic procedure is to drill holes, fixing of nozzles or packers, and grouting of the epoxy material through the same.”
Reduce water-cement ratio
According to Asish Prajapati, R&D and QC Manager, STP Ltd, the strength of concrete is normally expressed as its compressive strength. The most common idea of gaining higher strength of concrete is to reduce water-cement ratio. And this percolates to idea that admixture (plasiciser) increases the concrete strength. This is not true for liquid admixture or plasticiser. However, he adds, “Liquid admixture changes the properties of concrete mix. This may reduce water-cement ratio and keep the same workability, this may act to slow down setting of concrete (for hot summer situation), to accelerate setting (during cold situation). But in no case liquid admixture or plasticiser increases the strength concrete by chemistry; strength increase is perhaps the side effect of admixture or plasticiser.”
Different plasticisers play different water reducing effect and thereby reduce the capillaries in a dry concrete. Lesser the volume of these capillaries higher is the strength of concrete. Removal of air by vibration, suctions during concrete laying also improves the concrete strength.
He adds, “Solid admixture in the form of minerals in true sense helps in concrete strength mostly in delayed way.”
Modern concretes are designed for high flows, strengths and durability
“Just like how the needs of modern concretes is changing, the admixture technology also has evolved a great deal, modern concretes are designed for high flows, high strengths and durability like never before. This has made the admixture companies also to dig deep, research and come out with newer technologies to suit the new requirements,” informs, Pralhad Mujumdar, CEO – Concrete and B2B Business, ACC Ltd.
He adds, “Polycarboxylate ethers (PCE’s) that the admixture companies call have changed the way modern concretes are designed, the water reduction potential of new age admixtures is now manyfold as compared to the days of SNF’s.”
Mujumdar believes concretes of high flows can be designed with very less water contents or low water to binder ratios as commonly called in the world of concrete technology, this not only helps achieve higher strengths but also use other SCM’s which enhance durability of concrete. He adds, “The other innovations like viscosity modifiers, rheology modifiers help produce self compacted concretes and high flow mixes with great ease which has helped reduce unnecessary increase of mortar content in concrete to achieve pumpability which also is a modern day challenge.”
Mujumdar also believes buildings are now going higher and higher because of space constraints and elements are becoming thinner and thinner; all this has been possible with the new age admixtures. Of course the powdered versions of admixtures now find huge applications in grouts whose demand is increasing day-by-day because of rapid industrialisation and huge infrastructure growth potential.
ACC has a variety of solutions to address the construction challenges in the form of Supercrete and Supercrete HS, which are the high-strength high durability range of concretes, Jetsetcrete is a high early strength concrete, Durocrete is a high durability concrete, Flowcrete is a self compacted range of concrete and of course ACCogrout which are the grouts.
Challenges in earlier PCEs
Swapnil R. Deshmukh, Sr. Marketing Manager, Chembond Chemicals Ltd informs, “Nowadays modified PCE based admixtures are available which also offer good rheology control. One of the challenges in earlier PCEs was the increased stickiness of the concrete mix, now there are some molecules which offer excellent reduction in stickiness. This is often necessary while designing very high strength mixes which have a tight water-cement ratio and high fines. There are other issues associated with PCEs such as, rapid loss of slump, dosage and temperature sensitivity, sensitivity to moisture content.”
Deshmukh opines, “Due to such factors use of PCE based admixtures in lower strength mix designs is many times avoided by concrete producers. Modified PCEs are useful in meeting the requirements of lower strength mixes. Often, due to use of manufactured sand or stone dust, there are issues with regard to slump retention or segregation, these needs to be addressed by smart formulations of blended PCE molecules.”
Concretes based on hydraulic binders such as ordinary Portland cement have a common tendency to crack. There may be different type of cracks and various reasons for cracking to take place. The main reason is shrinkage in plastic and hardened state. Sometimes these cracks are minimal and may be ignored or treated on the surface itself. But when the cracks tend to penetrate deeper, they start affecting the durability of concrete. Cracks may appear in a floor slab, foundation, basement slab; roof slabs a beam or a column. These cracks may affect structural, aesthetical or environmental performance of the utility. This creates a need to treat these cracks carefully, with proper materials and techniques.
He informs, “There are a number of methods and techniques which are developed by the construction industry to such cracks. Crack injection using either Epoxy Resin or Polyurethane resin based grouts, is one of the most efficient and effective technique. Although not new, these techniques and materials have been getting refined and innovative for quite some time.”
Factors affecting strength of concrete
The strength of the concrete depends on 3 factors:-
- The strength of aggregate
- The size of aggregate
- The water-cement ratio
Prajapati from STP Ltd informs, “Concrete strength cannot be more than aggregate strength. Granularity of aggregate to fill the voids and to be coated with cement paste is the main factor for a high-strength concrete.”
Polymer mortar based on epoxy is of high-strength and suitably used for repairing any damaged concrete. Polymer plays the role for strength gaining in concrete.
Flow able concrete in the form of grout also uses plasticiser to enhance flow but strength is determined by the grade of cement and other minerals.
STP has the wide-range of plasticisers, polymer base repairing concrete and grout to help construction industries to have solution for high-end use of high strength concrete.
Effective admixtures help concrete technology for better results
Surlaker from MC-Bauchemie feels that the maximum benefit of using admixtures can only be realised, by using it in conjunction with correct concrete technology. MC offers value addition tools such as mix design analysis, grading curves analysis to maximise benefits for concrete and increase durability.
Surlaker adds, “Admixtures like Zentrament, and the Muraplast FK and Powerflow range of admixtures (plasticisers and superplasticisers) are especially designed for concretes requiring high early and final strengths. These high-range water reducers, based on selected second and latest generation polymers, are free of chlorides and can be adjusted for slightly extended workability time. The concretes so produced are free from bleeding, segregation, are pumpable and require minimum compaction. These are suitable for use in the prestressed and precast industry for manufacturing elements such as beams, columns, slabs, railway sleepers, concrete piles, rails, posts, electrical poles, concrete pipes, etc.”
The development of strength is rapid enough to enable early stripping of moulds for rapid, economic construction on account of lesser formwork requirements. With the correct concrete technology and optimum use of Zentrament, Muraplast FK and Powerflow range of admixtures, about 15-20 per cent cement savings may be achieved by maintaining the same slump and strength.
Apart from concrete super and hyperplasticisers, MC-Bauchemie specialises in a range of:
- Integral waterproofing additives based in Dynamic SynCrystallisation – MC-Special DM
- Centrilit NC (nano-crystallizer) is a pozzolanic concrete additive based on amorphous alumosilicate for enhancing mechanical properties and durability of concrete
- Accelerating, retarding, srinkage reducing and grouting additives for concrete
- Compacting aids for dry – Mixed concrete and roller compacted concrete – Murasan BWA range
- Specialist high-performance curing compounds that heals micro-cracks – Emcoril range
Produce Intelligent and reliable construction chemicals
CICO Technologies Ltd is one of the leading and trusted brands in the construction chemical industries with the oldest brand CICO in the country. Mallik from CICO, informs, “We produce and market groundbreaking, intelligent and reliable construction chemicals that make construction projects not only safer, but also stronger and environmentally viable.”
CICO manufactures and supplies wide-range of admixtures from normal plasticiser to hyper plasticiser of different base. Also, CICO manufacture a wide-range of grout-able epoxy material which has very high-strength and durability as well.
Supercoat Premium
ACC claims that they have many new offerings for addressing the growing needs of construction but would like to mention one of the most exiting solutions from the house of ACC which will go a long way to address road repair solutions.
Often it is observed that roads remain closed to traffic for weeks due to repair work that causes huge inconvenience. Mujumdar from ACC states, “ACC’s Supercoat Premium is magical in the true sense since this is going to make road and runway repairs very easy and fast. This solution hardens within 15 minutes of placing and has the capability to ramp up compressive strength very fast and hence the repaired portion of the road, expansion joint or the runway or the spillway of a dam can be commissioned for operations with 15 minutes of placing and finishing.”
ACC’s Supercoat Premium has been demonstrated and commissioned in many places of India and has a huge growth potential and varied applications in the days to come.
Various solutions offered by Chembond are:
KEM BOND EP 1 – KEM BOND EP 1 is a specially formulated non – shrink, solvent free epoxy resin based system blended with fine inert fillers. It is supplied as a two component material in pre weighed quantities ready for onsite mixing and use.
KEM EPOXY TILE GROUT – KEM EPOXY TILE GROUT is a solvent free epoxy resin blended with selected fine fillers. It is supplied as a three component system in pre-weighed quantities ready for on-site mixing and use.
KEM EPOXY GROUT ELV – KEM Epoxy Grout ELV is a two part, solvent-free, very low viscosity, low modulus epoxy resin system designed to seal cracks in dry concrete and masonry. It is suitable for repairing structural cracks.
The loads in concrete are distributed in a better manner and thus helps improve the overall strength and load carrying capacity of concrete.
Sunny Surlaker, Head of Admixture Division, MC-Bauchemie India Pvt Ltd
Water-reducing admixture reduces the water requirement to achieve the desired workability for a particular mix of concrete and makes the concrete dense, strong and durable.
Sukanta Mallik, Assistant Vice President – BDG, CICO Technologies Ltd
Just like how the needs of modern concretes is changing, the admixture technology also has evolved a great deal, modern concretes are designed for high flows, high strengths and durability like never before.
Pralhad Mujumdar, CEO – Concrete and B2B Business, ACC Ltd
The most common idea of gaining higher strength of concrete is to reduce water-cement ratio.
Asish Prajapati, R&D and QC Manager, STP Ltd
Crack injection using either Epoxy Resin or Polyurethane resin based grouts, is one of the most efficient and effective technique.
Swapnil R. Deshmukh, Sr. Marketing Manager, Chembond Chemicals Ltd
Cookie Consent
We use cookies to personalize your experience. By continuing to visit this website you agree to our Terms & Conditions, Privacy Policy and Cookie Policy.