Why Climbing Formwork
By Edit Team | March 15, 2018 1:13 pm SHARE
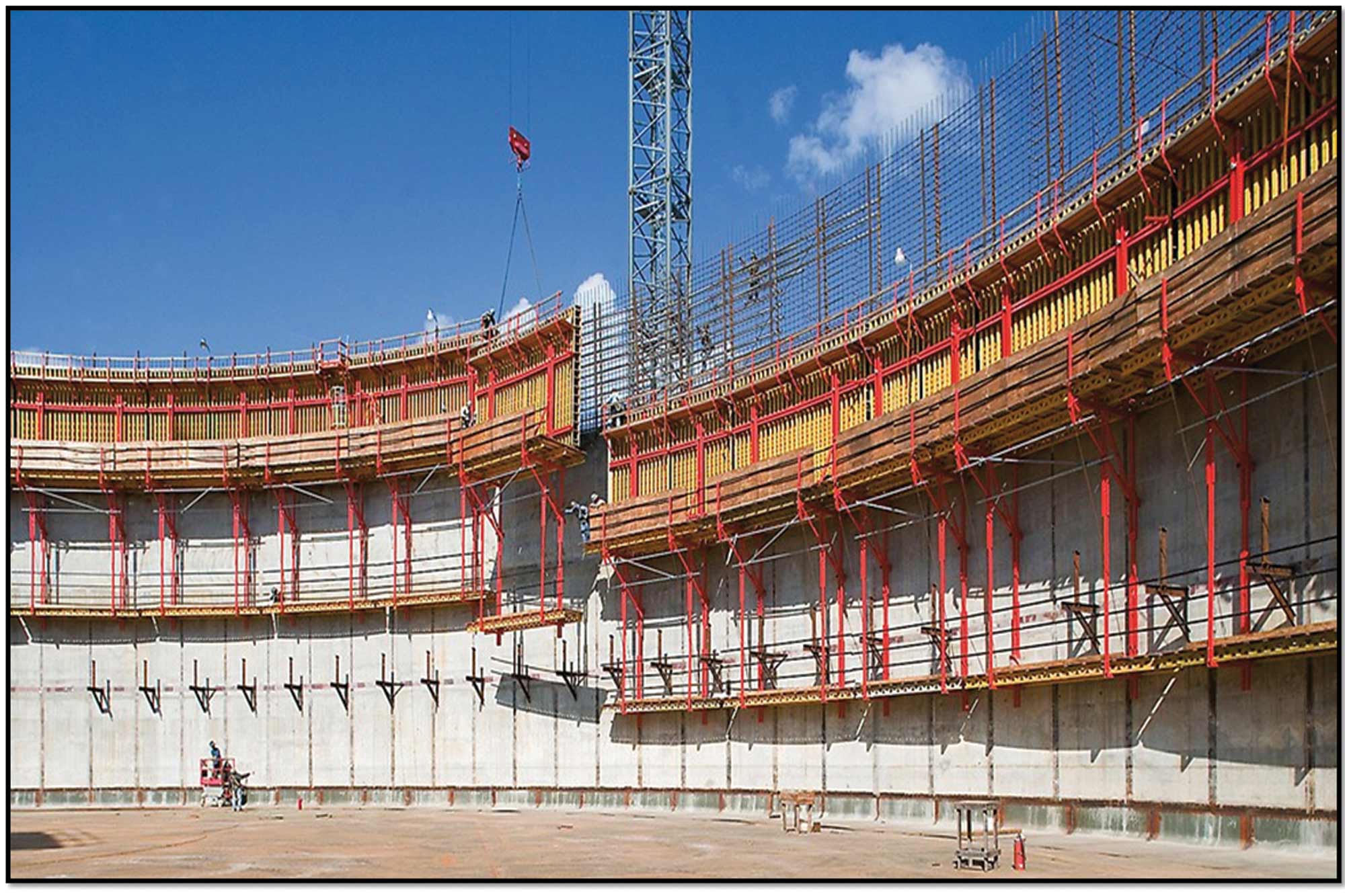
An in-depth analysis on what makes climbing formwork an integral part of today’s construction.
Formwork is temporary or permanent molds into which concrete or similar materials are poured. In the context of concrete construction, the falsework supports the shuttering moulds. There are three types of formwork system slab formwork or deck formwork, flexible formwork and climbing formwork. Here we present you a brief overview on climbing formwork; how it is been assembled, its benefits and application areas.
Climbing formworks for vertical concrete structures
Climbing formworks represent an effective solution for structures that require seamless walls, or their form is very repetitive. There are several types of climbing formwork, depending on the type of building being built. They can move on their own, using hydraulic or electric jacks, commonly known as ‘self–climbing formwork’, or they can be relocated with cranes and other equipment. Siddharth Shah, Managing Director, Cosmos Construction Machineries and Equipments Pvt Ltd says, “There is also a gliding formwork called slip-form but it is moving continuously (when pouring is being made) instead of periodically like the self-climbing formwork. The self-climbing formwork remains in place during the pouring process. Crane picked-up jump forms are typically used on buildings of five stories or more; fully self-climbing jump form systems are generally used on structures with more than 20-floor levels.”
Pradeep Ghumare, Director, NOE Formwork India Pvt Ltd said, “Climbing formwork system is a special type of system for vertical concrete structures that rises with the building process. It allows the reuse of the same formwork over and over for identical or very similar casting sections and floors further up the structure. It can also enable very large concrete structures to be constructed in one single pour, which may take days or weeks as the formwork rises with the process, thus creating seamless structures with enhanced strength and visual appearance, as well as reducing construction times and material costs at the joints which would otherwise require extra reinforcement or connectors. Climbing formwork permits controlled, regular working cycles on all tall structures.”
S. Revathi, Market Research Analyst, Doka India says, “Climbing formwork is a type of formwork for vertical concrete structures that rises with the building process. It is majorly for towers and skyscrapers or that requires a seamless wall structure. It can be divided into two parts based on its operation self-climbing and crane climbing systems, this classification is based on the system used to carry formwork from one level to other. In self climbing hydraulic pumps are used whereas in crane climbing as the name suggests cranes are used to take system to next level.”
Two types of climbing formwork systems
Self-climbing
The structure elevates itself with the help of hydraulic or mechanic leverage equipment. Ghumare says, “The entire core formwork is hydraulically raised independent of the crane. At the push of a button, all platforms along with interior and exterior formwork for an entire floor can be raised in one single cylinder stroke. To do this, it is usually fixed to sacrificial cones or rails emplaced in the previously cast concrete. These systems are relatively complicated and costly.”
Climbing systems with mobile drives are the first step into the world of automatic climbing. Revathi says, “Guided at all times on the structure, they free up the construction crane and can be repositioned even at high wind speeds. We have systems like automatic climbing formwork Xclimb 60 – for structures of straight forward shape of any height, with innovative mobile hydraulic system.”
The built-in hydraulics enables simultaneous repositioning of large multiple-platform assemblies without exposed fall hazards. Revathi said, “Spacious, high-capacity working platforms are ideal for the construction workflow. We have systems like automatic climbing formwork SKE50 plus – for universal use, with a lifting capacity of 5 metric tonnes per climbing unit and automatic climbing formwork SKE100 plus – for high requirements such as greater influences, additional working platforms or live loads with a lifting capacity of 10 metric tonnes per climbing unit in this category.”
Crane-climbing
Ghumare informs, “The formwork around the structure is moved upwards with the help of tower cranes once the hardening of the concrete has proceeded far enough. This may entail lifting the whole section or be achieved segmental. These are cost-effective and versatile systems.”
Firmly interconnected, the shaping wall formwork and the climbing scaffold are quickly crane-lifted as a single unit. Revathi explains, “The different system versions combine ease of working with trouble-free adaptation to different forms of usage. We have climbing formwork MF240 – for structures of any shape and height, with a platform width of 2.40 metre, shaft platform – for the inside formwork of pier and pylons, Dam formwork D15 and D22 for
single sided use, forming solid cross-sections with block heights up to 4 metre.”
She adds, “Guided at all times on the structure, the climbing system can be repositioned even at high wind speeds, so climbing operations are less wind-dependent, faster and safer. We have guided climbing formwork Xclimb 60 – for structures of straight forward shape and of any height, with weight-optimised guiding shoes for this segment.”
Assembling climbing formworks
Shah, says, “Normally, this type (climbing formworks) of formwork is constructed from steel members. Concrete form panels are attached to this frame; some of them supported on rollers. After the concrete walls are poured, it is released and moved away from the wall. Then, if self-climbing formwork is being used, jacks lift the frame up to the next level or to the next area where it will be used. This is normally a relatively fast procedure.”
He adds, “Once the climbing formwork is in position, the panels are closed, and the next concrete wall is poured. The cycle continues, which is normally three to five days. Faster times can be achieved but one needs a really specialised and trained crew. However, the limiting factor to faster times is usually the construction of the floor slabs, which are poured as a separate process.”
Revathi states, “In self climbing formwork there are different setup depending on the structure, every formwork assembly is unique and can only be designed on the basis of project drawing and requirement.”
Benefits of using climbing formwork
According to Shah, climbing formwork usually does not require a crane to move them reducing one’s general condition cost. Increase construction speed is obtained by allowing the vertical and horizontal parts of a building to be built concurrently. It minimises labour time and has a better productivity rate (these systems are designed for repetitive actions) and less labour is required to set up the forms. Increases safety as the labour of setting and removing is less than traditional systems.
Climbing formwork does not need additional supports to the formwork (it is supported by the walls just poured). It can be used during almost all type of weather. Normally, they provide an area for use as a scaffold. High-quality surface finishes can be achieved. It can sustain high winds (better productivity on windy days). The formwork system is easy to clean and reuse with little waste generated compared to traditional systems. Other protection systems (screens) can be hung off a big jump form and climbed with the system. Some of these systems can be installed in such way that even a concrete pump can also be used within the same area and space. Long lengths can be obtained combining different section for each particular project. Some formwork systems can be used at an inclined angle. These systems will minimise the usage of scaffolding and temp work platforms.
Revathi says, “It is (climbing formworks) the best solution for the construction on the heights and getting them done in optimised time, maintaining sync during climbing, concrete pouring and de-shuttering that too in the safest way possible.”
She adds, “Use of any climbing system provides safety in lifting and handling at great heights. It can be pulled back to provide working area to the person on the height. Large and secure platforms are attached for people to stand comfortably without the fear of height while working. It can be dimensioned to many different requirements over a wide application range. It can be used hand in hand with other formworks used and fasten work. It is highly adaptable to complex designs and different concrete finishes. Self-climbing formworks enables large sets of formwork to be lifted simultaneously without needing a crane. Self-climbing can also help where crane mobility is not possible or restrained due to safety issues or due to high wind pressure.”
Ghumare explains the following benefits of NOE Crane- climbing platform AB 300
• Compact: Transport-optimised dimensions.
• Safety: Self-locking suspension hooks provide the highest level of safety; safe access down to suspended platforms below.
• Long service life: Steel parts are hot-dip zinc galvanised.
• Ready for immediate use: Can be used on site immediately after unloading from the lorry.
• High load-bearing: Permissible service load 300 kg per Sq metre (scaffold group 4 in accordance with DIN 4420).
• Bigger size: Longer length: 4.00 metre; 6.00 metre and super-wide with width: 2.30 metre working width: 2.10 metre.
• Variable: The hinged NOE working platform AB 300 can be attached centrally or off-centre by up to 25 cm.
Flexible hook arrangement
• Flexible: The fastening can be chosen to suit one’s purpose, e.g. scaffold bolt M 36, threaded anchor M 36×430, removable cone; climbing shoe can be attached to the walls as well as slab edges.
• Versatile: Practical internal and external corner solutions; adaptable to a wide range of construction site requirements through the modular system with a regular hole arrangement.
• Ease of handling: The travelling device will allow the formwork to be closed and opened quickly with no need for a crane; less crane-time needed, since the folding platform and formwork are moved up in one single lift; simple adjustment options for precise horizontal and vertical alignment of the formwork.
• Most cost-efficient climbing system: Due to the combination of the folding platform AB300 and modular (aluminum or steel) wall formwork there is time and cost-savings from using pre-assembled platforms, lowers manpower costs because the formwork can be shuttered and de-shuttered without waiting for the crane, increases job-site productivity, wide choice of formwork, as the platform can be combined with either panel or timber-beam formwork systems from 50 to 90 kN/m2 permissible concrete pressure.
Application areas
• High rises and sky scrapers (lift shafts, perimeter facades walls and stairwells)
• Bridge piers and pylons
• Power stations
• Barrages
• Dam
• Cooling towers
• Airport control towers
• Silos
Climbing formwork system is a special type of system for vertical concrete structures that rises with the building process.
Pradeep Ghumare, Director, NOE Formwork India Pvt Ltd
Climbing formwork usually does not require a crane to move them reducing one’s general condition cost.
Siddharth Shah, Managing Director, Cosmos Construction Machineries and Equipments Pvt Ltd
It is the best solution for the construction on the heights and getting them done in optimised time, maintaining sync during climbing, concrete pouring and de-shuttering that too in the safest way possible.
S. Revathi, Market Research Analyst, Doka India
Cookie Consent
We use cookies to personalize your experience. By continuing to visit this website you agree to our Terms & Conditions, Privacy Policy and Cookie Policy.