Demand for energy-efficient pumps likely
By Edit Team | September 17, 2018 11:08 am SHARE
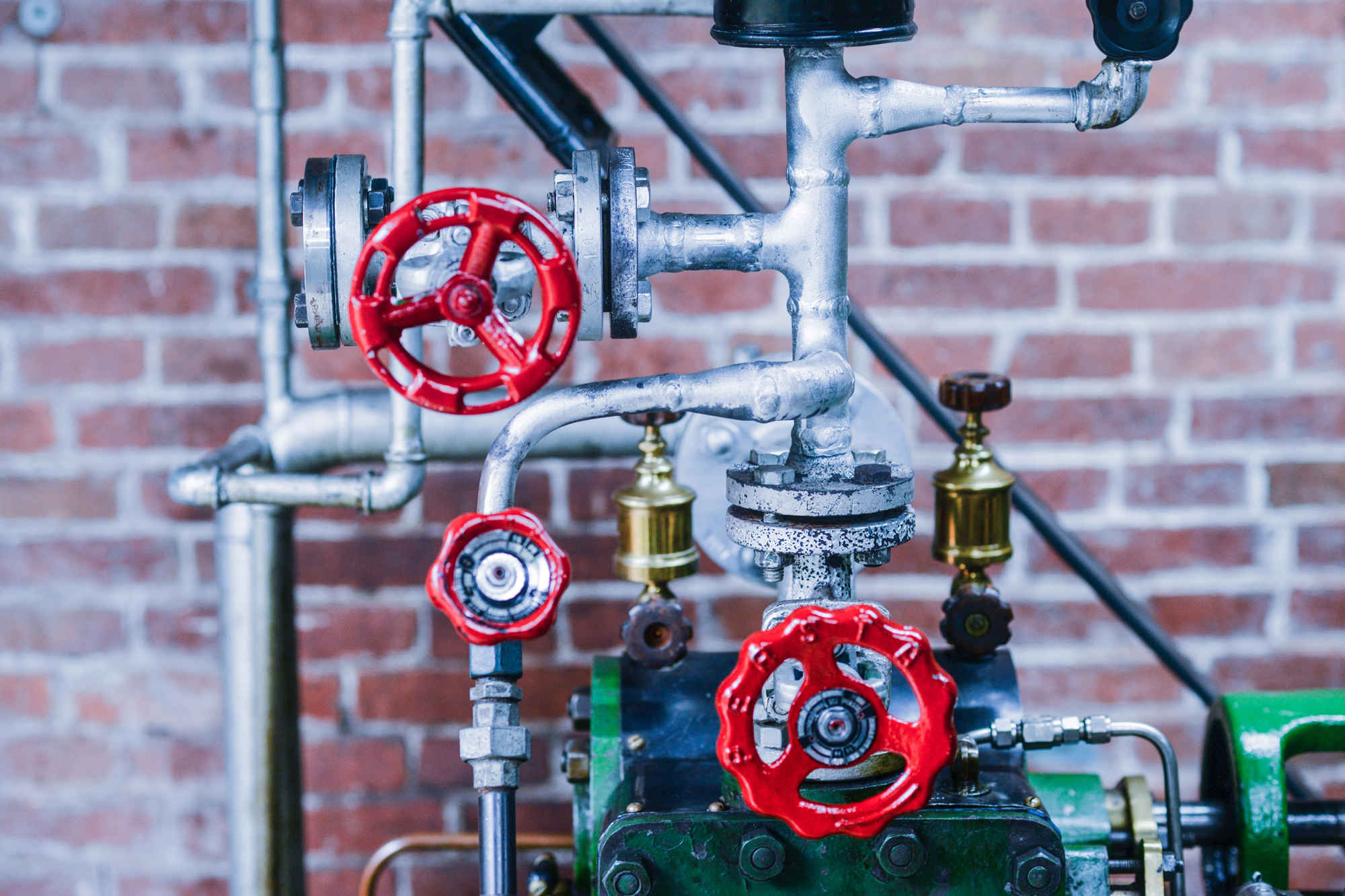
Energy inefficiency, quality, reliability among major challenges amid accelerating demand.
Indian pumps and valves industry has grown significantly over the last two decades, and has been critical in increasing productivity of core sectors including agriculture, engineering, manufacturing and heavy industries. Furthermore, India is close to attaining self-sufficiency in pumps and valves for captive power generation, pulp and papers, energy efficient pumps in utilities and in agriculture sector.
Demand in India
Rising profitability
With rapid growth of pumps and valves in the country, urbanisation is expected to cater to 70 per cent of India’s GDP by 2030. Moreover, public investment in infrastructure including roads, bridges, ports and commercial buildings will create newer avenues for growth for the sector. Additionally, India already exports pumps and valves worth over US$ 1.55 billion, serving various engineering segments to over 100 countries. According to the source, exports in pumps and valves segment is growing at a steady rate of 10-12 per cent annually, the potential for the market to expand and increase its profitability is on the rise.
Great demand: intelligent and energy-efficient pumps
The Indian economy seems poised for the next phase of growth. It is being projected that the Indian water pumps market will touch $3.2 billion by 2023 according to a report by TechSci Research. Rising industrialisation and infrastructural activities are likely to fuel demand for water pumps across India in the coming years. Mahathi Parashuram, Regional Head – Public Affairs, Communications & Relations, Grundfos Asia Pacific Region says, “Increasing focus on development initiatives such as Smart Cities will see a demand for intelligent water and wastewater management’s solutions. These solutions will automatically mean, a greater demand for intelligent and energy efficient pumps.”
Challenges for manufacturers
Energy inefficiency of pumps
According to studies pumps alone, consume around 10 per cent of the world’s total energy used. This means that almost 9 out of 10 pumps are inefficient. If one looks at replacing these pumps with energy efficient pumps, like Grundfos, one can very easily save around 4-5 per cent of this energy. Unfortunately, any at times people end up buying products that have a low initial cost without any regard to the costs of power consumption and maintenance over the life of the product. However, what they fail to understand is almost 85 per cent of the lifecycle cost is power or energy costs and inefficient pumps end up consuming more energy thus incurring recurring costs. Grundfos’ focus has always been to provide solutions that are energy efficient. Mahathi says, “We develop our solutions in such a way that they require significantly less maintenance and repair than some of the other products in market.”
Major hurdle
With ever-evolving technologies, complying with the highest quality systems becomes a critical element to ensure the smooth functioning of any manufacturing plant. The major area of concern is that there is a lack of focus to implement proper standardisation and certification that ensures authenticity; this creates an issue for backward and forward integration with field devices. Another issue noticed in the ecosystem is the limited understanding of compatibility parameters based on demand from the market and the portfolio range available with the manufacturer. With over 600 plus valve manufacturers in India, the lack of product differentiation has emerged as another issue. Additionally, yet another major concern is the ambiguity in this industry related to fragmented nature of smaller players active in the market because the Indian market situation greatly vary with volatile demands and expectation from the end user.
Currently, the focus on the energy-efficient aspect of pumps and valves is still limited. On the contrary however, it is vital that companies start focusing on increasing energy efficiency of their products that will help counter the after-effects of fossil fuel exhaustion. Small-scale sectors across industries are the backbone of the Indian engineering sector. Rising awareness levels about long-term cost savings from adoption of energy-efficient equipment (like in the agriculture sector, in the case of pumps) can help in furthering the demand in the market. Another issue facing domestic pump and valves manufacturers is a general scarcity of qualified talent in the design and manufacturing areas.
Danfoss High Pressure Pumps (HPP)are backed with decades of experience with developing pumps for critical applications, which has pioneered the development of axial piston pump technology to bring all the advantages of positive displacement pumps to high-pressure applications. Anuraaga Chandra, Director – Cooling and Heating, Danfoss India says, “The versatility of Danfoss’s HPP pumps is in its multi-fold applications that includes reverse osmosis, gas turbines, industrial cleaning, humidification and fire fighting among others.”
Danfoss’ pumps have multi-fold applications that include reverse osmosis, gas turbines, industrial cleaning, humidification, among others.
Anuraaga Chandra, Director – Cooling and Heating, Danfoss India
Cookie Consent
We use cookies to personalize your experience. By continuing to visit this website you agree to our Terms & Conditions, Privacy Policy and Cookie Policy.