Drilling machines: better efficiency gives higher yields
By Edit Team | April 17, 2019 10:18 am SHARE
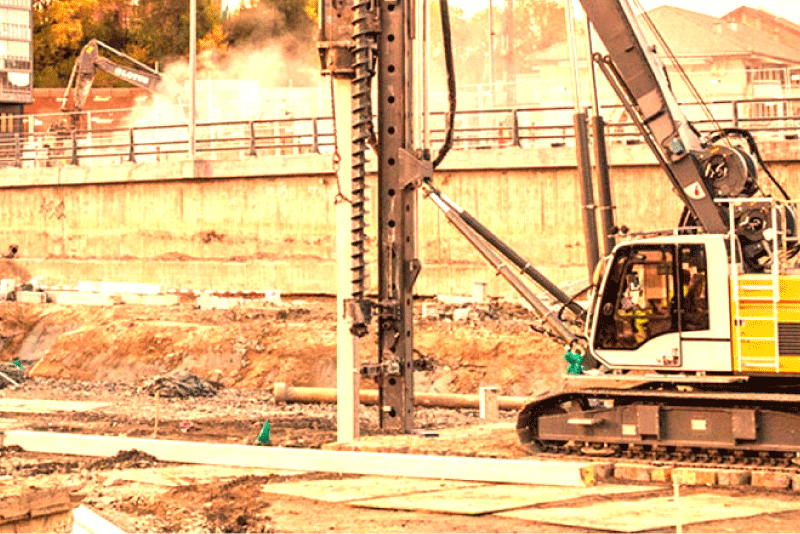
Rate of penetration is equivalent to drilling efficiency and is the major criterion to drive down operational cost.
Generally, requirements to drill a hole are energy source, cutting mechanism, energy transmission, feed system, rotation system and hole flushing medium. Whereas, drilling capacity is controlled by rock structure, percussion power level, bit diameter, type and rotary speed, flushing and coupling loss percentage. The rate of penetration in drilling mainly depends on drill rig set up time, collaring, drill hole stabilisation time, rod handling and rod count length, moving time (bench location) and effective hour per shift.
For better drilling efficiency one should measure and mark-up drill hole’s location. Make diameter in accordance with drilling pattern. Drill holes should be parallel with constant burden. Bottom of holes must be at the same level. The drill rig should be well positioning.
Following are the rock properties that affect drilling:
• Hardness: Hardness and compressive strength.
• Elasticity: Majority of rock minerals have an elastic-fragile behaviour, which obeys the Hooke’s law and are destroyed when the strains exceed the limit of elasticity.
• Plasticity: Some rocks the plastic deformation precedes destruction. This begins when the stresses exceed the limit of elasticity.
• Abrasiveness: Abrasiveness is the capacity of the rocks to wear away the contact surface of another body that is harder, in the rubbing or abrasive process during movement. This property has great influence upon the life of drill.
• Texture: The texture of a rock refers to the structure of the grains or minerals that constitute it. The sizes of the grains are an indication, as well as their shape, porosity etc. All these aspects have significant influence on drilling performance.
• Structure: Discontinuities, cracks, joints and planes of weakness are important for a proper understanding of the real ability of a rock mass volume to with stand load, of how and why it fails and of the resulting fragment size and shape.
Selection criteria
“Breaking of rock for socketing of pile is done with conventional tripod rigs with chisel that uses percussion method. In a hydraulic rotary piling rig the rock is drilled in by cutting tools like rock auger or core barrel by rotary method,” says DV Brahme, Regional Manager, MAIT India Foundation Equipment.
The criteria for selecting right drilling or piling rig for drilling in rock for socketing of end bearing piles are the following:
• Uniaxial Compressive Strength (UCS) of the rock to be drilled in. The commonly used unit for this rock property is Kg/cm2 or Mpa.
• Core Recovery (CR) value (of rock) in percentage.
• Diameter of the bore to be drilled.
• Length of socketing in rock.
Based on the above details a rig having suitable specifications is selected such as torque available for drilling, pull down force available, weight of the rig and centre of gravity and correct drilling tools with perfect geometry of cutting edge as well as bits.
Solution
MAIT India is a one of the leader in the manufacturing of hydraulic drilling rigs and other foundation equipment, tools and accessories. The company manufactures an extensive range of hydraulic rigs for bored piles, water wells, CFA, diaphragm walls, jet-grouting, casing oscillators, stone-columns, etc. MAIT is the an Italian manufacturer of piling rigs for bored piles who also manufactures hydraulic hammers for cast- in-situ driven piles and precast piles. The company also offers hydraulic vibro-float for stone columns as an attachment on its rigs. MAIT uses latest technologies and quality materials such as hydraulic components and engines having world-wide diffusion so that spares are easily available. The prompt after-sales service, easy availability of spares and highly qualified assistance provided by the company ensures customer satisfaction. MAIT rigs are multipurpose machines which can be used for different foundation techniques such asbored piles, CFA piles, diaphragm walls, stone columns, driven piles, etc.
MAIT’s rig models and its capacities are as follows:
HR 180
The HR 180 is a highest sold model because of its versatility and it is easily adaptable to many different applications such as drilling with augers or buckets, execution of drilling casings directly with rotary and by casing oscillator, Continuous Flight Auger (CFA), diaphragm walls and execution of double head drilling.
HR180 has a diameter of 500-1600mm with casing and 2000mm without casing. The depth ranges of 40m, 50m and 60m. Diaphragm walls are of 600-1000mm, with thickness up to 34m depth.
The HR 180 is available in two versions HR 180 CP and HR 180 THD. HR 180 CP – the standard version is equipped with a pull-down cylinder which exerts its force on the rotary and it is principally utilised for drilling large diameter bore holes. The rotary is able to work with a stroke of 5.100 m (17 ft) approx. The HR 180 CP uses a parallelogram system of articulation. HR 180 THD – the THD system moves the rotary by utilising the winch, allowing the rotary to be used along a larger stroke of the mast, 10 m (33 ft) approx. The THD version is particularly useful for driving and extracting casing tubes directly by the rotary and increases daily productivity.
HR 130
The HR 130 is a powerful compact rig that does not require
disassembly for transporting from job to job. It is able to drill large diameters with augers and buckets and can also be equipped with several kits which allow to drill with Continuous Flight Auger, diaphragm walls, down the hole hammers.
The HR 130’s particularly modular conception provides 170 KNm torque and it is easily and rapidly convertible depending on the drilling requirements, allowing the operator to carry out a wide variety of jobs which would otherwise require the use of different and expensive equipment. The HR 130 comes equipped with electronic depth counter, automatic levelling system and air conditioning and heating system in order to better accommodate the operator.
HR130 has a diameter of 500-1300mm with casing and 1500mm without casing. The depth ranges of 40m. Diaphragm walls are 600mm – 800mm, with thickness up to 25m depth.
Breaking of rock for socketing of pile is done with conventional tripod rigs with chisel that uses percussion method.
DV Brahme, Regional Manager, MAIT India Foundation Equipment
Cookie Consent
We use cookies to personalize your experience. By continuing to visit this website you agree to our Terms & Conditions, Privacy Policy and Cookie Policy.