Concrete measures for structural stability and long-term infrastructure
By Edit Team | August 5, 2023 3:33 pm SHARE
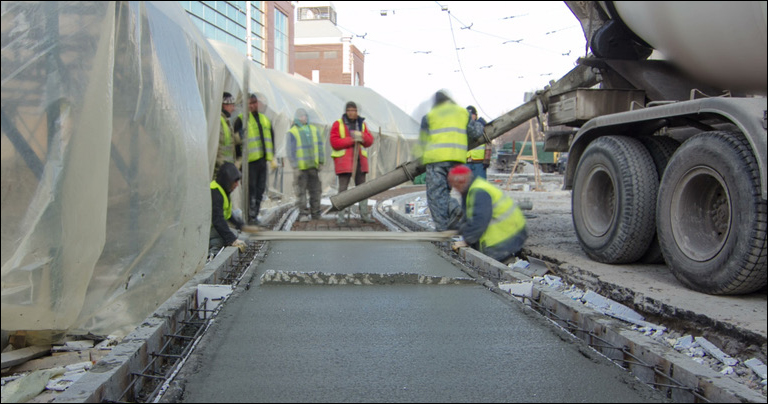
This discussion highlights the importance of standardising quality and examines the potential of RMC as a substitute for cement in construction projects. Additionally, it delves into the various strategies and initiatives adopted by the industry to realise these objectives.
Implementing concrete actions becomes paramount in the quest for structurally sound and sustainable infrastructure. Leveraging advancements in cement and ready-mixed concrete (RMC) technologies, optimising supply chains, and embracing eco-friendly practices, the building material industry strives to bolster structural integrity while maintaining a commitment to environmentally responsible construction. This discussion sheds light on standardising quality and explores RMC as a potential substitute for cement across construction projects. It further delves into the strategies and initiatives employed by the industry to achieve these goals.
Structural strength and safety in infrastructure projects
The building material industry relies on various technologies like ERP, CRM, TMS, and Enterprise Reporting to streamline operations and enhance customer satisfaction. Industry 3.0, starting in the 1960s, brought automation and efficiency to goods manufacturing. While these technologies remain relevant, Vishal Kanodia, Managing Director of Kanodia Cement Limited, stresses the need for newer innovations to increase cost-effectiveness and sustainability.
Anil K. Banchhor, Managing Director & CEO, RDC Concrete (India) Pvt. Ltd., emphasises high-performance cement and advanced RMC technologies. High-performance cement offers higher load-bearing capacities and safety margins, while RMC extends construction lifespans and reduces repairs. Improved shrinkage control enhances structural stability, and workability advancements ensure proper placement for structural integrity. These materials allow engineers to design lighter and safer structures with better quality control and reinforcement. Advancements in RMC technology have significantly improved structural strength and safety in various infrastructure projects, producing more durable structures.
Fibre-reinforced concrete further enhances structural stability by reducing cracking, and special admixtures increase water resistance, making it more resilient against water and chemical damage. Specially formulated admixtures trigger a catalytic reaction, increasing water resistance and improving durability.
In summary, the building material industry’s technological integration improves efficiency and customer satisfaction. Embracing newer innovations enhances cost-effectiveness and sustainability, paving the way for safer and more durable infrastructure.
RMC as a substitute for traditional cement for construction
The building material industry can boost sustainability through various means. Utilising alternative sustainable materials like modular design and precast construction enables faster building with reduced material waste. Embracing renewable energy sources like solar panels reduces reliance on non-renewable energy. Initiatives like carbon credits, wastewater treatment and reuse, and material recycling promote eco-friendly practices. Here, Anil highlights the environmental benefits of using ready-mixed concrete (RMC) in construction. RMC’s controlled batching reduces waste and conserves resources while incorporating supplementary cementitious materials supports recycling efforts. RMC production enhances air quality and leads to energy efficiency and durability in structures. Sustainable practices like recycling and reclaimed aggregates further contribute to environmental preservation. RMC plants also implement water management strategies to reduce consumption and recycle water, reducing their environmental impact. These measures collectively foster eco-friendly goals, aiming to lower carbon emissions, conserve resources, and promote sustainability in the construction industry.
Whereas, Gopal Krishna, Business Head at Aparna RMC, explains that RMC production in centralised batching plants allows for more efficient energy use than traditional on-site cement production, leading to significant reductions in greenhouse gas emissions and improved consistency and durability of structures.
Observance of regulatory standards and project specifications for cement and RMC
Quality control and certification are crucial in the construction industry, particularly for cement and ready-mixed concrete (RMC). Adherence to established standards ensures consistent manufacturing processes and high material quality. Rigorous testing and inspections identify non-conforming materials, guaranteeing safety and excellence in structures. Documentation provides traceability and transparency throughout production and construction.
Considering this, Anil emphasises the role of independent certification bodies in evaluating processes and granting certifications, assuring material compliance. Quality control extends to all aspects of construction, monitoring material handling, placement, and curing to minimise defects and enhance safety. Robust practices and certifications ensure structures meet industry standards.
In RMC, quality control involves a well-structured Quality Management System and adherence to Standard Operating Procedures (SOP). Gopal Krishna elaborates on techniques like Process Control, Control Charts, Acceptance Sampling, and Product Quality control for monitoring and improving RMC processes.
These comprehensive quality control procedures ensure that the concrete mix complies with strength, workability, and durability specifications. The certification system guarantees top-quality RMC delivery by aligning SOPs and processes with industry guidelines.
Meeting demands for large-scale infrastructure projects in cement and RMC procurement
The building material industry leverages smart supply chains to optimise logistics and reduce waste. Technologies like autonomous mobile robots (AMR), indoor drones, and visual AI automate material handling and warehouse operations. IoT-based asset tracking provides real-time visibility for improved inventory management.
According to Vishal, smart last-mile logistics can optimise goods transportation to their final destination. Utilising vehicle telemetry, geo-fencing, and drones can enhance last-mile delivery efficiency.
RDC Concrete, India’s leading independent RMC manufacturer, efficiently meets the demands of large infrastructure projects by overcoming transportation and supply chain challenges. They ensure timely deliveries with an extensive network of 87 plants and 700 transit mixers. Collaborating closely with suppliers and logistics partners, they secure quality raw materials and ensure on-time product delivery.
RMC manufacturers face transportation logistics and supply chain management challenges for large-scale infrastructure projects. They employ specialised transportation equipment like insulated trucks and pumps to maintain concrete quality over long distances. Micro-planning of customer needs is prioritised, and supply chain management systems track concrete movements for timely delivery. Collaborating with contractors and project managers, they customise transportation and supply chain solutions to meet specific project requirements.
RMC and sustainable infrastructure
The building material industry leverages smart supply chains to optimise logistics and reduce waste. Technologies like autonomous mobile robots (AMR), indoor drones, and visual AI automate material handling and warehouse operations. IoT-based asset tracking provides real-time visibility for improved inventory management.
According to Vishal, smart last-mile logistics can optimise goods transportation to their final destination. Utilising vehicle telemetry, geo-fencing, and drones can enhance last-mile delivery efficiency.
Anil takes this opportunity to discuss how RDC Concrete efficiently meets large infrastructure projects’ demands by overcoming transportation and supply chain challenges. They ensure timely deliveries with an extensive network of 87 plants and 700 transit mixers. Collaborating closely with suppliers and logistics partners, they secure quality raw materials and ensure on-time product delivery.
RMC manufacturers face transportation logistics and supply chain management challenges for large-scale infrastructure projects. So, he suggests collaborating with contractors and project managers; they customise transportation and supply chain solutions to meet specific project requirements.
The building material industry’s integration of various technologies has proven highly beneficial in optimising processes and enhancing customer satisfaction. The advent of Industry 3.0 brought automation and efficiency, but the sector must now focus on adopting newer innovations for increased cost-effectiveness and sustainability. High-performance cement, advanced RMC technologies, fibre-reinforced concrete, and specialised admixtures pave the way for lighter, safer, and more durable infrastructure, setting new standards for the construction industry’s future.
Spokespersons and Quotes:
“High-performance cement and RMC extend construction lifespans with improved safety.” – Anil K. Banchhor, Managing Director & CEO, RDC Concrete (India) Pvt. Ltd.
“Smart last-mile logistics optimise goods transportation for sustainable infrastructure development.” – Vishal Kanodia, Managing Director, Kanodia Cement Limited
“RMC production with centralised batching reduces emissions, enhancing structural durability.” – Gopal Krishna, Business Head, Aparna RMC.
Cookie Consent
We use cookies to personalize your experience. By continuing to visit this website you agree to our Terms & Conditions, Privacy Policy and Cookie Policy.