Ultra high performance concrete: sustainable and cost effective
By Edit Team | May 17, 2016 12:44 pm SHARE
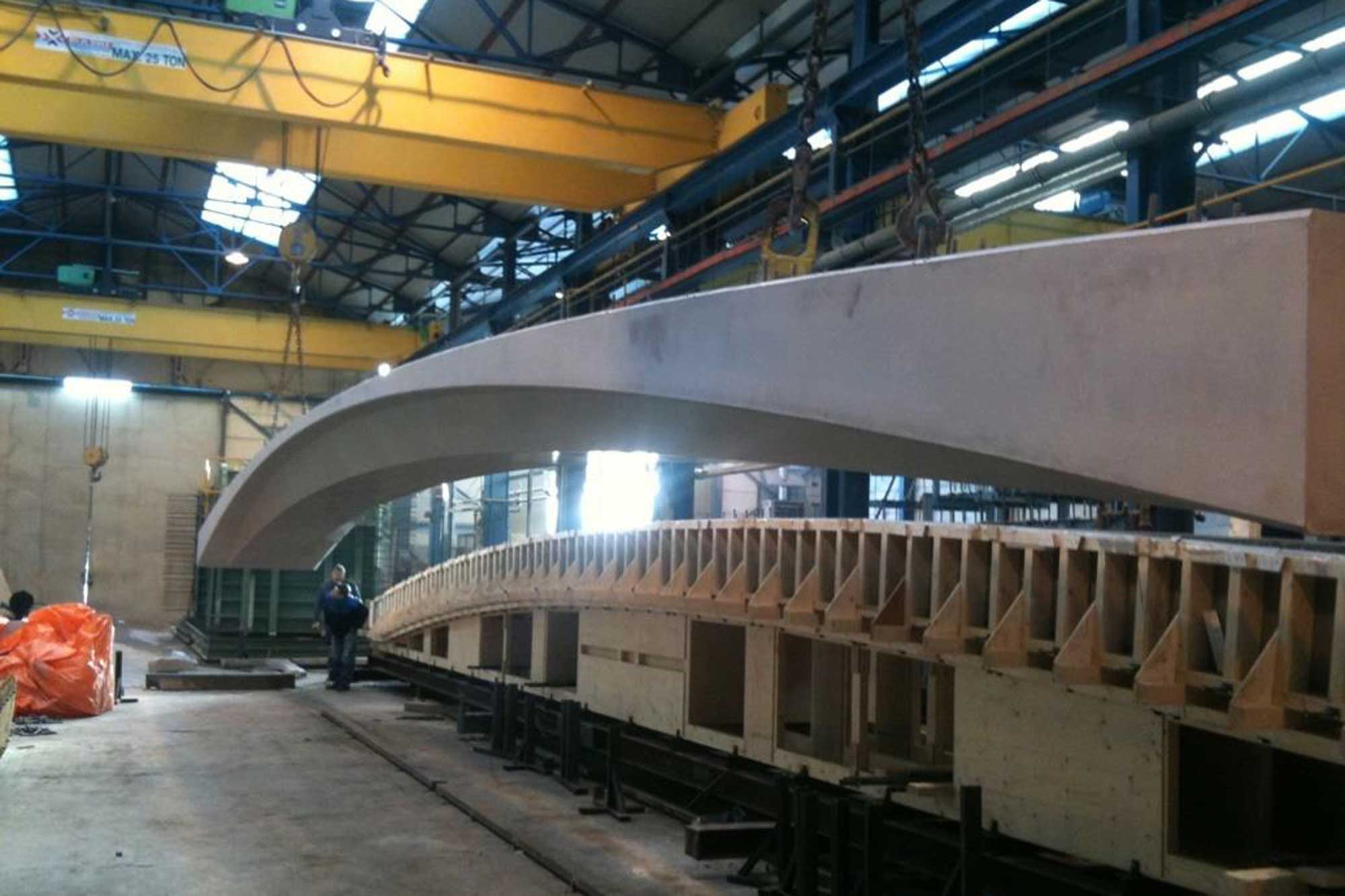
The article explains practical application of UHPC concrete by generative development and optimisation methods
Ultra high performance concrete is a modern concrete that was developed during the last decade. It is a material that is generally characterised by (although not limited to the one) having a high compressive strength from 120 MPa to 200 MPa. Of late more and more projects are being constructed worldwide which demonstrate the potential of this new kind of cement bonded material.
Modern cement bonded high tech materials that are developed by employing Nano technology optimising materials do have better mechanical properties than ordinary concretes or HPC. UHPC not only has the structural performance which is much higher than HPC, But also have ceramic like surface behaviours, impermeability to water and gas, very high heat resistant or work as insulation material. Hence UHPC will be the next generation high performance material that can be used in classical building applications like structural pre-cast elements, facades, columns etc. That is not all; UHPC can be used in machinery-industry for e.g. form-giving tools and integrated parts of machineries. Further, inspiring designer, architects and engineers see UHPC for new applications where concrete wasn’t a choice before.
Technology
It is a material technology by matching of the physical and chemical complex interactions, such as packing density, water film thickness, interparticle forces, as well as the stoichiometric coordination of all raw materials reserve potential in the concrete. Due to the densification UHPC is characterised by a dense micro structure with a very low amount of capillary pores (< 1.8 vol.-%) that leads to increasing the corrosion resistance, which increases the compressive strength from 80 MPa to 500 MPa. UHPC reinforced by a sufficient amount of steel, other high performance fibres or fibre mesh can reach a tensile strength of more than 20 MPa and in particular cases a flexural strength up to 75 MPa for a 6 mm thick panel. Especially the high compressive strength allows a high grade of pre-stressing that is very interesting for prefab columns or monolithic bridges like the Goosebridge in Germany.
The Goosenbrueck, Utrecht, NL, is made with a maximum grain size of 5 mm with a span of about 20 m. It has a cross section with a minimum amount of reinforcement and prestressing steel. It is pumpable grade ultra-high strength concrete. Except for the prestressing reinforcement and the steel fibres, no additional steel reinforcement is used in the bridge. The concrete including steel fibres was pumped with a conventional rotor-mounted concrete pump into a closed mould.
The interesting part of development of UHPC is that all the material parameters can be influenced individually. This means for example: workability, early strength, compressive strength, flexural strength and even costs can be adapted to required levels. ‘Performance’ doesn’t only represent compressive strength but all the other essential parameters that are fundamental for high-tech products. UHPC is engineered by:
• Using mathematical algorithms to calculate the optimal packing density in combination with the optimal water film thickness around each particle in the mix, and
• Using the locally available raw-materials and the available production technologies.
All given raw materials are analysed by laser diffraction, optical and scanning electrons Microscope methods and characterised by derived mathematical entities. With these input data the optimal packing density in the range of 0 to 0.125 mm can be calculated by including the water film thickness in an evolutionary, non-linear cross-over computational process.
The special effect of water film thickness related of the packing density is shown in the following example:
In a) the water film thickness around the cement grains with the pore water is shown. When replacing the cement by a pore-filling substitute the solid content is increased and displaces the water from the cavities. This water can then be saved and used to optimise the water film thickness as b). The scheme shows that in addition to the cavity filling the reduction of the water film thickness is essential to ensure that the increased computational density can be effective.
Often in concretes a high flexural strength instead of a high compressive strength is required. Through the targeted combination of high tensile strength, bond strength, a flexible nonmetallic reinforcement of a 6 mm thick, plate-like element, having a flexural strength of 70 MPa has been developed. These have already been used in the industries and opens up wide areas of application far beyond the conventional application.
Often pan mixers are available in precast plants, with insufficient mixing intensity in fines graded concrete systems. By intelligently controlled mixing and dosing processes also these mixers are processable to mix a concrete with a compressive strength of above 180 MPa. Shortest mixing times, even below one minute, are possible with high-performance intensive mixer with increased efficiency.
The workability was assessed with a slump flow of 95 cm and a low dynamic viscosity (t500 < 5 sec.). The mix is free from segregation or sedimentation in a number of experiments. The compressive strength after 28 days without heat treatment was 125 MPa. With respect to a smallest possible shrinkage the content of hydraulically active substances (i.e. cement, puzzolana) was kept as low as possible without compromising the cohesiveness and durability of the material.
Other positive side effect when using UHPC in the precast production is the high early age strength. After 2 days, the compressive strength is usually about 90 MPa, whereby the storage in the factory can be substantially reduced.
Through the use of ultra-fine and finer cements the strength development could be accelerated significantly, as table 1 shows. Especially the rapid development of flexural strength is remarkable and allows a very early demoulding of the concrete elements. The specimens were stored thermally insulated to simulate the state of the element.
Cost effectiveness
Next to the material costs itself, the new design of the pre-cast elements can lead to more filigree, lighter and ‘greener” products. By downsizing dimensions and sections, the costs per element are equal or lower compared to regular concrete because lower concrete volume. Not only volume but using these new high-tech concretes means reduction of steel-reinforcement, mould costs, labour costs and so on. Finally, the overall costs of a Quantz or UHPC pre-cast element are the essential factor for calculating the economic efficiency and the return of investment in these new technologies.
Sustainability
The economic effects, structural advantages and the overall performance of the new materials are directly related with each other. The whole development from concrete production to casting to installation e.g. a pre-cast element must be seen holistically.
Conclusion
With the advent of UHPC new horizons of construction industry have come into being. The parameters of concrete which were so far thought to be impossible have now become a reality. New markets for concrete have unveiled with the advent of UHPC. With the optimisation of section and using ‘less’ material, the ‘green’ construction is also possible with UHPC. Hence UHPC is here to stay in the construction industry for long.
Authored by__
M N Ramesh, Director, Talrak Construction Chemicals Pvt. Ltd
Dr. Ing. Thomas Teichmann, CEO, G.tecz Engineering
Contact
Talrak Construction Chemicals Pvt. Ltd.
No. 148, Sri Gururaghavendra Complex
Basaveshwara Circle, RR Nagar,
Bengaluru – 560 098
Tele: +91-9663101013
E mail: chethana.g@talrak.co.in
www.talrak.co.in
Cookie Consent
We use cookies to personalize your experience. By continuing to visit this website you agree to our Terms & Conditions, Privacy Policy and Cookie Policy.