Advances in automation for real-time screening performance
By Staff Report | August 13, 2024 2:54 pm SHARE
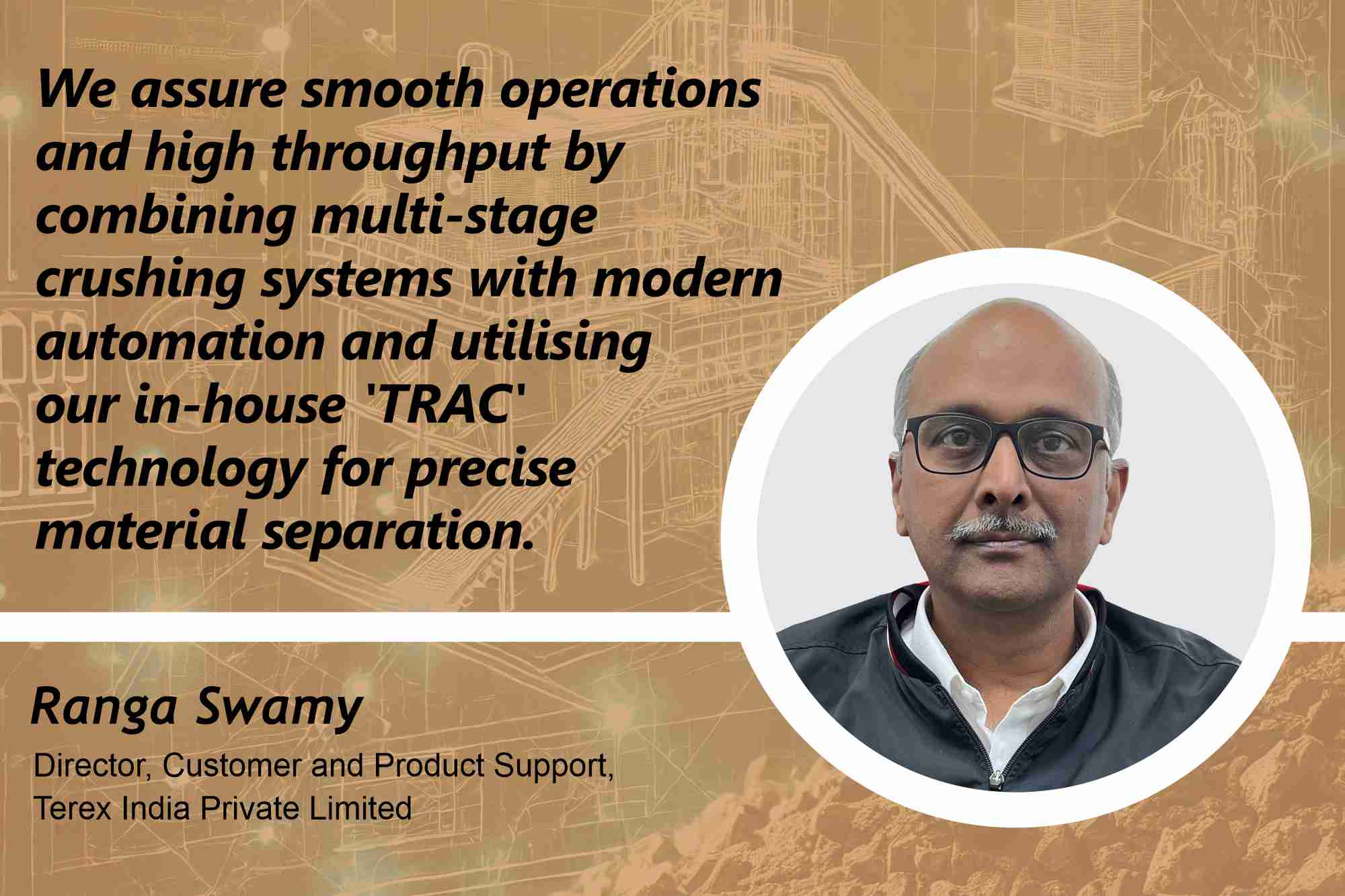
Terex India leverages cutting-edge technology to improve crushing and screening efficiency and accuracy through automation, artificial intelligence, sophisticated materials, and sustainable practices, ensuring industry leadership and remarkable results.
How do you use automation and control systems to improve the efficiency and accuracy of your crushing and screening operations?
Automation systems are critical for improving the efficiency of our crushing and screening processes. We use automation to give appropriate feedback and control units, enabling us to manage crushing forces and power usage properly. This ensures that the processes are always optimised for peak performance. Our ACE Series automation, for example, contributes significantly to preserving this equilibrium, resulting in more efficient and accurate methods.
Can you elaborate on the role of machine learning and AI in optimising the performance of your crushing circuits?
We are dedicated to using cutting-edge technologies to improve the performance of our crushing circuits. While we use telematics extensively to collect and analyse data, we recognise the enormous potential of AI and machine learning to improve these operations. Telematics enables us to monitor equipment health, measure operational parameters, and provide insights for maintenance and optimisation. We intend to incorporate AI and machine learning to enhance our skills. These technologies will allow us to do advanced predictive analytics, optimise real-time equipment settings, and eventually increase operational efficiency to unprecedented heights. This strategy demonstrates our commitment to constant innovation and staying ahead of the industry.
What are the most significant wear factors affecting your crushers, and how do you mitigate these through material selection and design improvements?
Abrasion and impact are major wear variables that substantially impact crusher performance. We offer various material chemistries, including manganese, martensitic, and high chrome, customised to specific applications and feed materials. We’ve invested in a rock testing facility to recommend the best material chemistry for certain applications, guaranteeing that our crushers are durable and effective. These techniques help to reduce wear and increase the life of the equipment.
How do you integrate multi-stage crushing systems to ensure operation and maximum throughput?
We have invested in automation throughout its product line, allowing for the integration of multi-stage crushing systems. Most of our products support this integration, which allows plant operations to be controlled using wireless remotes. We also use telematics data for analysis and feedback, which, coupled with level sensors and weighing systems, helps to improve throughput and ensure that the crushing systems run smoothly.
What innovations in screening technology have you adopted to improve material separation accuracy and efficiency?
We have created a modified in-house “TRAC” device for online data collection and analysis, focusing on vibrating structures like screens and feeders. This innovation contributes to the precision and efficiency of material separation by offering precise insights and enabling real-time modifications. The “TRAC” gadget is an important component of our efforts to improve screening performance and maintain consistent quality.
How do you monitor and control dust emissions from your crushing and screening operations to comply with environmental regulations?
We have joined AquamistTM to provide innovative dust suppression solutions for monitoring and controlling dust emissions. These solutions are available through our aftermarket products and are specifically intended to reduce dust emissions effectively. Using mist to catch dust particles, we assist our operations in complying with environmental standards while maintaining a safe and clean work environment.
What are the key considerations for scaling up your crushing capacity without compromising product quality and equipment longevity?
When increasing crushing capacity, we prioritise preserving the same footprint for new high-capacity equipment as previous models. This enables renovations without requiring large structural changes, making the process more efficient and cost-effective. We also prioritise strong design and high-quality materials to maintain increasing capacity for equipment longevity and product quality. These issues are critical for attaining long-term growth and sustaining excellent quality.
For more information, visit: https://www.terex.com/en-in
Cookie Consent
We use cookies to personalize your experience. By continuing to visit this website you agree to our Terms & Conditions, Privacy Policy and Cookie Policy.