AIML: optimistic of positive growth
By Edit Team | June 21, 2014 8:16 am SHARE
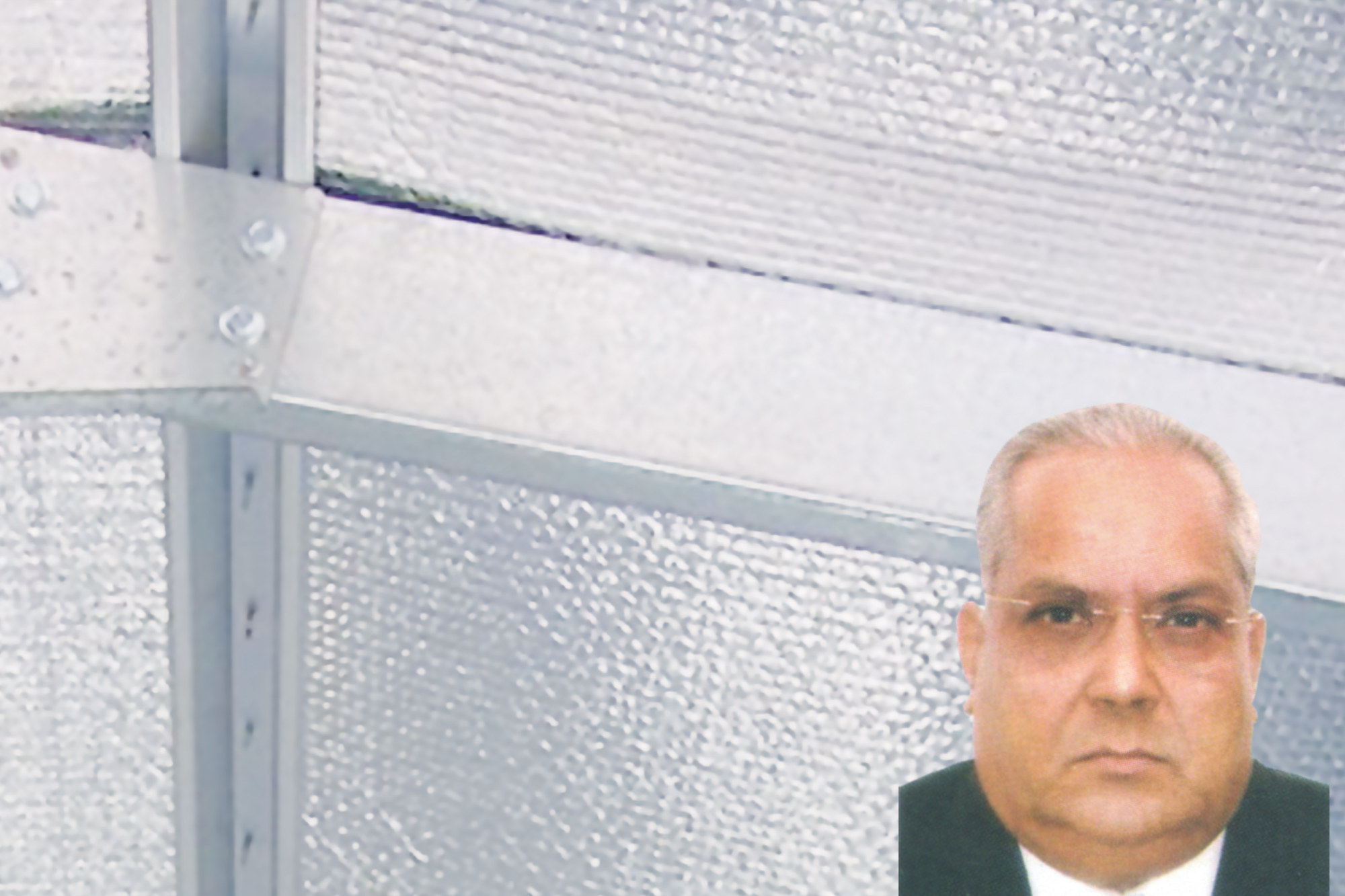
“We are planning to enter backward integration for design and build. We are also looking forward to include substructure site activities in near future,” informs Anil Kumar Sharma, Director, Alliance Integrated Metaliks Ltd.
AIML offers structural solutions for heavy applications. The company has provided key solutions for many major infra projects. In an interview with B2B Purchase, Anil Kumar Sharma talks on AIML and its product offering. He also reveals the company’s expansion plans.
AIML has gained expertise in providing steel solution for use in major structures. Could you explain the products and solutions you offer for this particular area of operations?
We offer plant fabricated and assembled steel girders and beams in various configurations for easy erection and commissioning at site with minimum manual interface. This reduces the erection time and cost as well as project completion time.
What are the USPs of your composite deck columns and beam solutions?
Shuttering and support for composite deck columns and beam solutions is a very tedious exercise for creating floors in high-rise building and dismantling the same involves additional cost. Also, no activity can take place at floor level till concrete gets cured.
Composite deck is a productive solution that acts as load bearing support by grid of underneath beams and transfers direct load to columns. This gives a permanent shuttering and shares the load pattern designed for the floor. Once laid, mass concreting via concrete pumps can be done at various floor levels at once.
Name some of your key projects under these business verticals.
We have provided solutions for infrastructure projects and power plants like DMRC, NHAI and NTPC.
You also offer erection and launching solutions for structures and bridge girders. Could you discuss the features of these solutions in details?
AIML provides turnkey solutions to rail over bridges and NHAI span bridges. Proper evaluation of the site is conducted before sending the materials to site. Trial assembly is conducted by deploying 100-tonne crane before sending the finished bridge span to site. When fabrication and erection is being done from single source, the fabrication accuracy gets factorised into erection efficiency without passing on the efficiency to various agencies. This helps project to run at desired speed as per schedule. Further there is no compulsion to dump the finished goods at site. So one can synchronise supply and execution demand.
In a bridge erection project, reducing construction time is one of the most sought after aspects. How do you contribute to these aspects?
Apart from drawings, the interface of matching the connections of plant fabricated goods is done well in time and is induced into finished product by taking due care at initial stage.
Moreover, all the connection members are trial assembled at plant with bolted connections and then shipped to site reducing assembly error while launching.
You announced doubling of capacity to 60,000 tonne per annum. What is the current status?
Due to slow economics in the recent past, the target was put on hold for some time. Now with the new face of the government, we will revisit our expansion plans.
Do you have any other expansion in pipeline?
We are planning to enter backward integration for design and build. We are also looking forward to include substructure site activities in near future.
Due to slow economics in the recent past, the target was put on hold for some time. Now with the new face of the government, we will revisit our expansion plans
Cookie Consent
We use cookies to personalize your experience. By continuing to visit this website you agree to our Terms & Conditions, Privacy Policy and Cookie Policy.