Building strong
By Edit Team | July 29, 2015 7:03 am SHARE
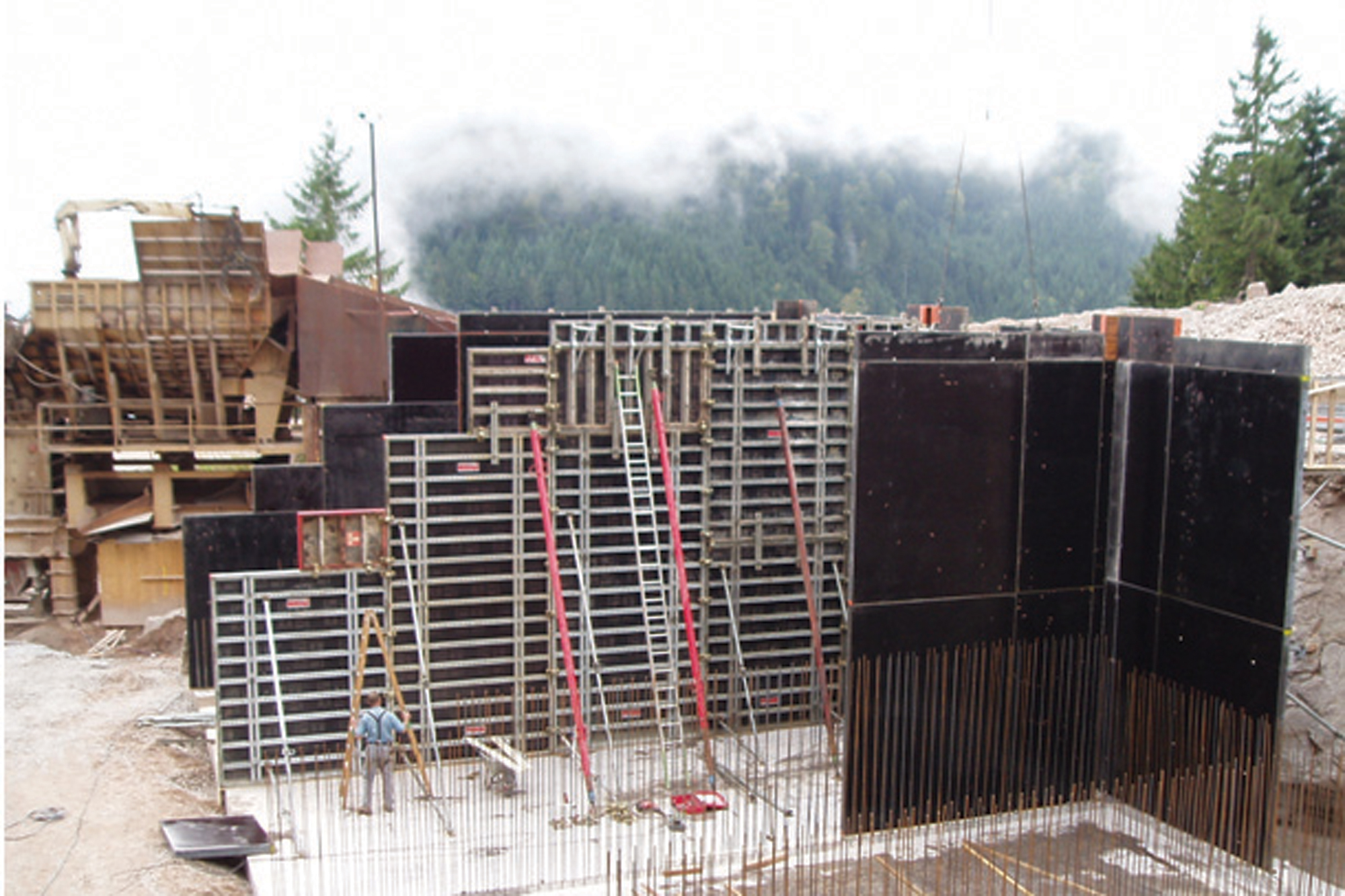
This article explains the advanced scaffolding and formwork technology
Every construction site is unique. Manufacturers want to find out the best solutions for the challenges faced during execution of projects. Availability of wide range of products with high quality systems in this field is the solutions for the challenges. Keeping in mind the basic challenges the article speaks about how to overcome them with the help of new technologies in scaffolding and formwork.
Acceptance
Scaffolding is integral and basic part of construction, in past India has always focused more on quantity rather than quality of construction. “We have always sourced out cheapest solutions on the cost of safety and quality. In simple word we are too late to adopt this technology,” informs Pankaj Udeshi, Assistant General Manager Procurement, Supreme Infrastructure India Pvt. Ltd. He adds, “But the trends have changed now, the bamboo has been replaced by steel pipe (Props) and battens have been replaced by beams.”
Speaking about the acceptance of scaffolding and formwork, Rohitt Sharma, Director, Maini Scaffold & Formwork Systems Pvt. Ltd., Faridabad says, “In today’s scenario, when India is on the threshold to become the world’s youngest country with 64 per cent of its population in the working age group, the housing demand in the country is set to rise.” He further adds, “Due to acute shortage of housing units, government and developers are keen to shorten the huge gap between supply and demand in the shortest possible time. Focusing on timely delivery and cost effective construction methods, exploring modern and advance techniques are progressively in demand.”
The boom in the construction industry has opened up new opportunities for the growth and development of the scaffolding and formwork industry in the country. Vijay Kalantri, Chairman and Managing Director, Dighi Port Limited says, “With the government laying special emphasis on construction and infrastructure development in the 12th Five-Year Plan, opportunities abound the Indian scaffolding and formwork industry. The industry is witnessing major transformation and the reasons for growth are aplenty. First, the speed and uncertainty with which projects are awarded these days, a contractor has no choice but to ensure a quick completion and move on to the next one. Secondly, scaffolding and formwork provides qualitative consistency in construction besides good surface finish, thereby saving a lot of finishing time and plastering material,” he shares.
“The construction companies are paying greater attention to labour and time saving. Hence the acceptance of technologically advanced system formwork is steadily increasing in India, and the scaffolding and formwork industry is in expansionist mode,” says Pradeep Ghumare, Director, NOE Formwork India Pvt. Ltd. Further he adds, “However the advantages of latest system formwork, especially those of higher modularity and higher repetitions, and its usability for various projects, leading to lower cost-of-ownership needs to be appreciated by the contractors. To overcome the initial investment aspect, NOE Germany offers international low-cost financing for their system formwork.”
Speaking about the constraints Mr Sharma says, “Due to time constraints, users prefer suppliers with technical team who can offer end to end solutions i.e. designing with the use of latest software, manufacturing with automatic facilities with robotic concept, hassle free logistics and best on-site support followed by after sales services on single call.”
Latest technology
Aluminium formwork has been making very fast inroads because it is durable, readily available and lightweight. “Customers are more interested in opting for formwork solutions which are user friendly, with in-build safety features enabling speedy construction which make the project more viable and cost effective,” says Mr Sharma.
Mumbai-based OxyGreen Constructions Pvt. Ltd. provides following technologies in co-operation with its principles from Malaysia, China, Belarus and Germany:
• TAAL Aluminium Formwork System
• Aluminium helipads with fire retardant system
• Solid wooden villas
• Ultra-luxurious glass-wood villas.
Commenting on the advantages of TAAL aluminium formwork systems, Samit Patil, Managing Director, OxyGreen Constructions Pvt. Ltd. says, “500 clear repetitions are possible with TAAL aluminium formwork system. Its high quality material- Aluminium Alloy 6061-T6 is derived from original aluminium billets and ingots and all its material undergoes vigorous quality checks.”
TAAL presently has a factory of its own measuring 2,00,000 sq.mt and another 6,00,000 sq.mt factory being constructed. TAIAO is one of the leading companies in the world to manufacture aluminium helipads with retardant system and the only company in Asia. It exports 90 per cent of its products all over the world from China and Malaysia with future plans to expand in deeper Asia and Latin America.
“The industry is seeking greater takers for aluminium formwork for column beam- slab casting and for easy-to-use and economical craneless systems. Also there are revamped versions of Alvert for vertical casting and Aludek for horizontal casting with drop head methodology, which offer a smooth finish and a cycle of five to seven days. These systems then can be used in slab with beam grids,” shares Mr Kalantri.
Mr Udeshi says, “Development from traditional formwork systems to latest formwork systems was very fast, one system replaced by another with advanced techniques and new and different usage methods. The various systems such as Cuplock, H-Frame, APS unit, tubes and fittings, props and spans.” He said, Mivan, Doka, Peri, Paschal, Zurich are some of the popular for developing above systems.
NOE Formwork India Private Limited shares some latest technology trends in system formwork, they are as follows:
• Minimum number of tie-rods
• Minimise number of panel connections
• Less number of formwork pieces per unit area (m2)
• Lower weight of formwork
• Higher single-pour height
• Larger panel area
• Enhanced facing of formwork with use of synthetic ply for higher quality and higher usage / repetitions
• Repair ability of formwork facing: Birch Ply and Synthetic Ply can be easily repaired, and further reused
• Higher flexibility and modularity of formwork
• Ease of stripping
• Ease of attaching accessories
• Highest safety (fulfilling stringent DIN/EN norms)
• Higher panel symmetry.
Solutions offered
There are a bagful of growth drivers. Construction in India is growing in all sectors, need of speedy and quality construction, labour scarcity in key areas of construction, extensive usage of concrete pumps and safety requirements. These drivers necessitate the introduction of new technologies in almost all areas of construction. There are number of opportunities for advanced formwork systems in India. The demand is growing as there are several projects going on in various sectors and many more are expected in future.
Some solutions offered by NOE Formwork India Private Limited are as follows:
NOEtop large panel formwork system with integrated strong back:
• Versatile system
• Multiple choice of tie positions
• Optimal size module
• XXL
• No marks
• Standardised
• Reduced number of system components
NOE modular circular formwork system:
• NOEtop R 275 Circular Formwork
• NOE R 110 Circular Formwork
NOE prop aluminium support system (patented clamp).
Mr Udeshi says, “In present days aluminium formwork systems are very well-known for doing construction of large areas of similar design, similar types of construction for affordable housing or high rise building having same style of construction and design, but it requires deep planning while procuring the aluminium formwork to get minimum procurement quantity provides repetitive of usage and avoid extra procurement or increase unreasonable of cost.”
“MFS Aluminium Formwork Systems and MFS Steel Scaffolding Systems offer formwork solutions and services for construction and maintenance industry and are known as complete solution provider in the respective industries. It includes basic to advanced aspects of formwork and scaffolding components which can cater the need of forming any modern structure. Aluminium formwork systems, steel scaffolding systems and access scaffolding are the front line products,” shares Mr Sharma.
Commenting about the solutions preferred by Dighi Port, Mr Kalantri comments, “Industry experts are unanimous in their views that all the big projects, which used to have a time frame of 2 to 3 years, are now being completed in 18 to 22 months. The movement of the construction industry towards modernisation and mechanisation is a key factor. Secondly, contractors are time bound and face scarcity of labour. Since projects are time-bound these days, quick and timely completion is a major criterion. Scaffolding and formwork plays a major role in addressing these issues.”
Speaking more about the product details he says, “Globally, Topec slab formwork is widely used for construction. It is a simple, lightweight aluminium formwork that can be safely handled by three men, without a crane. Significant reductions in cost and increase in productivity can be achieved as compared to conventional table forms because safe erection and dismantling can be done from the ground and Topec’s large 1.8 sq.mt panels can quickly cover areas and support slab thicknesses of up to 400 mm. Smaller panels can be used to support thicker slabs of 500 to 750 mm. Topec needs no secondary or primary beams and clamps. Its main components are simply panels, props and bearings. Panels can be supported by tubular steel props with quick release mechanism propping heights up to 3.5 m are possible.”
Rent or buy?
Many companies provide the required formwork system to the customer on rental basis. This helps the customers in adopting the modern system for their projects, but at a cost budgeted for that specific project only.
“Interestingly, the rental option is turning about to be feasible,” shares Mr Kalantri. Further he says, “On the customers’ part, this also ensures maximum utilisation of the system with no provision required for carry over cost at the end of the project. On the other hand most of the top players in construction industry have formed a separate scaffolding and formwork division in their organisations by realising the importance of the system and its optimum utilisation.” Builders and contractors want to bring down the investments on scaffolding and formwork and are therefore happy to hire the systems at feasible rates for a stipulated time. People are opting for rentals in order to curtail investments and storage costs.
Mr Udeshi states, “Deep planning is required to buy the formwork or renting it as it involves cost and storage space, maintenance and can be useful in future projects.“
For Purchase
• Required for continuous or big projects and duration for completion are very short.
• Constructions of similar design work so that we can use for maximum repetition.
• Having sufficient facility to store and skilled staff to maintain the same in best possible manner.
• Having clear calculation of costing and profitability by using these systems.
For rent
• Mid-size project, no immediate chances of repetition and even break-down are rare.
• No storage facility and skilled staff to maintain the same.
• Designs of constructions are different and not possible to accommodate in present stock.”
“Selection between buy and rent is majorly influenced by factors i.e. size of project, time period for which material is required, percentage of non-standard and special material required etc. Though in rental option high initial investment of user is avoided but if period of rent is more then this option is not viable,” shares Mr Sharma. Rental option has advantage of initial cost minimisation and ensures maximum utilisation of scaffolding and formwork system without provision of carrying forward the cost at the end of project. He further adds, “With modern trends where projects are launched in series, strategies and planning should be made for long run and considering huge number of repetitions which any formwork system can withstand, major consideration should be given to buy the formwork system which can be treated an asset .”
“Though initial investment is higher in any aluminium formwork system but considering repetitiveness of formwork, quality end results, avoiding entire plastering, safety features and less dependency on skilled work force option to buy aluminium formwork system is a viable option,” says Mr Sharma.
“As greater numbers of construction companies set their priorities for success, opportunities will continue to grow for providers of formwork and scaffolding,” Mr Kalantri concludes.
Image courtesy: NOE Formwork India Pvt. Ltd.
Cookie Consent
We use cookies to personalize your experience. By continuing to visit this website you agree to our Terms & Conditions, Privacy Policy and Cookie Policy.