CE maintenance tips for enhanced uptime
By Edit Team | May 8, 2021 6:00 pm SHARE
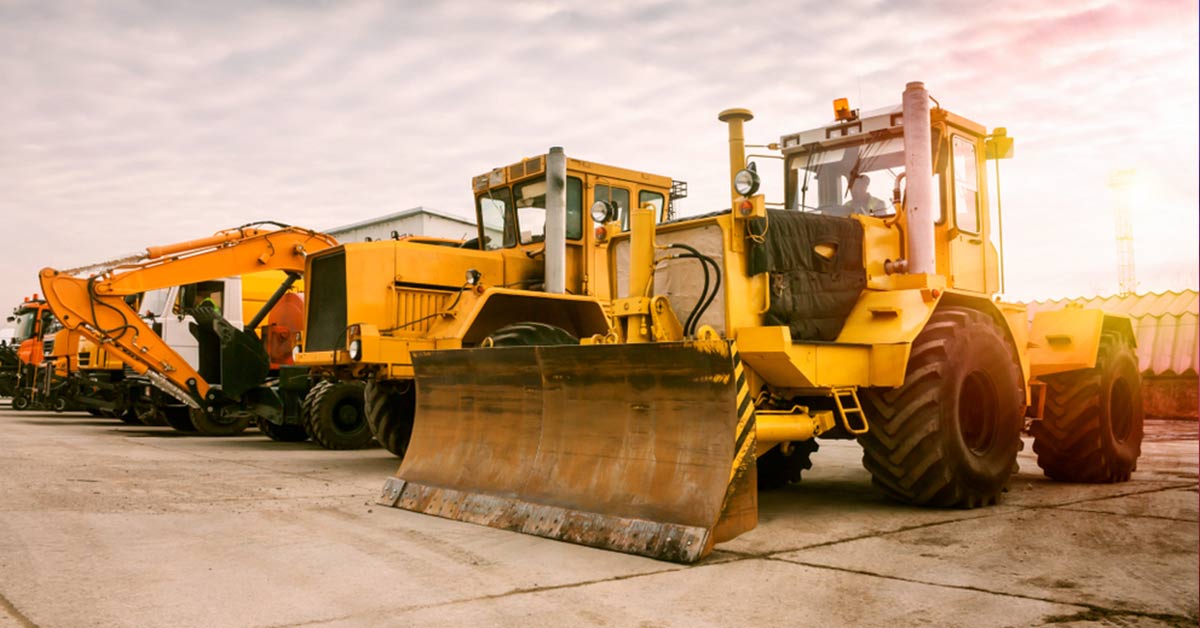
Regular maintenance of construction equipment (CE) plays a pivotal role in the equipment uptime resulting in enhanced productivity and cost efficiency. Industry leaders discuss the key factors involved in effective CE maintenance.
Indian construction and mining sector has seen many small, medium and big projects being undertaken in recent times. At a time when the contractors are dealing with stringent quality parameters and tight execution deadlines, it is imperative for them to have optimum utilisation of equipment during the project execution.
Crucial for machine uptime
How important is regular and timely maintenance of construction equipment and machinery? The best answer to this question can be what Naresh Thakur, Head – Training Department, L&T Construction & Mining Machinery, says. “It will be a surprise when we say that around 70 per cent of all troubles on machines is a result of inadequate maintenance. And therefore, if we have to extract the best of the machine, we have to focus on maintenance.”
Construction and mining equipment operate in extreme conditions as they encounter rough terrains, rocky underfoot conditions, greatly varying temperatures and humidity, and long working hours. These factors take adverse impact on the equipment and without timely maintenance, can wear the machine components.
When we talk about faster construction of roads and highways, and other infrastructure projects, the role of construction equipment (CE) becomes crucial. And for the seamless execution of projects within the timeline, effective maintenance of CEs is the need of the hour. Periodic maintenance of construction equipment reduces equipment downtime, lowers overall operating costs, and increases overall productivity. Regular repairs and upkeep prevent parts and components from excessive wear and tear and sudden failure.
Dimitrov Krishnan, Managing Director, Volvo CE India Pvt Ltd, says, “Timely maintenance ensures the ready availability of machines and predictable levels of operational efficiency. It also helps in parts planning and optimised inventory management. Construction equipment are expensive assets and need to be maintained with care to ensure longevity and return on investment.”
Construction and mining equipment encounter rough terrains, rocky underfoot conditions, greatly varying temperatures and humidity, and long working hours. In such conditions, “adopting a disciplined regimen of proper lubrication and maintenance for all the components is essential along with regular cleaning after a day’s work,” says Sandeep Mathur, India CE – Brand Leader, Case India.
Hridesh Kumar, Business Development Manager (Aftermarket & Asphalt), Dynapac Road Construction Equipment (India) Pvt Ltd, also highlights the importance of regular maintenance of CE for uptime as he says, “It is highly imperative in today’s construction equipment fleet management that you need to have optimisation of the equipment, fuel consumption monitoring, preventive maintenance strategies, and equipment utilisation. This is of utmost importance for all those are involved in the process.”
Large construction contractors have a vast range of equipment working at multiple projects across various parts of the country. According to PK Thakur, VP – Plant & Equipment, GR Infraprojects Ltd, handling a large fleet of equipment spread across the country is a challenging task. Also, today a range of specialised and advanced equipment are being used. Providing them a rationalised and optimum maintenance is daunting task. “Expenses of plant and equipment are categorised into three segments: fuel cost, plant and equipment manpower cost and the real maintenance cost. If we holistically compare these costs, it is found that 13-14 per cent of the total turnover of the company comprise these expenses,” he adds.
Replacement of critical parts
All components will have a fixed amount of life and the life will depend on the application, duty cycle, load factor, the surroundings, etc. Changing critical parts and components at regular intervals is of utmost importance to avoid unplanned breakdown of machines and equipment while at work. Ready availability of parts and components in time will save from the machine breakdown and thus saves on loss of time and money.
Safety critical parts is of crucial importance in maintenance processes. Naresh Thakur says, “These are certain parts like the fuel line, the suction hose, and travel line hoses, which is not visible but when it fails, can cause major damage to the machines. And therefore, these are the items, which are mentioned in the operator manuals of all OEMs, and if you are a user, please focus on the replacement of these items.”
New developments in CE maintenance
Routine maintenance and preventive maintenance are the two major methods followed by companies for the upkeep of their construction equipment, according to Krishnan. With the emergence of new smart technologies like big data, artificial intelligence (AI) and internet of things (IoT) in CE, predictive maintenance methods are gaining importance today. “New-age digital technologies and connectivity now allow us to keep track of machine conditions and performance round the clock and on the go. Machine owners and project personnel have ready access to vital reports on the progress of work in their sites,” says Krishnan.
Naresh Thakur adds, “When we talk about preventive maintenance, 80 per cent of the time that people spend today at sites is focusing on preventive maintenance and the balance is attending to failures. This is where we need to bring about a shift the way we think.”
Mathur highlights the importance of predictive maintenance in the upcoming market scenario, “With predictive maintenance, customers can reduce downtime, save any additional repair cost, keep the machine up to date and maintain its performance and delivery in a category where machines face heavy wear and tear, predictive maintenance is of paramount importance.”
“With predictive maintenance, the expected time of failure of critical aggregates and components can be reasonably estimated well in advance. This helps in obtaining such items just-in-time,” Pawan Kumar, Chief General Manager & Marketing Head, BEML Limited, points out.
Monitoring and ensuring utilisation of maximum units of assets, very strict monitoring of operators, efficient dispensing of fuel, monitoring of fuel consumption and stop pilferage of fuel, and timely preventive maintenance are the major challenging tasks in construction projects. In order to meet these challenges, GR Infraprojects partnered with Moba Mobile Automation to develop a comprehensive digital solution, Site-Matics.
Dynapac offers its telematics system, the Dyn@ Link which can help the customers in the whole monitoring and control of the equipment. “The site managers can track the use of the machine efficiently. They will be able to see kind of productivity these machines are giving, and they can monitor the machines in the day today activities. The site maintenance team will get timely pointers to the preventive maintenance and services and will be able to ensure that all the parts are available in time. So, the uptime of the machine is maintained,” adds Hridesh Kumar.
Skill development matters
A skilled person can operate the equipment or machine at its optimum efficiency as he knows each and every aspect of the machine. Similarly, a skilled maintenance person can maintain the equipment effectively as he knows the machine and the parts and technologies associated with the machine. So, it is imperative for the operating and maintenance personnel to be skilled for the job. As Krishnan says, “The life and value of a machine are in their hands. It is therefore imperative to equip operators, technicians and mechanics with knowledge and skills related to machine operation and maintenance.”
Mathur points out the importance of skill development, “To an extent, every machine is only as good as its operator. Lack of training also means that operators may overwork a machine beyond its capability resulting in downtimes due to frequent service requirements.”
Naresh Thakur is of the view, “Maintenance requires a lot of discipline. Training, motivation of the people who are doing it and giving them the importance plus somebody accompanying him show the right way to do it. This will help you extract the best out of these equipment.”
Meeting the challenges
The industry is now transforming from traditional maintenance practices to technologically-driven digital monitoring processes. “The need of the hour is to ensure maintenance of expensive assets like construction equipment are entrusted to those who know their job. Technical training, competency development and adoption of best maintenance practices in handling next-generation machines is one way forward,” Krishnan suggests.
For better maintenance practices, Pawan Kumar lists out the following, “Strictly adherence to maintenance schedules prescribed by OEMs; To impart training to the maintenance staff of customers; Spontaneous corrective action for the signals/indications given by the warning alarms; To adopt GPS-based preventive maintenance solutions; Smart wear to guide technician with step-by-step instructions during repair work; and Adopting AI-based predictive maintenance tool.”
According to PK Thakur, people should use centralised lubrication system because it saves a lot of time. “The current Covid time is very challenging for us from maintenance perspective as we are facing manpower shortage and we have to preplan for the parts and components in time at various project sites. In this scenario, we need to have more mechanised solutions for maintenance and digitalisation will definitely help to overcome many of these challenges,” he concludes.
Cookie Consent
We use cookies to personalize your experience. By continuing to visit this website you agree to our Terms & Conditions, Privacy Policy and Cookie Policy.