Disc Brake Maintenance
By Edit Team | January 28, 2013 7:09 am SHARE
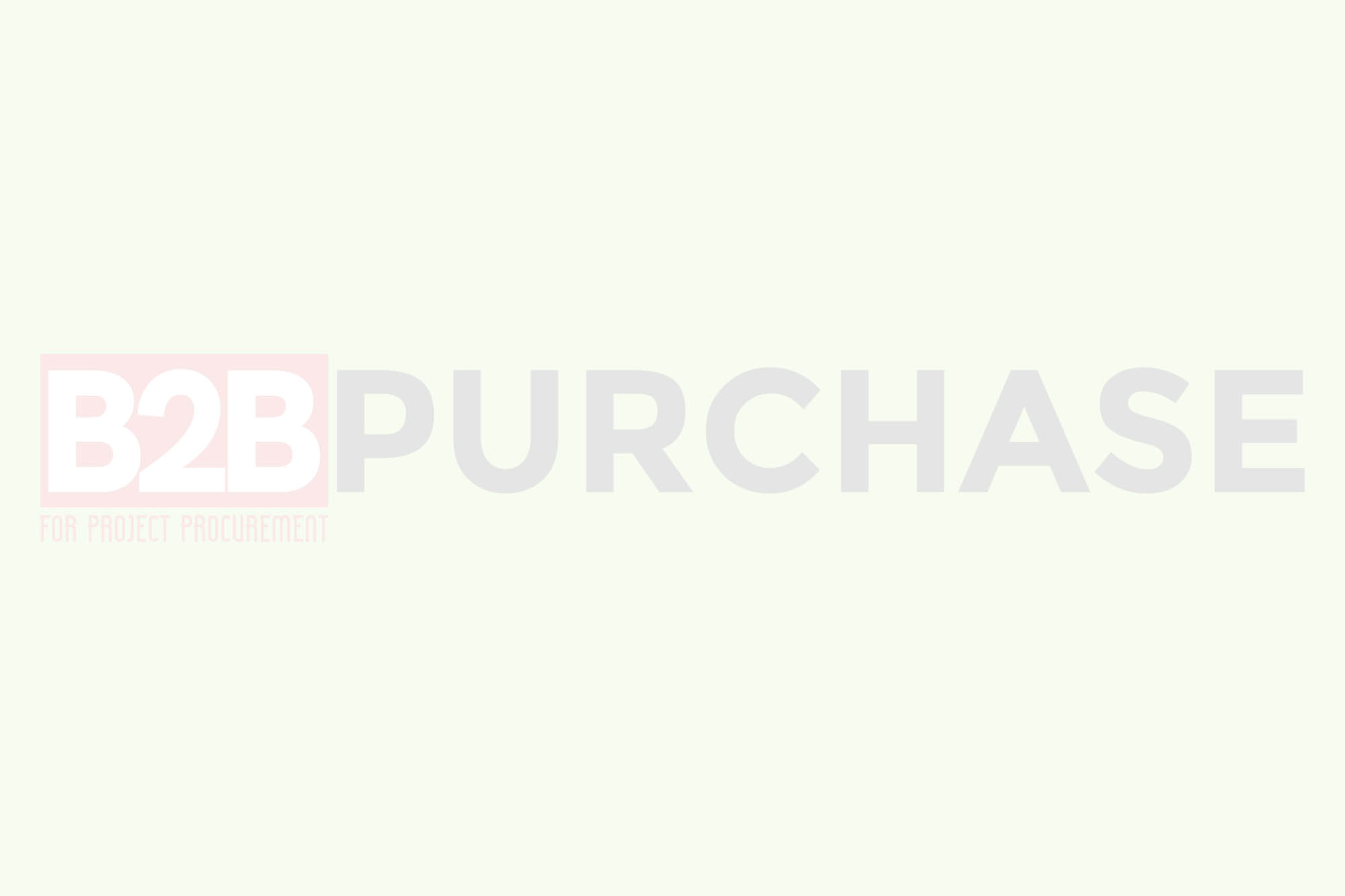
Are you confident that whenever you put your foot on the brake, the machine you’re operating will stop? Keeping brakes in good working condition is essential for safe machine operation. The only way to ensure that your brakes will be there when you need them is to follow a thorough maintenance program.
Construction and mining equipment use a variety of brake system types -drum, dry disc, wet disc and hydrostatic. Dry disc brakes are popular on a widerange of machines including front–end loaders, articulated haulers and rigidframe haulers. Although similar to the type found on most automobiles, these disc brakes are considerably larger.
A disc brake consists of a disc, or rotor, which rotates with the wheel, and a stationary caliper which holds the brake pads or linings, hydraulically actuated pistons press the linings against the disc. This causes friction and heat energy which stops the disc and machine.
Disc brake enemies include dirt, heat and water in the air or hydraulic system. Spend a few minutes checking the brakes at each, wheel, and you’ll save considerable money and downtime if the brakes need to be overhauled or the disc replaced.Brake maintenancePerforming a weekly or monthly brake system inspection is a simple, cost effective way to avoid larger, more expensive problems in the future. Also, since you rely on brakes in an emergency, the few minutes spent at each wheel may prevent injury and machine damage. See the chart on Troubleshooting Disc Brakes.
Depending on machine type, visually inspecting the brake(s) and disc is usually fairly easy. Check the linings for severe or abnormal wear. A taper or worn spot in one area means the brakes have been severely used (many frequent high-speed stops) or abused (operator riding the brakes) and the lining should be replaced.
At the end of a shift, if a walk–around inspection reveals one or two discs are cooler than the other disc, investigate to find out if all brakes are operating properly. Measure discs with deep grooves or wear marks to make sure they have not worn past the manufacturer’s specified minimum thickness. If material is available, the discs can be turned. This is usually less expensive than buying new.
If the disc is too thin and the linings worn, the linings could fallout, resulting in complete loss of brake power. Cracking or discoloration of the disc means the brakes have seen excessive heat. This could be due to a faulty component in the air or hydraulic system, or the operator may be riding the brake pedal.
Wash dirt, sand and mud from around the disc and brake to prevent linings and discs from wearing abnormally fast. Wash more frequently in harsher environments. Look for wet oil on the brake or wheel possibly indicating a loose fitting, bleeder or hose problem.
Finally, don’t forget the hardware. Tighten loose and replace missing nuts and bolts.System maintenanceBrake system actuation types include straight air, air/oil and full hydraulic. Follow the manufacturer’s recommended intervals for maintaining these systems.
A leaking hydraulic hose can run the brake system dry or down far enough to prevent the brakes from applying properly. Fluid loss calls for an inspection of all system lines and fittings. Before going into the brake, always check the lines first. Tighten and repair as required and replace any lines or hoses that are kinked, dented, cut or bent.
If you find a leak at the brake, determine whether it is external (fittings, bleeders) or internal (piston seals). Leaking piston seals or cap seals usually mean major brake repair (off the vehicle) is necessary.
Water and dirt contamination is a major problem for all brake system types. Water can freeze and corrode components in air systems and contaminate full hydraulic systems. Any dirt that gets into the air or hydraulic system accelerates wear on seals and rubbing surfaces.
Follow the manufacturer’s recommended fluid specifications and maintenance schedules regarding cleaning and replacing filters. Make sure the various brake valves in the circuit are adjusted properly to the manufacturer’s pressure(s) and other specifications. Too much pressure can lead to accelerated wear and early failure of brake system components. Too little pressure can cause insufficient brake torque and an excessive stop distance in an emergency situation.
RetardersMany construction and mining machines have a retarder as standard equipment to assist in the braking effort. Construction equipment and smaller mining machines typically use an engine or hydraulic retarder in the transmission. Large surface mining trucks with diesel electric propulsion systems use electric motors for retarding capability.
Retarding systems usually do not have any wear components. When properly used, these systems are effective and can save considerable wear and tear on the brake system. The service brake system can then be used for its most important functions – low-speed applications and emergency situations.
To ensure proper brake use and function – and to extend brake life – make sure operators are adequately trained.
Replacement partsReplace brake system components with parts meeting the manufacturer’s specifications. Using components that don’t meet the brake manufacturer’s specifications may result in loss of braking ability and possible injury or damage.Linings are the most important brake component. They determine the stopping capability of the machine and have a direct impact on the life of internal brake components such as seals, backup rings and pistons.
Many raw materials are used in friction materials for disc brake linings. Organic linings can contain a variety of ingredients such as asbestos, graphite, brass, lead, aluminium and rubber. Semi-metallic or semi met contains metal particles bonded together by pressure at elevated temperatures. Each unique lining material has its own set of wear and performance factors. Without strict quality control, linings containing the same ingredients can performand wear completely differently.
Make sure your replacement linings meet the manufacturer’s specifications for coefficient of friction (stopping capability), heat transfer properties and wear characteristics. Some sintered metallic and semi-metallic linings may transfer excessive heat to the brake’s rubber components causing seal and piston damage, and possible brake fluid vaporisation.
Most friction material is chemically bonded to the carrier or back plate. Some suppliers use rivets.
Choose carefully to avoid using linings that wear prematurely, gouge the disc or chunk off. Downtime and lost production should be considered when calculating the cost of replacing linings.
For more effective braking, don’t mix new and used linings in the same brake and don’t use two different lining materials in the same brake. Also, many disc brakes require the use of hardened carriers. If lining assemblies with inadequate steel carriers are used, the pistons can actually imbed themselves into the carrier possibly destroying the brake.
After putting on new linings, burnish the new material following the lining or equipment manufacturer’s procedure. Burnishing conditions the lining to function effectively at various temperatures. A burnishing procedure usually calls for a number of brake drags and stops to elevate the friction material temperature.
Make sure seals and rubber components, such as boots, are the right size and are compatible with the brake system fluid. Boots protect the seals and the surface of the pistons from mud and water contamination. If you have to replace a leaking piston seal, replace all rubber components at the same time. That way you won’t have to bring the machine back into the shop to replace another bad seal or torn boot after a short period of time.
Brakes are an essential part of mobile equipment. To ensure continued, safe operation, adopt a complete brake maintenance program following the manufacturer’s recommendations for periodic inspections. Do that and you can feel confident that your brakes will be there when you need them.
Carlisle Brake & Friction Headquartered in Solon, Ohio, with over 1,800 employees worldwide with manufacturing facilities globally located in the US, UK, Italy, India, China and Japan. Carlisle serves over 100 leading original equipment manufacturers in 55 countries, making Carlisle the right choice for your new brake or friction design, no matter where you are in the world or what you want to be.
Cookie Consent
We use cookies to personalize your experience. By continuing to visit this website you agree to our Terms & Conditions, Privacy Policy and Cookie Policy.