EPDM Gaskets: An integral part for any window system
By Edit Team | January 5, 2016 6:29 am SHARE
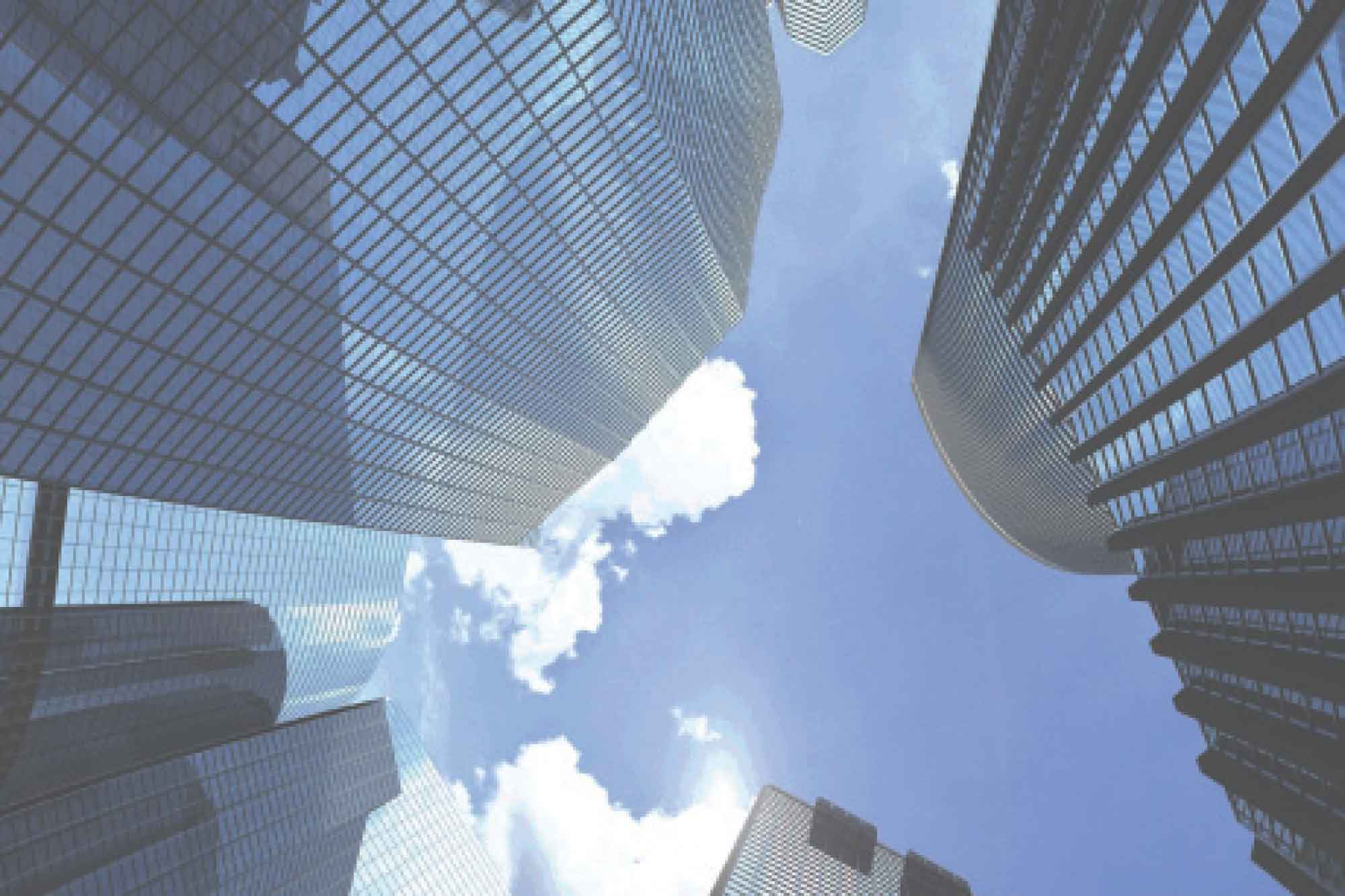
An article by AviGiri to raise awareness on gasket properties, manufacturing techniques and standards to ensure that the customer makes an informed decision while purchasing rubber gaskets
Gaskets are the least visible part of the window, and are often misconstrued as the least important part as well. However, this cannot be further away from the truth. AviGiri seeks to shed light on this matter, and inform fabricators, builders, and architects of the importance of using high-quality Microwave Cured EPDM Gaskets in their respective window systems.
Many of the features that window manufacturers boast about such as: sound-proofing, temperature insulation, and energy efficiency are in fact directly related to the accurate fitment of the gaskets. So why then is there a trend to spend uncompromisingly on high quality aluminium or uPVC channels, the most advanced glass technology, and utilising the best accessories, while simultaneously maintaining a complete lack of interest in the quality of gaskets associated with the final product? This occurs not because of a deliberate avoidance of the quality of gaskets, but due to the wide variety of gaskets available in the market. A summary market-analysis will reveal that a fabricator may purchase gaskets from as low as Rs. 40 per Kg up to Rs.250 per Kg. The question arises is which is the best?
The key is to look into the manufacturing process involved and the standards that are maintained. This succinct article seeks to raise awareness and build on a theoretical understanding of the differences caused due to the various manufacturing techniques of gaskets. How the gasket is cured will determine its tensile strength, durability, and ability to withstand temperature and ozone conditions. A quality gasket will not crack even after many years, which otherwise could be disastrous to the reputation of the window manufacturer. Imagine the warranty on a state-of-the-art window system being void because of the failure of the gasket!
Microwave-Cured EPDM Gaskets
EPDM- Ethylene Propylene Diene Monomer, is a synthetic rubber that was developed solely for outdoor application. Therefore, this has widely been accepted as the only form of rubber used in the construction industry. Only when the highest grade of EPDM is sourced, can the final product guarantee its quality. However, simply sourcing high quality EPDM will not suffice. Many chemicals are involved in the manufacturing process, and for these chemicals to interact in a desired manner depends on the manufacturing technique and the standards followed. The widely accepted gasket manufacturing standards are the DIN 7863 standard and the ASTM C864 – 05 standard. Adhering to these Standards automatically ensures that one receives a quality gasket product.Simultaneously, there are two types of curing techniques: The conventional Steam-Cured (Autoclave) Technique and the more superior, Microwave Cured Technique.
Microwave curing is done through a Continuous Vulcanisation Line, the advantages of which are:
• No dimensional variations
• No impurities due to use of fillers
• Higher quality compound and raw material used.
This manufacturing process along with following the above mentioned standards ensures that the gaskets have the following properties:
• High resistance to ozone, weathering, and abrasion
• Temperature resistance from -40 C to +140 C
• Resistance to UV radiations.
Only microwave cured EPDM can be guaranteed for a minimum of 10 years, promising:
• No cracks
• No discolouration
• No loss in tensile strength.
Authored by-
Avinash Pai
Business Development Manager
Mob: +91 9980 223 200
Email: apai@avigiri.com
Avigiri Urethane and Rubber Industries Pvt. Ltd.
Cookie Consent
We use cookies to personalize your experience. By continuing to visit this website you agree to our Terms & Conditions, Privacy Policy and Cookie Policy.