Everest Engineering set to launch India-made GJJ Passenger Hoist next year
By Edit Team | January 6, 2024 1:53 pm SHARE
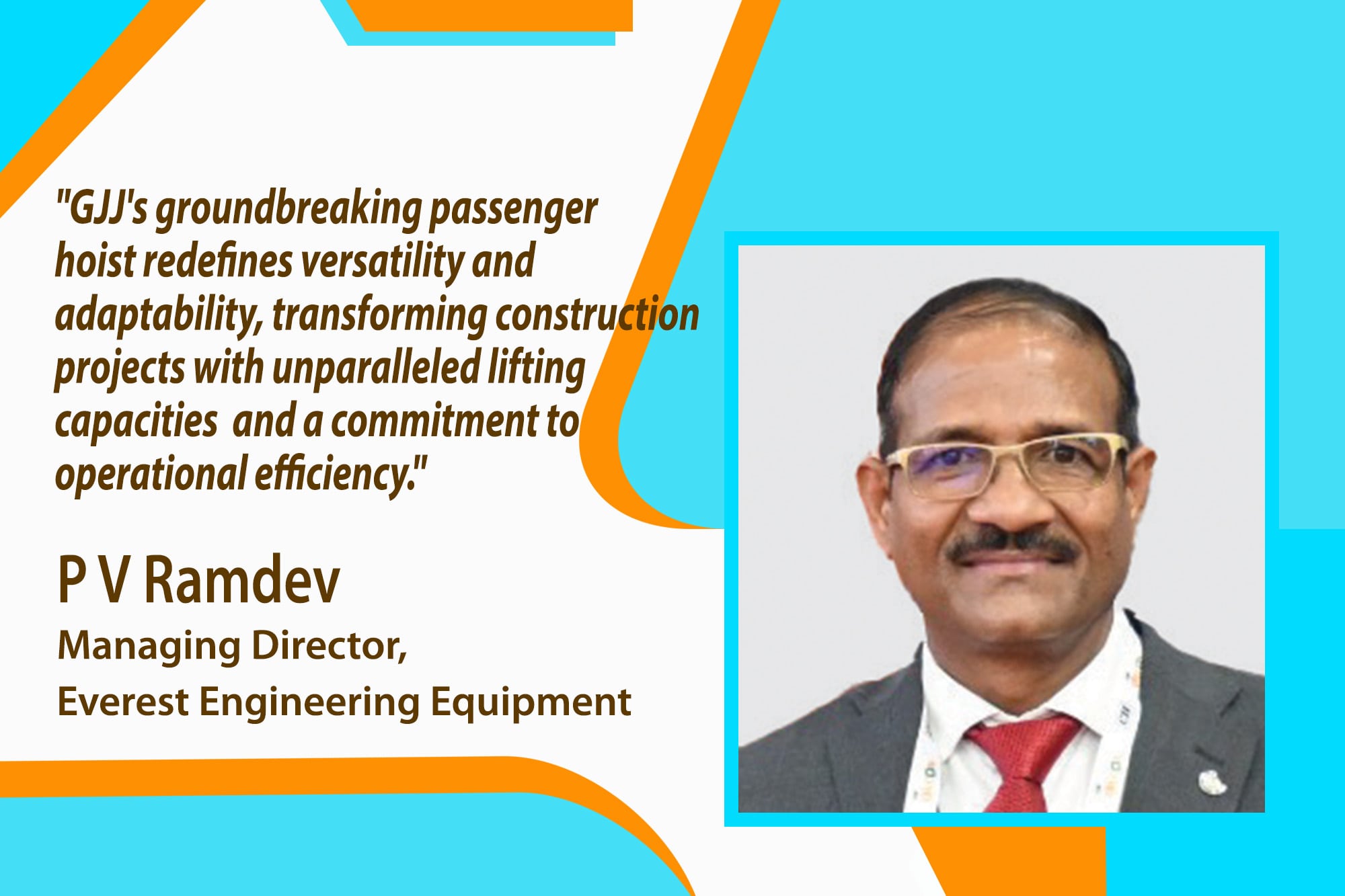
P V Ramdev, the Managing Director, and Shanker Raj, the CEO of Everest Engineering Equipment, shed light on the innovative strides and collaborative efforts driving the success of their groundbreaking passenger hoist in the construction industry.
What is the weight capacity of GJJ’s groundbreaking passenger hoist, and how does its adaptability contribute to its versatility in construction projects?
P V Ramdev: GJJ, a globally recognised brand, proudly unveils its revolutionary passenger hoist that combines passenger and material lifting capabilities. This innovation sets a new standard in the world market, distinguishing itself as the largest hoist ever designed. Operating on a single vertical mast section, the hoist boasts a remarkable 3.2-tonne capacity and offers versatility by seamlessly accommodating multiple capacities, including 2.7 tonnes.
What sets this hoist apart is its adaptability. When utilised at its maximum capacity of 3.2 tonnes, it achieves a speed of 46 meters per minute. Alternatively, with a slightly reduced load of 2.7 tonnes (only 500 kilograms less than the maximum), the speed escalates to an impressive 63 meters per minute. The flexibility doesn’t end there – the hoist’s length, initially four meters, can be adjusted to 3.6 or 3.2 meters, providing diverse configurations tailored to specific project requirements.
Notably, the hoist can comfortably carry 38 people or 3.2 tonnes at full capacity. With a 2.7-tonne load, it accommodates 32 people on the reduced tonnage. This adaptability makes it an invaluable asset for various construction projects.
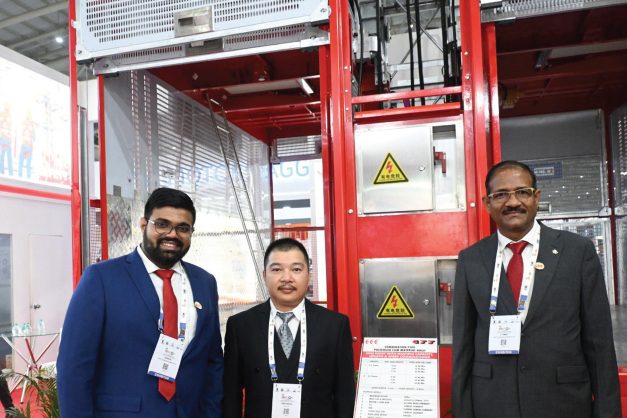
Can you elaborate on the joint venture agreement with GJJ for production in India and the collaboration with Everest Engineering?
Shanker Raj: The culmination of this momentous achievement was marked by an inauguration ceremony graced by Mr. Christopher Liu, a distinguished guest from GJJ USA and the registered brand owner of GJJ worldwide. The journey to introduce this product spanned two years, driven by meticulous testing and validation processes adhering to stringent European standards.
Adding to the excitement, a joint venture agreement with GJJ has been established to initiate production in India. In collaboration with GJJ, Everest Engineering aims to commence production in 2024, promising an Indian-manufactured GJJ passenger hoist. The venture underscores the commitment to delivering quality products globally, enhancing the accessibility of this cutting-edge technology to various countries. The stage is set for a new era in construction technology, marked by the fusion of innovation and adaptability. Initially, the volume was very low. It is 120 units per year, and our production facility can produce up to 1800 units yearly. That much capacity is there. Some major components will be supplied from GJJ initially, and slowly, we can produce everything in India.
What is the potential for GJJ’s groundbreaking hoisting solution in the Indian market, particularly in industrial segments like steel plants and cement plants?
P V Ramdev: The potential for this groundbreaking product in the Indian market is substantial, particularly in the industrial segments. Over the past 2-3 years, there has been a significant demand for a hoisting solution with extended length and increased lifting capacity, particularly in steel and cement plants. Responding to this demand, our R&D efforts began four years ago, culminating in the recent launch of this innovative equipment. The Indian market shows a keen interest, especially in applications requiring substantial height and lifting capabilities for permanent structures. However, the product’s appeal extends beyond India, as GJJ has a global reach. With numerous manufacturing plants worldwide, GJJ will strategically decide which plants will cater to the needs of each country, and our plant is poised to be a key contributor to meeting this demand.
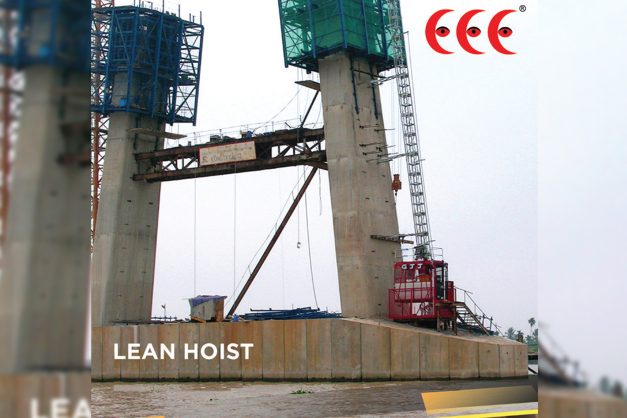
How do modular components contribute to operational efficiency and sustainability, mainly when project requirements vary?
P V Ramdev: Our company is committed to ensuring operational efficiency and sustainability in our products, focusing on reducing the industry’s metal usage. While constructing equipment from alternative materials like plastic is a desire, it must still be attainable. Instead, we’ve devised a competitive approach tailored for industrial segments. Rather than purchasing multiple units, our innovative strategy involves offering modular components. For instance, if someone requires a four-meter cage, the next project may not, making the previous machine obsolete. Through collaboration with GJJ, we aim to mitigate the need for frequent equipment replacements, thereby minimising metal consumption. Our concerted efforts align with a broader initiative to promote responsible resource usage, advocating for reduced consumption of natural resources, including metals in an environmentally sustainable manner.
How does your company stay updated on market innovations, and how does the collaboration between your in-house R&D team in India and GJJ contribute to this?
Shanker Raj: Staying abreast of market innovations is integral to our company’s ethos, and we accomplish this through our dedicated in-house R&D team in India, working collaboratively with GJJ and introducing our latest machine-involved strategic decisions to uphold customer continuity. A key consideration was retaining the existing mast sections that our customers were accustomed to, preventing the need for a complete overhaul of their equipment. Changing mast sections would have forced them to invest in an entirely new machine. Thus, our goal was to maintain the familiarity of the mast sections while achieving a new target: a four-meter cage on the same platform with a three-by-two configuration.
This posed a significant design challenge, as we had been supplying machines with twin cage bases or single cage bases on the 650 x 650 runnable mast section. The challenge lay in adapting this existing framework to accommodate the desired 3.2t with 4 meter-long cage. Our digital and design teams successfully navigated this challenge through collaborative efforts, ensuring the product’s integrity and meeting our innovation goals. The result is a testament to our commitment to technological advancement and customer satisfaction, aligning with our longstanding tradition of supplying reliable and adaptable construction equipment.
Cookie Consent
We use cookies to personalize your experience. By continuing to visit this website you agree to our Terms & Conditions, Privacy Policy and Cookie Policy.