Uncover how UltraLabs stays at the forefront, ensuring services consistently meet or exceed industry standards.
What is your primary focus in the construction and infrastructure sectors?
Our company specialises in blending and supplying lubricants, focusing on serving the construction and infrastructure sectors. Since 2014, we have extended our offerings to include Ultra Laps, an offshoot of our primary operations. Our clientele primarily consists of major mining and custom construction players, including original equipment manufacturers (OEMs) in mining. We provide comprehensive oil analysis solutions, allowing our customers to submit oil samples for testing. Our detailed oil analysis reports offer predictive insights that empower our clients to anticipate and prevent potential failures. This predictive approach enhances equipment performance and translates into significant cost savings for our valued customers.
Talking about the on-site test kit, how does it align with your customer’s current needs in the construction and infrastructure sectors?
We are dedicated to showcasing cutting-edge technologies that provide added advantages to our customers. This year’s highlight is our on-site test kit for biodiesel content in diesel. This innovation allows customers to test biodiesel levels conveniently without sending samples to a laboratory. The on-site test kit streamlines the process, saving both time and costs for our clients. We take pride in continually introducing new solutions that enhance efficiency and empower our customers with the latest advancements in the field. Our commitment to innovation reflects our ongoing efforts to meet and exceed customer expectations.
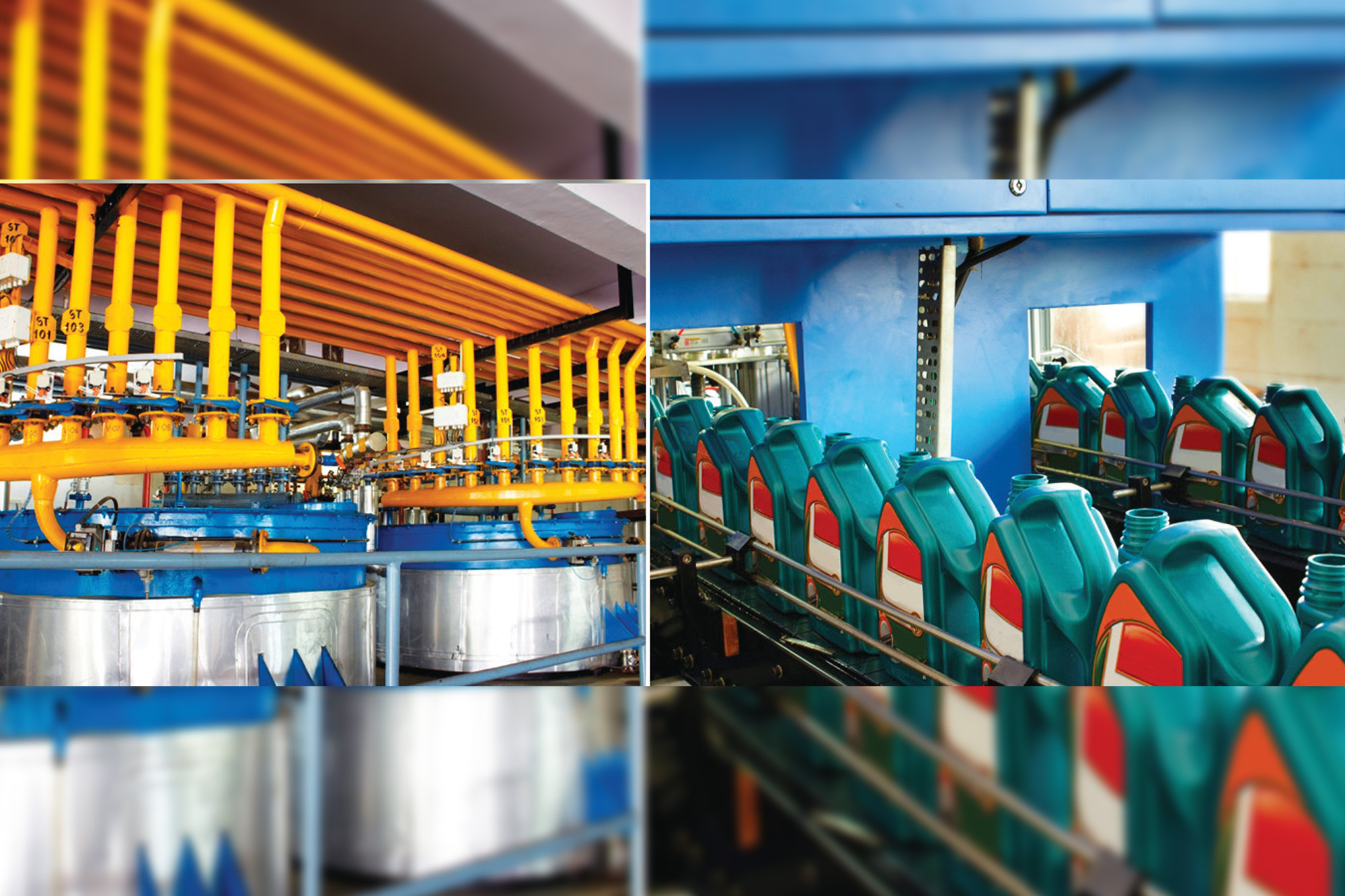
What steps do you take to ensure that your company remains agile and adaptive to the fast-paced nature of technological advancements and industry changes?
Our commitment to staying at the forefront of innovation stems from a close relationship with our customers, who play a pivotal role in shaping our direction. By actively engaging with them, we gain valuable insights into their challenges. For instance, the inspiration for our latest on-site test kit for biodiesel content arose from specific issues faced by some customers. Collaborating with technology partners, we addressed this challenge head-on. The result is a cutting-edge instrument capable of swiftly detecting biodiesel content. This proactive approach to problem-solving, fueled by customer feedback, exemplifies our dedication to continuous improvement. By remaining attuned to the evolving needs of our clients, we ensure that our solutions align with industry demands, fostering a culture of innovation that directly benefits those we serve.
How does your proactive maintenance strategy provide a competitive edge for your clients in the construction industry?
A paramount concern for clients is the imperative to curtail operational costs, particularly in the construction and mining sectors. Departing from a reactive stance, we advocate a proactive approach, offering insights into machine performance and health through a comprehensive analysis of fluids used in these machines. By providing proactive maintenance recommendations, we enhance machine durability, directly reducing end-user operational costs. While crucial, technology is not the sole driver; economics also plays a significant role. Incorporating economic factors ensures that clients derive tangible benefits, elevating profitability in their operations. This proactive strategy minimises equipment downtime and provides a competitive edge, directly contributing to enhanced business efficiency and client profitability.
As technology and testing methodologies evolve, how does UltraLabs stay at the forefront to ensure its services meet or exceed industry standards for accuracy and efficiency?
At Ultra Labs, ensuring accuracy, efficiency, and promptness is a fundamental commitment in all our activities to benefit our customers. We have established arrangements nationwide for swift sample collection, ensuring minimal Total Activity Time (TAT). This expedited process enables customers to receive testing results promptly, facilitating immediate action initiation. By minimising delays, we empower clients to proactively address potential machine failures, directly enhancing the efficiency and effectiveness of their operations. Our dedication to accuracy and efficiency underscores our commitment to delivering timely and reliable information that directly contributes to the success of our customers’ endeavours.
Cookie Consent
We use cookies to personalize your experience. By continuing to visit this website you agree to our Terms & Conditions, Privacy Policy and Cookie Policy.