Everest special warehouse project for Nahar Industrial Enterprises
By Edit Team | December 19, 2023 11:57 am SHARE
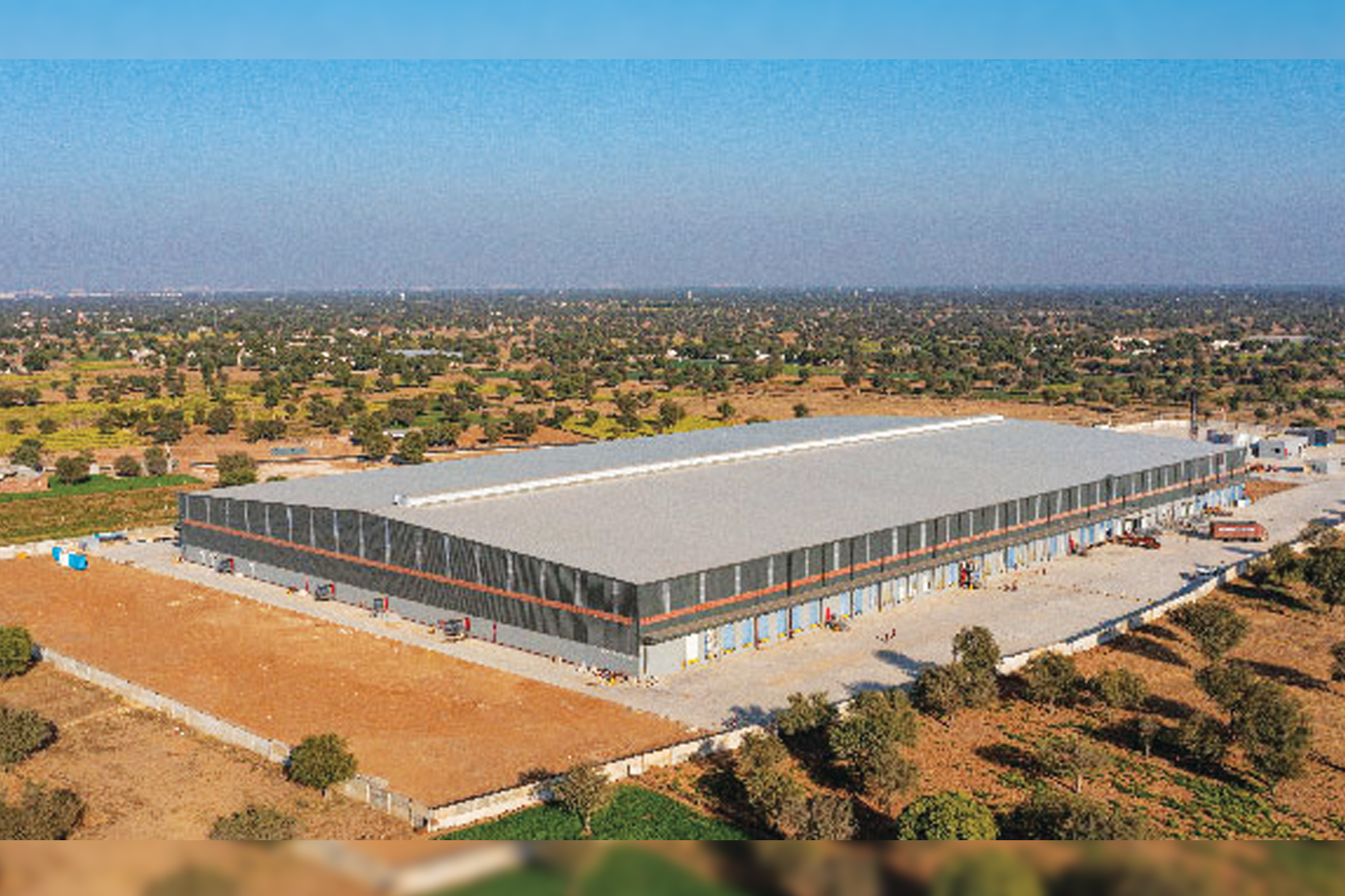
Using pre-engineered buildings (PEB) has revolutionised the construction of low-rise industrial and commercial structures. Everest has demonstrated its expertise in PEB design and execution with its latest project with Nahar Industrial Enterprises Ltd. This article analyses the architectural elements, special qualities, and difficulties encountered in building this expansive warehouse.
Pre-engineered buildings are widely used for low-rise industrial and commercial structures. The advantages of using PEB for industrial and commercial structures are multi-fold. A warehouse building is a typical low-rise structure spread across a large area and used for storing finished goods, raw materials, or other goods. The building may have an office area, utility room, etc, inside the building. A major part of the area will be used for storing and transporting goods. The type of goods will govern the storage method. Stacking and Racking are some of the common storage methods.
The design of a warehouse is governed by its layout. Clear spans and long aisles are required per the warehouse’s usage. Storage and movement of the materials inside the building govern the building plan. One of Everest’s latest projects is a Nahar Industrial Enterprises warehouse. The building is an example of a perfectly executed warehouse design and will be used as a distribution centre. A case study of the project is given below.
Project brief
Nahar Industrial Enterprises is the country’s top textile manufacturer, with other businesses under its group. The company planned to build a warehouse for its business arm that is in the warehouse business. Nahar Industrial Enterprises Ltd. is associated with Everest for executing the pre-engineered building. The customer had worked with Everest and acknowledged that Everest has a reputation for being the most reliable partner in the industry.
Everest employs advanced manufacturing processes at its plant and has adopted the latest digital technologies for material management, resource allocation, and construction management. This gave customers the faith to choose Everest. In addition to the customer’s previous relationship with Everest, the excellent customer service Everest offered made it stand out from its competitors during the bidding process.
Geometry
The warehouse has an area of over 3.5 Lakh Sqft. The width of the building is more than 130m, and it requires large unobstructed spaces for the movement of forklifts to transport goods. Everest designed a multi-span frame with optimum column spacing to achieve the layout requirements. Jack Portals and Jack beams were provided to reduce interior columns for unhindered space required for material movement inside the building.
Architectural features
The structure features a mezzanine spanning its length, with flooring made of concrete over a Deck sheet, capable of supporting human and material weight. For the lighter sections, non-composite joists were reinforced with shear studs. Addressing the client’s specific concerns about potential leaks, the building was equipped with standing seam roofing, chosen for its excellent water resistance and extended lifespan. Efficient rainwater management was ensured by installing gutters and downspouts designed to handle the expected rainfall intensity. Roof monitors and S-type louvres were incorporated to ensure sufficient ventilation within the building. This design choice enhances air circulation and helps maintain indoor air quality.
Uniqueness
Uniqueness The building’s future expansion plans include extending the end walls. To accommodate this, the end wall columns were specifically designed to allow easy removal of the wall cladding during the expansion process. Given that the building spans over 200 meters, it is subject to temperature effects, leading to thermal stress on the structure. To counteract this, slotted purlin holes were implemented, enabling the structure to expand and contract with temperature changes, effectively mitigating the impact of thermal variations. Additionally, the building needed to support pipe racks and cable trays. For this purpose, brackets were strategically designed to handle the specified load requirements.
Challenges
The building had two Important aspects that remain the concern of all customers. They are the cost of the building and the time of construction. Everest ensured that the cost of the building was economical with respect to weight and construction. Since the project had a very short timeline, the design and release of the drawings had to take place on a very tight schedule. The material dispatch had to follow the erection sequence, which required accurate planning. Any error would cost the company its plans to commence operations on time. Everest addressed all challenges quickly and successfully delivered the project.
Economy and Timeline
The expertise and experience of Everest in the steel building Industry gave customers the confidence that Its project would be completed on time and that it could carry on with Its business plans as per schedule. The economy and timeline were adhered to by the manufacturer, Everest, which resulted in success for all project stakeholders.
Cookie Consent
We use cookies to personalize your experience. By continuing to visit this website you agree to our Terms & Conditions, Privacy Policy and Cookie Policy.