Harnessing hydraulic flow for optimal off-grid performance and fuel efficiency
By Staff Report | October 21, 2024 4:33 pm SHARE
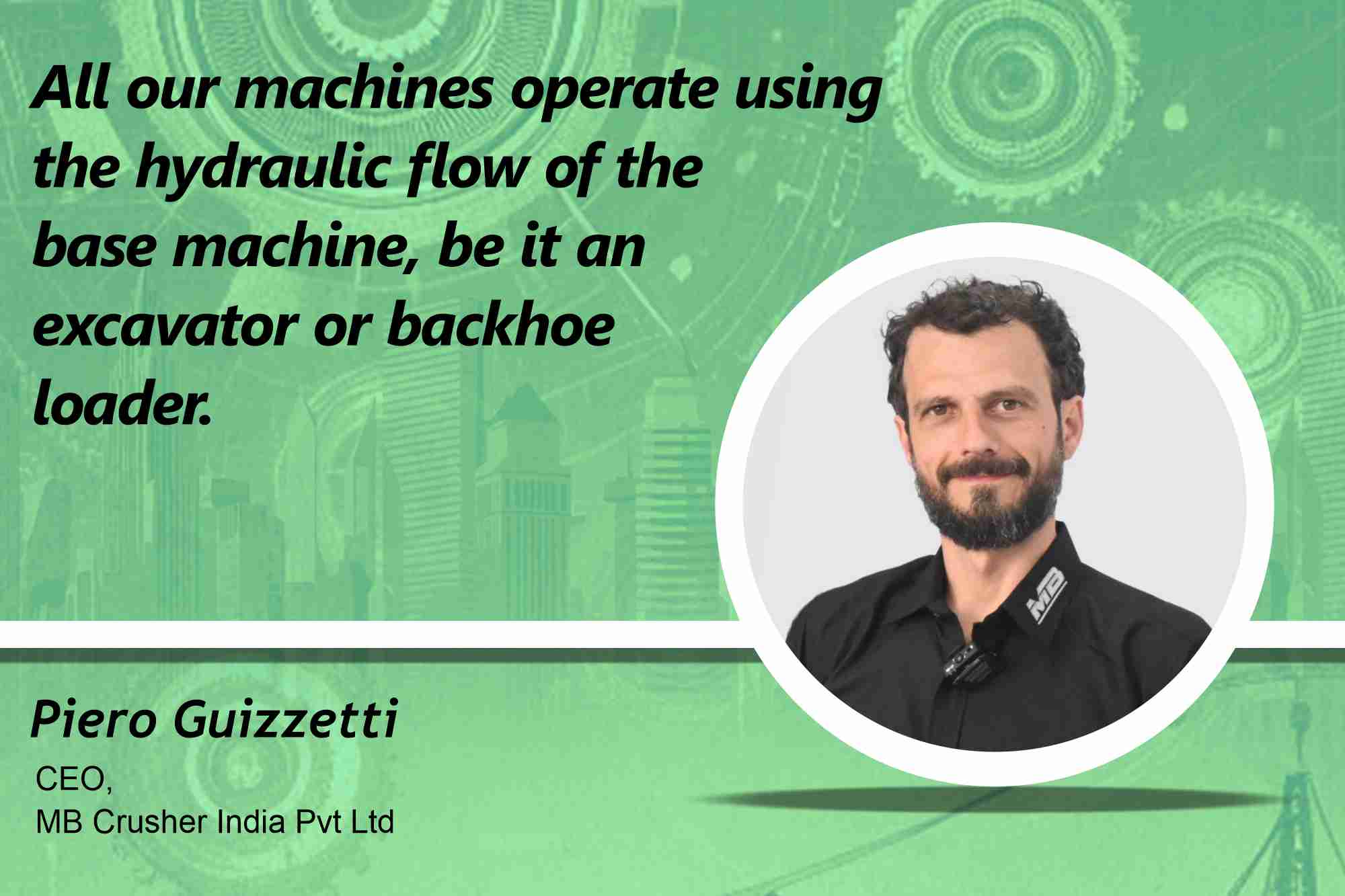
MB Crusher’s self-sufficient equipment harnesses hydraulic flow from excavators and backhoes, ensuring optimal performance in off-grid locations and minimal impact on fuel usage. Discover how this innovation sets a new standard in construction efficiency.
What key innovations will MB Crusher showcase at Intermat India 2024, and how do they meet the needs of India’s construction and mining sectors?
I would like to highlight two of our primary innovations. The first is our HDS line, which we introduced in India about a year ago. This machine serves primarily as a shaft screening unit for damp, wet, organic material. Interestingly, it also works as a crushing unit for softer materials like coal and laterite. This versatility particularly appeals to the Indian market, where companies are keen to minimise capital expenditure.
Rather than pushing our core product, the BF line – our primary crushing unit – we are positioning the HDS line as a cost-effective alternative. It comes at about half the CapEx cost of our BF line and offers a fine-tuned solution for the Indian context.
The second innovation is within our BF line, which remains our flagship product category. Specifically, the BF90 model has been designed to fit the 21-ton excavator class, which is the most prevalent in India. Over the last two years, based on feedback from Indian users, we have reinforced certain key areas of this machine to optimise it for India’s unique rock strata. These improvements reflect our commitment to tailoring solutions to local needs.
How does the MB-LS170 screening bucket contribute to efficient recycling in projects?
The MB-LS170 is part of our screening bucket line for backhoe loaders and is also compatible with excavators through our MB-S line. Specifically, it is suitable for backhoes between 8 and 15 tons, making it perfectly compatible with machines like India’s 3DX and Manitou, one of our key partners. We even did a live demo with them at the last BC India event.
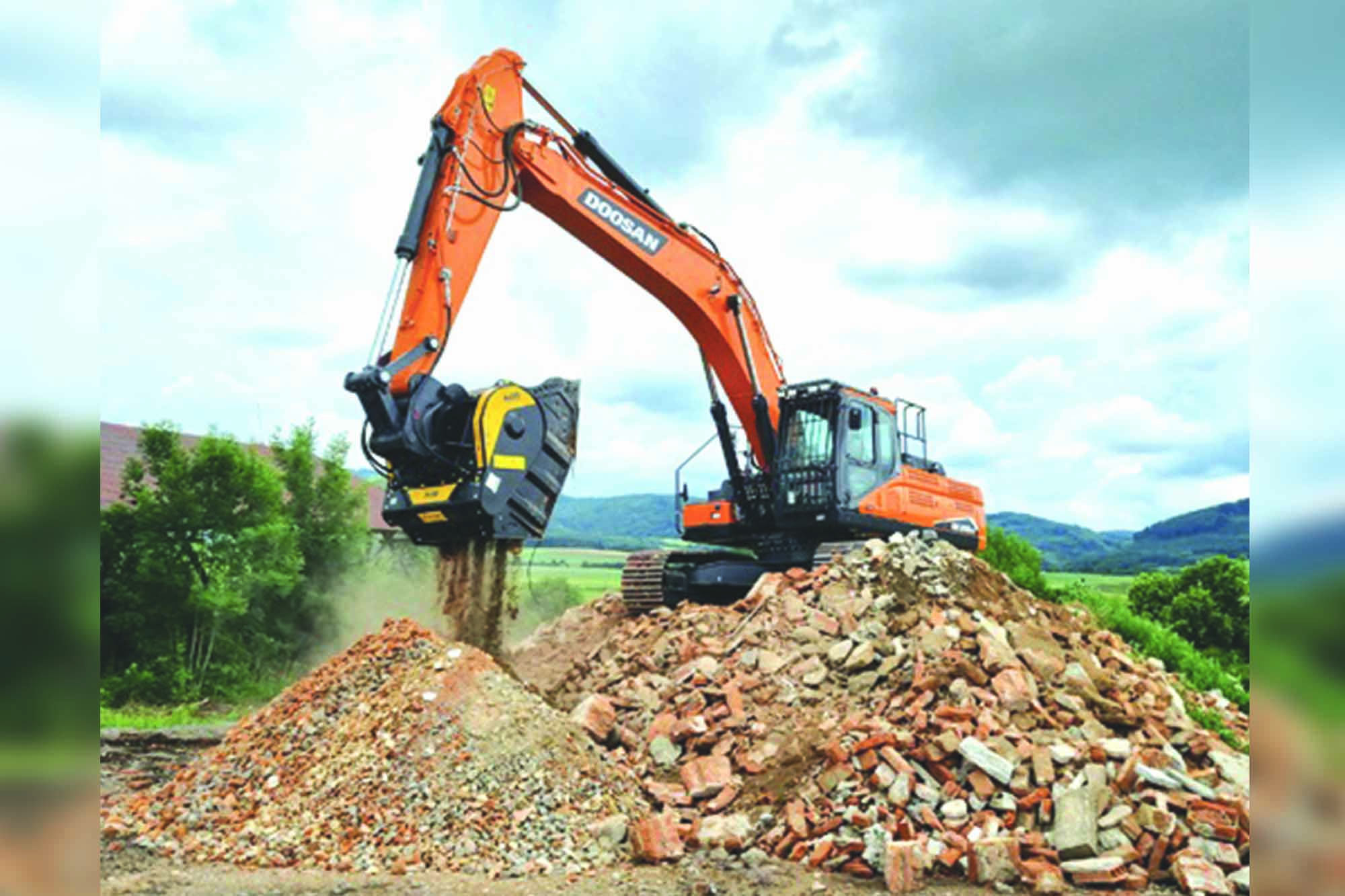
Regarding the battery recycling project, this was a case where the disposal of batteries wasn’t properly segregated; they were mixed with soil and fine materials. We tested around 45 cubic meters of this waste and discovered that 90 percent of the material was below a size of 15mm. We fitted the MBL S170 with a 15mm mesh and achieved excellent results, with hazardous materials like batteries retained in the screening chamber. In contrast, soil and other fine materials were separated.
Another noteworthy application is in municipal solid waste recycling. We’ve deployed our HDS units in landfill operations to screen and crush organic material. This allows us to create RDF (Refuse Derived Fuel) pellets fed into power plants for energy generation. Our equipment, like grapples and screeners, is crucial in optimising waste management.
How has MB Crusher equipment demonstrated efficiency and longevity in handling delicate yet durable materials like glass?
Glass is a unique material, both hard and frail. Many assume it is easy to break, but glass ranks quite high on the Mohs hardness scale. However, due to its brittle nature, it doesn’t cause significant wear on our equipment.
For example, in a glass waste processing installation we conducted in India, we achieved 50 percent higher productivity than what we advertised in our brochure. Additionally, the material’s low abrasiveness meant that even after 1,500 hours of operation, the crusher’s jaw plates hadn’t needed replacement. This highlights the machine’s efficiency and its longevity in handling delicate materials like glass.
With companies exploring unconventional environments like underwater and extraterrestrial mining, does MB Crusher foresee any potential applications of its technology in these areas?
Underwater and extraterrestrial mining are gaining attention, particularly deep-sea mining for earth materials. While we haven’t developed a full solution for these environments, our drum cutters and screening machines are submersible up to the depth of an excavator’s boom.
For instance, we’re using our MB-S line to source riverbed materials in India. Our equipment can be submerged to screen and wash materials directly from the water, eliminating the need for additional washing cycles after the material is extracted, saving time and resources.
How does the hydraulic flow of base machines maximise efficiency and self-sufficiency?
The beauty of our equipment is that it doesn’t require external power sources. All our machines operate using the hydraulic flow of the base machine, be it an excavator or backhoe loader. We don’t require additional power generators or fuel consumption, making them perfect for off-grid locations. If your excavator consumes 15 litres of fuel per hour, adding our equipment doesn’t increase that fuel consumption at all. It’s highly efficient and self-sufficient.
India is a vast and fragmented market, which challenges ensuring a widespread and capillary presence. Each region operates differently, so being close to the customer is critical. Despite these challenges, we are committed to sustainability through innovation, minimising waste, and reusing materials directly on-site. We constantly strive to adapt and meet the specific needs of the Indian environment while maintaining our high standards of quality and efficiency.
For more information, visit: https://www.mbcrusher.com/en/sr/
Cookie Consent
We use cookies to personalize your experience. By continuing to visit this website you agree to our Terms & Conditions, Privacy Policy and Cookie Policy.