Henkel India sets up two new Labs
By Edit Team | April 20, 2017 10:02 am SHARE
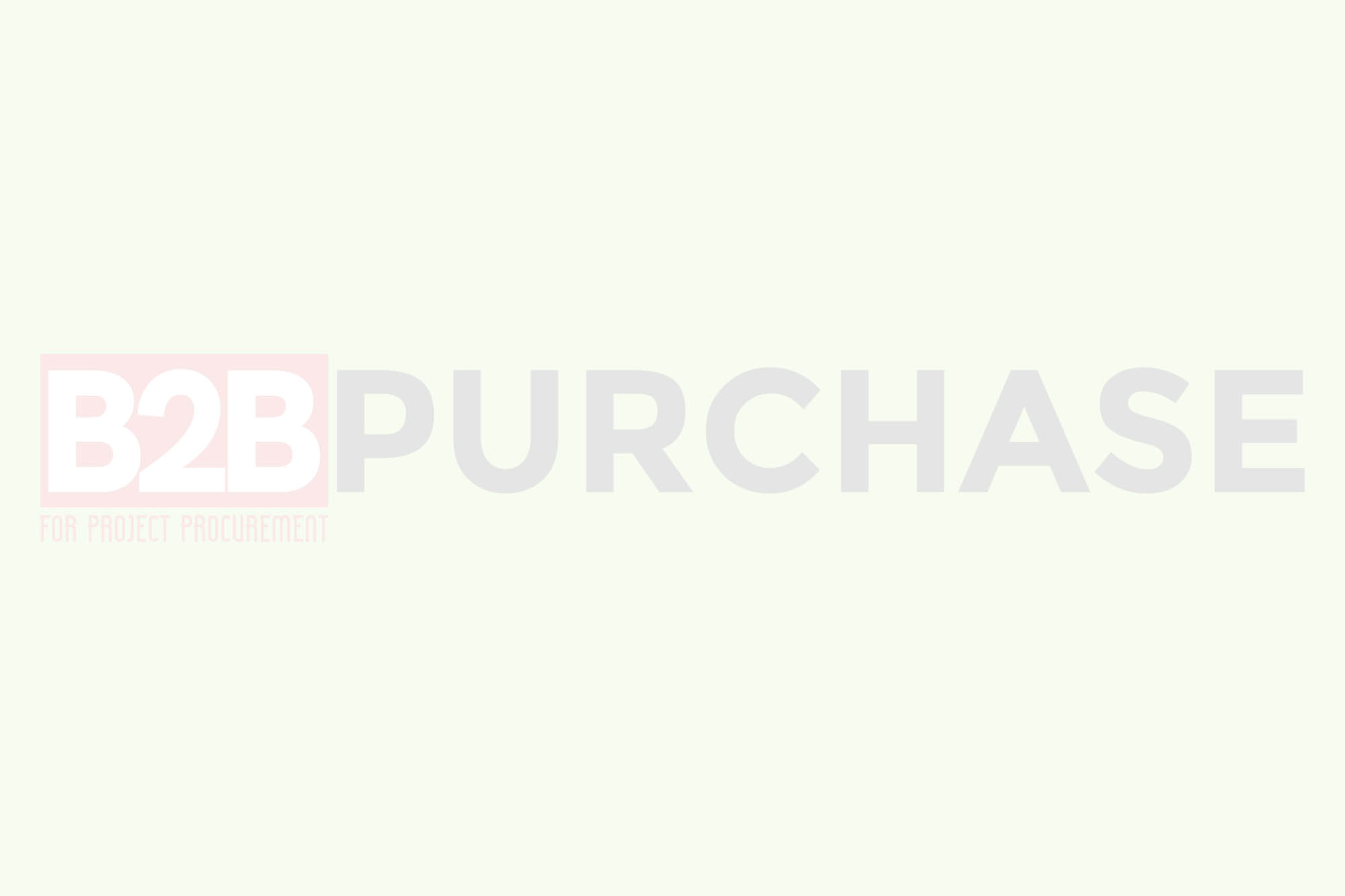
Henkel Adhesives Technologies India Private Limited (Henkel India), a fully owned subsidiary of Henkel AG & Co. KGaA, the leading solution provider for adhesives, sealants and functional coatings, has recently expanded the capabilities of its Pune Innovation Center with two dedicated laboratories, one for Maintenance Repair and Overhaul (MRO) and the other for Acoustic and Noise, Vibration and Harshness (NVH). The MRO Application Development Center facilitates development of products that can meet the unique needs of customers to save costs, improve energy efficiency, extend service Life of industrial assets, reduce downtime and improve performance; test products in simulated conditions in-house before they are used in actual conditions; and train customers on product selection, application, and best practices. On the other hand, the Acoustic Engineering Center enables Henkel India to offer cutting-edge solutions to meet the evolving and challenging requirements of customers in the area of NVH.Equipment used in industrial facilities such as pumps, pipes and surfaces of all kinds – have to be able to withstand harsh conditions and heavy-duty use. Henkel works hand-in-hand with customers from heavy industries to meet these new challenges, providing a one-stop shop for tailored services. The new MRO Application Development Centre at Pune is fully equipped to develop and offer Loctite Polymer Composite solutions to rebuild, repair and protect industrial equipment. With extremely hard reinforcement fillers, Loctite Polymer Composite products have excellent wear resistance and superior adhesion. They are designed for specific service conditions to protect and extend the service life of a wide range of plant and equipment. The advantage of using these products is that they act as a sacrificial and renewable working surface, protecting the structural integrity of the original substrate. The MRO Center has full capability to apply and test the performance of these innovative solutions in typical industrial operating environments.Speaking about the role of Henkel in light weighting, Dr Kourosh Bahrami, Global Head of Henkel’s MRO business, said: “We play an important role and are the pioneers in mainly two areas.” He further explained, “We help in reducing the direct weight by applying lesser body coating. This is possible as we have a superior technology, which enables better performance with lesser material.”The more important aspect to which Bahrami drew attention to is the alternative solution to welding. He said: “Welding has its own limitations. When it comes to joining two different materials, especially those that are lighter in weight, or joining a metal and an alloy or a composite material, adhesives are the only option. With the growing usage of plastic or composite material, the application of adhesives is acquiring a formidable position.”Supporting the views of Bahrami, Pradhyumna Ingle, Head of General Industry for Henkel in India, said: “One cannot weld steel with aluminium. There is no way that can take place. Hence, adhesives are the only option that can be used. Adhesives or similar multi substrate bonds are a reason that almost all car manufacturers have a tie up with Henkel.”Ingle added: “No car in this world rolls out without a Henkel product on it. We have acquired a strong association of working with the OEMs and we provide tremendous workmanship with the aftermarket support. This is where our role is very important. Adhesives promote the usage of thinner and lighter materials. They offer the benefit of light weighting.”Henkel not only focuses on the automotive sector but also caters to a wide range of industries. “We blend the knowledge that we have gained in the automotive industry with other industrial sectors. We have used adhesive solutions in the railway coach industry in India. With the usage of adhesives we could reduce the weight of the coach by 250 kg per coach. That not only reduces weight but also give superior coach quality and energy saving. This can help in adding another coach and also give more comfort to the passengers,” added Ingle.Another area where Henkel has ventured into is light weighting in the appliances space. Explaining this point, Bahrami added: “We are working with washing machine manufacturers and even manufacturers of dishwashers to reduce the weight of such appliances by reducing the weight of the materials used.”He further points out that the usage of adhesives has eliminated the usage of fasteners in motors.“We have made the process of manufacturing electric motor simpler and more efficient while increasing the reliability of the end product,” he says. Explaining about the working in the Pune Innovation Center, Ingle said: “We have a team of 40 chemists who are working on some or the other technology. They are the experts in their own technology. We also have sales and technical teams that look after the specific application challenges.”The acoustic lab facilitates vehicle and component level testing for different applications as per international standards. It also helps meet high level product validation tests based on customer requirements. Henkel’s trained team of engineers analyse acoustic material properties of structures and panels to determine their effectiveness in automotive, off-road equipment and appliance applications. With the latest equipment and software, to perform measurements and analysis, Henkel is able to offer full capabilities including Computer Aided Engineering (CAE), Finite Element Analysis (FEA) and lab testing. With the new acoustic NVH capabilities, the Center will provide a boost to the existing simulated environment for the automotive, off-road equipment and appliance industry portfolio’s acoustic structures.
Cookie Consent
We use cookies to personalize your experience. By continuing to visit this website you agree to our Terms & Conditions, Privacy Policy and Cookie Policy.