How to choose Structural adhesive for application
By Edit Team | January 17, 2018 10:29 am SHARE
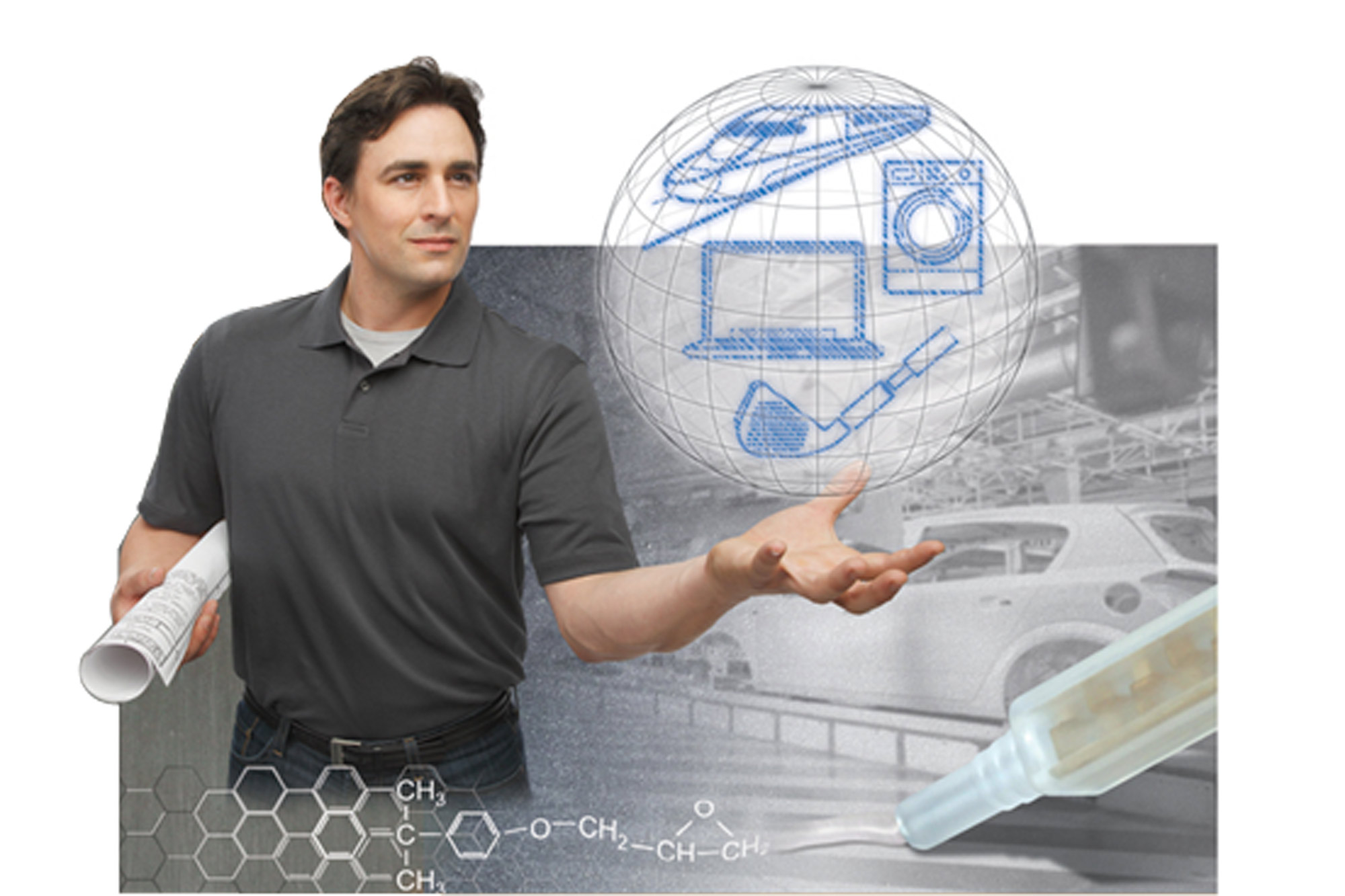
Why use a structural adhesive?
Structural adhesives (SA) are chosen for a multitude of assembly operations. Unlike mechanical fastening methods, they don’t damage substrates (i.e. no need to drill holes; no heat distortion as when welding metal); they can join dissimilar materials without galvanic corrosion; are amenable to a number of different geometries; don’t concentrate stress at a few localised spots (thus increasing fatigue resistance); and don’t require refinishing steps or leave protrusions (aesthetically more pleasing). Structural adhesives also play an important role in the move to composite materials, which allow for significant weight reduction with comparable stiffness, compared to metals.
Selecting a structural adhesive
SA should be chosen with the end-user requirements firmly in mind. Once these are known, the proper adhesive can be selected by matching the requirements to the different processing and performance characteristics.
In particular, end use conditions to consider include:
Expected conditions during end use:
- Temperature
- Humidity
- UV exposure
Chemical resistance required
- Fluids
- Cleaning solutions
- Are there any specialised chemicals which may contact the bonded part
- Will contact be continual or only occasional
Cleanliness or environmental issues during production and end use
- Outgassing, ionics, corrosion potential
- Toxicity, disposal
Mechanical challenges
- Impact, vibration, fatigue
- Stress type and magnitude
Types of structural adhesives and their performance criteria
They can be generally categorised by chemistry. Although hybrid products can be formed, in general the categories of structural adhesives are: Epoxies (one and two part formulations); acrylics (two-part and two-step formulations); urethanes (two part formulations); and cyanoacrylates (“instant adhesives”).
In general, certain trends hold true: Acrylics overall provide the highest bonding strength on plastics, and may also provide good bonds to metals. However, they tend to have lower vibration or impact resistance than better epoxies (thus, lower fatigue resistance) and lower performance at temperature extremes. They also cure-shrink more than epoxies and urethanes. Two-part acrylics tend to bond well through many common stamping and forming oils, so in many cases they may require less surface preparation to use. However, most common products have high odor and contain a flammable material. There are some low-odor products that do not contain the flammable substance, such as 3M™ScotchWeld™ Acrylic Adhesive DP8805NS and DP8810NS; which can provide a more pleasant working environment. Newer acrylic adhesives are shelf-stable up to 18 months at room temperature in a 10:1 mix ratio.
Cyanoacrylates tend provide good shear strength on many plastics and rubbers (although primers may be required); but are rigid and show low peel and impact resistance; and are not good for long term applications on metals or glass.
Urethanes tend to be quite flexible, but have lower strength in general. They can be relatively good plastic, rubber and composite bonders and generally are lower priced than other categories of structural adhesives.
Epoxies come in the widest range of properties and can have the best overall properties on metals and often on thermoset composites. Standard 5 minute rigid epoxies that are commonly available in hardware, tend to be brittle, and are best suited to applications where relatively low stress and no impact are expected. Flexible epoxies, such as 3M Scotch-Weld Epoxy Adhesive 2216, have higher peel strengths and hence better impact performance; they are also good choices for parts which may require some flex in end use. Toughened epoxies, such as 3M Scotch-Weld Epoxy Adhesive DP420 and DP460, actually incorporate elastomeric regions which absorb impact, and thus provide the highest shear, peel, impact, vibration and fatigue resistance; and hence are chosen for the most demanding end-user applications. In general, however, epoxies require rigorous cleaning of oils from metal joint surfaces for room temperature bonding.
Based on these generalities, if an engineer is looking to bond ABS to stainless steel, for a part that will see moderate environmental stress (e.g. -20 F to 150 F, for example) but little vibration or impact, the choices would likely include epoxies and acrylics. Add vibration or impact to the criteria, and the choices would tip towards epoxies or specially toughened acrylics.
An engineer seeking to bond wood to plastic for outdoor use, where significant movement of the substrate may occur due to changes in the weather, would consider urethanes for their flexibility; if higher strength is needed a flexible epoxy could be chosen.
Bonding a low surface energy plastic (such as HDPE or glass-filled polypropylene) to itself or to another plastic or metal would require a specialty acrylic, such as 3M Scotch-Weld Structural Plastic Adhesive DP8010 Blue.
Two-part epoxies, acrylics and urethanes require some amount of time for the cure to start after the parts are mixed and the surfaces to be bonded are mated; this allows positioning but also requires that the parts to be fixture in place until some level of cure has occurred. This period of time is referred to as set time, fixture time, green strength or time to handling strength—in any event; manufacturers define it differently so the engineer needs to carefully consider the data on the datasheet to correctly determine the parameters for each adhesive.
Authored by:
Ashu Seth
Technical Manager
Industrial Adhesives and Tapes
3M India Ltd
Cookie Consent
We use cookies to personalize your experience. By continuing to visit this website you agree to our Terms & Conditions, Privacy Policy and Cookie Policy.