How to reduce downtime of mining equipment
By Edit Team | November 24, 2014 7:29 am SHARE
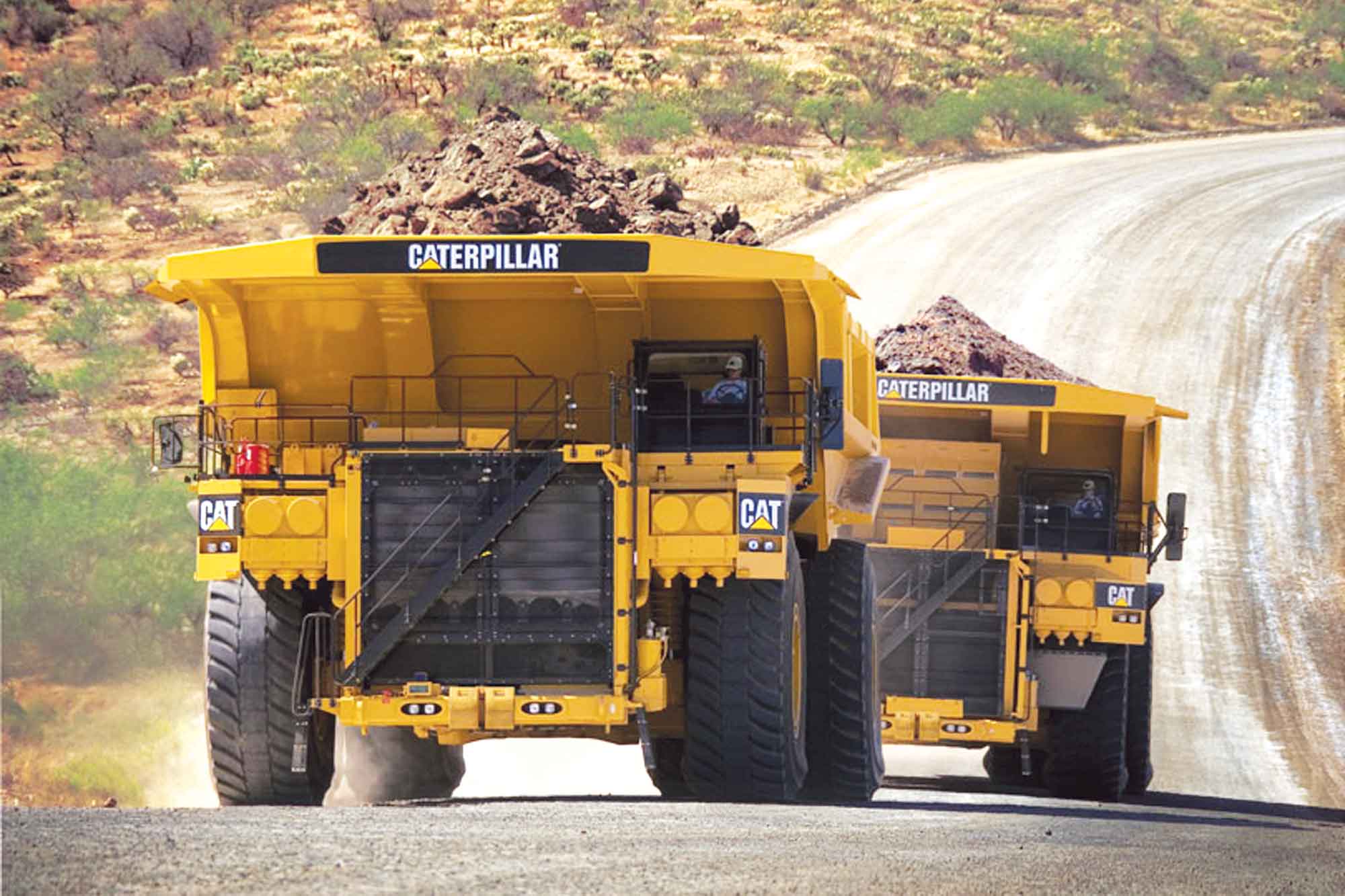
In the mining industry, any technology that reduces downtime and increases productivity finds high demand. Let us get an insight on how this can be made possible
To reduce cost per tonne significantly in a mine without any capital investment, one has to improve equipment reliability. Doing this means reducing total downtime which, in turn, will help reduce overall cost. The total cost per tonne may go up slightly in the early phases of equipment reliability improvement, but will go down over the time.
There are two types of downtime: planned downtime, and unplanned downtime.
Planned downtime
Planned downtime is operating time lost due to planned events. These are events where you have no intention of keeping the plant operational, such as breaks, scheduled maintenance, and holidays.
After subtracting planned downtime from plant operating time, the remaining time is called planned production time. This planned production time is the benchmark that unplanned downtime events are measured against.
Unplanned downtime
This measures the loss of planned production time due to unplanned events that cause downtime. These events can occur for a variety of reasons – operator error, mechanical problems, and lack of oversight are some of the biggest causes.
Each of these events results in time where operations are shut down; add all that time together and you get the total amount of unplanned downtime. When you divide the total unplanned downtime by the planned production time the result is the plant’s availability.
Reducing downtime of mining equipment
The question arises – how can downtime be reduced? There are several actions that directly impact downtime, however the most important component for improving and sustaining equipment reliability is planning and scheduling. The actions that directly and significantly reduce total downtime are:
• Faster and higher quality repairs through planning and scheduling
• Lubrication practices and operating practices
• Installation, alignment, and balancing practices for rotating equipment
• Detailed cleaning
• Fixed time component replacements
• Engineering and design of equipment.
Though there are some other practices which can act as catalysts to reduce downtime, the above ones are major factors.
“Miners are always looking for ways to enhance mine site safety, reduce costs, improve profitability and boost efficiency,” observes Ramesh Tipirneni, Country Manager, Caterpillar India. “Cat MineStar System helps customers do that, providing the most comprehensive suite of mining technology products in the industry. It consists of a number of configurable capability sets that allow you to scale the system to your mine site needs.”
Cat MineStar System helps manage everything from material tracking to sophisticated real-time fleet management, machine health systems, autonomous equipment systems and more. The capability sets – fleet, terrain, detect, health and command – can be used in combination or individually to allow your operation the flexibility and scalability it needs to be more productive, efficient and safe.
Cat MineStar works across virtually any mine site asset, surface or underground, improving uptime and availability to meet even the most challenging business needs.
Planning and scheduling
The planning and scheduling process is very critical to implement since it enables and controls all resource allocations in maintenance. The process aligns production schedules with maintenance schedules and enables a structured partnership between operations and maintenance. Once a basic planning and scheduling process functions in a mine, it is possible to implement the other processes since time is better utilised at that point.
In order to effectively utilise the mine’s resources and reduce downtime of equipment, the maintenance work has to first be planned, then scheduled. A planned and scheduled job will be executed faster and with higher quality and therefore reduce downtime of equipment.
Need of planning resource
A mine needs a trained resource that performs planning. A planned work order includes: materials, tools, lift equipment, technical documentation, safety assessment, permits, job instructions, skills needed, time estimate for job, cost estimate, physical constraints, etc. A good planner must plan for sufficient number of craftspeople to extract the required work in time.
Health technology by Caterpillar
Reducing unplanned or unscheduled downtime has been a challenge over the period. Caterpillar offers Health technology to answer the challenge.
“By identifying many types of potential equipment problems before failure, Health technology works to minimise unscheduled downtime and productivity loss,” says Mr Tipirneni.
In addition, it helps keep operating costs in check by streamlining service and maintenance management and scheduling. The condition and availability of mining equipment have a significant impact on a site’s cost. When machines are not operating at peak performance, or when unscheduled repairs reduce machine uptime, sites feel the impact directly on their bottom lines.
It’s estimated that the total cost of unscheduled downtime can be as much as 15 times that of a scheduled event. By using on-board technologies that monitor machine health, mine sites are able to address potential problems before they become failures. Sites can schedule maintenance around their production schedules, protect critical machine availability and reduce costs by making repairs before components fail.
Also Health and condition monitoring systems collect critical event-based machine condition and operating data for entire fleets of equipment. Information can be downloaded from machines and analysed by the maintenance team using a wide range of diagnostic and analytic reporting tools.
Health technology has its other advantages in its own way as follows:
Streamline planning and scheduling : Health technology includes comprehensive maintenance and service planning capabilities. It enables managers to track what equipment is due for service, schedule repairs and maintenance, see what procedures have been performed and monitor how the machine is performing once it goes back to work.
Identify site issues : It can also help identify issues beyond the equipment, including problem areas within the mine site itself. With GNSS tracking capabilities, it generates reports showing where health and operational alerts occur. That can help spot site problems—such as suboptimal haul road conditions—that affect machine health, machine availability and asset life.
Universal functionality: In addition, it offers universal functionality that works with virtually any mine site assets, including off-highway trucks, wheel loaders, motor graders, wheel dozers, shovels and light duty vehicles, as well as equipment from other manufacturers.
Summary
Considering all the points discussed, it can be said that downtime can be reduced significantly through reliability and maintenance improvements. There is no capital cost for improving reliability and it is therefore often one of the most cost-effective ways to reduce downtime. Also planning and scheduling work processes is at the core of any reliability improvement since the work process controls all maintenance work and joins the production schedule with the maintenance schedule.
Miners are always looking for ways to enhance mine site safety, reduce costs, improve profitability and boost efficiency.
Ramesh Tipirneni, Country Manager, Caterpillar India
Cookie Consent
We use cookies to personalize your experience. By continuing to visit this website you agree to our Terms & Conditions, Privacy Policy and Cookie Policy.