Innovations in Crushing and Screening technology
By Edit Team | April 9, 2021 11:31 am SHARE
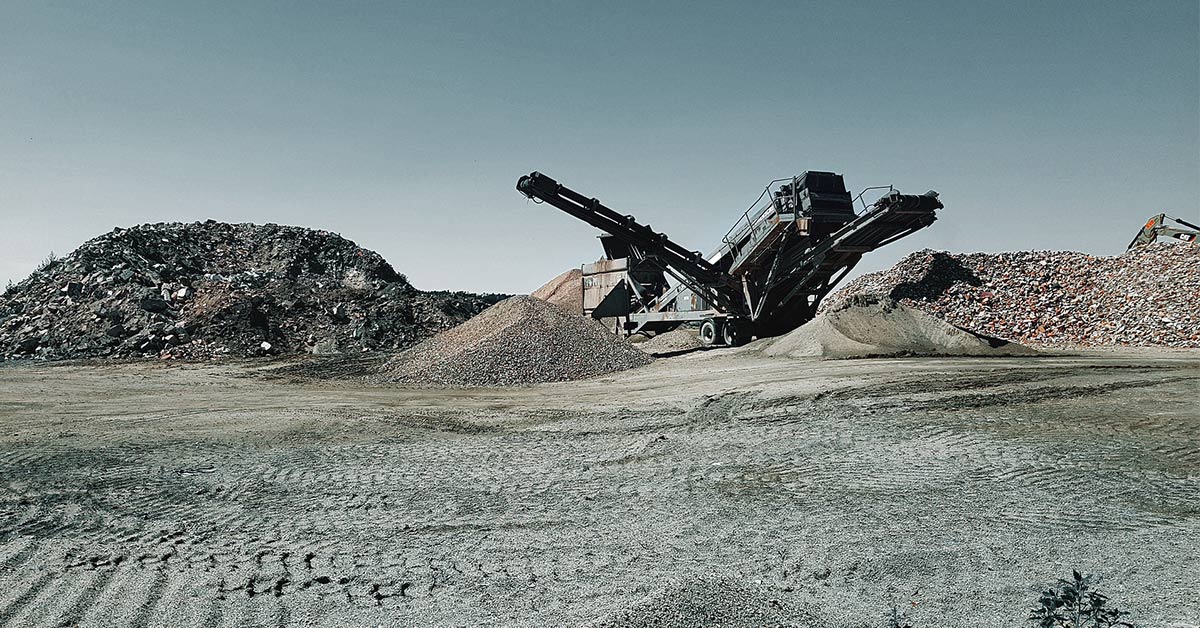
Growing construction and mining activities demand for innovative solutions in crushing and screening technology. Industry leaders elaborate on the technology trends in crushing and screening equipment for construction and mining applications.
As we enter the new financial year, the construction and mining activities are back on growth path after the severe pandemic impact hitting the overall economy. Road construction is picking up fast while mining activities are gaining momentum after the policy push from the government. All these have led to opportunities and new prospects for the equipment market.
Pushing up demand
At a time when the construction and mining activities are seeing renewed growth in the country, it is imperative for the crushing and screening operations to be productive and efficient. Innovative technologies improve the performance of these equipment to meet the emerging demands of the aggregate and mining market. Crushing and screening equipment play a major role in the infrastructure development of the country by supporting aggregate manufacturing and mineral processing.
As J Bezaleel Manoah, Associate General Manager (Mechanical), Patel Infrastructure Ltd, says, ‘’Crusher plant is the backbone of our civil construction industry’’. Patel Infrastructure Ltd, the leading road EPC contractor in the country, created a world record in February this year, laying 14,000 cu m of concrete in 24 hours for Delhi-VadodaraMumbai Expressway. “We executed this feat with 18.75 m width pavers and it was a challenging task. We had to do micro-level planning as it involved many components such as sand, aggregates and crushing equipment. It was a total team effort and we achieved our target with a clear vision’’, he adds. The company has set up own crushing units for crushed aggregates and sand required for the expressway project. The company has 200-250 TPH crushing plants for projects in Tamil Nadu, Rajasthan and across India.
Piero Guizzetti, CEO, MB Crusher India, says, “Two of our important segments, crushing and screening, are very much driven by infrastructure development in its most general sense. And India is one of the world’s most exciting markets. Sectors like roads, railways, ports and urban transportation have seen a major chunk of government spending as public sector outlay is greater in these areas. Real estate has also been a boon with the private sector contributing significantly. Mining and quarrying are constantly recovering from the closing of most concessions a few years back.’’ The company offers a product portfolio capable of cutting, crushing, screening and processing stones, rocks and organic matter. These solutions are applicable and compatible with all makes and models of excavators and backhoe loaders.
Technology trends
When it comes to faster construction of roads and highways, the role played by crushing and screening plants is immense. Technology has come a long way as we have also witnessed a rise in new age technologies in the recent past.
Roads and highway projects are becoming bigger with more expressways are being constructed in the country. This has driven the demand for higher capacity crushers and screens. Jayanta Pradhan, Vice President – Service, Propel Industries, observes, “In every 12-14 km, you need a 200 TPH crusher plant. Now, the 200 TPH plant has been upgraded to 250 TPH plant and 300 TPH plant has been upgraded to 350 TPH. With the enhancement in TPH, the crusher can cover 42-46 km from 35 km.”
Based on the project requirement, there are three different applications such as mobile crusher, stationary crusher and wheel crusher. Maintenance play a crucial role for any equipment to sustain in the long run, and crushing and screening plants are no exceptions. According to Shantanu Banerjee, Country Head, HAZEMAG allmineral India Pvt Ltd, people who were using old crushers had a bad experience because of issues in hydraulics, operational parts, chain breakage etc. He adds, “Indian operators look for short-term gains while selecting low cost crushing plants and it’s quite unfortunate in the long run. Being a German company, our equipment last for 12-15 years and accordingly, the cost is higher in such machines. At the end of the day, a customer who looks at long term benefit will prefer a robust plant.’’
HAZEMAG’s machines are PLC-controlled and do not require a dedicated operator to operate the machine. So customers can save the manpower cost and structural cost. The company offers newgeneration crushers especially for coal mining applications.
The role played by technology and automation in crushing and screening plants has gone through a massive change in recent times, according to Anubhav Chandra, Manager – Sales, RD Infra Equipments Pvt Ltd. He says, “Technological adaptation has always been a big challenge. It’s not an overnight process, but technological changes can happen within a year or two. Gone are the days of going to your plant to get the product report as with the upgradation of technology, you can now get product report on your mail via mobile phone. This change is going to happen and it all depends on the investment that the client is willing to make in his plant. We are moving in the right direction and initiative such as ‘Make in India’ will only help us further with new technologies.”
Green initiatives
Currently, the crushing and screening equipment market is dominated by diesel powered plants and machines. However, leading players are offering hybrid and electrical powered models for various applications. This can reduce emission in crushing and screening. However, there are issues related to dust and suspended particles in crushing operations. When it comes to mining, there are a lot of issues related to environment and emissions. In India, mining sector is dominated by coal mining. Elaborating on this, Shantanu points out, “Coal mining is largely an open cast operation as a gust of wind is enough to create a dusty environment. Particularly in a crusher, dust generation is more basically when the tippers or dumpers are unloading on to the crusher. Actually there is very less dust generation in crushing operations. It does not really impact the environment but some customers have installed sprinkling system on the crushing zone to reduce dust.”
Propel has introduced electric mobile screen plants that promotes environment-friendly operations. The innovative switching from diesel power system to electric power system helps the customer increase plant productivity with the same input, according to Jayanta.
Innovations in M-Sand technology The use of manufactured sand (M-Sand) has seen unprecedented growth in the country, after the ban of natural sand mining in many states.
M-Sand has many advantages over natural sand. The growing demand for M-Sand has led to the requirement for higher capacity and better technology crushers. Jayanta is of the view, “The problem is not with the sand generation but with the optimisation of the plant. It all depends on the plant and its TPH capacity to give the required amount of output. If a customer wants to enhance his old plant then there are three solutions available. They are vertical shaft impactor (VSI), fine cone and roll crusher.’’
On a positive outlook As projects are growing bigger and execution period shorter and stringent, it has become imperative to use large capacity, efficient and technologically advanced crushers and screens for better and improved productivity to match the project requirements. In this scenario, it is imperative for equipment players to focus on technology over cost. With the trend is shifting from capex towards opex, technology will drive most of the operational growth in the country.
As Piero says, “We are seeing opportunities rise in that industry in a pocket of specific applications. We foresee the major demand drivers for crushing and screening machines as GSB requirements for roads, quarry operations for aggregate manufacturing, M-sand production, recycling and reusing demolished concrete materials, mining, among others.”
Crushing and screening equipment market has evolved over the years with diversified application segments. Apart from the traditional segments of mining and quarrying, new segments of M-Sand and waste recycling are gaining momentum and going ahead there will be more demand from these segments. The real growth will lie in providing the right capacity machines for the requirements.
Cookie Consent
We use cookies to personalize your experience. By continuing to visit this website you agree to our Terms & Conditions, Privacy Policy and Cookie Policy.