Layher Allround Shoring: ideal for honeycomb-shaped silo
By Edit Team | March 23, 2015 8:52 am SHARE
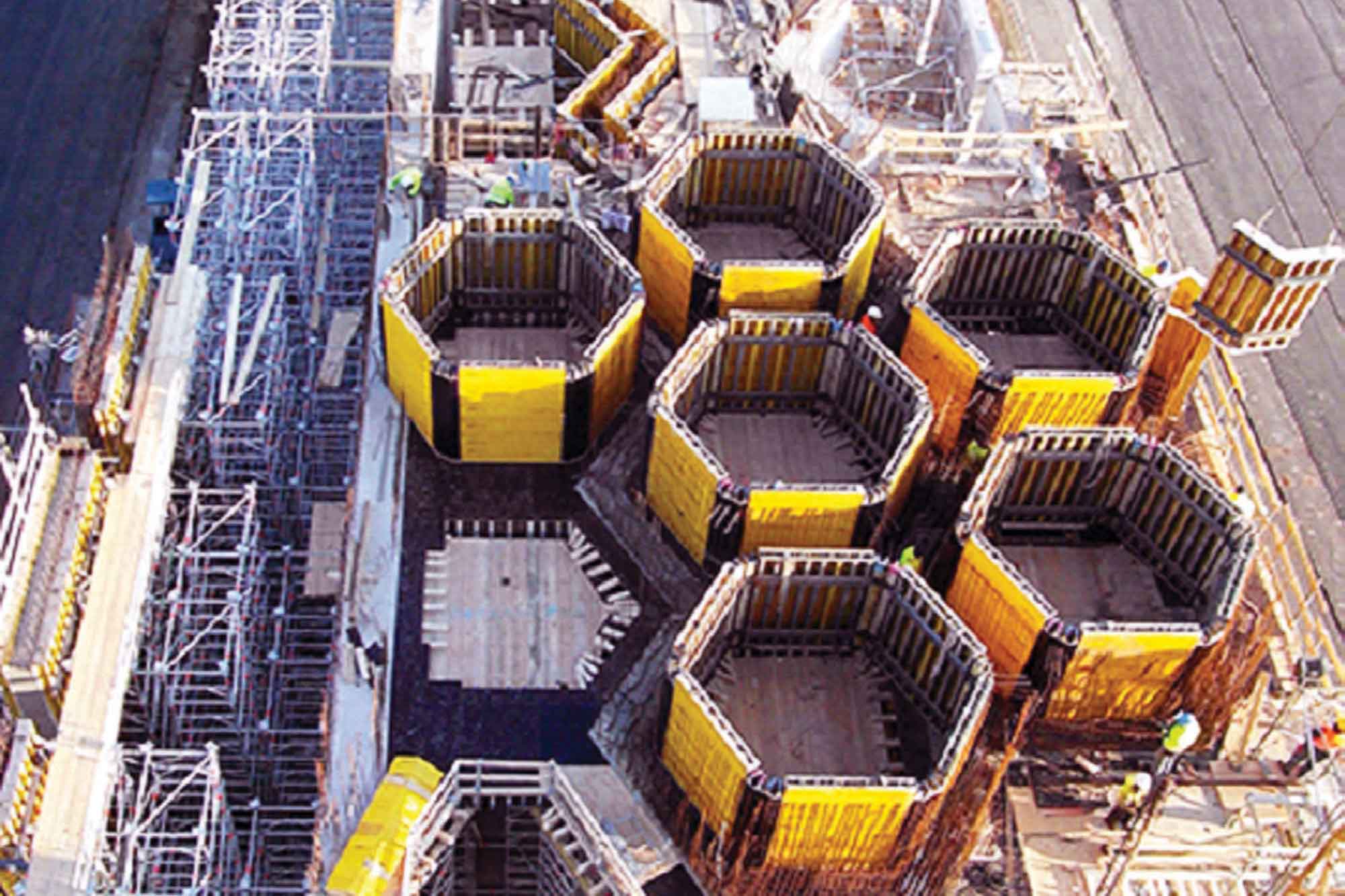
Square, rectangular or hexagonal – thanks to its flexibility in application, Layher’s Allround Shoring TG 60 proved to be the ideal solution for building a honeycomb-shaped silo complex around 90 metres high at Brake in Lower Saxony
Layher Allround shoring TG 60 uses a simple, unique and bolt free connection technology. Sliding the wedge head over the rosette and inserting the wedge into the opening immediately secures the component. There is still sufficient play to secure the other end of the ledger. A hammer blow to the wedge transforms the loose connection into a superbly strong structurally rigid one. The face of the wedge head is now precisely positioned against the standard.
Layher’s Allround Shoring TG 60 proved to be the ideal solution for building a honeycomb-shaped silo complex around 90 metres high at Brake in Lower Saxony. With this system of modular design, the construction company was able to adapt the shoring structure for supporting the wall and ceiling formwork precisely to the geometry, and also use it both as work/protection scaffolding and as a site access.
When a silo complex around 90 metres high and with 38 cells is built directly on the lower Weser, which is a river of sea depth, that’s no small thing for all concerned. For example, it’s not just that the inhabitants of Brake, a sea port in Lower Saxony, have to get used to a completely new skyline: the construction company was faced with challenges by this new structure. “Strong support” were the key words in this context in addition to 360 concrete piles, which extended as far as 19 metres down into the soil to provide the foundation for the structure, which is some 1,400 sq.m. in area, a complex shoring structure was also required for the various construction phases.
To enable trucks to drive directly underneath the appropriate silo for loading, walls were built only partially, and then a honeycomb-like grid of beams was provided 12 metres up as the joist for the six-sided cell shafts. The shoring performed several functions in this project: support of the wall and ceiling formwork, work and protective scaffolding for providing this formwork, and site access. The geometry posed a particular challenge: to adapt the shoring precisely to the formwork in the area of the partly zigzagging walls too, an extremely flexible system was needed. So our choice was for Layher’s Allround Shoring TG 60.
Layher’s Allround Shoring TG 60 is a combination of high-strength shoring frames and standard parts from the proven Allround Scaffolding range, ensuring rapid building progress: firstly, rapid assembly considerably improves efficiency at construction sites. This is assured by the reduced number of components in the prefabricated shoring frames when compared to individual parts, by the low component weight of no more than 18 kilograms, by bolt-free wedge-head connectors, and by the efficient use of material thanks to variable bay lengths. In this way, the TG 60 system adapts variably to the existing loading situation and to the specified geometry.
The key advantage for us of Allround TG 60 Shoring was its compatibility with the comprehensive component range of the Allround system. It was possible for all these requirements to be implemented not only optimally, but also in an extremely economical way in terms of work preparation, logistics and handling, thanks to fewer basic components. With hexagonal shoring towers inside the honeycombs, the construction precisely matched the six-sided contour of the wall formwork, with a maximum clearance of 30 cms, for example in the area of the walls in their zigzag configuration. Layher steel decks were used as non-slip work surfaces and as fall prevention devices, as well as decks with hatches for integrated access.
The installation of further shoring towers between the individual supporting walls to disperse vertical loads during the concreting work for the joists presented no problems. “However, for supporting the ceiling formwork at the edge areas it was rectangular shoring towers that were used. Since we had the option of extending the bay length – from 1.09 to 3.07 metres depending on the load – we made savings both in material and working time. The shoring towers for the individual wall sections were coupled by bolt-free wedge-head connections with Allround ledgers and diagonal braces. Once the concrete was sufficiently strong, the shoring towers could also be quickly repositioned by crane and modified for the next sections – an efficient solution”, as the site engineer emphasises.
This was how Allround Shoring TG 60 provided with strong support for the construction of what is now known as “Silo 6”. The new complex shot up by nearly three metres a day – and the facility for storage and processing of grain, animal feed and oil seed has since been officially opened. This construction project had become necessary in response to rising market demand for higher turnover rates and separate storage of agricultural products. However, the existing silo capacities had proved insufficient at peak periods. With a storage volume of more than 500,000 tonnes, the port of Brake will now be further consolidating its role as one of Europe’s leading agricultural locations besides Ghent in Belgium.
Authored by_
Mithilesh Kumar,Director,
Layher Scaffolding Systems Pvt. Ltd.
Cookie Consent
We use cookies to personalize your experience. By continuing to visit this website you agree to our Terms & Conditions, Privacy Policy and Cookie Policy.