Oil your way to maximised output in mines
By Edit Team | April 17, 2019 10:36 am SHARE
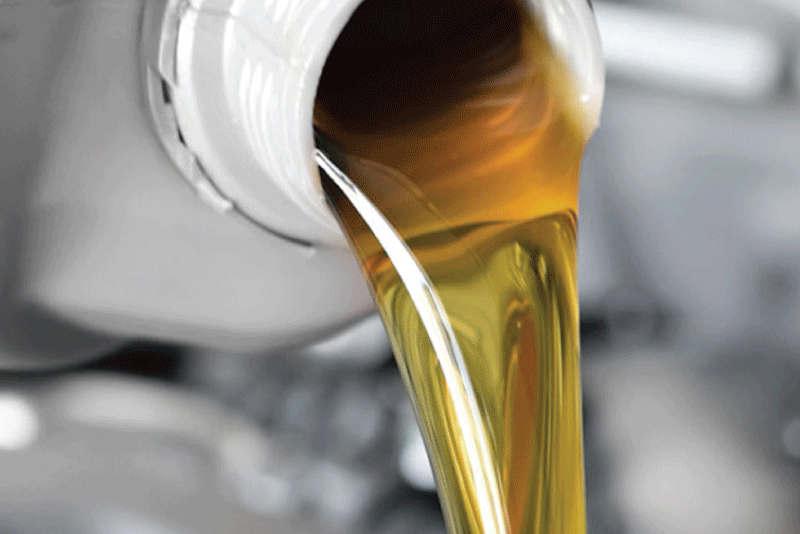
Increased production level entails long drain interval and using energy-efficient, high quality lubricants, cutting maintenance costs.
Reducing cost is essential to mining operations. So, lubricants that will protect mining equipment for extended periods under the toughest conditions are required. This allows mining companies to extend equipment life, decrease oil consumption and reduce logistical costs. Mining industry is expected to witness strong economic growth in the next few years, expanding potential for increase in lubricant consumption. BS VI norms are expected by 2020, which will lead to quality enhancement in lubricants and increased use of synthetic lubricants in construction andmining segment.
With new emissions effective by 2020, the entire focus of lubricant industry has shifted towards up-gradation of engine oils. The product meeting specifications like API CJ4, CK4 and FA4 will be in demand to meet desired performance levels.
The company blends entire range of engine oils up till API CJ4 all approved and certified by American Petroleum Institute (API). “Our entire range of hydraulic fluids developed for mining industry is approved by Rexroth Bosch (HLP/ HVLP/HVI). Our main aim is to blend best quality lubricants to enhance equipment life, negligible downtime and simultaneously increase drain intervals for better commercial viability to lower the total cost to customer, says Sandeep Ganjoo, Sr. AGM (Business development), Apar Industries.
Apar’s quality driven transmission oils fortified with additives to combat transmission noise/chattering /shuddering and provide excellent frictional characteristics to improve fuel economy and gear shifting. Company’s transmission oils meet and exceed the latest specifications as laid by various OEM manufacturers like Caterpillar TO4.
The company also have AdBlue (Aqueous Urea solution) available in its bucket for equipment fitted with SCR technology to meet new stringent emission norms. Currently in India, they are the only lubricant company having separate plant facilities to blend AdBlue, claims Ganjoo.
Advancing productivity
ExxonMobil aims to develop breakthrough technologies that guarantee substantially improved energy efficiency. Long component life helps reduce worn equipment disposal and maintenance-related waste, accruing energy efficiency benefits. “Many of our advanced-technology lubricants lower overall traction versus mineral oils, helping to reduce the amount of fuel or energy consumed while operating, and have potential to reduce energy costs as well as associated emission,” says Shankar Karnik, General Manager, Industrial Lubricants, ExxonMobil Pvt Ltd.
The company provides a range of technical services to help keep the machines running at peak efficiency while also extending machine and oil life, reducing downtime and lowering operating costs – thus advancing productivity and energy efficiency.
Reliability
Nearly every business in construction, mining and infrastructure sector is under increasing pressure to lower operating costs and increase efficiency.
High-performance lubricants from GS Caltex offers ultimate reliability at all temperatures, lower oil consumption, significantly lower fuel consumption and specifically extended service intervals, says Jayanta Ray – GM Industrial and OEM, GS Caltex India Pvt Ltd.
Key drivers
Higher engine outputs, improved combustion stability, higher EGR levels, DPF, etc are some of the key drivers observed when shift is happening from emissions to fuel economy. This certainly has an impact on hardware and also on the lubricant used in engines of construction machinery and fleet, says Siva Kasturi, Asia Pacific Regional OEM Manager, Shell Lubricants.
Today, all construction OEMs are continuously focusing on design of new machinery, reliability of their equipment and component performance through strong asset management diagnostic tools. The trends are more focussed towards operational issues, troubleshooting challenges and unscheduled maintenance planning, etc.
Lubricant technology plays a vital role in keeping these machines running reliably and efficiently. The customers today are constantly striving to improve fuel efficiency, energy savings, operational reliability, and enhance competitiveness by avoiding lost output and maintenance costs. Poor lubricants and lubrication practices can cause equipment downtime which can lead a firm to losses. Hence, in today’s operations where severe conditions and cyclic peak loading are the new norm, a lubricant becomes a critical element in the lifespan of any major construction or mining operations
OEMs and end-users in general manufacturing industry are becoming more familiar with the modern advancements in lubricants and lubrication systems including the importance of filtration, cleanliness, regular monitoring of oil through Shell LubeAnalyst.
Fuel consumption
Lubricants are being used for essentially four purposes such that lubrication of the equipment, cooling, protection from environment and cleanliness, according to Anirban Das, Business Manager, SI Group-India Private Limited.
The aforementioned four attributes not only increase the effectiveness and efficiency of the instruments, but also save from fatigue and eventually failure.
Lubricants will help to reduce the metal to metal contact so reduces the friction. Cooling of the equipment will lower down the heat so efficiency will enhance and chances of component wear and tear will be lowered. Whereas, due to lubes the oxidation and corrosion will take care. By virtue of that chances of the rust will be reduced. Clean equipment always gives less of the wear debris so overall the life of the equipment will definitely improve so as down time will reduce.
“With better productivity, direct cost on maintenance, manpower cost and energy cost, all will be positively affected, adds Das.
Fuel consumption is a bigger part of the production cost reduces 2-3 per cent; so any industry will be benefited to reduce the maintenance budget of the equipment with better lubricant.
Latest offerings
Deliver long-lasting protection
Mobil SHCTM Elite is specifically engineered to deliver long lasting protection for machines operating under extreme temperatures in industries such as general manufacturing, metals, energy, and pulp and paper, says Karnik.
Mobil SHC Elite can deliver 12 times the oil life of mineral oils and double the oil life of Mobil SHC 600 synthetic oils in continuous operating temperatures as high as 130C (266F), potentially replacing glycol-based lubricants in high temperature systems. This helps reduce the potential risk of mixing glycol-based products with incompatible mineral oils and most synthetic lubricants.
BS VI Compatible Engine OilsKixx HDX CK-4 15W-40
This is a high-performance heavy-duty premium quality engine oil which exceeds industry and engine manufacturers’ performance requirements. It is formulated using advanced additive technology to provide outstanding protection for on-and off-highway applications, including GHG 17 and EPA 2010 compliant engines of on-highway diesel vehicles using ultra low sulphur diesel (ULSD), as well as 2014 compliant engines for off-highway diesel vehicles, says Ray. It meets API CK-4 heavy duty engine oil specifically formulated for 2017 greenhouse gas (GHG 17) compliant diesel engines designed to meet lower CO2 emissions and improved fuel economy, in addition to EPA 2010 compliant low emission diesel engines with selective catalytic reduction (SCR), diesel particulate filter (DPF) and exhaust gas recirculation (EGR) systems. It is fully compatible with previous engine models and previous API oil service categories like API CJ-4, CI-4 Plus, CI-4 and CH-4.
Extra-long life, high performance hydraulic oil
With most conventional hydraulic oils, equipment runs less efficiently; cycle times are longer; energy is lost. Conventional fluids force the user to deal with shorter oil life. Kixx HVL long life hydraulic oil is engineered so that it can make the equipment more responsive, and operates faster and more efficiently. Its formulation helps prevent varnish deposits that can bog down the hydraulic system. This premium hydraulic oil holds up under higher pressure, and much longer than conventional oils.
High performance fully synthetic gear oil: KixxGearSyn GL-5 75W-90
This is a high-performance synthetic heavy-duty gear oil suitable for use in heavy-duty driven axles and differentials. It is designed for long-drain capability and formulated with a combination of synthetic base oils (poly alpha olefin) and high performance additives.
More credible buy Shell Lubricants provide products and services, which may be a little more expensive, but upon use provide value.
”Our products are a more credible buy as we can quantify, monitor and demonstrate the value saved provided to a customer. Hence, in the long run, our customers derive benefits of lower maintenance costs, lower total cost of ownership, reduced unplanned equipment downtime and more reliable system operations,” says Kasturi.
Shell Lubricants produces products for general manufacturing, power, construction and mining sectors including power engine oils, turbine oils, electrical oils, gear oils, hydraulic oils and greases.
Shell Lubricants has always had a customer centric approach; aiming towards bringing innovative ideas and technology in its products and services.
Addressing need for automatic lubrication
KLT offers high-quality, self-contained automatic single point lubricator (SPL) product line under the brand name Pulsarlube. Pulsarlube products have been successfully launched and distributed throughout the world, including North and South America, Africa, Asia, and Europe, via direct and indirect distribution networks. KLT is represented by Gulf Oil Lubricants India Ltd in India offering the entire portfolio of products and services.
“Pulsarlube automatic lubricators address need for automatic lubrication in industrial manufacturing. to keep machinery in the best condition,” says Tammy Yang, International Business Manager, KLT Co., Ltd.
Applications in which Pulsarlube SPL systems can be the optimal solution:
• Contaminated operating environments.
• Equipment can only be lubricated when it is not running and equipment downtime does not occur often enough to suit the re-lubricating frequency.
• The equipment is out of reach or located in hazardous conditions, like high temperatures and heavy load conditions, which may raise a safety concern from manual lubrication.
Adopting Pulsarlube SPL systems can be highly beneficial anywhere in manufacturing, processing, and/or material handling operations. We have demonstrated improvement in bearing life on account of improved lubrication practices thereby improving your production reliability, adds Tammy.
The electro-chemical (also commonly known as gas type) and the electro-mechanical lubricators are the two major product lines of Pulsarlube. Electro-chemical lubricators, Pulsarlube E and V, generate inert nitrogen gas which is more stable, reliable and less susceptible to ambient temperature fluctuations compared to hydrogen gas type lubricators. The Pulsarlube gas type SPL offers superior performance at competitive pricing, generally 5-10 per cent less than competitor’s.
The electro-mechanical lubricator (Pulsarlube M) can be used for years and lubricate up to 8 points using a divider block; therefore, it helps save cost substantially over manual lubrication while providing the best quality lubrication. Pulsarlube M offers advanced features and benefits users. A large built-in LCD display provides all information needed to assess lubricator and lube point conditions at a glance in an easy-to-read format. High pressure allows the user to lubricate hazardous and out of reach areas and to lubricate multi points which could save the substantial amount of operation cost to the customer.
Aim is to blend best-quality lubricants to enhance equipment life, downtime and simultaneously increase drain intervals.
Sandeep Ganjoo, Sr. AGM (Business development), Apar Industries
Higher engine outputs, combustion stability, among other key drivers are observed during shift from emissions to fuel economy.
Siva Kasturi, Asia Pacific Regional OEM Manager, Shell Lubricants
Long component life helps reduce worn equipment disposal and maintenance-related waste, accruing energy efficiency benefits.
Shankar Karnik, General Manager, Industrial Lubricants, ExxonMobil Pvt Ltd
With better productivity, direct cost on maintenance, man power cost and energy cost, all will be positively affected.
Anirban Das, Business Manager, SI Group-India Private Limited
Pulsarlube automatic lubricators address need for automatic lubrication in industrial manufacturing.
Tammy Yang, International Business Manager, KLT Co., Ltd
Cookie Consent
We use cookies to personalize your experience. By continuing to visit this website you agree to our Terms & Conditions, Privacy Policy and Cookie Policy.