Plasma Arc welding offers better control of the arc and produces cleaner welds
By Edit Team | November 9, 2020 6:45 pm SHARE
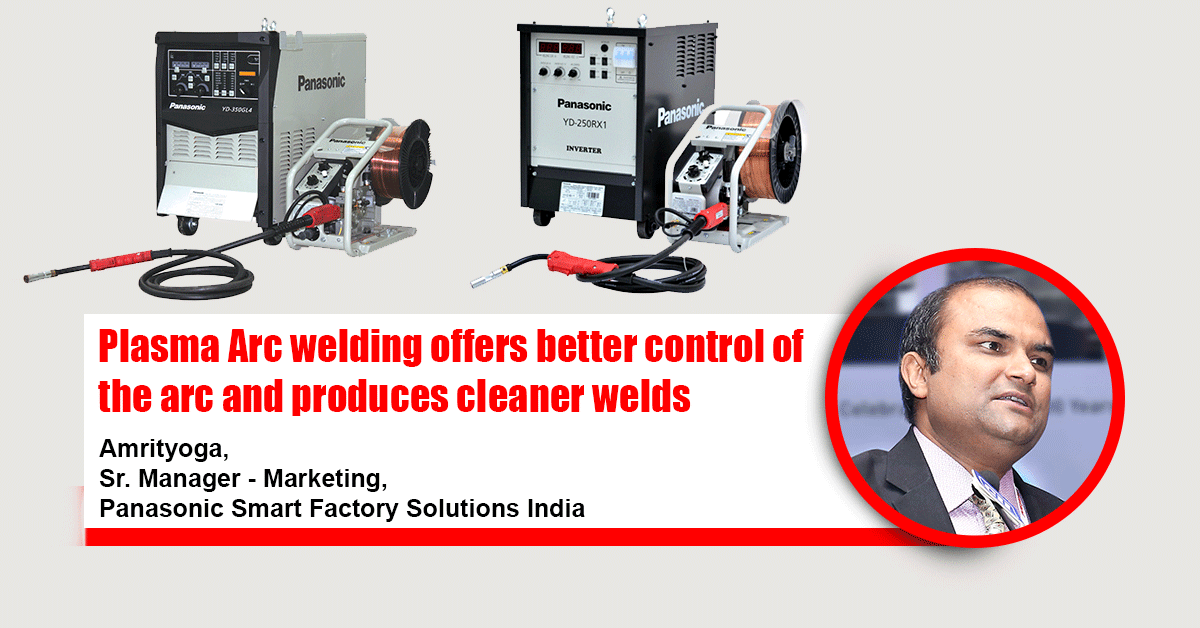
The main advantage of PAW is in the control and quality produced in the part being welded. The torch allows better control of the arc and welds are cleaner and smoother and a smaller heat-affected zone (HAZ) happens in welds says Amrityoga, Sr. Manager – Marketing, Panasonic Smart Factory Solutions India.
What are some of the popular fusion welding methods?
In fusion welding, we use heat to melt the base metals and mostly add filler metal. Commonly used fusion welding processes are Arc welding, Oxy fuel welding, Electron Beam welding and Laser beam welding. The most popular method is Arc welding. Following is the tentative break-up of different Arc welding methods in the year 2019 (based on filler metal deposit quantity).
• Gas Metal Arc Welding (GMAW) – 47 per cent
• Shielded Metal Arc Welding (SMAW) – 42 per cent
• Others (Gas Tungsten Arc Welding (GTAW) +Flux Cored Arc Welding (FCAW) + Submerged Arc Welding (SAW) + Plasma Arc Welding (PAW) etc.) – 11 per cent
What are the different factors which affect weld size, shape and quality?
Variables, as mentioned by AWS D1.1 which affect the weld size, shape and quality, are base materials, filler metal, the position of welding, preheat and welding direction. Other factors include ampere, voltage, travel speed and shielding gas.
What are the advantages of plasma welding? In which industries would you recommend a professional to use it?
PAW (Plasma Arc Welding) method is similar to the GTAW (Gas Tungsten Arc Welding). In this process, an electric arc between a tungsten electrode and the work piece is constricted in a cross-sectional area, its temperature increases because it carries the same amount of current. This constricted arc is called plasma, the fourth state of matter. The process works by ionizing gas, a process that occurs at high temperatures. When ionized gas can conduct electricity. The gas is then used to transfer an electric arc to the work piece being welded. The high heat of the arc will fuse the two pieces of metal.
The main advantage of PAW is in the control and quality produced in the part being welded. The torch allows better control of the arc and welds are cleaner and smoother and a smaller heat-affected zone (HAZ) happens in welds. However, a major limitation is that PAW involves high initial set up cost. PAW being a highly specialized welding process, the training and expertise required is also higher.
Application industry of PAW:
• Marine and Aerospace industry
• Welding of pipes and tubes of titanium
• Repair tools, dies and mould
• Hard facing coating on turbine blade
What is your take on fully automatic welding systems and its use in the existing scenario across different verticals?
There are many benefits of automating the welding process such as an increase in productivity, repeatability, human safety, quality, reduction in labour cost and the consumption of consumables with correct welding parameters. It also reduces production cost, reduction in wield distortion and offers increased competitive advantage.
Traditionally the automotive sector is the biggest user of automatic welding. Almost 90 per cent of the robots go to the automotive industry and the second user is the construction equipment industry. There is a trend to adopt robotic welding in the hospital furniture industry, E-rickshaw, agriculture implement industry and ship building. The main reason being the shortage of labour and enhanced quality requirement especially for export-oriented companies.
Cookie Consent
We use cookies to personalize your experience. By continuing to visit this website you agree to our Terms & Conditions, Privacy Policy and Cookie Policy.