Polysoude presents TIGer bicathode technology
By Edit Team | July 28, 2014 9:35 am SHARE
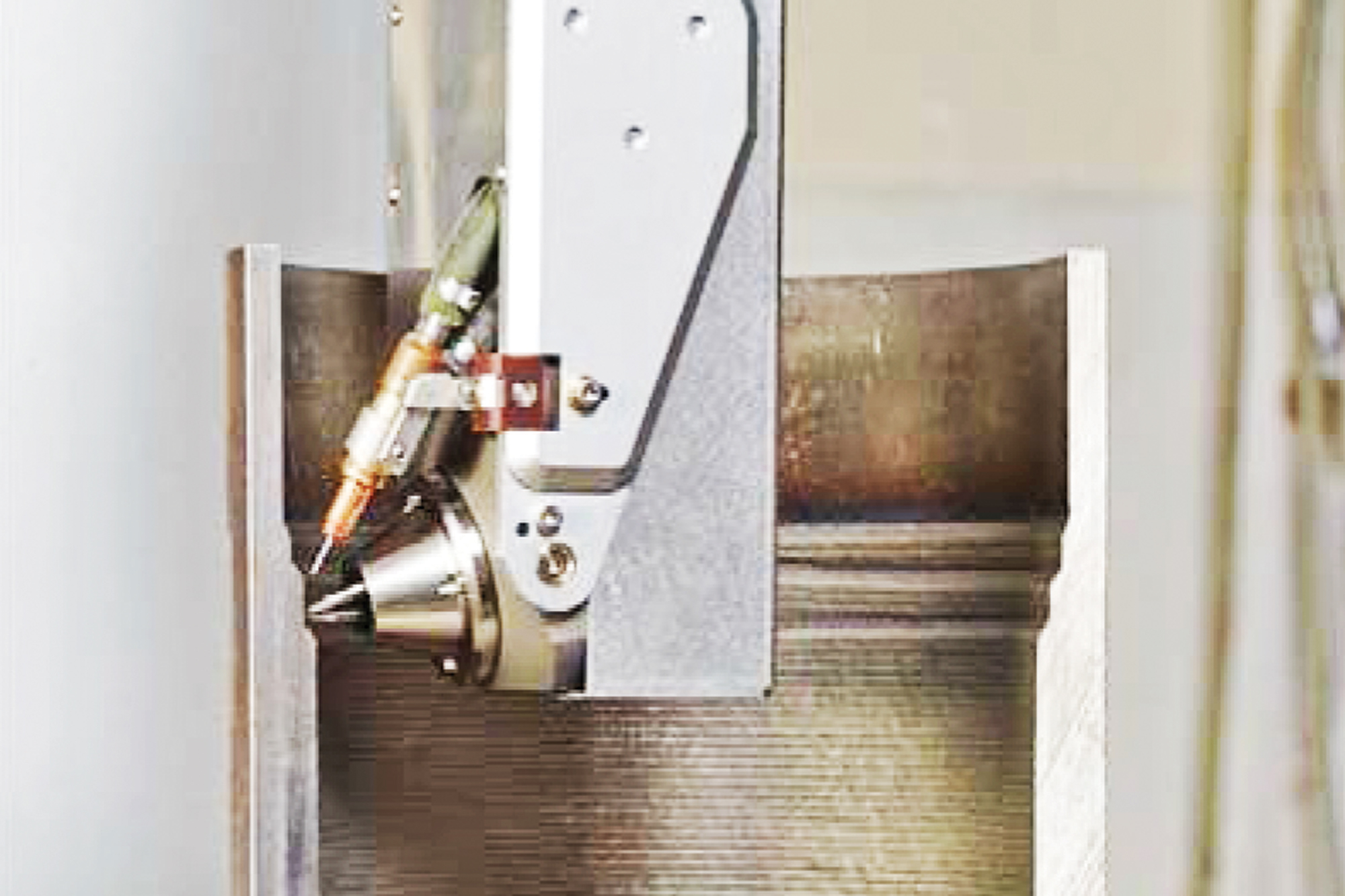
Zero defects and surprisingly efficient operation: Polysoude makes it possible with its TIGer bicathode technology
Today engineering companies, contractors, pipe manufacturers, etc. agree that the GMAW (Gas Metal Arc Welding) process and its variants (CMT, STT, cold arc, etc.) have almost reached their limits in terms of productivity and in particular quality.
However, with GMAW, achieving zero defects is very difficult, but not impossible, believes Polysoude. Most players in the field of offshore oil and gas exploration concerned agree that within the next 3-4 years, the unavoidable combined request for mechanical resistance/fatigue and corrosion resistance will lead to zero defects (zero lack of fusion and zero porosity).
Concerning the TIG process, zero defects is considered normal, but up to now, the issues of productivity and efficiency have subsisted.
Polysoude, has constantly been working on improved technology solutions, and now it has launched its latest development in the TIGer bicathode technology. This involves the juxtaposition of two TIG arcs and thus allows for considerable improvement and efficiency of the process.
The optimisation of the layer thickness leads to significant savings, while the optimised welding speeds go approximately 3 times faster than the conventional TIG Hot Wire technology.
In all cases and whatever the pass thickness is chosen, complete control over dilution is provided with a rate of 1.5 to 2 per cent after the second layer deposited. After showcasing the product for the first time in an exhibition in Germany, Polysoude is planning to organise live demonstrations and cladding tests on samples from potentially interested companies as well.
Cookie Consent
We use cookies to personalize your experience. By continuing to visit this website you agree to our Terms & Conditions, Privacy Policy and Cookie Policy.