Precision and safety are top priorities in the welding industry
By Edit Team | March 8, 2023 9:58 pm SHARE
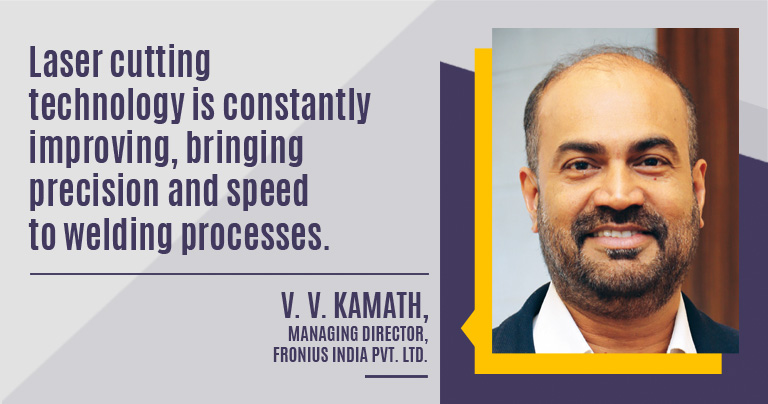
How are automation and robotics advancing the welding and cutting businesses?
Due to the shortage of skilled workers, the welding and cutting industry is turning to automation and artificial intelligence to overcome its shortcomings. For instance, robots can detect and correct path deviations in the programmed path, with the help of the welding system. The industry is also seeking to derive manufacturing costs through data documentation and comparing the budgeted versus actual cost of production, including the cost of consumables and power.
How is the welding industry evolving in providing technology-enabled solutions for industrial infrastructure?
The welding industry has come a long way from using individual welding machines for each process to having 3-in-1 multi-process machines with all functionalities. This advancement in technology has led to cost savings on capital investments, and the ability to use the right process for the job by selecting it within one machine. Additionally, the learning of welding is becoming more user-friendly with the use of apps and games, making it more attractive to younger generations.
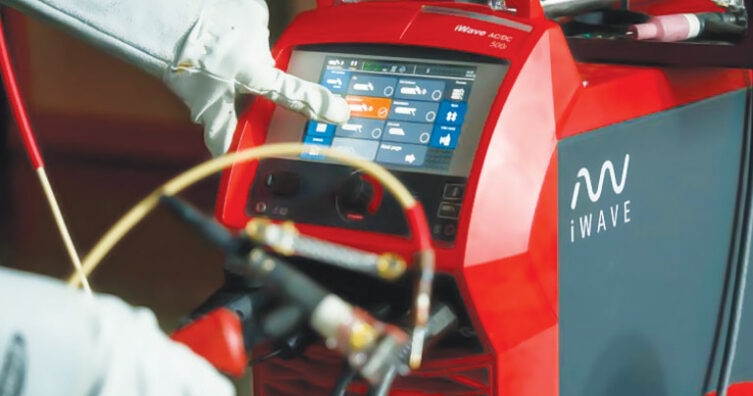
What kind of precision and safety can you expect by adopting technology-enabled welding practices?
With the advancement in technology, precision and safety are top priorities in the welding industry. Welding machines have several safety options that ensure the safety of the operator and the job, such as the Welding Process Standards (WPS), which the operator must follow. The monitoring of the parameters of the welding process can now be automated through the use of upper and lower limits, and any deviations from these limits are automatically recorded and alerted by the machine, ensuring precision and safety.
Where do we need to improve our welding and cutting skills?
To improve welding and cutting skills, the industry needs to focus on establishing more Centers of Excellence with the latest technologies to train the workforce. These centers should provide practical training on advanced equipment, as using outdated equipment would not prepare the workforce for the industry’s current demands.
How are welding monitoring systems benefiting construction and infrastructure practices?
Welding monitoring systems are still in the beginning stages of implementation, but they will be crucial in the future, especially with the increasing use of advanced materials. The construction industry is still heavily reliant on manual or semi-automation processes, and the implementation of monitoring systems may take time.
What investments would be required to promote skill development and training activities?
Establishing Centers of Excellence requires the right kind of investment, including the creation of buildings and seminar halls and the provision of proper equipment infrastructure for skill development. Investing in advanced equipment will help train the workforce to meet the industry’s current demands.
How are laser technologies gaining prominence? Laser technologies are gaining prominence in cutting and welding applications due to their accuracy levels and speed. They require proper fitting of components before welding, and they are predominantly used in automation processes. However, their usage is still less prevalent compared to other welding processes.
Cookie Consent
We use cookies to personalize your experience. By continuing to visit this website you agree to our Terms & Conditions, Privacy Policy and Cookie Policy.