Products high on quality, reliability
By Edit Team | December 18, 2018 10:32 am SHARE
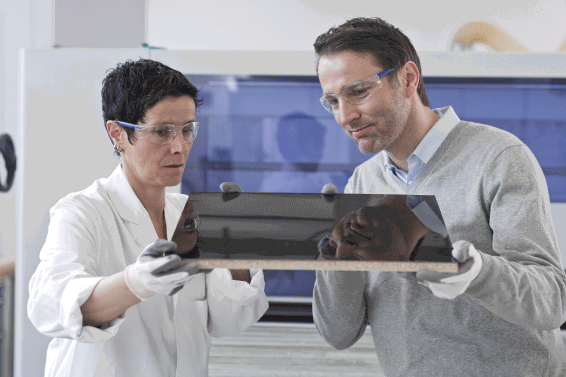
Understanding product design, identifying customer requirements and market needs are some of the vital factors to be considered.
Adhesives and sealants used in the construction industry must be durable, stable and resistant to heat, weather, chemicals and moisture. The reliability factor starts right from design stage where the material need to be tested on range of substrates, over broader regime of environmental conditions. This is backed up with well documented standard application procedures, with clear do’s and don’ts definition.
Ability to study compatibility
“Ability to study compatibility on specific substrates, custom tests in laboratories before executing projects can be another great enabler for driving reliability and confidence,” Pankaj Kumar, Manager, Industrial Adhesives & Tapes Division, 3M India Limited.
Understanding specifics
Adhesives and sealants can be made more reliable by understanding the specifics while designing the product. “A good understanding of the movement and tear strength needed along with the environmental factors associated with the usage scenario, according to Aseem Kumar Singh, National Sales Manager, AIPL Marketing Pvt Ltd.
Identifying customer needs
Adhesives and sealants can be made more reliable by developing formulations based on design parameters and customer requirements. There is a need to clearly identify the customer requirements and need of the market. A clear definition of requirements makes it very easy to design and develop the specific adhesives and sealants. Most of the failures happen because certain requirements were not considered during the design phase, says Shilip Kumar, President – Henkel Adhesives Technologies India Private Limited.
Henkel tries to convince its customers to allow working with them as early as possible; ideally at the design stage itself. This helps us in recommending or developing the right adhesive or sealant. This also helps support the designing of new applications.
“Minor change in the selection of adhesives or sealant at early product design stage can provide much greater bond strength and improved quality,” he adds.
Needs and expectations
“Different customers have different needs and understanding these needs is an important factor when it comes to manufacturing the right products,” says Shenoy Muralidhara, Country & Commercial Director – Huntsman Advanced Materials.
Moreover, reliability is yet another element which customers consider before choosing the product. Working on new products which can meet specific challenges and stringent requirements of the customers is an important element for Huntsman. For e.g. products withstanding extreme climatic conditions, user friendliness, chemical and temperature resistance, are sure to be in demand.
Advanced offerings
GPH VHB tapes and structural adhesives
3M has a wide range of reliable solutions for the building and construction industry to improve safety, productivity and efficiencies through each stage of the project. Company’s innovative and high performing products can be used for a variety of applications.
“We have the broadest range of bonding solutions right from double sided thin bonding tapes, sprayable adhesive, very high bonding VHB tapes, extreme sealing tapes, polyurethane hybrid sealants, functionalised structural adhesive based on different chemistries and passive fire protection solutions for solving and servicing needs of the industry, says Pankaj Kumar, Manager, Industrial Adhesives & Tapes Division, 3M India Limited.
Some of the recent advancements and disruptive changes in these solutions include introduction of newer products like GPH VHB tapes and structural adhesives which can with stand high temperatures process. Another example is fire stop water barrier FWBT tape which when used in accordance with relevant UL systems can water seal and prevent smoke and fire ingress during fatalities thus driving a sea change making process simpler and life safer for the occupant.
D-3 Grade water resistant wood adhesive
AIPL Marketinghas five different variants of adhesives and three variants of silicone sealants specifically designed to cater to the different climatic conditions of India.
“Our most advanced offering included D-3 Grade water resistant wood adhesive that can withstand 48 hours of cold water resistance and one hour of boiling water resistance. For sealants, we have a neutral cure prepared silicone sealant adhesive that offers excellent adhesion weatherproof performance in multi-purpose sealing applications and a sprayable single component, self-expanding polyurethane adhesive with high thermal and acoustic insulation properties, says Aseem.
UV-curing hotmelt
Henkel’s innovative UV hotmelts belong to the group of radiation-curable adhesives. They are solid, mono component and are processed at temperatures of about 100 C. They contain acrylates and photo initiators, which are activated by UV light to form polymers. TECHNOMELT UV hotmelts fully cure in fractions of a second and can be processed immediately. Being VOC and solvent free, the UV-curing adhesives are the way forward, says Shilip.
”Traditional technologies (foil lamination and traditional coating) for generating high-glossy effects include the application of a high-gloss film laminate to wood based panels. However, this process is cost-intensive and the use of paints and varnishes on melamine faced panels is a difficult task. This is mainly because the primers used here offer poor adhesion on melamine and are not as flexible as a UV-curing hotmelt,” he adds.
In ‘Fusion Coating,’ Henkel’s UV-curing hotmelt, Technomelt CHS 370 UV, is applied directly to the melamine faced panels where it acts as a primer for one or several further coats of lacquer that create the desired high-gloss effect. It enables creation of high-glossy finishes which proves less costly than the lamination of high-gloss films on wood-based panels.
Barrier Koat and Klad X
Huntsman offers an extensive range of adhesives and sealants that meet the varying needs of a number of industries. The recently launched Barrier Koat and Klad X as a part of its Araldite Builder Range.
“Barrier Koat is used to combat leakage and Klad X is used for vertical cladding of marbles. With a fast bonding time of 30 minutes, this high strength adhesive is suitable for outdoor application and large projects, says Shenoy.
Additionally, the Araldite Karpenter range recently came out with Karpenter Plus, a high-grade adhesive for the wood industry, he adds.
Factors hampering efficiency
The efficiency of sealants is greatly driven by application consistency in bond line, ultimate cure, and time taken for it cures completely which is a very critical. These issues can be circumvented with broad based solutions which 3M can offer with VHB tapes which give faster bonding, consistent bond line, with pressure sensitive adhesive technology with no dependency on time for cure, says Pankaj.
Structural gaps
Factors like the movement associated with the thermal coefficient of various surfaces have a major role to play in the efficiency of any sealant. Major scale applications like building construction cannot undermine even the smallest of factors to ensure proper results and provisions like structural gaps to counter thermal expansions also play a major role, believes Aseem.
Lack of understanding
Surface preparation of substrates, right application tools, and right sealant product for the application plays an important role in how well it seals and sustains. Lack of understanding of the requirement, leads to the sealant being inefficient, says Shilip.
Poor quality products
Wrong selection or application of a product is the major factor which can hamper the efficiency of any sealant. Having sufficient knowledge of products and its end-user application methods is imperative as it will only help make an informed decision before choosing the right adhesive and sealant. Moreover, availability of poor quality products at low cost is also another factor that can lead to significant hampering, says Muralidhara.
Considerations for picking right quality
Reliability, credibility of completed applications
Factors driving right quality selection at a broader level include, reliability, credibility of completed applications in long run, ease of processing, says Pankaj. This is backed up with detailed study data on durability with technical dossiers defining product usage and right applications go a long way. Other considerations include compliance to international standard systems like ASTM, UL, BS and other relevant standards.
Understanding properties
For choosing the right quality, engineers will have to understand the properties of products and then choose the ideal fit for their application, says Aseem. Budget limitations should not influence the right application especially at critical points of construction. The parameters to consider are the shrinkage or expansion tolerance, area coverage, flexibility, bond strength, substrate and base of the sealant used.
Some of the factors for picking the right quality are:
Substrate type: steel vs aluminium vs zinc.
Application method: spray, roller, dip or other.
Curing conditions: moisture cure, heat cure, UV curing, room temperature curing or other.
Environmental exposure condition: UV, humidity, dust, oil (engine oil, transmission or other).
Expected performance level: torque value, shear strength, impact or any other mechanical test requirement.
Understand quality of substrates
There are many options of adhesives and sealants available with each having its own set of advantages, specialties, and limitations.
“There are numerous criterions involved in order to choose the right adhesive for the job, one of them being – the surface that needs bonding and the atmosphere in which one is bonding the substrates, says Muralidhara.
Bonding processes and performance parameters
Moreover, understanding the mechanical stress and environmental conditions on the bond needs to be taken into consideration too. Furthermore, the bonding processes and performance parameters of the adhesives and sealants are some of the key factors which need to be considered for picking the right quality. Customers also need to have an in-depth understanding of the right brand and the right grade of products before finally choosing it.
Factors driving right quality selection at a broader level include, reliability, credibility of completed applications in long run, ease of processing.
Pankaj Kumar, Manager, Industrial Adhesives & Tapes Division, 3M India Limited
For choosing the right quality, engineers will have to understand properties of products, then choose the ideal fit for their application.
Aseem Kumar Singh, National Sales Manager, AIPL Marketing Pvt Ltd
Adhesives and sealants can be made more reliable by developing formulations based on design parameters and customer requirements.
Shilip Kumar, President – Henkel Adhesives Technologies India Private Limited
Bonding processes and performance parameters of the adhesives and sealants are some of the key factors which need to be considered for picking the right quality.
Shenoy Muralidhara, Country & Commercial Director – Huntsman Advanced Materials
Cookie Consent
We use cookies to personalize your experience. By continuing to visit this website you agree to our Terms & Conditions, Privacy Policy and Cookie Policy.