Safe machine interlocking systems for hygiene-sensitive locations
By Edit Team | May 25, 2022 11:35 am SHARE
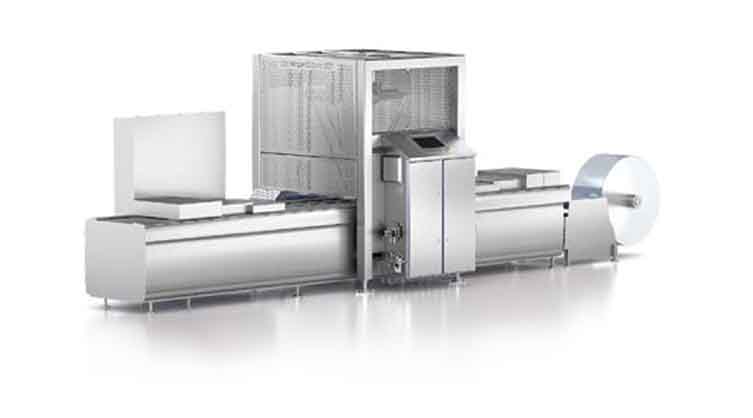
In the SAC Loader, Singer & Sohn GmbH has developed a compact, flexible and powerful system for the packaging of food items, a truly multi-talented insertion robot.
For around three decades, Singer & Sohn, a family-run business now in its second and third generations, has been the renowned manufacturer of systems for packaging, temperature control, and handling of food items.
“We focus completely on the food business,” Christian Singer, Representative, Singer & Sohn, said of the organisations concentration. Meat processing and sausage making account for about 60 percent of our systems. Baked products, seafood, confectionary, and pet food take up the rest of the space. The firm’s systems rely on automation, ranging from linear automation to six-axle robots, and the company is dedicated to efficient, dependable, and safe operation.
The SAC Loader, which is known for its exceptional adaptability, is no exception. The primary aim to develop this system was to offer an extremely multi-talented insertion robot solution. This system is also capable of handling products like steak, slices of sausage, hamburgers, pieces of cheese, and salmon fillets.
From the infeed conveyor to the handling station
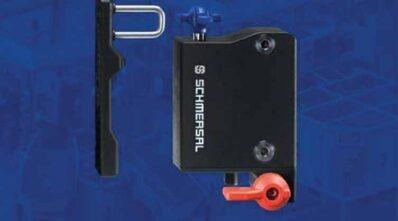
The AZM300 solenoid interlock was developed according to the principles of hygienic design.
The workflow remains to be the same. The inserted products make their way to the handling station via the infeed conveyor. Later, an intelligent camera sensor determines the position and orientation of the incoming product. Based on the sensor data, a robot in delta configuration grips the product and inserts it into the packaging. The picker can also grip or suck in products that have already been packaged and place them in boxes or crates. The packaged goods are then conveyed away via the outfeed conveyor. With a range of selector programmes, the system can be quickly changed over to new products, formats, and packaging.
As the SAC Loader packages food, a design consistent with the principles of hygienic and design was both essential. This includes no dead spaces where contamination can accumulate. The entire system may be cleaned using foam, further, cleaning High-pressure cleaning at up to 28 bar is possible.
Exposed installation of the safety switchgear requirements applicable in various production and packaging systems in the food industry, are toxic to the electrical components.
Majority of these components can be housed in protected switch cabinets and boxes, although the safety switchgear for safety guard monitoring can’t do that. These devices must be installed in an exposed location near the safety guards.
If the position of the safety guards on food processing machines need just monitoring, then that can be obtained through the safety sensors. Often, as is the case with the SAC Picker, you need to prevent operators from opening the safety guards and stopping the process.
In such situations, it’s critical to install solenoid interlocks. These must be equipped with mechanical components as they are responsible to keep the safety guard enclosed until the hazardous movements in the work are halted.
For such applications, conventional solenoid interlocks are unsuitable, as they have openings for locking and interlocking, however, they lack a hygienic design. The AZM300 solenoid interlock is different, and has been specially designed by Schmersal for applications in food processing facilities.
An innovative solenoid interlock
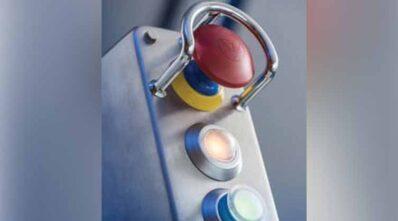
On other machines, Singer & Sohn uses the N range of command and signaling devices.
The main feature of the AZM300 is a new type of solenoid interlock in the shape of a Maltese cross, which engages in the actuator in the door. There are no dead spaces or zones in which material can collect. In addition, with degree of protection IP 69, this solution is also suitable for use in areas in which machines are cleaned with a high-pressure cleaner.
This is exactly what the requirements profile of the SAC Loader demands and led to designers at Singer & Sohn choosing precisely this solenoid interlock, which is suitable for uses up to PL e in accordance with EN 13849 or SIL 3 in accordance with EN 61508. It also has a number of other benefits. The latching force for example, i.e. the non safety- related interlock function, can be set when the safety guard is unlocked. This allows the interlock system to be carefully adapted to individual requirements.
The AZM300 uses a secure RFID sensor for identification and coding of the actuator. This makes it possible, among other things, for the user to choose between three types of coding and thereby determine the appropriate level of anti-tamper safety:
The solenoid interlock has proven its worth in previous SAC Loaders and the designers at Singer & Sohn have come to expect nothing less. In addition to the AZM300, the company also uses other solutions from Schmersal.
In some systems, the HMI is fitted with command and signaling devices from the N range of products. This range has been specially developed for use in the food industry and satisfies the requirements of hygienic design. The AZM200/201, which also offers the benefits of integrated RFID sensor technology, is often used to safeguard hazardous areas by means of larger safety guards in non-hygiene sensitive areas.
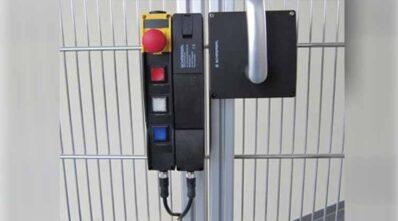
The AZM201 is often used to safeguard non-hygiene-sensitive hazardous areas with larger safety guards.
And when it comes to monitoring the position of safety guards on systems foamed and cleaned at high pressure, the stainless steel CSS30 safety sensor is without doubt the right solution.
The overview reveals that the choice is that of the user. In practice, many machine manufacturers opt for the Safety Field Box including, but not only, those who have previously used simpler integration options such as IO Parallel and the safety installation systems, and are familiar with their benefits.
They then decide to take the step over to the Safety Fieldbox, which offers an even higher level of integration of both the safety- related and operational signals from safety switchgear devices.
www.singer-und-sohn.de http://www.schmersal.in/
Cookie Consent
We use cookies to personalize your experience. By continuing to visit this website you agree to our Terms & Conditions, Privacy Policy and Cookie Policy.