Technology and market trends to transform PEB sector
By Edit Team | November 11, 2021 8:19 am SHARE
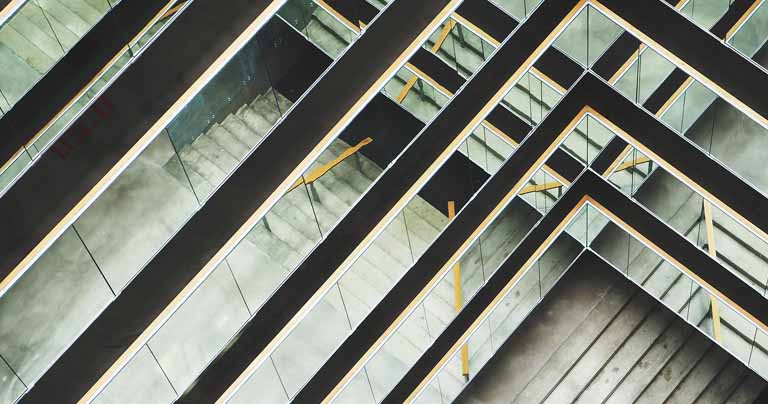
Discussing the present trends, experts from the PEB sector share their optimism on how technological advancements are redefining the structural trends and designs for PEB in India.
Market dynamics for pre-engineered buildings in India
Pre-engineered buildings market is expected to grow due to several factors. The rising demand for green buildings and the growing need for shortening the construction cost and time, along with increasing demand for lightweight building structures (with ease of installation and modular) are expected to drive the market growth in the forthcoming years.
According to Puneet Mathur, Business Head – Building Solutions, Tata Bluescope Steel, “Single storey buildings are expected to see high demand owing to rising investment in logistics, infrastructure and industrial constructions. The economic advantages of utilising pre-engineering building systems have enabled architects to revolutionise the way we build structures with an increased demand for a one-stop window, hassle-free execution and early occupation of the premise.
According to Dr. Abhay Gupta, Director, Skeleton Consultants Pvt Ltd – We need to change the mindset towards PEB. When we say rapid, it doesn’t mean that we only construct a component of the building rapidly. It is the pre-engineered building per se when we all know. The real mindset towards PEB is that the rapid construction in every component of a building.
Apart from industrial and commercial segments, PEB is finding a big movement in housing sector also. Why housing? There’s a huge shift of the population from rural to urban areas and this has created a huge gap between the demand and the supply.
Impacts of digitalisation in PEB sector
Adapting newer technologies for optimising operational efficiencies has become the new normal. The use of advanced software and 3D modelling for structural detailing and designing for precision engineering has always been a part of our customer-centricity.
Noting the impacts, Puneet highlights that– customer demands have drastically changed over the last 2 years, compelling us to ride the digital wave with full preparedness. “However, we have further improved our digitisation efforts by the introduction of new-age enhanced digital tools, to further achieve precision and operational efficiency.” Right from design & engineering, to swift supply chain integration and disruption in logistics have sooner become a reality. Being digitally inclined to us has ensured timely project delivery and healthy profitability.
Opportunities and challenges towards regulations for efficiency in PEB
The greatest challenge for prefabricated and pre-engineered buildings in India is the perception shift from conventional construction to the pre-engineered steel structures. No doubt it is changing over the years, but the pace is still slow, and people are still not experimenting enough.
Volatility in steel prices remains as one of the biggest challenges in the PEB industry. Most of the PEB contracts are fixed-price contracts, and any exposure to steel price increase erodes the margins and profitability of the projects take a hit. Sharing his opinion on it, Puneet feels “this naturally has an adverse impact on the overall operations and overcoming these challenges is a struggle. On the other hand, post-implementation of GST and granting infrastructure status to the logistics segment; the PEB industry has shown remarkable growth due to a surge in demand for high-quality warehousing from E-commerce and logistics coupled with emerging opportunities in metro rail stations, depots, airports, ports and the new Greenfield factories to produce steel, building materials, consumer durables, automobiles, auto, chemicals, pharma, textiles, and many others.
Redefining the business prospects for infrastructure and PEB sector
The Indian Pre-Engineered Steel Buildings (PEB) market is experiencing strong growth powered by infrastructure development and the growing popularity of PEB systems within the industrial sector. Sectors such as automotive, power, logistics, pharma, FMCG, and capital goods provide massive growth opportunities for PEBs in India. Noting the same, Puneet highlights “With technological advancements turnaround time and scalability have gained immense importance within the construction industry. Growing as an off-shoot of PEB industry, is the new Heavy Engineering and larger Infrastructure projects such as airports, international terminals, power plants, ports etc. that require heavy steel structures and a different approach in comparison to PEB.” There are investments happening in sectors like health, retail, urban development, industrial, aviation, hospitality to name a few that add up to greater prospects of infra projects in PEBs.
Whereas, as per Dr. Abhay’s views, “Affordability and sustainability are the key factors that drive the demand for PEB. We don’t see concrete structures being in very good conditions after a few years. Steel is a material which is very consistent, good and reliable.” It is long-lasting, durable though the cost is a bit higher. But with proper designing and detailing, an efficient construction can be done with cost-effectiveness.
PEB gives us speed, quality, safety, sustainability, good thermal acoustics and fire-resistant characteristics, and lifecycle cost. All the brick walls can be replaced with prefabricated sandwich wall panels. These walls are very rapid, very efficient, lightweight and costing more or less the same.
“When we start rapid construction, we have made one component of the building rapid and if the other components are not rapid then our entire objective is lost. So, these walls help us to get the rapid construction”, adds Abhay.
Transforming PEB structures with latest technologies
Technological improvements over the years have contributed immensely to the enhancement of quality of life through various new products and solutions; especially in construction. “Technology when backed by R&D efforts, paves the way to innovation and product superiority! One of our innovative products, that works to our advantage, our X factor; is the MR24 Roof System, offered as part of BUTLER® Building Solutions,” Puneet explains. The MR-24® roof system is the industry’s first and finest standing-seam metal roof, with more than fifty years of proven in-place weather-tight performance. It not only addresses your top-end functionality; but combines efficiency with aesthetics and sustainability. Fixed with specially designed clips MR24 Roof offers wind resistance in high wind areas with minimal impact.
Dr. Abhay on the other side highlights the significance of Light gauge Steel Frame Structures (LGSF). The light gauge frame system is used in the small components, small housings and wall panels. The government is targeting to construct 11.2 million houses by 2022 in urban areas and about 10 million houses in the next three years in the rural areas, which is a huge number. There are new methods and technologies identified, which will help us to bridge this gap.
Future prospects
We should adopt the lateral load resisting system, the gravity system, the horizontal diaphragm and the walls as a complete integrated solution. All of these when we make with the rapid technologies of this time, you get beautifully finished slab systems. There are several options in prefabricated sandwich panel system and all these options have been practically tested and are being done in our country only. So, these are the new wall systems which will help us to do the rapid construction.
Cookie Consent
We use cookies to personalize your experience. By continuing to visit this website you agree to our Terms & Conditions, Privacy Policy and Cookie Policy.