TimeTwin Digital: top deposition rate, thanks to two wire electrodes
By Edit Team | February 17, 2014 10:02 am SHARE
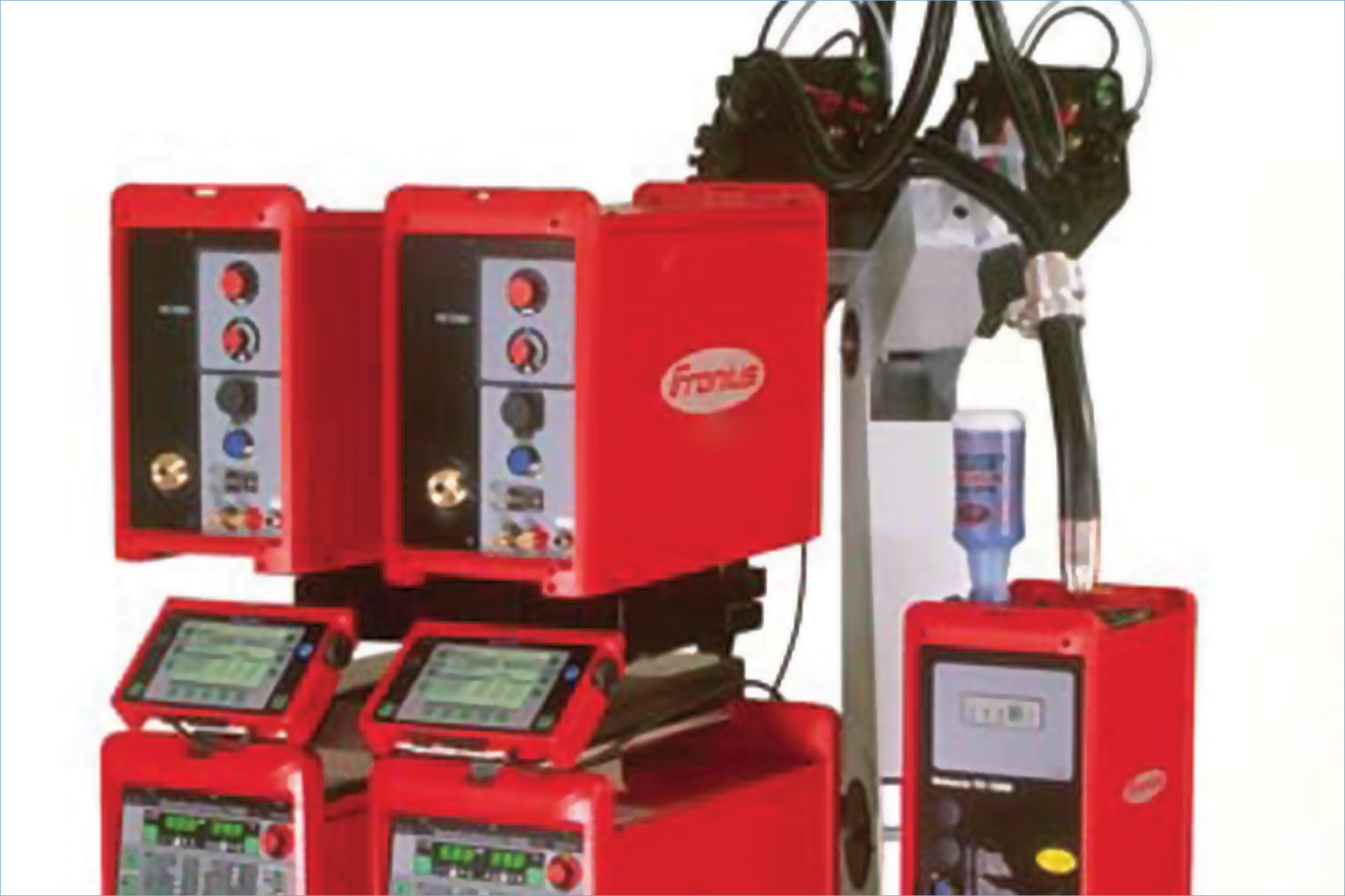
Atandem welding process by Fronius and which makes electrical insulation of the two electrodes easier
Demand is increasing steadily for welding processes that assure superlative welding quality and simultaneously boost profitability and cost effectiveness. This is feeding the development of high-performance welding processes having an increased deposition rate. These methods are characterised by a deposition rate of more than 8 kg/hr in the case of steel. Users are converting this greater deposition rate either into larger seam cross-sections or into greater welding speeds. Higher deposition rates can be achieved by enlarging the cross-sectional area of the wire or by using more than one flash-butt electrode at the same time. The tandem process, in which two electrodes weld simultaneously, falls into the second category and is the subject of this article.
Welding process
If two simultaneously welding wire electrodes are employed in MSG welding, two variants are possible: In twin-wire welding, the two wire electrodes are guided jointly through the same contact tube which means that both electrodes have same electrical potential on a continuous basis.In the case of tandem welding on the other hand, each electrode has a separate contact tube. The contact tubes are electrically insulated from each other. It is thus altogether possible that the two electrodes have different electrical potentials.
TimeTwin by Fronius is a tandem welding process. On account of the electrical insulation of the two electrodes, two electric arcs are generated that can be adjusted and optimised independently of one another. Both the performance and additional parameters — such as lengths of the two electric arcs — can be controlled separately, which means that it is possible to achieve a stable electric arc and perfect drop release for both electric arcs.
A further advantage of this principle is the fact that either of the two electrodes can be defined as the master or the slave. This means that the electrode which has the leading role in the welding process is not defined unalterably. As a result, both welding directions are possible, and this in turn enables a reduction in the cycle time. It is also possible to use just one electric arc, i.e. to perform single-wire welding.
It is also possible to choose the type of electric arc (standard electric arc or pulsed electric arc) of the two electrodes independently. In essence, there are four variants:
* Pulsed electric arc in one electrode/ pulsed electric arc in the other electrode (most common variant)
* Pulsed electric arc in one electrode/ standard electric arc in the other electrode (for achieving maximum welding speed and gap bridging)
* Standard electric arc in one electrode/ pulsed electric arc in the other electrode (for deep penetration)
* Standard electric arc in one electrode/ standard electric arc in the other electrode (least common variant).
In standard practice, TimeTwin is only used in automated applications. The first of the mentioned variants, i.e. two pulsed electric arcs, is realised in the majority of applications. Also, the construction-material transitions are usually phase-shifted by 180 degree.
Welding equipment
For the tandem process TimeTwin, the availability of two power sources is essential because two electric arcs need to be powered. However, it is not sufficient to simply adapt the power sources to this process. Instead, all the equipment must be adapted. Basically, that includes the welding torch, the wire advancing mechanism and the cooling circuit. In general, Fronius sees itself as a company offering complete welding systems which are constructed modularly. Fronius welding systems are highly robust and enable “plug and weld”.
Power source
A substantial enhancement was realised in the power sources for the tandem process TimeTwin: Compared with the power sources previously used, the new power source series TimeTwin Digital 4000/5000 was converted to all-digital technology. It is also possible to control the welding process in a completely digital manner. A digital signal processor (DSP) takes care of this control. The analogue welding voltage/ analogue welding current are registered on the electric arc. These analogue values are converted to digital signals by an analogue-to-digital converter which feeds the digital signals to the DSP. The DSP then controls the welding process so as to adjust the actual values to the desired/ nominal values. This all-digital control principle yields considerable benefits:
The electronic control circuits are now very small and compact because the entire control is handled by one electronic module, the DSP. Along with the inverter technology, this entails that all the power sources can be very lightweight and compact.
System control can be very quick and flexible which strongly influences the welding result. It is possible, for example, to react very quickly to changes in the separation distance between the contact tube to the work piece so that the length of the electric arc can be controlled very flexibly.
The digital control is not vulnerable to any temperature drifts. As a result, the all-digital control is characterised by outstanding long-term stability.
It is also vital that the two power sources communicate with each other. This is essential for the synchronisation of the two electric arcs and consequently the construction-material transitions. There was a technical innovation here too: in the device range TimeTwin Digital 4000/5000, the communication between the power sources takes place via a data bus on which data transmission rates of up to 10 Mbits per second are possible.
The two power sources for this process are standard power sources which have an installation set for the data bus and the appropriate software. This brings with it the considerable advantage that the two power sources can be disconnected again at any time and can thus be used as separate power sources. In this way, the spare parts do not differ from those of standard power sources, which substantially simplify the logistics.
An additional advantage of this system is in the case of automated applications, the robot can activate the two power sources as a single power source, which simplifies practical use considerably. An enhancement compared with previous systems was also introduced in the communication between the robot interface and the power source, whereas, in previous systems, up to 40 lines ran in parallel between the power source and the robot interface, communication in the new range of devices TimeTwin Digital 4000/5000 takes place via a LocalNet or a field bus. Both the LocalNet and field-bus solutions minimise the wiring costs as well as reduces interference from noise signals.
Welding torch
In the tandem process, two wire electrodes must be maintained for the welding process. Although in this process the contact tubes of the two electrodes are electrically insulated from one another, they also run through a common gas nozzle which entails that the two electrodes must share a common welding torch. Fig 5 shows a schematic representation of the foremost section of the torch. Here, the electrical insulation of the two contact tubes can be seen very clearly.
A major feature of the welding torch for TimeTwin is the cooling of the torch. Because a lot of heat is generated in this process, and this heat must be subsequently dissipated. The gas nozzle is cooled all the way to the front and good heat dissipation is also ensured in the area of the contact tubes.
The Robacta Drive Twin, one of the two types of welding torch, is a push-pull torch, having an additional wire advancing unit in the torch. In it, two flexible tube packages are guided between the two wire advancing mechanisms and the torch. This torch is used specifically in the case of soft and fine wires, making high-precision wire advancement possible. Besides, a push-pull torch is required if splash-free ignition SFI is to be used. Then there is Robacta Twin Compact in which the two electrodes are guided between the wire advancing mechanisms and the welding torch in a common flexible tube package. Although the later torch is not a push-pull torch, its slim-line construction brings considerable advantages as far as accessibility is concerned.
Cookie Consent
We use cookies to personalize your experience. By continuing to visit this website you agree to our Terms & Conditions, Privacy Policy and Cookie Policy.