WELDING & CUTTING: ADVANCED TECHNIQUES AND PRACTICES
By Edit Team | August 9, 2021 5:01 pm SHARE
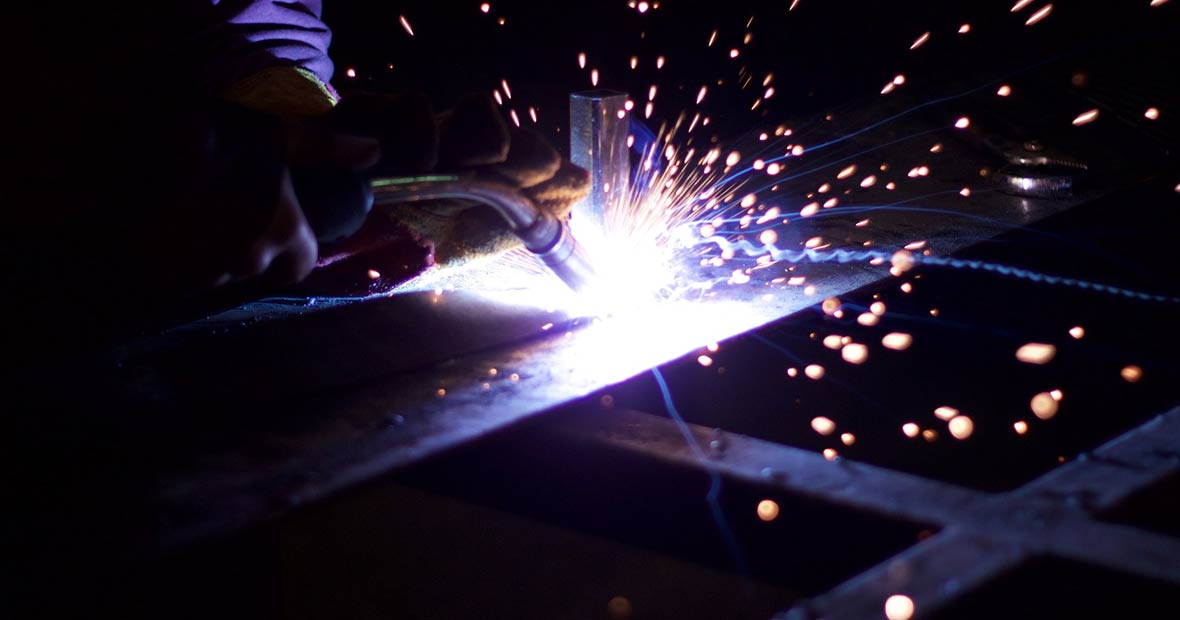
Automation and mechanisation are critical for welding and cutting industry as the players are coming up with advanced solutions to match the upcoming industry requirements.
Welding and cutting play an important role in various industries ranging from infrastructure construction, automotive, transportation, process industries andoil & gas. In recent times, the Indian construction and infrastructure sector has grown leaps and bounds with many new projects the above-mentioned segments. Use of metals especially structural steel is growing exponentially in constructions where welding and cutting play an important role to create the structural frameworks.
Evolution instructural welding technology
In welding,there are different modes like manual, semiautomatic, automatic, mechanized, robotic etc. N. Rajasekaran, National Secretary, Indian Welding Society, says, “In many applications, we use manual mode and it is time to move towards mechanised and automated modes of welding processes.”
According to him, there is a rapid progress in the modern technology which is required in many types of welding applications ship building, boiler mounting structures etc. In India, around30 to 50 percent of structural welding is done by shielded metal arc welding (SMAW) process because it is a versatile process and can perform welding in all positions. In the submerged arc welding (SAW) process, the welding position is restricted to downward and horizontal positions. Overhead position and vertical positions are not possible but this is the preferred method for heavy structural applications.
Gas metal arc welding (GMAW) is another method used for heavy structural infrastructure applications. This is widely used in robotic applications in the automotive sector, but it can also be used in infrastructure applications. The shielding is being given by Argon+CO2. Especially for steel, 80 percent Argon and 20 percent CO2 can be used for shielding.
Lean management in welding
Welding consumes a lot of energy and other resources ranging from gas, metals and other supporting materials. So, it is imperative for the welding process to be costeffective and economical. By adopting lean practices, this can be achieved, according to Satish Sawant, Director, Institute of Welding and Testing Technology (IWTT). “We need to adopt new technologies andautomation in welding, but along with that we need to have control over the quality of our weld.For this we have to implement lean management practices in welding,” he says. The customer is interested in achieving top-class quality at minimum cost.
Material wastage is another major issue. We always focus on the welding where cutting is also equally important. Selection of cutting process is also very important for cutting in the right way thus minimizing material wastage. Improper storage of materials also leads to added cost.
Availability of trained welders is a major challenge. It is estimated that there will be a requirement of 22 lakh welders by 2024. “Most of the welders have good skills, but they don’t follow the standards. So, they need to be qualified as per the standards and if we do appropriate qualification, before starting the job, that can also help us to minimise cost,” says Satish.
Selection of the equipment also plays important role in cost saving along with maintenance. Even if we buy the best machine available in the market, it has no use unless we maintain it. Power saving solution is another important aspect in cost-effective welding. New technologies coming up like IGBT can help us in the saving on power.
Power resources advancements
Advancements in power sources is significant in the recent past, especially in MIG welding. Productivity in welding processes has improved over the years. Compared to the manual arc welding, the latest processes provide up to 7.5 times faster welding. “If you want to improve your productivity in welding applications, you can move to mechanised MIG welding. The advantages of going into mechanised is decrease in the volume of weld metal input.In mechanised applications, the number of passes keep reducing. The operators or welders need minimal training for mechanised operations, according to NimeshChinoy, Director – Sales & Marketing (SigmaWeld), Electronics Devices Worldwide.
Over the last 20 years, inverters have become the norm and we moved away from the traditional thyristors and transformers. “Digital power sources, which enable you to have a lot of programming possible with the advanced AI features inbuilt into the power source for ease of welding, and modular technology,” says Nimesh. We have been traditionally using largely a single power source and if something goes wrong, we have to stop the entire setup. With the new technology, within one equipment, you have many small power sources. Typically, these come in multiples of 200 Amps, according to Nimesh.
Thermal cutting processes
While the mechanical cutting processes are accurate and there is absolutely no heat impact, the processes are costly as well as slow. According to Prashant Chaturvedi, General Manager, Messer Cutting Systems India, there are new cutting processes evolved in the market using oxy-fuel, plasma and laser. “In the oxy-fuel cutting, we use oxygen and fuel as acetylene, LPG or BMCG. In plasma technology, we use heat of plasma to cut. The latest one, the buzzword that the whole industry talks of, is laser cutting. Today, all three thermal cutting processes of laser, plasma and oxy-fuel equally exist in our engineering world,in their own space,” he adds.
During welding, we need to prepare different types of joints. So, in the cutting process itself, you can use the beveling tools now and reduce your post cut operations of preparing the weld joints. If a right tool is used, you can straight away cut the plates and then a small finishing can give you a ready plate.
So, what plate or metal you’re going to cut, at what thickness and finish requirement, all together would decide which process is going to be used. Laser would have the least running cost, but at the same time, it has a heavy investment. A laser cutting machine would not cost much higher maybe 3-4 times to an oxyfuel cutting machine, but oxyfuel process would require continuous consumption of the gases. And similarly, plasma process can be the fastest process, but at the same time, it would also have the consumable involved. So, you have to make a holistic approach in terms of your application.
“We have a range of equipment where we have both the option of plasma cutting and laser cutting are available which is a unique combination,” adds Prashant.
Looking ahead
Welding started and continued in the country for a long time following the traditional manual methods. However, with the technology evolution in other industry segments, welding and cutting segment also gathered momentum in adopting new technologies and solutions for an economic, productive and efficient operation in various processes. Welding sector has seen a tremendous growth in the recent past with wider applications in various industries. Going forward, the market is expected to gain prominence in embracing more advanced process and technologies that is going to further modernise the Indian welding and cutting industry.
—
“In many applications, we use manual mode and it is time to move towards mechanised and automated modes of welding processes.” – N Rajasekaran, National Secretary, Indian Welding Society.
–
“Along with adopting new technologies in welding, we need to embrace lean management practices for the cost-effective welding operations.” – Satish P Sawant, Director, Institute of Welding & Testing Technology.
–
“Digital power sources, which enable you to have a lot of programming possible with the advanced AI features inbuilt into the power source for ease of welding, and modular technology.” – NimeshChinoy, Director – Sales & Marketing (SigmaWeld), Electronics Devices Worldwide.
–
“Today, all three thermal cutting processes of laser, plasma and oxyfuel equally exist in our engineering world, in their own space.” – Prashant Chaturvedi, General Manager, Messer Cutting Systems India.
Cookie Consent
We use cookies to personalize your experience. By continuing to visit this website you agree to our Terms & Conditions, Privacy Policy and Cookie Policy.