Wheelabrator’s multi-table shot peening machine – DRT
By Edit Team | July 25, 2017 5:26 am SHARE
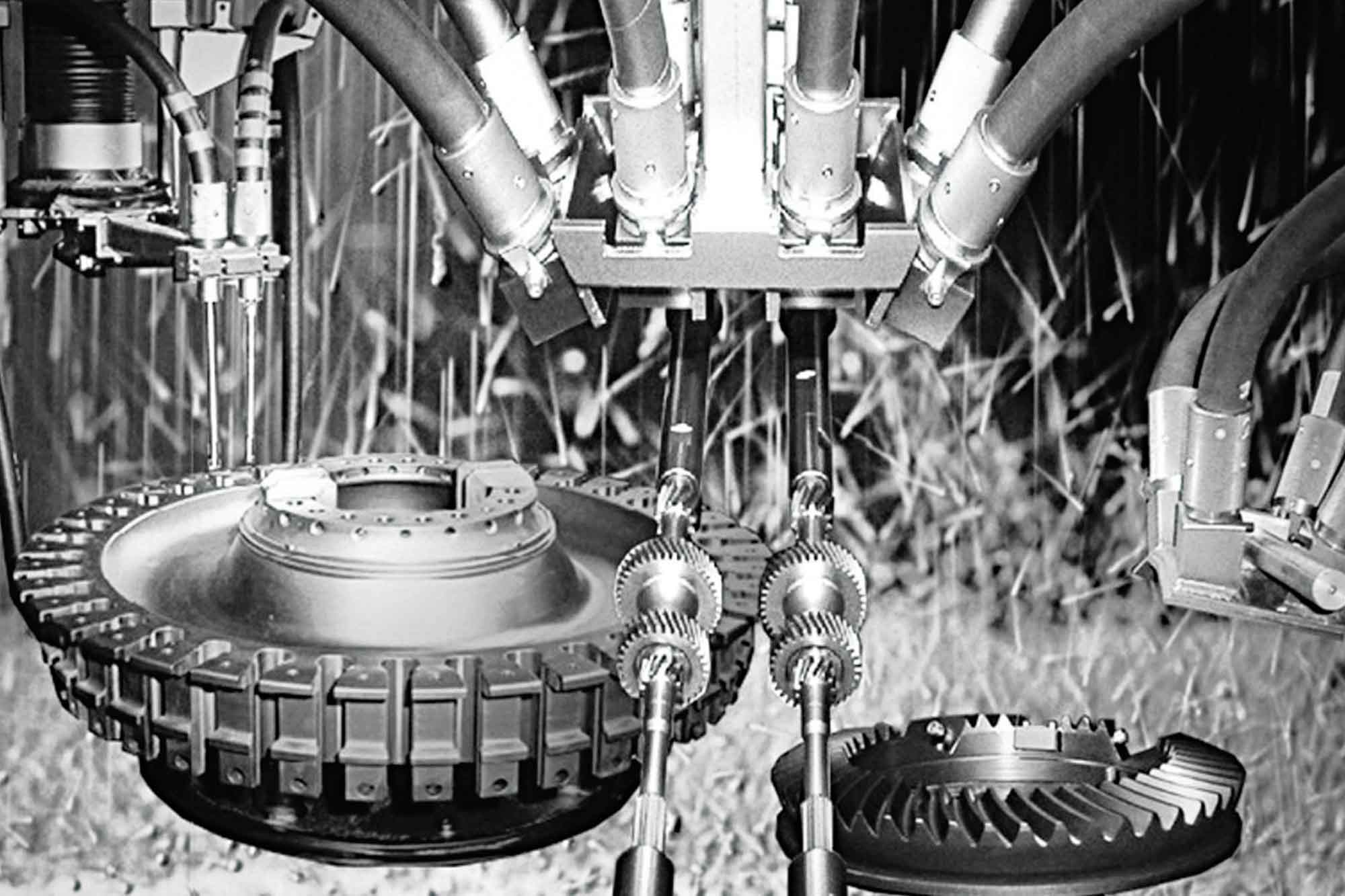
The automotive market is becoming more and more demanding with increased expectations from the components being used in terms of better life, increased efficiency and higher workloads. Since safety and speed are important aspects in this industry, manufacturers are constantly upgrading their processes and adapting international norms. Components which are subjected to cyclic loading such as crankshafts, springs, transmission gears, connecting rods, etc are increasingly subjected to shot peening operation. To achieve the perfect solutions for automotive industry, Wheelabrator peening machines incorporate programmable control and automated component handling systems. These operate in line with pre-set programs to ensure the precise repeatability of the peening effect, which is essential for volume production. Shot peening, which is a means of controlled blasting, induces compressible stresses in the component thus increasing its fatigue life.
Wheelabrator offers multi-table wheel shot peening machine — DRT. The machine is installed with one or two ROTO-JET blast wheels for standard applications and Saturn HD blast wheels for heavy duty applications. The main chamber is made from Mn (manganese) steel with replaceable liners in the direct blast zone. The wheel drives are fitted with Variable Frequency Drive (VFD) to ensure that the wheel rotates at set RPM controlling the shot impinging velocity of the components. The number of independent rotary table has to be between six and twelve. The drive used for the table indexing is mounted on top of the machine and the indexing time can be as low as 3 seconds for 30 degree rotation. Normally for shot peening, conditioned cut wire shots are preferred. The size of the shots is selected based on the component size, shape and profile that need to be peened. The machine shot recirculation system is fitted with multi-deck Gyro screen for the classification of the shots and allowing only the chosen size shots for the shot peening needs. The screen normally used is off line and continuously in operation. The machine is also equipped with safety and operation interlocks. This machine is offered from DISA India Ltd’s state-of-the-art manufacturing facility based at Hosakote, Bengaluru. The application, engineering and services play an important role in the peening solution implementation. Hence, the Wheelabrator team has been trained including MFA training to ensuring perfect installation. The machine is always assembled and tested in the Hosakote plant before dispatch.
Shot Peening
Shot peening is used widely to enhance the fatigue resistance of highly stressed metallic components. This in turn will improve the performance of safety-critical components. Any metallic component that is subjected to cyclic stresses within its elastic limit can benefit from the shot peening process. Peening is achieved by propelling a stream of media (precisely manufactured round steel shot, glass or ceramic beads) at components, at high velocity under fully controlled conditions utilising a compressed air stream or, centrifugally, by means of a vaned wheel. Components that would benefit from this technology include aero engine fan blades, aircraft structural parts and automotive transmission systems. Peening is different from cleaning on various functions such as media velocity, media size, shape to name a few.
Measuring effectiveness with almen strip
Effectiveness of the peening process is important to ensure that the correct intensity of stress is being created. This is achieved with the aid of Almen strips. This strip is manufactured from spring steel for strict tolerance of hardness, size and flatness, and is peened on one side only. The effect of the induced compressive stress on the strip results in bowing or curving. The extent of the curve is proportional to the energy imparted by the shot and is measured on an Almen Gauge. This gives the amount of energy imparted by the stream of shot and absorbed by the strip thus measuring effectiveness of the process. X-Ray diffraction techniques also provide an accurate method of measuring the actual stresses within the component and quantifying the actual effect of the peening process. Results are achieved by measuring the angle of reflection in relation to the angle of incidence that varies dependent on material composition and residual stresses.
Advantages v
In addition to enhancing performance, there are other important benefits from the process:
Compressive stress helps prevent crack formation
The compressive stress helps to prevent crack initiation; as cracks cannot propagate in the compressive environment generated by peening.
Reduced friction
Components which are moving in relation to each other, such as bolting, riveted assemblies, sliding or rolling parts, can wear and fail as a result of microscopic transfer of material from one surface to the other. The surface finish produced by the peening process provides pockets for lubricant retention; it also reduces the surface area in contact under rolling or sliding conditions, thus reducing friction.
Increased wear resistance
Peening also has a surface hardening effect and helps the ‘skin’ of the material to resist wear. These characteristics, when combined provide excellent anti-galling properties making the components more resistant, work better and with increased efficiency.
Less corrosion
lntergranular and stress corrosion cracking can be inhibited by shot peening which modifies the properties of the metal at a metallurgical level. The process advantageously alters the granular structure at and near the surface, producing a condition less prone to corrosion.
Defining equipment choice
An important and complex aspect is the selection of correct equipment and process parameters. Component variables such as size, shape, material, hardness, application and operating environment all have to be considered. The topography of the component is also an important factor. For instance, if a radius is smaller than that of the shot, then it will result in a non-peened area. Sharp edges, blind holes or hidden areas also need special attention to ensure good coverage and to avoid damage. Independent of the type of media propulsion, shot peening requires monitoring and closed loop feedback for critical process parameters such as media velocity and flow. The ‘science’ of peening rests in all such parameters and close adherence will result in a final product that performs to or above expectations.
Wheelabrator, a world leading surface preparation technology manufacturer presents state-of-the-art surface preparation and peening technologies to prepare, peen and finish an extensive range of components across all industry sectors. Its aim is to lower cost per part, and in India, it is transferring the European technologies to its Indian manufacturing centres. It is adapting the technology to address the needs of the local market, and making the solutions more affordable.
Cookie Consent
We use cookies to personalize your experience. By continuing to visit this website you agree to our Terms & Conditions, Privacy Policy and Cookie Policy.