3 Technologies and Trends for MHE
By Edit Team | April 14, 2016 4:19 am SHARE
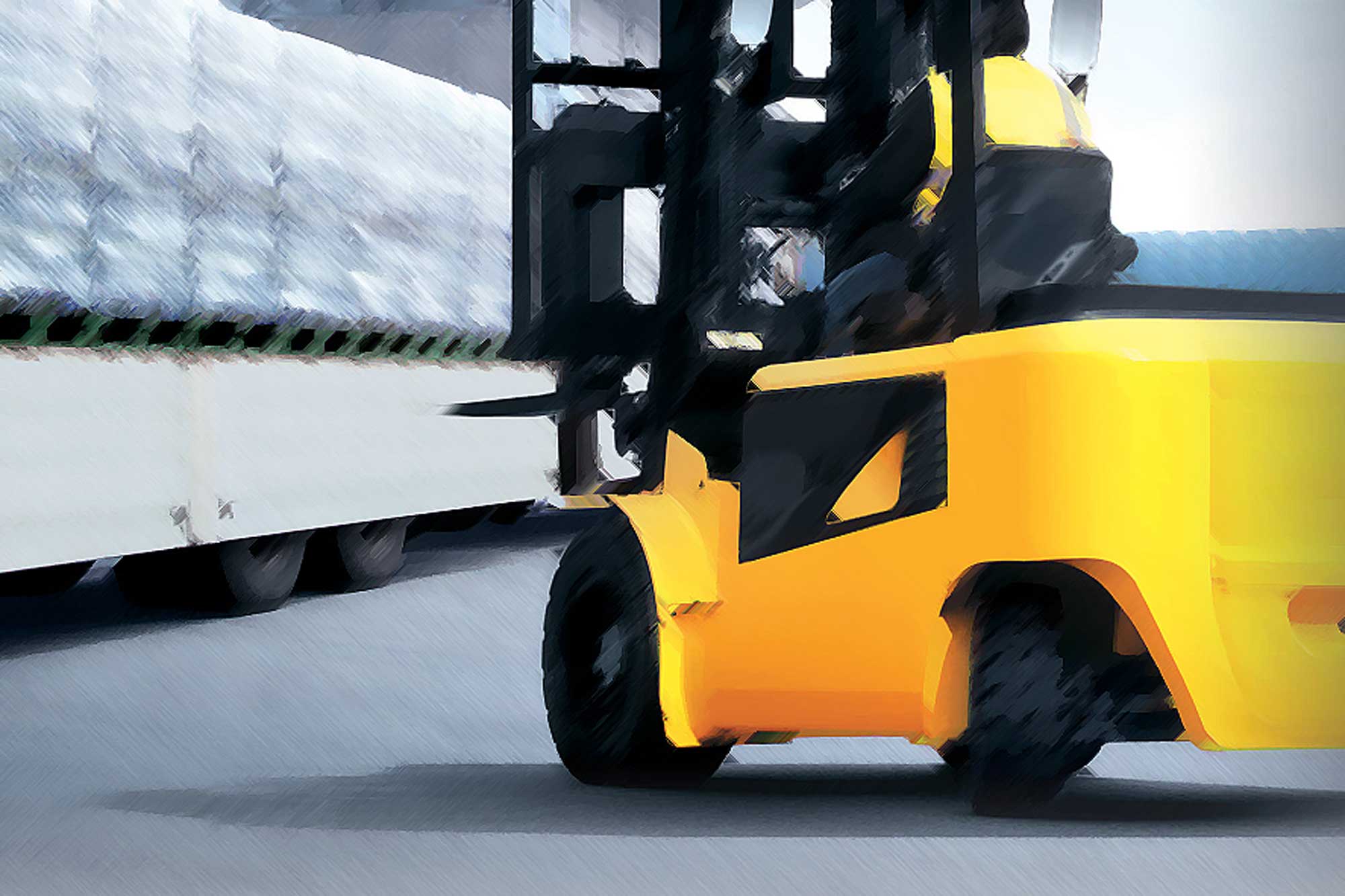
A small overview on the technology and trends for material handling equipment in the coming years
Customers today are definitely more aware of what the global marketplace has to offer and demand the same in India. This has ensured that the major Indian manufacturers have stepped up their game through product upgrades or international tie ups. Acceptance of lighter and more compact cranes is a shift that has happened within the last few years, factors that can give several advantages to clients.
“The industry has started becoming more customers oriented as compared to the past. By default, customers today expect a high-quality and well-timed customer service. As practice manufacturers have to place enabling structures in place ensuring zero customer complaints and prompt responses to service calls,” says Tushar Mehendale, Managing Director, ElectroMech Material Handling Systems.
The crane industry has not seen too many revolutionary changes in technology over the past few years; however evolutionary changes have certainly happened.
1. Radio remote technology
“One of the technology trends that ElectroMech is establishing is the standardisation of radio remote controls across all of our cranes. Radio remote controls offer a substantial increase in flexibility for the crane operator as well as allow safer operations as the operator needn’t remain under the crane. In addition, the need for the festooning system along the crane girder is negated, allowing the cranes to remain lighter as well as neater,” says Mehendale.
2. Anti-sway systems
ElectroMech provides anti-sway systems in its cranes that ensure the cranes can work at high travel speeds without worrying about load swinging dangerously. This in turn helps the customers in significantly ramping up their productivity. “An anti-sway system works on the principle of a pendulum, a load being handled by a crane acts like a pendulum, as the crane begins to move, the load begins to sway. The extent of this swaying depends on the length of the pendulum, or in the case of a crane, the length of the wire rope. Without corrective action, only friction will limit the extent of this and deaden this swaying. With no specific device to do this, controlling this swaying depends solely on the skill of the driver of the machine who manually applies a counter reaction to the movements of the load,” explains Mehendale.
The anti sway system offers several advantages, namely protection of the load and the machinery and less maintenance, lower risk of accidents, lower operator fatigue, lower cycle times and indirectly and lower energy costs.
3. Crane Control System (CCS)
“With its Crane Control System (CCS), Manitowoc is the first manufacturer to introduce a common operating platform across multiple product lines, and this will bring unparalleled ease of operation and service to the company’s cranes,” boasts Jens Ennen, Senior Vice President, The Manitowoc Company.
Ennen says that one of the fundamental drivers in creating the Crane Control System was to introduce a common user interface not only across the models within a product line, but across the entire family of Manitowoc cranes products. And so it is that anyone taking a look inside the new GRT8100 rough-terrain crane or the GMK5250L all-terrain crane will see the same features – a jog dial and central displays with common symbols.
“The commonality of design makes it easier for operators to switch easily between products, delivering obvious benefits in terms of productivity and efficiency. But it’s not only the system’s commonality that will deliver better value to customers,” says Ennen.
There are only seven major parts in CCS with common parts numbers across all brands. So servicing is easier and customers don’t need to keep large parts inventory. CCS has given performance improvements, such as increased load curves and faster commissioning for Potain cranes or the boom configurator mode for grove mobile cranes. And not only that, but moving to CCS is also going to deliver better reliability for the cranes.
The development of CCS includes an intense program of testing at Manitowoc’s PVC facilities, or Product Verification Centres. At these locations, each component that makes up the CCS is tested in a variety of conditions and through prolonged periods of operation to replicate real-life operation. After this comes a lengthy PPP, or Pre-Production Partnership, process where the first units are put to work in the field and their performance is closely monitored. Only once this is complete, the first CCS cranes are put into serial production.
“So far, the feedback from customers has been very positive and not only because of the simplicity the system brings to operation, its performance enhancements are also welcome. On the latest CCS range of Potain MDT topless cranes, the capacity increases are impressive. On some models, its inclusion boosts capacity by 30 per cent over previous units. Getting the crane to work is faster too because the commissioning technician can manage the entire calibration process from the cab and it takes just 15 minutes, versus the two to three hours that was previously required. As the calibration can be done from the cab, the technician does not need to check a series of points on the crane, as was previously required, so the process is considerably faster and manpower resources are saved,” says Ennen.
With grove mobile cranes, CCS also facilitates getting to work as the boom configurator mode allows the operator to select the correct boom configuration simply by entering the load, radius and; or height of the lift. Life for the operator and the service technician is made easier through CCS’ simplicity, modularity and ergonomic design.
————————-
Radio remote controls offer a substantial increase in flexibility for the crane operator as well as allow safer operations as the operator needn’t remain under the crane.
Tushar Mehendale,
Managing Director,
ElectroMech
Cookie Consent
We use cookies to personalize your experience. By continuing to visit this website you agree to our Terms & Conditions, Privacy Policy and Cookie Policy.