Essence of admixtures in concrete
By Edit Team | June 24, 2013 4:56 am SHARE
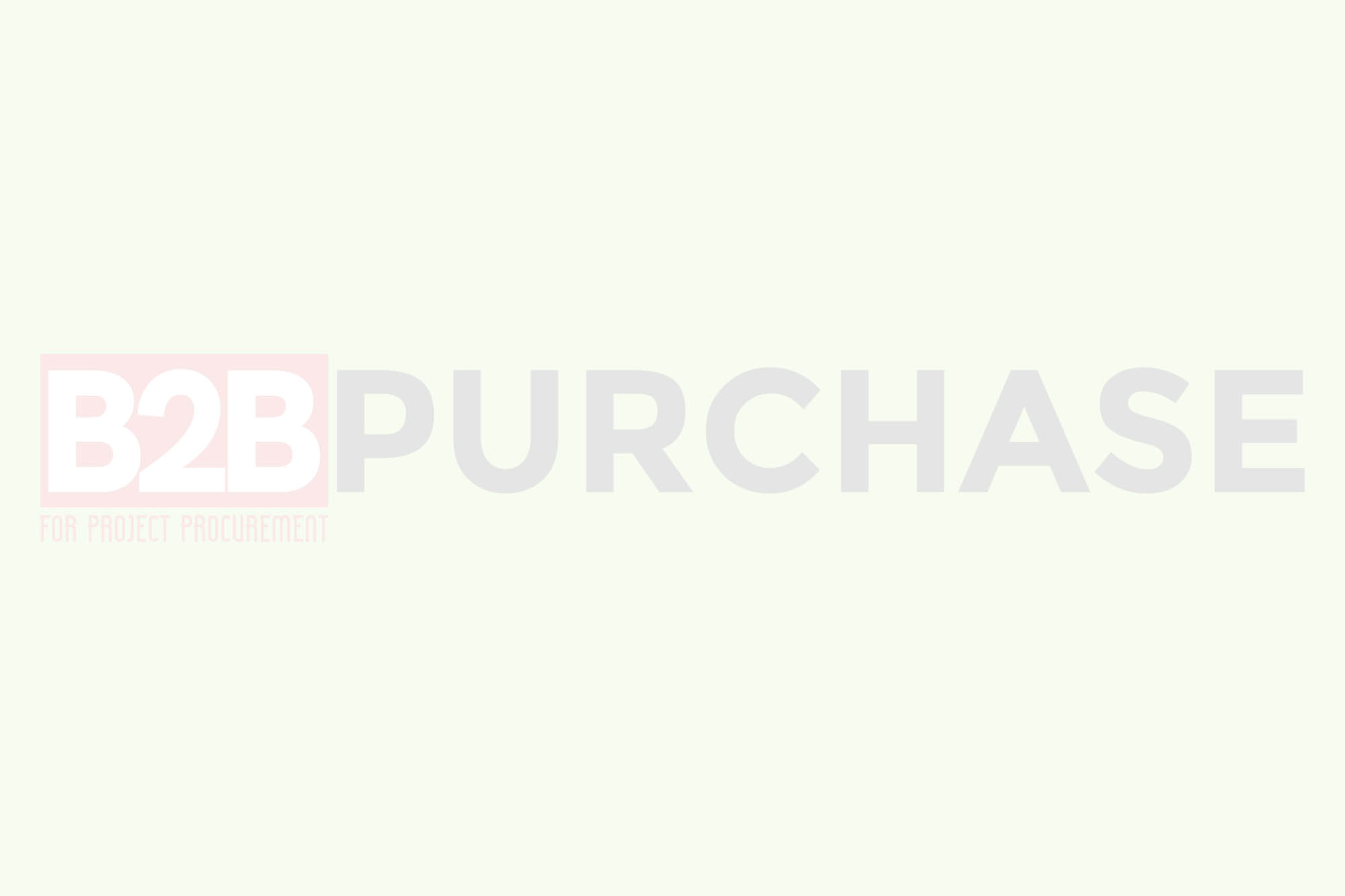
Chemical admixture. What are its important roles? How to classify and test chemical admixtures for concrete? Writes Deepak Kanitkar, GM – Technology and Business Development,Chembond Chemicals Ltd.
One of the most important, critical ingredients of modern concrete is the chemical admixture. The introduction of admixtures has changed the way we can work with the cement concrete. As the power’s equation states Vp=100w/c-36.15a. The porosity of concrete is inversely proportional to W/B ratio. The first and most important role of chemical admixtures is to reduce the water: binder ratio.
IS 9103, ASTM C-494, ASTM C 1017, BS 5075 (withdrawn) and BS EN 934 part 1, 2, 6 with supporting test methods are commonly used for classifying and testing chemical admixtures for concrete. There are different classes of admixtures, based on their effect on concrete properties. ASTM standard C-494 classifies admixtures in eight types from A to G and S. Apart from reducing the mixing water, chemical admixtures have various functions such as slump retention, set retardation or acceleration, strength acceleration and more. Each type needs to meet different criteria, specified in test specifications. Moreover, there are other types like air-entraining admixtures as per ASTM C-260, integral water proofing admixtures meeting the water impermeability requirements as per DIN 1048, anti-wash out admixtures, corrosion inhibitors, shrinkage reducing admixtures, foaming agents, corrosion inhibiting admixtures, and shotcrete accelerators.Chemical admixtures are based on various chemistries. Water reduction greatly depends on the type of chemistry a formulator uses to design the admixture. As we know, the best water reduction is achieved using PCE-based admixtures. This is a result of very efficient dispersion of the binder which PCEs offer. The effectiveness of PCEs is more evident when the W/B ratio goes below 0.35. The versatile chemistry of PCE polymers ensures their use in almost every mix design. SCC has been mostly associated with PCE-based admixtures. Along with the excellent water reduction, they also produce flowing concrete without segregation. If the mix is properly designed there is either no need for VMAs or their use could be limited. Nowadays modified PCE-based admixtures are available which also offer good rheology control. One of the challenges in earlier PCEs was the increased stickiness of the concrete mix, now there are some molecules which offer excellent reduction in stickiness. This is often necessary while designing very high strength mixes which have a tight water cement ratio and high fines. There are other issues associated with PCEs such as, rapid loss of slump, dosage and temperature sensitivity, and sensitivity to moisture content. Due to such factors, use of PCE based admixtures in lower strength mix designs is many times avoided by concrete producers. Modified PCEs are useful in meeting the requirements of lower strength mixes. Often, due to use of manufactured sand or stone dust, there are issues with regard to slump retention or segregation. These need to be addressed by smart formulations of blended PCE molecules.
As described earlier apart from the traditional use as water reducing agents and slump retainers, admixtures are nowadays used for more functional roles. Shrinkage reducing admixtures is an example. These are very effective in reducing cracks caused due to drying and autogenous shrinkage, also known as self-desiccation. They act on very fine capillaries with diameters between 2.5 to 50 nm in diameter, by reducing surface tension within pore solution. This helps in preventing collapse of capillary walls, thereby reducing cracking. Their use in heavy duty industrial floors, enables increased the spans and reduction in the requirement for number of joints. SRAs are mainly based on ethylene and propylene glycol derivatives. While using SRAs, one must consider their effect on final compressive strength and air entrainment. In general, at same W/B ratio, 10-15 per cent reduction in final compressive strengths has been observed. It is imperative that by adjusting the W/B ratio, one can actually maintain the desired compressive strengths.
The shrinkage could to some extent be determined from an equation derived by Tomita et al• (sh) = 390 + 2.89W – 21.77X-4.758E (x10-6)• Where W, X and E corresponds to unit contents (kg/m3) of water, SRA and expansive additives respectively.• This suggests that SRA are more than four times more effective than the expansive additives or the effective dosage of SRAs is only 20-25 per cent that of the expansive additives.
Preventing or rather delaying corrosion of steel in concrete is achieved by at least three methods: use of corrosion inhibiting concrete admixtures, CP systems and protective covering or penetrative treatments. The most important factors are chloride ingress and carbonation, apart from sulphate and other corrosive contaminants. CIAs are mainly based on inorganic chemicals such calcium nitrate/nitrite or bipolar acting agents based on amino alcohols and amino polycarboxylates. Various products are available in the market and are in most of the cases equally effective. The mechanisms are different, so as the dosages.
Uses of internal curing agents for concrete are also gathering momentum. They act by providing additional moisture in concrete for a more effective hydration of the cement and reduced self-desiccation. Internal curing means the introduction of a curing agent into concrete to provide this additional moisture. Two major methods currently available are: • Use of saturated porous lightweight aggregate (LWA) to supply an internal source of water. • Super-absorbent polymer (SAP) particles can absorb a very large quantity of water during concrete mixing and form large inclusions containing free water, thus preventing self-desiccation during cement hydration. For optimum performance, the internal curing agent should possess high water absorption capacity and high water desorption rates.
Most tunnelling work will never be complete without the use of gunniting or the sprayed concrete. Spraying concrete is a very sensitive application. The nozzlemens’ job will not be easy without the use of an accelerating admixture. Typically, quick setting is as critical as controlling the reheology of sprayed concrete. Accelerators combine both these requirement, thus reducing the rebound to a great extent and achieving the quick setting.
There are more and more applications which could be discussed. Admixtures for making pervious concrete, colorants for decorative concrete and admixtures used for stopping the rejected concrete from setting for a period as long as 24 hours are available.
Authored by—Deepak Kanitkar, GM – Technology and Business Development,Chembond Chemicals Ltd.
Cookie Consent
We use cookies to personalize your experience. By continuing to visit this website you agree to our Terms & Conditions, Privacy Policy and Cookie Policy.