First TIG narrow Gap welding handbook
By Edit Team | March 19, 2014 10:43 am SHARE
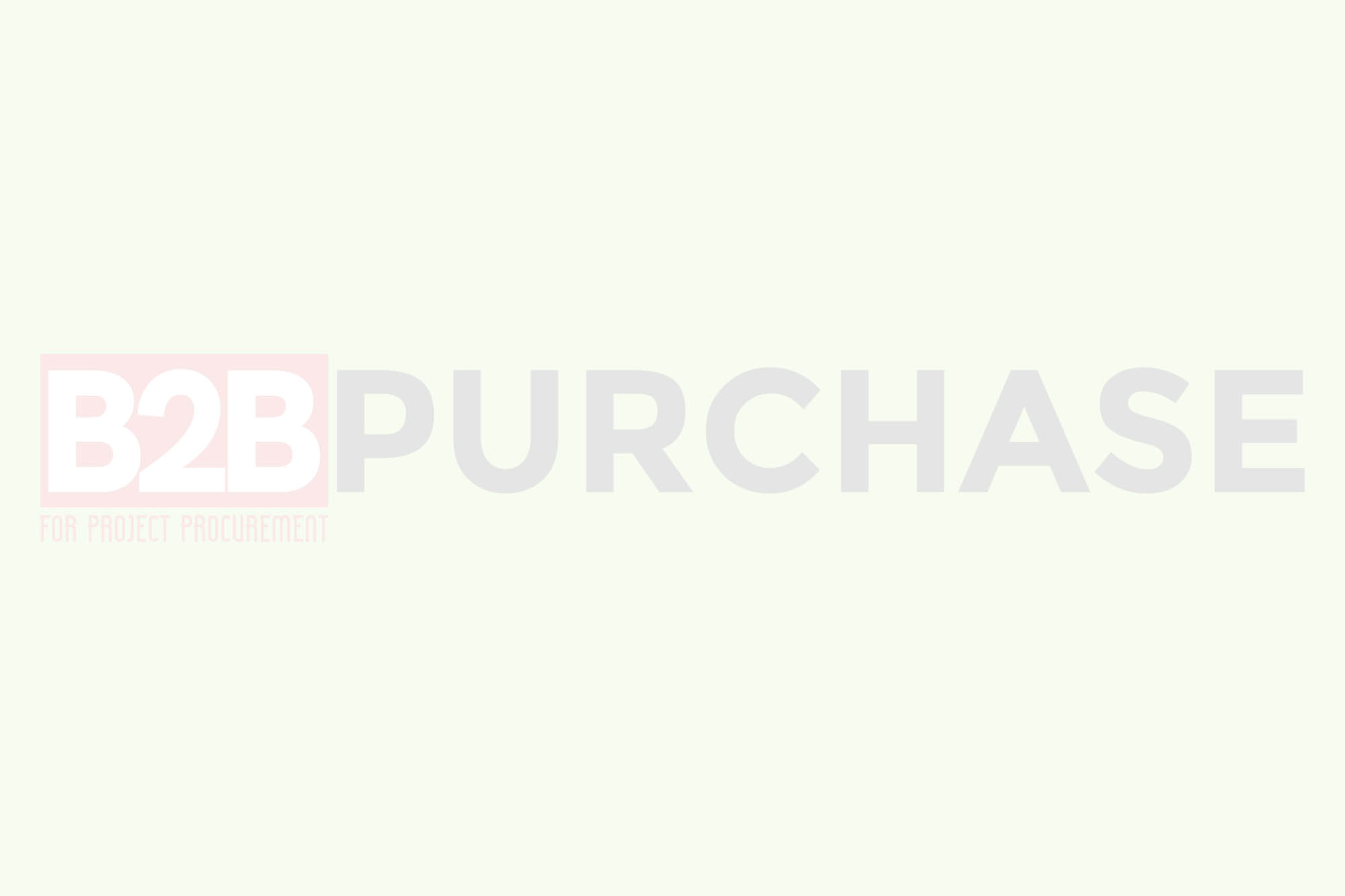
Polysoude has released the first ever reference document for TIG narrow gap welding
The quality and productivity requirements relating to welded joints are inexorably driving industrial companies towards the implementation of automatic processes. These primary objectives are however supplemented by more subtle notions such as heat input, weld seam regularity or even aesthetic criteria for sectors affecting the general public. Several decades of progress in TIG welding have seen it become an essential process that offers not only the widest scope of use but also reasonable operating constraints compared with more recent developments (laser or electron beam welding).
The effectiveness achieved in producing quality weldments using the TIG process, both in terms of productivity and control in all positions, is at the origin of a large number of automatic applications including orbital welding. This technique has now been popularised with the creation of numerous machines which have boosted recognition of the TIG process as a real alternative for the automated welding of a wide variety of materials. Efforts made in tool design (miniaturisation, robustness, increased duty cycles, etc.) have made it easier to optimise the designs and service performance of the equipment to be built. The whole range of benefits linked to TIG welding have not only encouraged the automation of sequences that were previously only done manually, but have also been the starting point towards applications involving increasingly large workpieces. Consequently many variants or developments towards high-power welding power sources, or the introduction of additional functions such as the use of hot wire or double wire feed, or the creation of specific tools such as cladding and narrow gap torches have decidedly widened the scope for TIG. Nowadays it is no longer unrealistic to consider using TIG to weld workpieces from 0.5 to 300 mm thick given the numerous relevant advantages.
The TIG welding approach on thick workpieces does however require some specific knowledge with regard, on the one hand, to the choice and use of equipment and, on the other, to workpiece preparation and the development of operating techniques. Productivity is a question that is invariably posed on developing a Narrow Gap operating procedure. However, in order to choose an operating technique, the strengths and weaknesses of that technique must be known beforehand to avoid ending up in an impasse.
Productivity gains are considerable and increase in proportion to the thickness to be welded. It is vital nonetheless to assess the thresholds below which the restrictions involved in Narrow Gap welding outweigh the substantial gains.
Several decisive factors come into play when analysing this question and the final choice must take account of the notion of relativity which may exist between the various situations. It can therefore be seen from comparative tests that, for thicknesses ranging from 12 to 15 mm, the increase in productivity between a conventional groove (angle of approximately 20 deg) and a Narrow Gap groove optimised in relation to the materials is not significant. Profitability will then increase, reaching a factor of 3 on sections around 55 to 60 mm thick.
At thicknesses of 30 mm and above, apart from the specific case of welding one-off parts, a Narrow Gap procedure must be used. The difficulties relating to materials or other operating restrictions are to be considered in order to choose the Narrow Gap technique that is appropriate and compatible with the application in question.
Today, POLYSOUDE has a comprehensive line of Narrow Gap welding torches for all thicknesses from 30 to 300 mm. The ranges and thicknesses to be welded are to be considered on the basis of the line of torches created and constructed according to various technological constraints. Each torch has a scope which enables it to be used from maximum thickness (maximum torch insertion depth into the groove) up to completion of surface capping runs.
With conventional torches from 0 to 45 mm, electrode stick-out has to be adjusted every 5 to 10 mm, when filling up the weld groove. So-called conventional torches remain fully versatile torches that are suited to all types of work. A category of intermediate tools called “V2 and V3 nozzles” exists for 0 to 100 mm thick sections. These nozzles have the particular feature of being insulated and channelling the gas to the root better than a conventional torch but without guiding the tungsten via a true electrode lance. From an insertion thickness of approximately 45 mm, these nozzles are combined with removable trailing shield assemblies to complete the weld, oscillated capping run included.
For thicknesses of 0 to 150 mm, 0 to 250 mm and finally 0 to 300 mm, a line of torches is also available with trailing shield assemblies (removable if necessary) for all runs from root to cap. All Narrow Gap solutions (i.e. 0 to 100 mm V2 and V3 nozzles, and 0 to 150 mm, 0 to 250 mm and 0 to 300mm NG torches) exist as fixed electrode or oscillating electrode versions.
The deliberate reduction in the volume of metal to be deposited, which is the main objective of Narrow Gap applications, highlights several operational difficulties including that relating to the lack of visibility for operators to track the welding.
These difficulties are explained by the effect of several combined factors that differ slightly according to the applications, but which include:• Groove width commonly between 10 and 20 mm for depths of 100 to 300 mm.• Welding on flat sheets or large diameter workpieces rendering tangential viewing angles almost impossible.• Preheating which is very often used when welding heavy wall thicknesses.
In addition to these technical aspects, it is also natural to seek comfort for the operator stations and to move them away from the arc given that the radiation remains quite strong due to the use of high currents.
To remain compatible with the industrial environment and refrain from overburdening the tools, it is possible to integrate the video function by design, as opposed to the use of add-on external cameras which disfigure the industrial nature of the equipment. The torch is not only the most complex tool, but is also the one that has the greatest exposure and the greatest influence on weldment quality. Consequently, testing methodologies have been developed to verify and validate the predominant functions where failure could impinge on welding results.
Two essential factors are to be considered:• The duty cycle (all functions mounted on the torch being globally combined and validated by the lack of deterioration of its initial function over time).• Bead shielding quality.
Validation is performed for each new torch reference with regard to functions such as video and gas shielding. More comprehensive tests are performed per torch family or as a result of a notable technological development.
Once validated, the concepts are reused per family to reduce the development time of variants and to capitalise on lessons learned on each model. It can be considered today that there are no longer any technological issues in using a Narrow Gap torch to weld sections with a thickness of 30 to 300 mm.
As there is no technological barrier, only technical criteria can be considered. Based on this fact, what are the alternatives, the common features, and the strengths and weaknesses associated with each methodology? The first choice to be made in TIG welding concerns the process variant: cold wire TIG or hot wire TIG welding.
Hot wire TIG welding machines generally have higher duty cycles with the capacity to use currents approaching 450 A. There are only advantages to be gained in opting for hot wire welding over the cold wire process and the former is increasingly used to weld sections over 10mm thick. These machines also offer the benefit of versatility and can make use of the two TIG welding variants quite easily. The only benefit of the cold wire TIG process may lie in the portability of the equipment for occasional use with a lower purchase price, as a direct consequence of the difference in power, for a complete installation. The various welding procedures are differentiated by the filling run layering strategy (cf. Comparison of the various NG filling techniques).
Four essential approaches and their advantages shall be examined:• Single stringer bead per layer for welding performance and productivity in all positions where shrinkage and preparation are fully controlled (Fig. 7: Single stringer bead)• Multiple-pass stringer beads per layer for optimum control over welding energy and difficult bimetallic joints (Fig. 8: Multiple-pass stringer bead)• Single oscillation pass per layer for welding in positions 5GT and 6GT with limited variations in width – a good compromise between productivity and ease of implementation (Fig. 9: Single oscillation pass)• Multiple oscillation passes per layer (rarely chosen) to use Narrow Gap TIG welding while adapting to existing preparations.
Workpiece profiles, thickness ranges and the environment are all essential data when it comes to defining welding equipment. Welding machines are generally matched to the welding tool to be used. A few typical examples of equipment configuration according to the thickness of the sections to be welded are provided below. For sections less than 45mm thick, usual mechanised or orbital welding equipment is suitable as long as it is compatible with the required duty cycles. More versatile and modular PC power sources are suited to mechanised applications, or even more complex applications such as welding robot-type holder-based solutions or orbital welding machines.
“Carriage”-type heads offer the advantage of being able to be used on circular or straight rails. The POLYCAR MP (friction drive) can be implemented on combined sections (curved or elliptical, etc.). Due to the simplicity of the POLYCAR MP profile, industrial companies can create their own tool. Straight rails are identical to the “seam welder” notion except for the fact that they can be used in all positions and are an easily implemented solution for linear welds. For thicknesses up to 100mm, the torch holders are the same as for conventional torches. Beware however of circular welds in a horizontal plane which, other than the particularity of being so-called self-restraining welds (high stress concentration), also call for Narrow Gap torches with a curved profile (to be avoided).
Beyond 100mm, the tools gradually increase in size forming, in certain cases, modules that weigh several hundred kilograms (turbine rotor applications, for example). For so-called mechanised applications, the solutions are identical but constructed on the basis of more robust components adapted to the context, the geometry and the weight of the subassemblies, in keeping with the thickness of the workpieces.
For orbital welding, however, the weight of the torches, the engagement strokes and the need to consider use of 15kg spools (justified by the volumes of metal to be deposited) call for larger tools than the POLYCAR 60-3 and MP orbital heads.
In this case, choose heads capable of moving heavy loads (80kg) with an offset providing sufficient flexibility to adapt to heavy-duty sheet metal workpieces. Use of a welding robot is also recommended for anything other than circular trajectories or where the industrial company wishes to acquire a more versatile tool. There are no particular considerations for solutions involving torches intended for applications up to 45mm. A retractable nozzle torch offers a multipurpose solution provided that electrode changing can be accepted as a non-automatable operation. For heavy wall thicknesses, torch weights and dimensions must be integrated and robots compatible with wrist loads of 10 to 50 kgs selected. The notion of trajectory remains linked to the profile of the torches which limits movements and implies studying torch positioning along the usual three axes. The use of a Narrow Gap torch renders the notion of automated preventive maintenance, such as electrode changing, somewhat illusory.
The other approaches are specific to robot use and are to be addressed according to workpiece dimensions and the level of automation (gantry, multi-robot station, seam tracking, etc.).
Narrow Gap TIG welding is no longer a solution for exceptional circumstances. It is important to consider it whenever the thickness to be welded exceeds 30mm. An initial analysis is imperative to ascertain the potential benefit, verify the absence of notable contraindications and above all to choose the methodology and equipment best suited to the context. There are a multitude of solutions with a significant level of industrial maturity confirmed by numerous concrete examples. The difficulties involved in implementing the welding procedures vary according to the chosen technique. The temptation to take a simplistic approach and skip a case-by-case assessment must however be avoided as there is no universal solution. Moreover, in terms of tools, the entire 30 to 300mm thickness range is covered with numerous variants and adaptation possibilities for special cases.
For the welding process, knowledge and mastery of TIG are highly important and enable the technique to be popularised, with recourse in the event of difficulties. From the point of view of industrial companies, the implementation of a Narrow Gap application calls for a structured approach with marked steps. In parallel, corresponding approaches for machining facilities, tracking and traceability of materials and inspection techniques may need to be undertaken requiring validation steps close to those used in welding. All of these anticipatory measures are justified by the prospect of substantial gains compared with the use of more conventional techniques.
Cookie Consent
We use cookies to personalize your experience. By continuing to visit this website you agree to our Terms & Conditions, Privacy Policy and Cookie Policy.