A path to reliable and high-performance screening media
By Staff Report | August 13, 2024 2:36 pm SHARE
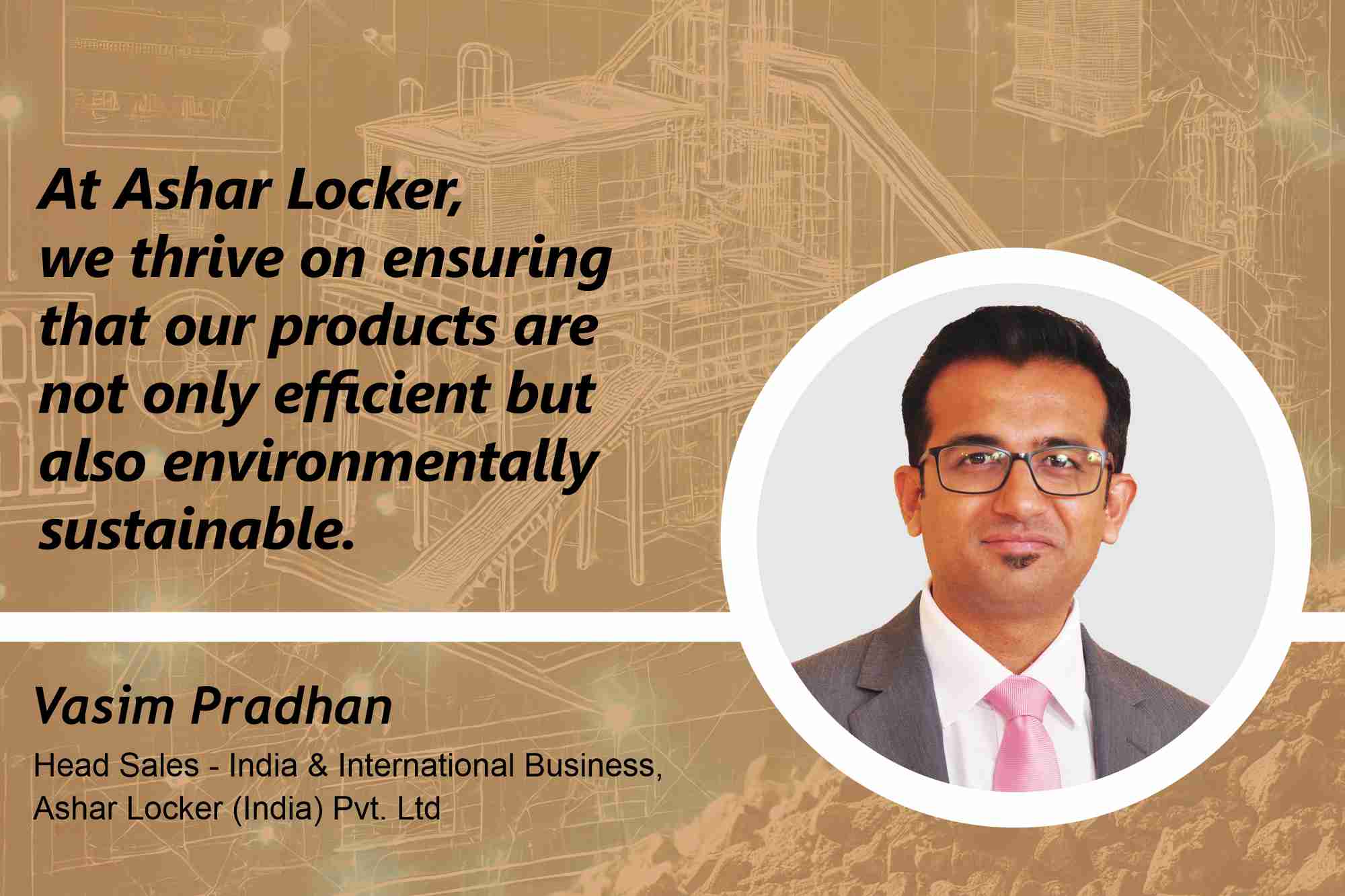
Through rigorous testing, precise material sourcing, and a commitment to continuous improvement, Ashar Locker delivers screening media solutions that consistently perform under varied operational conditions. The company’s dedication to innovation and customer education sets it apart as a leader in the industry.
How does Ashar Locker maintain consistent global quality standards across its diverse screening media solutions?
We comply with the latest ISO quality standards to consistently maintain high product quality and customer satisfaction. We procure our wires from either Tata Steel Ltd or other equivalent wire manufacturers from around the world. Our R&D team has derived the proper chemical composition for our wires to ensure maximum efficiency. Our wires are made to our grades by our vendors. Most local suppliers don’t even buy wires. Instead, they draw their wires by melting scraps or sourcing them from suppliers. These wires are of very low quality; hence, they always offer higher wire diameters to customers under the pretext of higher life. Still, they reduce the plant’s efficiency and increase their final products. We make our customers understand the importance of screening areas, which will help them improve their plant efficiency, thus reducing costs. Therefore, when customer chooses Ashar Locker as their screening partner, they are certain they have chosen the best and most reliable supplier for their screening needs.
We use rigorous testing methods to ensure that our meshes are the best in the world regarding quality. We embrace Lean principles such as First-In-First-Out (FIFO), PCDA, Just-in-Time (JIT), Standard Work, Standard Work, Poka-Yoke, and 5S, and we practice many more lean methods and tools. These methodologies optimise efficiency, reduce waste, and promote continuous improvement throughout our manufacturing processes. We have always believed in innovation & technology; our products have been in huge demand across all the minerals in the industry. Our dedicated R&D team has always focused on developing products that create value for our customers.
What technological features or innovations differentiate ULTRA-FLEX Anti-Clogging Screens from traditional solutions?
We have always believed in innovation and technology, which has made our products in huge demand across all the minerals in the industry. Our dedicated R&D team has always focused on developing products that create value for our customers. Some of our flagship products, like the Anti-clogging screens, have enabled our customers to operate their plants during heavy monsoons.
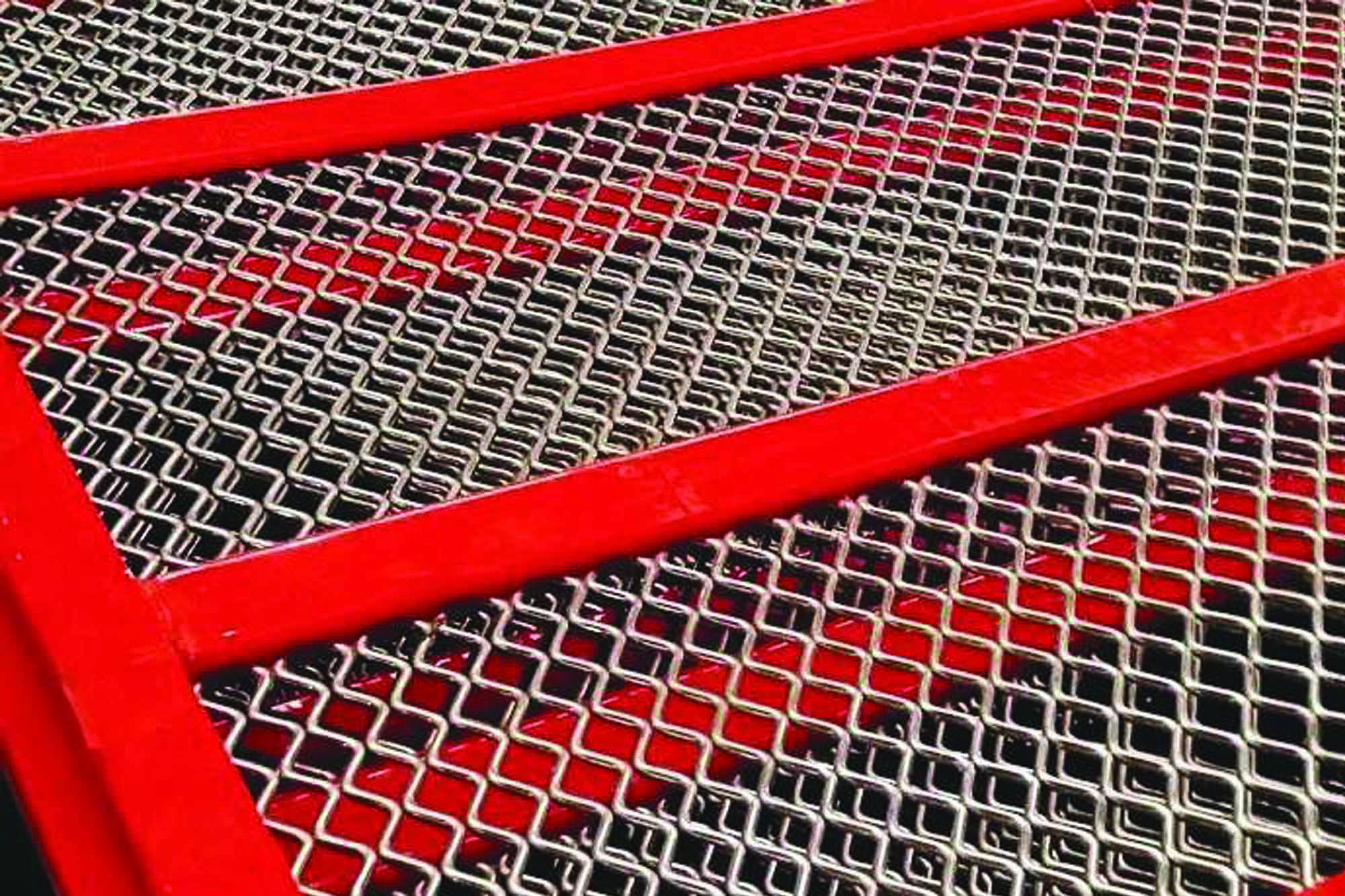
These screens combine polyurethane with steel to make them high-flexible screens that allow each wire to vibrate individually from end to end, allowing the material to pass through smoothly even in the wettest conditions. Ashar Locker was the first to introduce this product in India, which enabled our customers to achieve high throughput screening through the monsoon. Screening in those three months of the year had been a massive pain point for the industry. Poly-Ripple is a great alternative in any application where a customer encounters blinding in traditional wire mesh. Our technology used in the production process is developed in-house and is proprietary to our group.
Can you elaborate on the specific applications where ULTRA-FLEX Polyurethane Screening excels?
Ashar Locker’s ULTRA-FLEX Anti-clogging screens have proved highly successful in the manufacture of M-sand and P-sand over the past couple of years. These handmade and uniquely designed screens efficiently utilise every motion of the screen. Each wire vibrates individually, which improves the efficiency of the plant and helps develop precise cuts needed for sand manufacturing.
The Rubber & PU meshes, when compared to the wire mesh, have a better wear life, less dust generation, less sound pollution, and are more durable. The only drawback is the reduction in open areas for screening. Non-metallic and metallic have their place and importance, and customers are guided to install the right combination of meshes to bring value to their plants. The top deck can be non-metallic, the second one metallic, and the third can be an anti-clogging screen; this can be decided with the help of the company’s expert technical team.
How flexible are you in adapting screening media solutions to unique project demands?
As a complete solution provider, we must conduct onsite audits to ensure that our customers use the right screening media at different stages to ensure maximum plant efficiency. Our meshes are customised according to the client’s requirements. Once we receive an inquiry from our customer, we visit their plant or ask for the complete flowsheet of the plant to understand the exact requirements. Based on the data, we analyse the correct type of screening media and its exact specifications to maximise the output and increase the plant’s overall efficiency. Screens are generally the most neglected part of the crushing & screening circuit and customers more often stick to the same specification of meshes supplied by their respective OEMs. It is important to understand that every crushing & screening plant is different as the end product size varies from customer to customer. Also, the nature of the mineral/rock being screened varies from quarry to quarry. Once our team analyses the complete data, we offer end-to-end screening solutions to our customers based on their requirements. Our Anti-clogging screens are in high demand worldwide, as our team of experts have successfully developed a product that helps our customers operate their plants during the monsoon season.
Most local mesh suppliers often confuse customers by offering higher wire diameters under the pretext of increasing wear life, but this reduces the overall screening area, decreasing the overall plant efficiency. We always try to educate all our customers on the importance of selecting the right wire diameter according to their desired separations, thus resulting in higher productivity and a lower cost per ton on their screenings.
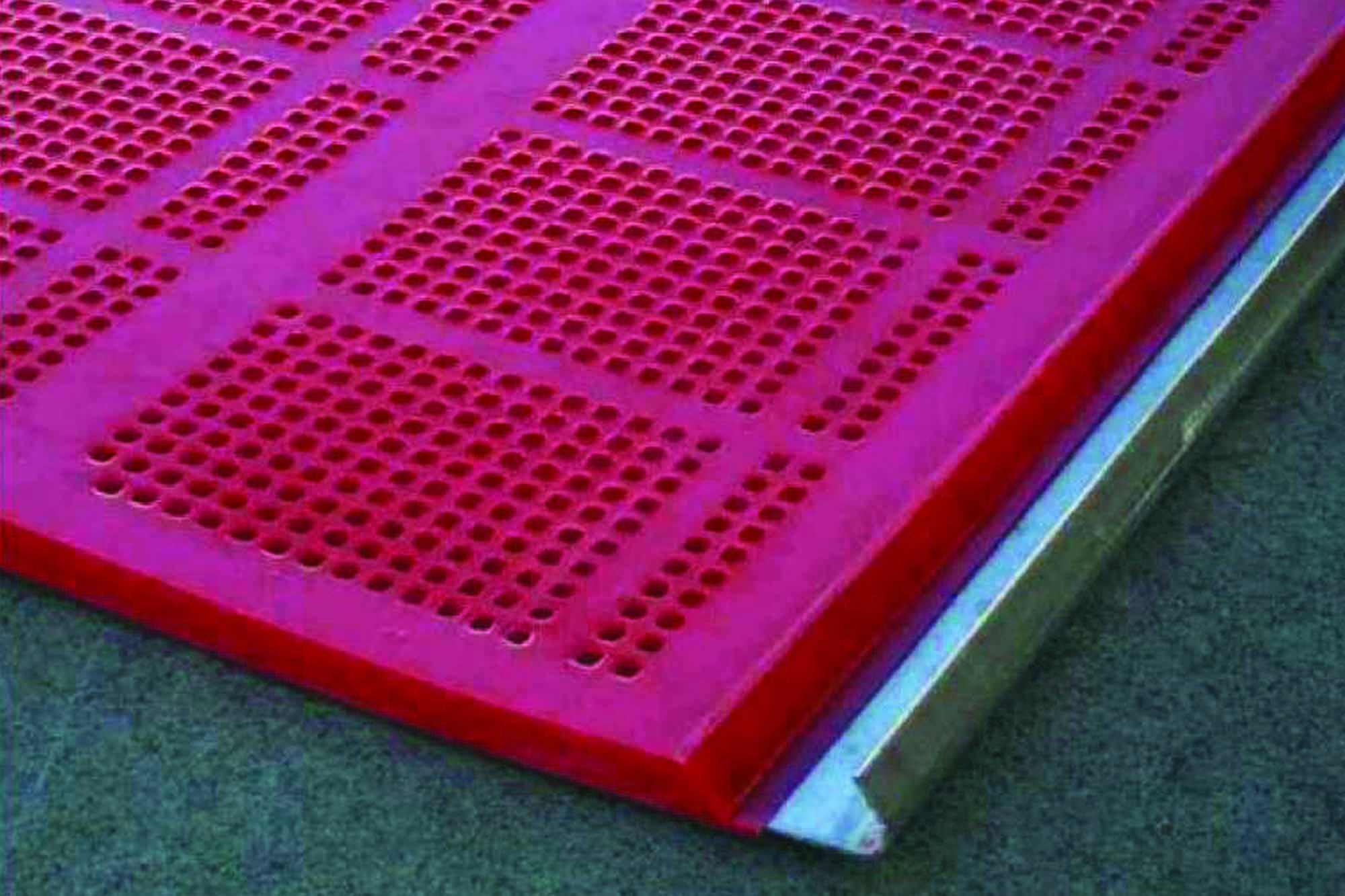
Could you elaborate on how sustainable materials in your screening media benefit the environment and enhance product performance?
At Ashar Locker, we strive to ensure that our products are efficient and environmentally sustainable. For example, many of our competitors use a chemical named MOCA for manufacturing Poly-urethan panels, which is very toxic and is responsible for causing cancer to the people involved in manufacturing these panels. This is done just to save cost. Moreover, when a customer uses any such panel at their site, they are exposing themselves to harmful emissions from these panels when exposed to sunlight. We at Ashar Locker do not use any such materials that may harm our employees, customers and the overall environment.
We also believe that it is not just our responsibility but also the customers’ responsibility to ensure that they ask the right questions of their suppliers during the procurement stage to ensure that such chemicals are not being used for their products. Only then will environmentally sustainable products continue to grow on the market.
How has the demand for screening media evolved, and how is Ashar Locker adapting to meet the emerging needs?
Over the years, there has been a significant shift from customers to good-quality products. Our customers now understand the importance of products that add value to their processes, resulting in higher productivity and a lower cost per ton on their screening. Our regular onsite plant audits and performance reports help them improve their product quality per customer demand.
There is a huge demand for Screening media solutions to support the ongoing infrastructure projects in India. Moreover, the artificial sand market has taken demand to the next level, resulting in overall growth and profitability. This year, the mining market has also shown some significant growth, and hence, we expect the demand to further improve over the next few quarters.
For more information, visit: https://www.asharlocker.com/
Cookie Consent
We use cookies to personalize your experience. By continuing to visit this website you agree to our Terms & Conditions, Privacy Policy and Cookie Policy.