Achieving crushing and screening efficiency
By Edit Team | February 23, 2017 9:23 am SHARE
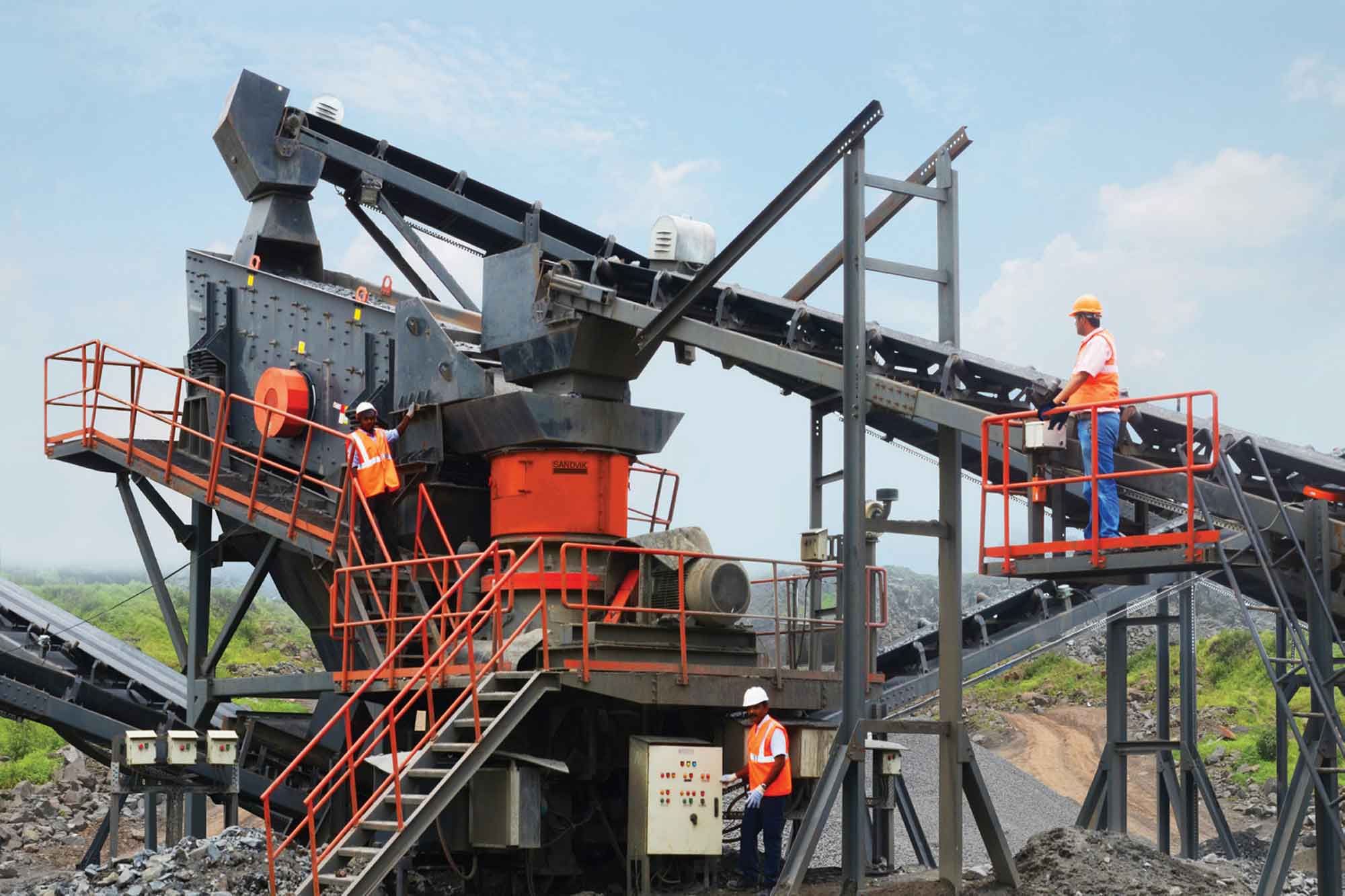
A summary through the experts opinion on how to achieve cost effective efficiency when it comes to crushing and screening sector.
The grinding and crushing of ore – is the most energy intensive step in mining. Also called as Comminution, the step involves the usage of tremendous amount of energy in mineral processing operations. There are a number of integrated strategies which can improve efficiencies and reduce energy use. New grinding technologies combined with selective blast design, ore sorting and waste removal and advances in modelling are just some of the approaches companies are adopting to improve ore grades and cut energy costs.
In this article we look at the steps that can be useful in achieving cost and energy efficiency for the crushing and screening industry.
“Cost and energy efficient crushing and screening does not mean low-priced Crusher or low running cost of Crusher. The main contributors in crushing and screening cost comes from cost of fuel or energy and tyre cost which is around 50 per cent in the conventional crushing system. So most of the miners have started programs to eliminate or reduce trucks,” says Sandipan Majumdar, Product Specialist Hazemag India.
Agreeing with the views of Majumdar, Chiranjit Banik, Product Specialist, Hazemag India says, “Most cost effective way is to use a combination of mobile or semi mobile crusher with integrated Wobbler and a conveyor from in-pit to out-pit that they can move along with the quarry face with the method that is known as ‘Truck and Shovel’.”
Sharing the advantages of the ‘truck and shovel’ method, Majumdar says, “The system is fuel efficient. Following the quarry face, it avoids transportation and thus saves diesel. In addition to this, it is easy to relocate, within few hours and not weeks.”
He further says, “Transporting the material using a suitable conveyor from in-pit to out-pit reduces the movement of the truck. This means feeding at the face of excavation.”
Banik says, “The technique of screening the under size from the feed material using an integrated Wobbler, means higher capacity is achieved by the system. Horizontal feeding facilitates straight line feeding and thus causes a major reduction in the jamming of feed material. Additionally, there is no need of conventional ramps or hoppers as the feed material builds up a ‘natural bunker’. Lower ramps are required when it comes to feeding with dumpers.”
The versatility of the Hazemag equipment is ensured by a comprehensive range of optional extras that allows the right machine to precisely match the demands of customer’s specific application. Range of mobile/ semi mobile crushers and screeners provides customer focused solutions for various core sectors and construction industries. The product mix encompasses feeder breaker, sizers, roll crushers, hammer mills, impact roll crushers, roller screens, apron feeders, chain conveyors for optimum solution. These range from quarrying applications processing material such as coal, limestone, iron ore aggregates and stones and other minerals.
Hazemag range of equipment has been proven throughout the world operating (more than 750 nos crushing, screening and conveying equipment with the biggest capacity of Feeder Breaker @2000 TPH) in variety of applications.
Sharing about the contribution of the company, Majumdar says, “In India Hazemag has supplied 37 units of crushers of various sizes from 2000 TPH to 250 TPH, with an output of (-) 150 mm to (-) 50 mm in single stage. As the different units are compatible with each other, they can be combined to operate in a train depending on the products required or are equally productive working as standalone units Hazemag mobile / semi mobile units are built to the highest quality and designed for ease of mobility, quick set-up time and transportation. “
Majumdar informs, “Many new features in the latest range of equipment have been introduced to simplify operation and maintenance and ultimately maximize uptime.”
These features include:
• Low investment,
• High crushing ration.
• Set-up at mine site without foundation.
• No conventional retaining wall is required for dumping the material in to feeder breaker
• PLC control system to enables the operator to fully control the performance of the unit from the control panel.
The Hazemag HFB series is a modularly designed system which fulfils a multitude of tasks in mining, on stockyards and trans-shipment sites and in the bulk goods industry. With the integration of Hazemag roller screen HRS into the chain conveyor the operator has an option which optimizes the volume flow towards the crushing roll. The same HFB plant but with integrated roller screen considerably increases the plant’s total throughput. Another advantage of the integrated pre-screening is the reduction of fines in the product granulation size.
According to Rajender Khoda, Group Business Development Advisor, Puzzolana Machinery Fabricators, the cost of operation and fuel efficiency are the important factors in the selection of crushing plants. He says, “Two major factors affecting the cost of operation is wear cost and fuel cost. Wear cost can be controlled by using right mix of manganese in wear parts while fuel cost can be minimised by using the Diesel-Electric power in place of conventional Diesel-Hydraulic Power. Electric drives are highly efficient and will have low operation, low maintenance cost and are also environmental friendly.”
Explaining the company’s offerings in the crushing and screening equipment sector, Khoda says, “Puzzolana Mobile Crushers and Screen are dual power system and we are the only manufacturer in India with dual power technology. This technology is environmental friendly and customer can either choose to operate the crusher with on-board DG set or can tap the external grid Power whenever possible. Puzzolana incorporated latest technology in their Track Crushing and Screening Plants.”
Sandvik Mining and Rock Technology, India is another leading name in the crushing and screening equipment sector. “Sandvik’s crushing and screening equipment offers the market’s most advanced and complete product range and a solution approach that contributes to increasing performance and productivity for our customers. Our partnership concept basically means that our customers will always find us available to discuss their challenges and opportunities,” says Ashoktaru Chattopadhyaya, Business Head Crushing and Screening, Sandvik Mining and Rock Technology, India.
He further says, “We address questions like- What can be improved? How can we reduce downtime? How can we optimize uptime? Do the operators need more training? Where can we further lower cost or increase output? We can analyse the problems together and refer them to dedicated specialists. This approach will lead to improved productivity, lower cost, improved energy efficiency and eventually better profitability.”
The challenge to lower the cost per ton of finished products requires a thorough knowledge of the whole quarrying process, combined with the best in equipment, service, support and consumables.
Discussing the features of the crushing and screening equipment by Sandvik Asia, Chattopadhyaya says, “Sandvik has a wide range of Crushers for any crushing needs in both Mining and Aggregate sector. In Coal Mining, Sandvik was the pioneer to introduce Horizontal Shaft Impactors (HSI), in stationary as well as wheel-mounted application; fully manufactured at our facility in Pune. Leveraging the upsurge in Iron Ore mining, Sandvik has geared up offerings in this sector too. We have already developed and started manufacturing of track mounted crushing units in India, and the field results are overwhelming.”
He further says, “One of our key contributions to sustainability is our state-of-the-art solutions for sand manufacturing. We have maintained our dominance in this sector and see significant opportunities in sand manufacturing plants coming up in Mumbai, Pune, Bangaluru, Madhya Pradesh and Kerala.”
Chattopadhyaya says, “Sandvik VSIunit is unique and has made sand processing possible in 3 stages of Crushing with the introduction of SandvikCH550 in stationary and mobile applications. When it comes to Sand Production Sandvik is dependable.”
Thus, the collective usage of the modern mechanised techniques will be of great help to the crushing and screening segment thereby achieving cost and energy efficiency.
Cookie Consent
We use cookies to personalize your experience. By continuing to visit this website you agree to our Terms & Conditions, Privacy Policy and Cookie Policy.