Allround Shoring TG 60 Ideal for Construction of Bridge
By Edit Team | July 25, 2022 6:36 pm SHARE

The TG 60’s modular design ensures that the system can be assembled quickly and safely despite the heights involved and be optimally adapted to the geometry.
Layher is a German company that has been manufacturing high-quality scaffolding systems for over 60 years. Layher has more than 35 sales subsidiaries all over the world. The materials are used for construction and building in a variety of industries, including shipyards, offshore, chemical facilities, power plants, refineries, and cement plants. Layher has become the global industry standard for scaffolding systems due to its cutting-edge products, cutting-edge technical solutions, and unwavering commitment to its customers’ needs.
Modular scaffolds are now commonly referred to as Layher Allround Scaffolding in the marketplace. The revolutionary Allround joint superseded the traditional scaffold approach with its distinctive, bolt-less attachment method. Allround Scaffolding offers unparalleled diversity in use: on building sites, in industry, in the chemical industry, in power plants, in the aircraft sector, in shipyards, in the event sector, in theatres and arenas, Allround Scaffolding fully lives up to its moniker as an “Allrounder.”
With the most challenging constructions and architecture, including the engineering construction industry, Allround Scaffolding perfectly met all requirements for working, protection, a facade, or support scaffolding. The Allround joint, which enables up to 8 connections in one plane with automated right angling and adjustable angle selection using self-locking wedge head couplers, is the system’s main component.
Application of Allround Shoring TG 60 for High Rise Structures with a Difficult Geometric Profile
Allround shoring TG 60 is suitable for the transmission of heavy loads at a height of 40 metres, plus a height difference of 20 metres, with the surface of the structure being curved inward relative to the ground contact area shown in the ground plan. The solution: Allround Shoring TG 60. Its modular design ensures that the system can be assembled quickly and safely despite the heights involved and be optimally adapted to the geometry.
The construction of a new continuous casting system on the premises of the steelworks makes it a site of superlatives. For example, the gigantic lattice boom crane towering up to 110 metres above the roofs is visible for miles. What’s not visible is the site itself: for the company’s biggest single investment, excavators have dug a 45-meter-deep hole, in which the new production facility is now being built. For concreting a 25-meter-long binding beam with a dead weight of 21 tonnes per metre, a 40-metre-high shoring structure had to be assembled too. When planning the shoring structure, not only heavy loads at great heights – up to 5.5 tonnes per standard – had to be taken into account, but also a difficult geometric situation. These included a height difference of 20 metres, with the structure’s surface curving inward relative to the ground contact area shown in the ground plan. The time factor, too, could not be underestimated: ten erectors had just twelve days to build a structure weighing around 110 tonnes.
The combination of high-strength Allround TG 60 Shoring Frames with standard components has been proven in the Allround range and the construction company’s crucial advantages. On the one hand, their rapid assembly considerably improved efficiency at the construction site. This was assured by the reduced number of components in the prefabricated shoring frame when compared to individual parts, the low component weight of no more than 18 kilograms, bolt-free wedgehead connectors, and optimum use of material to variable bay lengths. The TG 60 system is thus adapted to the actual loading situation and to the existing geometry. Another prime advantage of Allround Shoring TG 60 is its compatibility with the comprehensive component range of the Allround system.
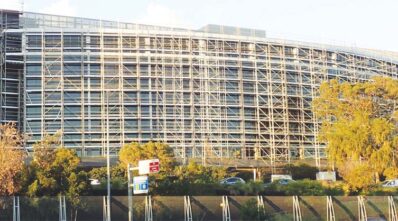
Layher Scaffolding a Free-Standing Curved Solution:
The Allround construction kit makes it affordable to satisfy any requirement on a construction site. Its interoperability with the Allround system and its quick wedge-head connectors guarantee the exceptionally adaptable construction of shoring structures, whether it is used to interconnect working levels and stairway towers, join massive shoring structures to ledgers and diagonal braces or modify geometry.
For this project, the combination of Allround TG 60 shoring towers and individual components of the modular Allround range was also a convincing solution. Underneath the binding beam, square-shaped shoring towers, linked together to brace them, were used to transmit the heavy loads. Allround compatibility with Allround parts could be achieved using Allround diagonal braces and ledgers, i.e., by bolt-free wedge-head connection instead of time-consuming structures using tubes and couplers. Also, no further single towers had to be built for the necessary widening. The TG 60 system offers the possibility of extending shoring towers with single frame sections. In order to accomplish this, the scaffolding erectors placed an additional shoring frame in front of each individual shoring tower. This frame could be connected to the square-shaped shoring tower using 1.09 metre to 3.07 metre long Allround ledgers and diagonal braces, depending on the specific requirement—in this case, to form a 2.07-meter wide bay. That saved on material and assembly time. The ingenious solution to compensating for the 20-metre height difference was that, for some bays, the ground contact surface was 20 metres lower on one side. To compensate for the differences in elastic deformation inside the overall structure over its height and to avoid stresses in the scaffolding, the erectors used a special rubber pad.
As regards height, in view of the great height, the topic of occupational safety was also in focus. Wherever practical, the shoring was preassembled on the ground section by section, with the precisely fitting sections then being lifted into position by crane. If this was not possible, the safer assembly sequence for Allround Shoring TG 60 came into its own. This procedure automatically affords all-around side protection during upright assembly, even without additional components, allowing safety regulations to be met in full for the first time in shoring construction. Once built, the shoring ensures safer working for the professionals engaged in subsequent work. In addition to the use of Allround brackets as a walkway for the concreting work and of an Allround stairway tower as site access, a completely closed work platform was also quickly constructed about 1.8 metres below the formwork level, using Layher scaffolding decks. This is how the scaffolding company Rende offered the construction company not only a safer solution with the new Allround Shoring TG 60 but also an economical one. Assembly and dismantling made progress ahead of schedule, despite a narrow time window, which sped up construction work and delighted the contractor.
For the construction of a continuous casting system, the new Allround Shoring TG 60 from Layher permitted work at 40 metres up, for concreting a 25-metre-long binding beam.
Expertise shared by:
Mithilesh Kumar, Director, Layher Scaffolding Systems Pvt Ltd
Cookie Consent
We use cookies to personalize your experience. By continuing to visit this website you agree to our Terms & Conditions, Privacy Policy and Cookie Policy.