Battery-operated earthmoving equipment will drive the construction projects
By Edit Team | September 7, 2023 12:29 pm SHARE
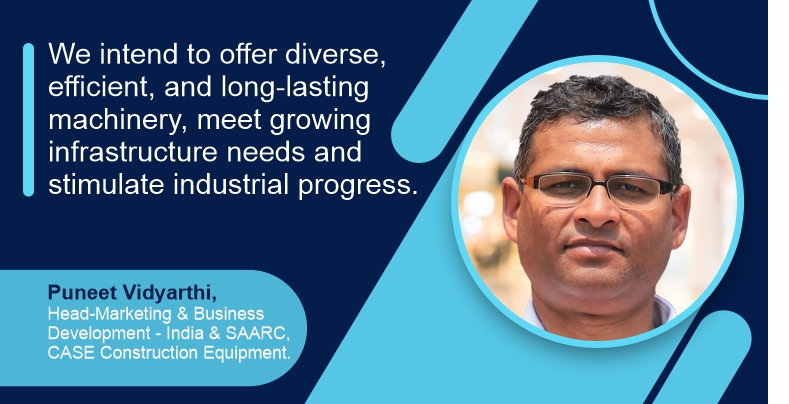
We intend to offer diverse, efficient, and long-lasting machinery, meet growing infrastructure needs and stimulate industrial progress.
Discussing the earthmoving equipment trends in infrastructure projects, Puneet Vidyarthi, Head of Marketing & Business Development for India & SAARC at CASE Construction Equipment, briefly elaborate on advancements in machinery efficiency, procurement and execution challenges, safety concerns, and the potential for battery-powered equipment to shape future projects.
What are the current trends and projections for the earthmoving equipment industry concerning infrastructure development?
The earthmoving equipment industry is currently experiencing a range of trends and projections tied to infrastructure development. Factors like urbanisation, population growth, and the requirement for enhanced transportation and utility systems are driving the demand for robust and efficient machinery. This trend will persist as governments and private sector entities globally invest in large-scale infrastructure projects such as roads, bridges, airports, and utilities. Additionally, an increasing emphasis on sustainable construction practices is increasing, resulting in a heightened interest in technologically advanced and environmentally friendly equipment.
Being one of the leading players in this industry, we are well-poised to capitalise on these trends. Through innovative product offerings, cutting-edge technologies, and a commitment to sustainability, we are expected to play a significant role in shaping the future of earthmoving equipment. Our dedication to providing versatile, efficient, and durable machinery aligns with the evolving requirements of infrastructure projects, ensuring a continued contribution to the industry’s growth and development.
How have recent advancements in backhoe loaders, excavators, and asphalt plants impacted construction projects’ overall efficiency and productivity?
Recent advancements in backhoe loaders and excavators have revolutionised the construction industry, significantly enhancing project efficiency and productivity. The integration of these advanced machines has proven to be a game-changer, optimising operations and yielding substantial long-term benefits, including improved outcomes, increased profitability, and a favourable return on investment.
The infusion of cutting-edge smart technologies has ushered in a new era for the construction sector. Telematics systems, for instance, have enabled real-time monitoring on these machines. These systems offer live updates on maintenance, tracking, utilisation, and security, enabling proactive maintenance and early issue detection. Timely SMR alerts convey critical information such as fuel usage, battery status, and geo-fencing, effectively reducing inefficiencies caused by unexpected equipment malfunctions.
Additionally, advancements in backhoe loaders have played a pivotal role in boosting construction efficiency. These versatile machines seamlessly combine digging and loading tasks, streamlining construction processes, minimising downtime, and optimising resource allocation.
CASE Construction leads the way by offering diverse excavators tailored to various needs. Their CASE Intelligent Hydraulic System (CIHS) significantly enhances fuel efficiency, breakout forces, swing speeds, and swing torque, resulting in a remarkable 5 percent increase in productivity. The CX220C LC Excavator, designed for tough applications, features a fuel-efficient electronically controlled engine and various energy-saving controls, ensuring high productivity and efficiency.
Similarly, the Case 770 NXe Loader Backhoe, equipped with advanced electro-hydraulics technology and a reliable FPT S8000 engine, excels in demanding loader applications. Operating in three modes—ECO, STANDARD, and POWER—it offers fuel economy, productivity, and enhanced efficiency, leading to impressive savings of up to 24 percent on fuel costs. This versatile powerhouse perfectly balances power and efficiency, setting new standards in the industry.
When procuring earthmoving equipment and executing infrastructure projects, what are the major challenges and roadblocks faced?
When procuring earthmoving equipment and executing infrastructure projects, budgetary limitations often hinder the acquisition of top-tier machinery. They can influence the scope of projects, underscoring the importance of making strategic choices that align with project requirements. Negotiating through the intricate web of regulatory approvals and permits demands precision and persistence, as delays in these processes can reverberate through project timelines and costs. Supply chain disruptions and shortages of skilled workers are prominent issues affecting the construction sector.
What strategies or technologies have been adopted to overcome these obstacles?
CASE acknowledges the importance of agility in tackling challenges and sustaining project momentum. Our ability to offer high-quality, cost-effective equipment is bolstered by sourcing parts from India and collaborating closely with local vendors for engines, engine components, forgings, and essential parts. This approach optimises costs.
We are committed to enhancing operator skills through our Skill Development Centre, part of the Hunar initiative, which supports the Indian Government’s Skill India Mission by training 240 professionals annually. Located in Sonvai, Rau, near Pithampur, the 1200-square-foot facility houses two theoretical instruction and counselling classrooms. We also run a training centre at our Pithampur plant, continuously honing operators’ abilities. Additionally, we’re exploring partnerships with larger training organisations to foster new entrepreneurs. Our dedication to innovation and cost efficiency remains unwavering.
What are the most critical safety concerns and project deadline challenges encountered by equipment owners and project managers while operating earthmoving equipment?
Operating earthmoving equipment presents a complex interplay of safety concerns and project deadline challenges that necessitate careful consideration and strategic management. Safety issues encompass a range of critical factors, from operator training and ground stability to minimising blind spots, managing personnel interactions, and maintaining equipment rigorously. To address these concerns, high-quality equipment, effective training protocols, clear communication, meticulous equipment maintenance, and unwavering adherence to safety measures are imperative in averting accidents and injuries on construction sites.
Which best practices or innovations have been introduced to address these issues effectively?
Our commitment to safety and productivity is ingrained in the design of our machinery. For instance, our 770EX series loader backhoes exemplify this approach by incorporating cutting-edge features that prioritise operator safety and comfort. The integration of advanced telematics enables real-time monitoring, while an audio-visual warning system with over 25 alerts enhances operator awareness. Engine protection shutdown minimises downtime, and expansive cabins with optimised sightlines contribute to enhanced visibility. Comfort is paramount, with ergonomic seats and intuitive controls creating an environment conducive to efficient work. Emissions, and compliance with environmental regulations can drive its adoption.
In shaping future infrastructure projects, battery-operated equipment can play a pivotal role by contributing to greener construction practices and aligning with sustainable development goals. It can lead to quieter operations, decreased air pollution, and enhanced job site safety. As technology advances and charging infrastructure improves, battery-operated equipment has the potential to become a cornerstone in the industry’s shift towards more environmentally friendly and efficient construction practices.
What are the potential barriers and incentives for wider adoption of battery-operated equipment in the industry, and what role might it play in shaping future infrastructure projects?
The broader adoption of battery-operated equipment in the construction industry faces challenges and opportunities. Barriers include higher costs, limited charging infrastructure, and concerns about battery life and efficiency, especially regarding construction equipment. However, incentives like reduced operational costs, lower
Cookie Consent
We use cookies to personalize your experience. By continuing to visit this website you agree to our Terms & Conditions, Privacy Policy and Cookie Policy.