Cranes engineered for toughest mining challenges
By Staff Report | October 21, 2024 3:35 pm SHARE
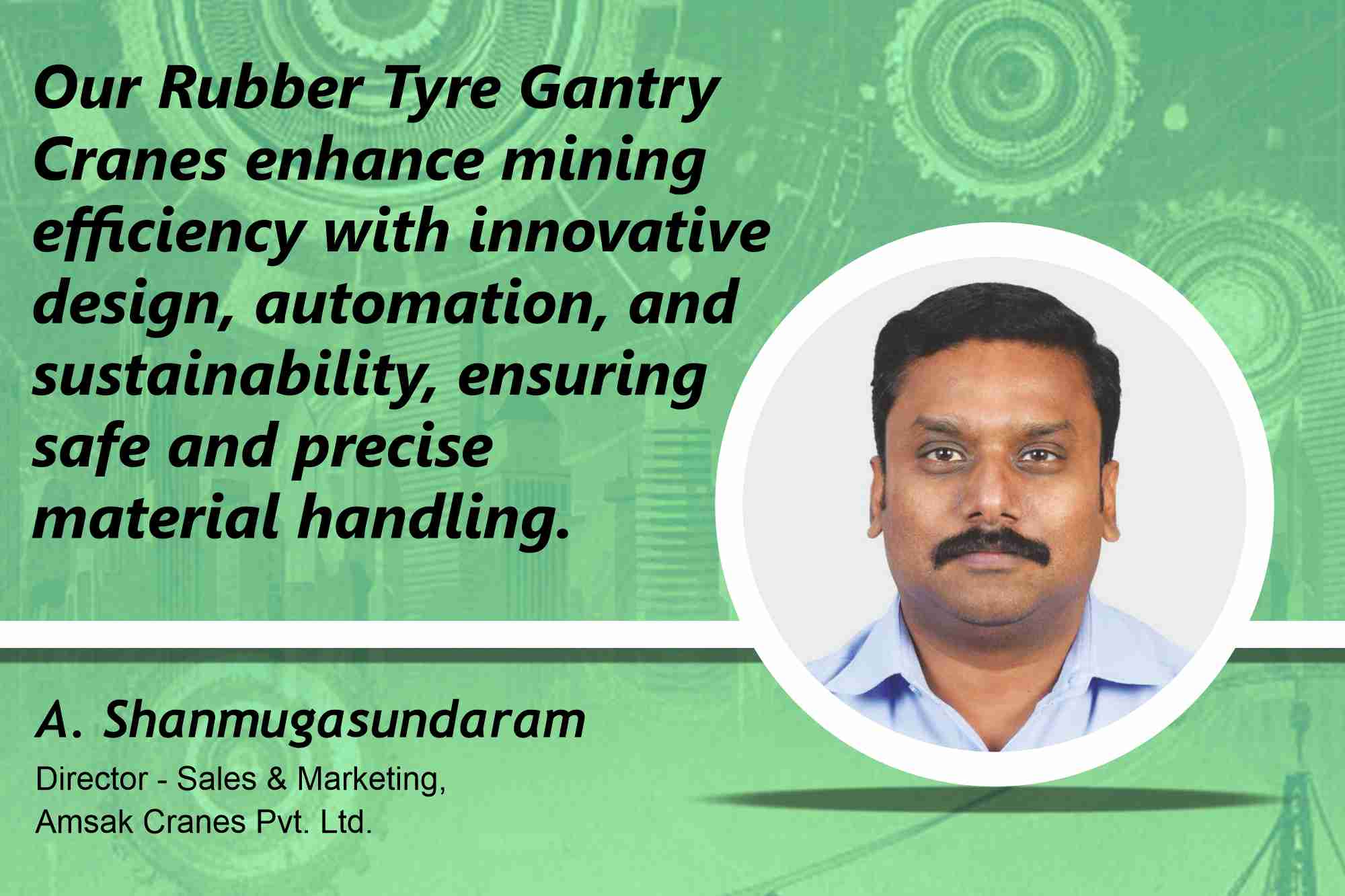
Amsak cranes are meticulously designed to confront the unique challenges posed by heavy loads and harsh terrains. With a focus on durability, safety, and efficiency, they ensure that every lift meets the rigorous standards of the industry.
What key features make your cranes suitable for the unique challenges of the mining industry?
When we design cranes for the mining industry, we focus on addressing the unique challenges of heavy loads, rough terrains, and harsh environmental conditions. Our cranes are engineered with reinforced steel structures, robust hoisting mechanisms, and high-capacity motors, allowing them to reliably lift loads of up to 200 tons. For oversized or irregularly shaped materials, we offer specialised lifting attachments to meet specific requirements.
We prioritise durability in our designs, utilising corrosion-resistant materials like galvanized steel and weatherproof coatings to combat the dust, moisture, and extreme temperatures commonly found in mining operations. Our cranes also feature filtration systems and robust hydraulic seals to protect vital components from wear and tear.
Safety is paramount, and our cranes are equipped with advanced features such as overload protection, anti-sway technology, and emergency stop systems. These ensure smooth operations and minimise the risk of accidents in challenging conditions. Additionally, we provide custom mobility solutions, including undercarriages designed for uneven surfaces, all-terrain tires, and outriggers to enhance stability.
To boost efficiency, we offer automation and remote operation options, allowing for precise control from a distance. Understanding the high costs associated with downtime, we also focus on ease of maintenance, incorporating accessible service points and modular components. By concentrating on these critical aspects, we ensure our cranes meet the rigorous demands of the mining industry, delivering reliable, durable, and safe solutions for heavy-duty applications.
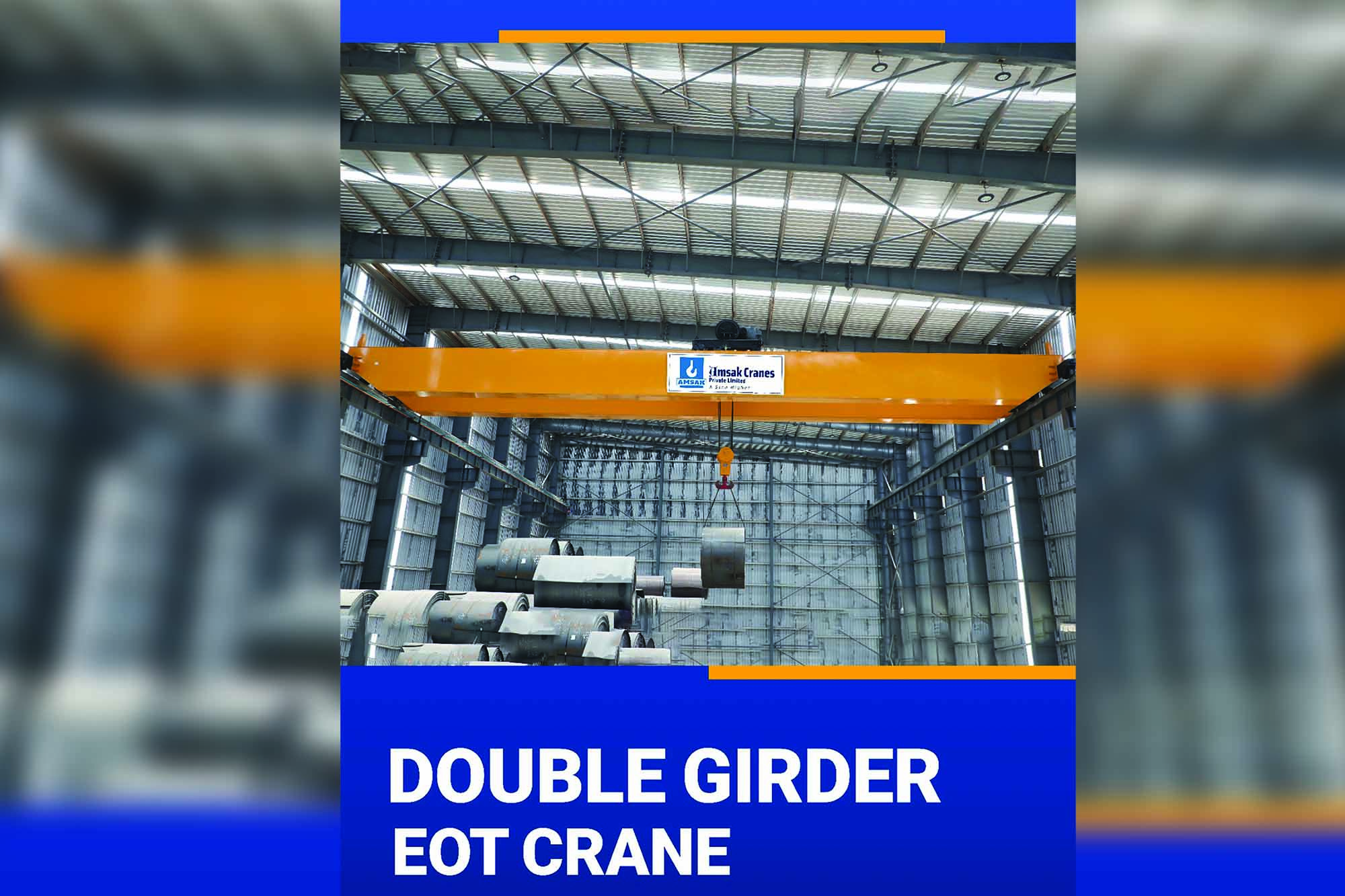
How do your M8 Extra Heavy Duty Cranes cater to the rigorous demands of the mining industry?
We design our M8 Extra Heavy Duty Cranes specifically for continuous, heavy-duty operations in the mining industry. These cranes are equipped with superior load capacities and classified under the FEM/ISO M8 high-duty class, enabling them to handle frequent starts, stops, and heavy loads, typically between 50 to 200 tons. This capability is crucial for 24/7 mining operations where heavy machinery and raw materials need constant movement.
Our cranes are constructed from high-tensile, corrosion-resistant steel to endure harsh environments, with protective coatings that shield them from dust, moisture, and chemicals. We prioritise safety with features like advanced overload protection systems and integrated anti-sway technology, which stabilise loads during transport. Emergency braking systems further enhance safety, ensuring instant stopping in case of power failure.
Additionally, our cranes are powered by high-efficiency motors with Variable Frequency Drives (VFDs) for precise control of speed and movement, crucial for handling sensitive loads. Designed to resist dust and moisture, our cranes operate efficiently in extreme temperatures, maintaining reliability in all conditions.
We also offer automation and remote control capabilities, allowing for safer and more efficient operations, especially in hazardous environments. Our cranes feature self-diagnostic systems for early detection of potential issues and easy access for maintenance, ensuring minimal downtime.
Our M8 Extra Heavy Duty Cranes provide the performance, reliability, and longevity essential for the rigorous demands of mining operations, allowing us to deliver customized solutions tailored to specific applications.
In what ways do your Gantry and Goliath Cranes leverage automation to improve mining operations?
We understand the critical role that automation plays in industries like mining, where efficiency, safety, and precision are non-negotiable. Our Gantry and Goliath Cranes are equipped with advanced automation and control systems designed to streamline operations, reduce human error, and enhance productivity. We utilise Intelligent Control Systems, such as programmable logic controllers (PLCs) that automate repetitive tasks like lifting and positioning, ensuring quick and accurate operations, especially in the high-demand mining sector.
Our cranes feature user-friendly Human-Machine Interfaces (HMIs) that provide operators with real-time data on load weight and positioning, essential for efficient handling in complex environments. Remote operation capabilities, including radio remote controls and wireless data transmission, allow for safe and flexible management of heavy loads from a distance, crucial in hazardous conditions.
We integrate anti-sway technology to prevent load swinging, and collision avoidance systems with laser sensors for real-time obstacle detection. Our load management systems ensure optimal weight distribution and protect against overloads.
Our cranes are equipped with energy management systems and variable frequency drives, promoting sustainable operations. Finally, our automation solutions are customisation, allowing us to meet the specific needs of our clients in the mining sector. By embracing automation and Industry 4.0 technologies, we are paving the way for smarter, safer, and more efficient operations in the future.
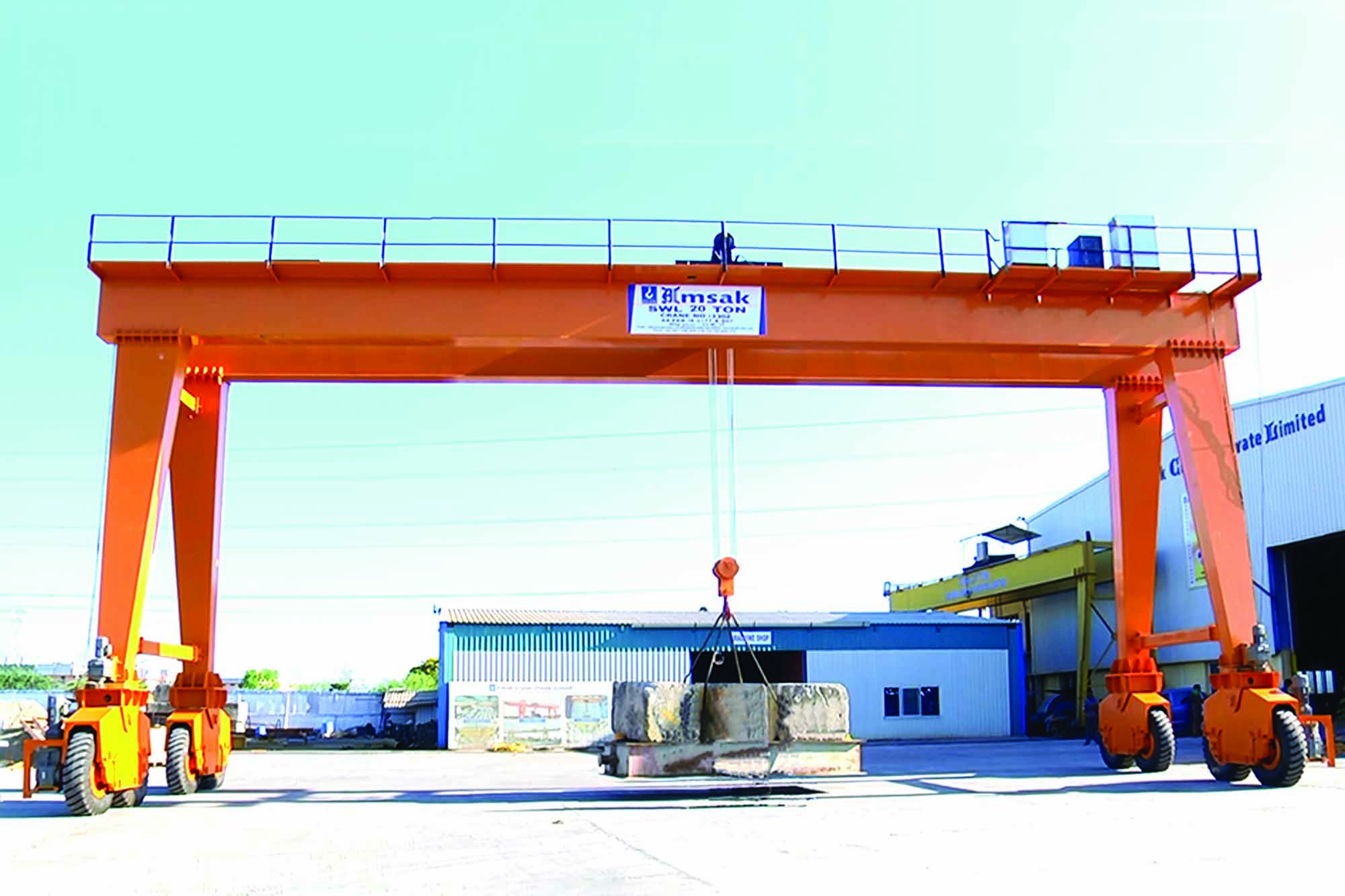
What innovations enhance the efficiency and safety of your Rubber Tyre Gantry Cranes in mining operations?
We implemented several innovations in the design and functionality of our Rubber Tyre Gantry Cranes (RTGs) to tackle the unique challenges of material handling in large mining yards. Our main objective is to enhance productivity, reliability, and operational efficiency through advancements in mobility, energy efficiency, automation, and safety systems.
Our RTGs feature advanced multi directional steering, allowing for flexible navigation in tight spaces, which is crucial in mining environments. We have integrated hybrid power systems that combine diesel engines with electric motors, significantly reducing fuel consumption and emissions. Our fully electric models ensure zero emissions, aligning with sustainability goals.
To further optimise operations, we offer fully automated options for material handling, with remote control systems that enable safe operation from a distance. Our cranes are equipped with load-sensing technology and anti-sway systems to ensure precise and safe handling of heavy loads.
The integration of IoT connectivity facilitates real-time tracking of operations and predictive maintenance, minimising downtime. With robust safety features, durable designs, and modular configurations, our RTGs are tailored to meet the rigorous demands of mining projects, ultimately maximising efficiency and reducing operational costs.
What benefits do upgrading older cranes offer for operations in the mining industry?
Upgrading older cranes in demanding environments like mining presents us with numerous advantages, primarily in extending equipment life, enhancing operational efficiency, and improving safety. Our experience shows that mining cranes face heavy-duty operations and harsh conditions, making upgrades a more cost-effective alternative to complete replacements.
By replacing critical components such as motors, hoists, and brakes, we can significantly rejuvenate a crane’s functionality. Strengthening structural components also allows older cranes to handle increased loads, while modern materials improve durability and resilience. Moreover, integrating automation systems enhances efficiency by reducing human error and speeding up material handling processes.
Modern upgrades like load monitoring and collision avoidance systems are essential for reducing accidents in hazardous mining conditions. Additionally, remote monitoring allows us to track performance in real-time, ensuring proactive maintenance and minimising unexpected downtime.
Crane upgradation provides a cost-effective alternative to new equipment, significantly lowering capital investment and ensuring compliance with current safety standards. By modernising our cranes, we not only boost performance but also align with Industry 4.0 technologies, positioning our operations for greater efficiency in the future.
For more information, visit: https://amsakcranes.com/
Cookie Consent
We use cookies to personalize your experience. By continuing to visit this website you agree to our Terms & Conditions, Privacy Policy and Cookie Policy.