Eco-friendly RMC with Green Pro certification
By Staff Report | September 11, 2024 4:15 pm SHARE
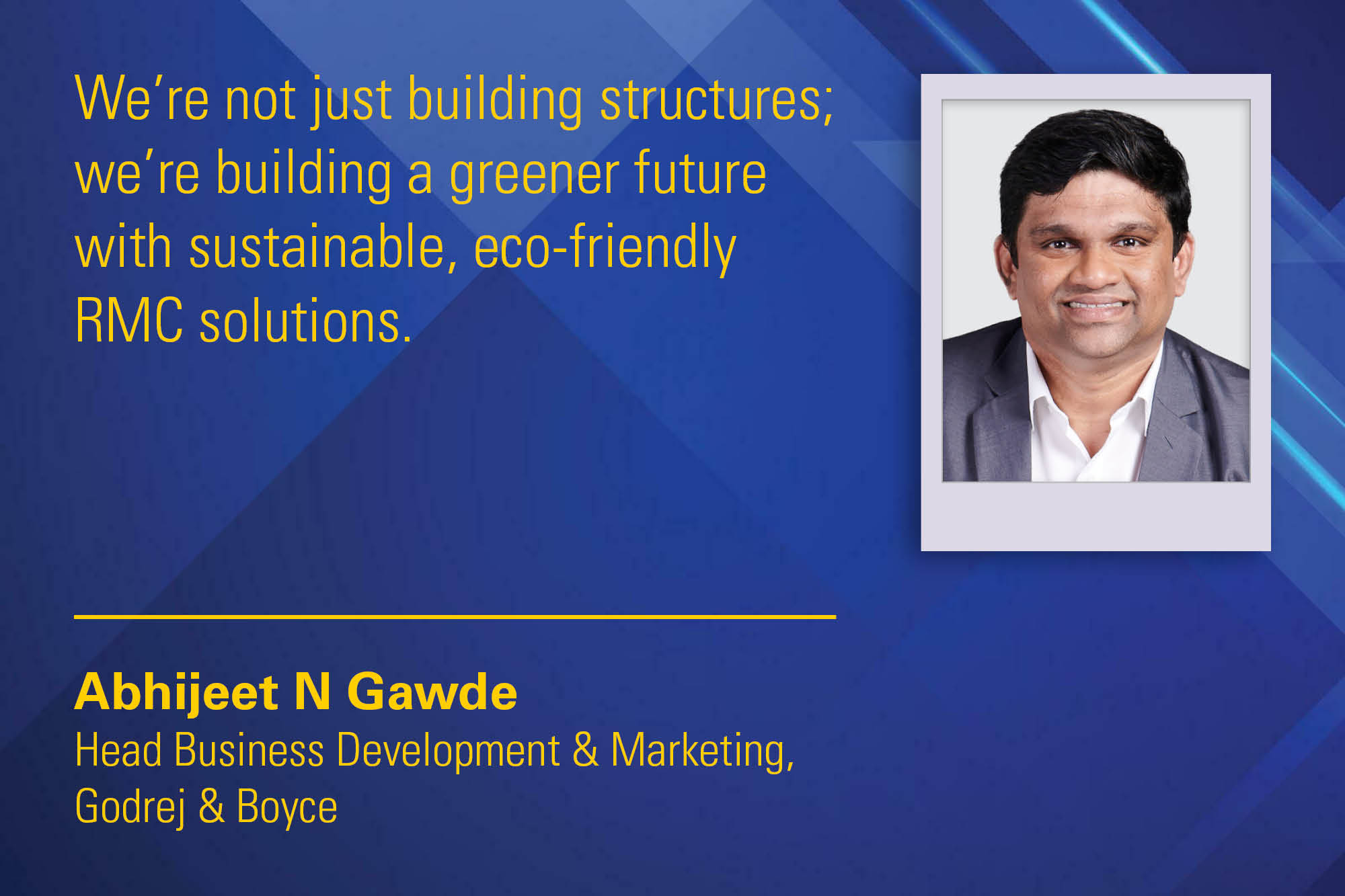
Godrej & Boyce TUFF brand pioneers sustainable, customisable RMC solutions certified by Green Pro. It utilises sophisticated technology and circular economy methods to produce high-quality, eco-friendly concrete products.
Please provide an overview of your current solutions in the concrete segment.
The Godrej TUFF Construction Materials brand provides a groundbreaking range of customisable and environmentally friendly solutions. Godrej & Boyce’s Construction company, which is part of the Godrej Enterprises Group, has obtained the Indian Green Building Council’s (IGBC) ‘Green Pro’ certificate for Ready-Mix Concrete (RMC) products such as Enviro TUFF, Xtra TUFF, and Easy TUFF.
Enviro TUFF is an eco-friendly concrete mix made by integrating industrial byproducts such as recovered Fly Ash or Grounded Granulated Blast Furnace Slag (GGBS). It reduces a project’s carbon footprint while improving its Green Building Rating. Similarly, we offer Xtra TUFF, a high-strength concrete version created utilising various cementitious material blends, resulting in dense, refined microstructures. Xtra TUFF is utilised in projects that demand thinner RCC beams and columns, such as high-rise buildings.
The Maharashtra State Electricity Board gave Green Energy Certificates to six of our Godrej Ready Mix Concrete Plants. We used the Circular Economy design concepts of ‘Recover, Recycle and Rebuild’ to recycle concrete trash into prefabricated concrete goods like construction blocks, pavers, culverts, ducts and other bespoke precast concrete products. We have established an automated Recycled Concrete Materials (RCM) manufacturing factory in Vikhroli, Mumbai. This industrial plant produces concrete blocks for walls and pavers from concrete rubble recycled from demolished concrete structures from building and infrastructure projects that would otherwise end up in overflowing municipal landfills. We have already recycled over 30,000 metric tonnes of concrete waste using circular economy concepts.
We are among the first RMC sectors to transition to 100% green energy. Similarly, our Recycled Concrete Materials (RCM) plant in Vikhroli West, Mumbai, uses only green energy.
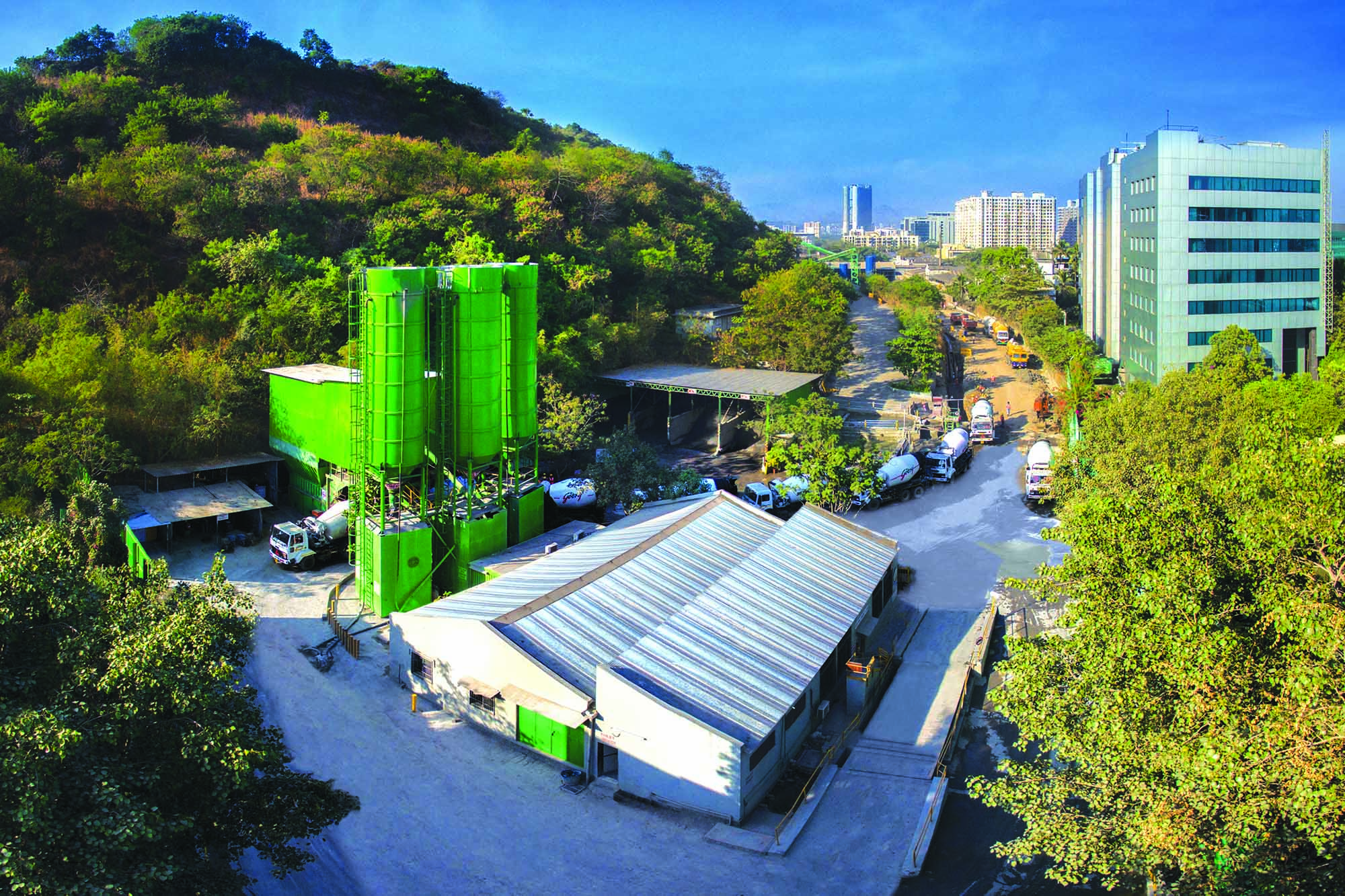
How does your product range cater to the needs of different types of construction projects?
We recognise that each building job is unique. That is why we provide customised RMC solutions to match the unique needs of each project. Our skilled engineers collaborate with clients to fully grasp their requirements. We create customised RMC mixes that ensure optimal performance and cost-efficiency using this collaborative approach.
In addition to the quality of RMC, client-centricity is important to our company processes. For over a decade, we have conducted third-party customer satisfaction surveys (CSS) through Nielsen across all of our three lines of business. Customer feedback has supplied us with insights that have enabled us to implement relevant improvement activities to improve our service quality. As a result, we have achieved best-in-class Net Promoter Scores (NPS) across all three of our business lines. Our NPS scores are 70 for Construction Materials, 89 for Real Estate Leasing, and 92 for Real Estate Development.
Over the last few years, our Construction Materials team has launched some pioneering initiatives to address our clients’ difficulties in the Real Estate and Construction industries. To deliver a seamless client experience, we used digital technology to create a one-of-a-kind mobile application called the ‘Godrej Go Tuff’ app. The ‘Godrej Go Tuff’ app includes convenient features such as real-time delivery tracking, which ensures transparency in optimising and managing every step of construction material supply from order to delivery. Godrej Construction’s Concrete Testing ‘Squad’ Van provides on-site testing services. It allows our customers to complete the approval process for ready-mix concrete mix design more quickly, as the results of mix design trials, cube testing, compressive strength, and sieve testing may be measured in hours.
What innovative technologies and practices do you employ to produce high-quality and durable concrete?
We have embraced cutting-edge technology by incorporating IoT devices and data analytics into our manufacturing operations. IoT is used to monitor mixer gearbox vibrations to predict gearbox failure, track the movement of transit mixers, deliver concrete and provide an estimated time of arrival (ETA) for the concrete ordered, and assist trucks in properly positioning on the weighing scale, allowing for accurate weighing. These advances allow for real-time monitoring of numerous parameters, resulting in exact control over the mixing and pouring processes. We continuously optimise our production procedures by studying data collected via IoT devices. This improves the quality of our RMC products and enables us to respond quickly to any deviations, assuring constant quality across production cycles.
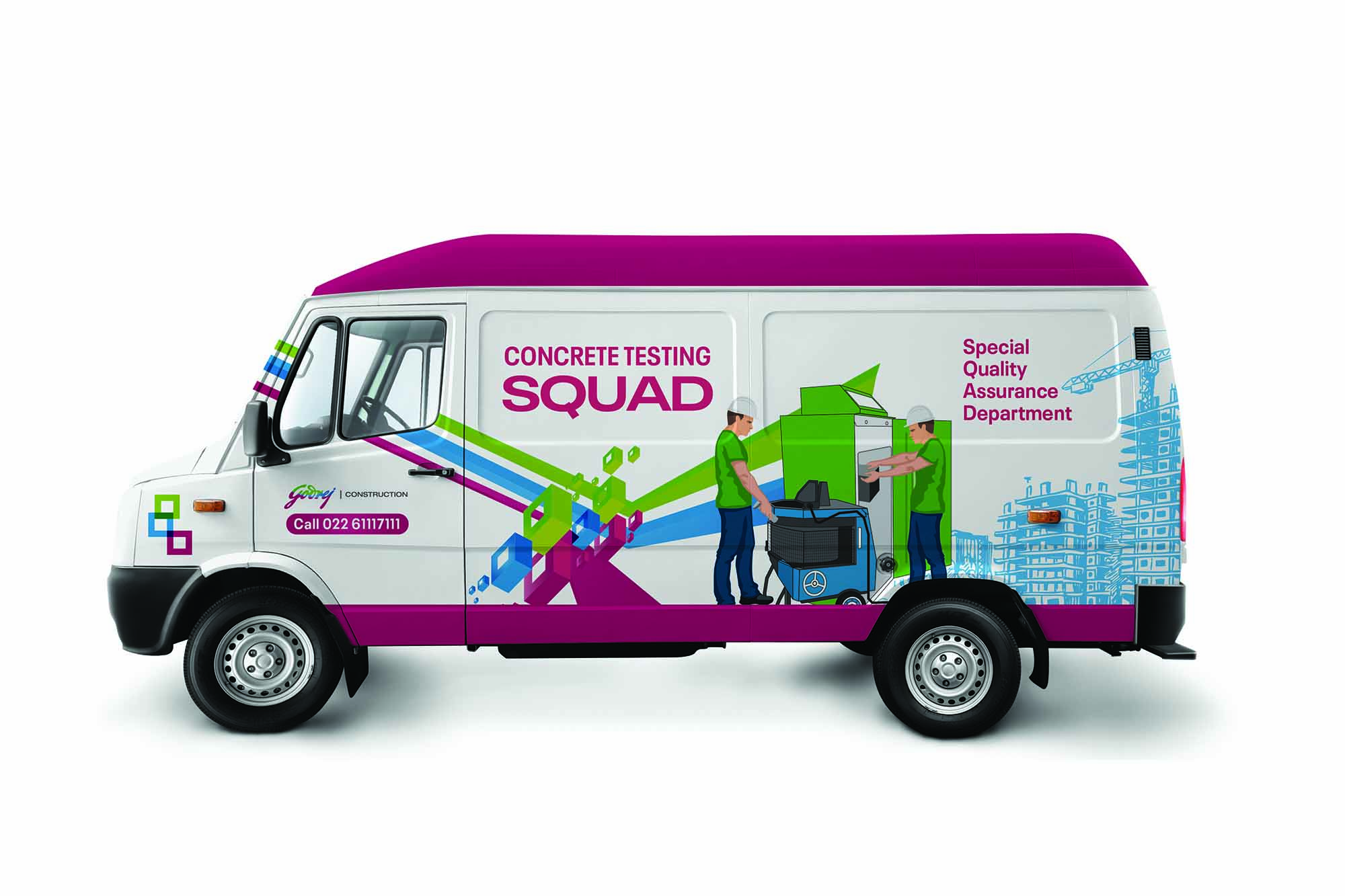
Our top aim is to ensure the highest quality RMC goods. Our RMC plants are certified by the Quality Council of India (QCI). Regular material testing, on-site inspections, and compliance with industry standards are all part of our quality control efforts. These stringent processes ensure that our RMC products are of the highest quality and comply with all applicable norms and regulations. Our RMC Central Quality Laboratory in Vikhroli, Mumbai, recently acquired a Certificate of Accreditation from the National Accreditation Board for Testing and Calibration Laboratories (NABL) per ISO/IEC 17025:2017. NABL accreditation demonstrates our commitment to providing high-quality products and services.
How is Godrej & Boyce incorporating sustainable practices into its RMC and concrete production processes?
Environmental stewardship is important to our business operations. We have introduced environmentally friendly production techniques and energy-saving technologies to reduce our carbon footprint. We also follow strict waste management guidelines and recycle water and other commodities.
Given rising infrastructure demands, the Ready-Mix Concrete (RMC) sector is approaching a tipping point. Ongoing trends, such as urbanisation, sustainable construction, and the requirement for quick project completion, create enormous prospects. The RMC concrete industry is on the verge of a significant transition, with an emphasis on sustainability, efficiency, and innovation. New product advancements and technologies, including smart concrete, 3D printing, carbon capture and utilisation, self-healing concrete, and recycled and green concrete, are poised to transform how we create buildings and infrastructure. At Godrej Construction, we are strategically aligned with these trends. We intend to capitalise on these opportunities by focussing on developing specialised goods in our sustainable line of TUFF Concrete solutions that address specific infrastructure requirements, guaranteeing that our clients receive the most efficient and dependable products.
What cutting-edge mix design methodologies are enhancing RMC performance?
As a specialised player in Ready Mix Concrete, we have always prioritised ongoing progress in concrete mix design, ensuring that the quality requirements for a project are continuously reached. We worked hard to create sustainable concrete mixtures that reduce carbon footprints while maintaining performance standards. Eco-friendly options, such as our TUFF line of products built from recycled concrete, are IGBC Green Pro certified and have standards, strength, and other properties comparable to those made from virgin materials. We are thrilled to participate in the prestigious Mumbai Coastal Road project, for which we have provided 440 big precast concrete box culverts weighing between 30 and 35 metric tonnes. These box culverts were utilised to construct a stormwater outfall into the Arabian Sea. The box culverts were designed to endure the severe coastal environments and significant traffic loads. To contribute to sustainable development, our concrete mix design uses up to 10 percent recycled concrete mix to produce these box culverts. This consideration was factored into the design of these concrete structures in close collaboration with the relevant project consultants and authorities.
For more information, visit: https://www.godrejenterprises.com/
Cookie Consent
We use cookies to personalize your experience. By continuing to visit this website you agree to our Terms & Conditions, Privacy Policy and Cookie Policy.