Fully mobile sizer stations power the future of mining
By Staff Report | December 21, 2024 3:29 pm SHARE
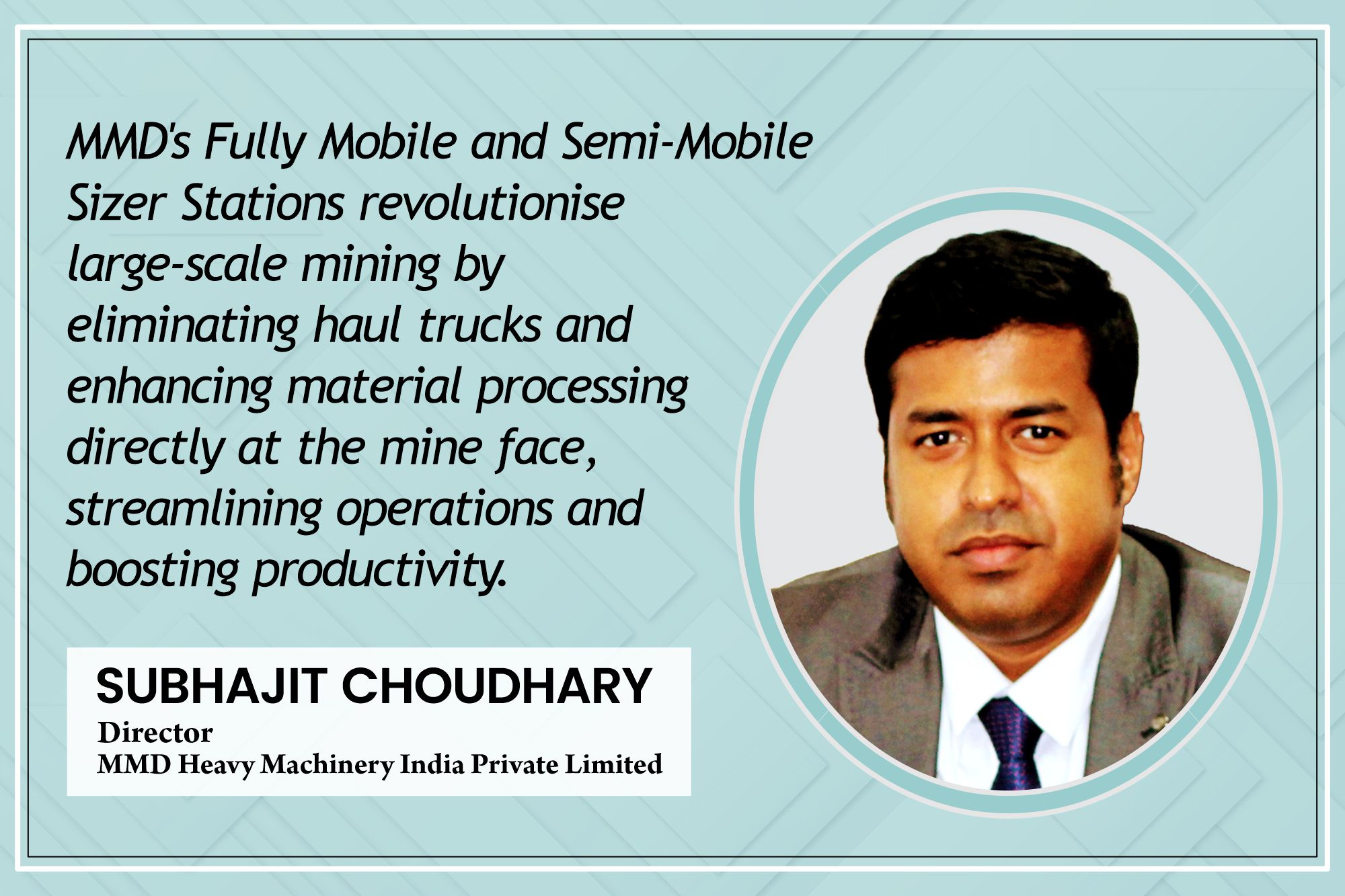
MMD’s patented Mineral Sizer technology offers compact, efficient solutions for mining challenges, solving space constraints, minimising downtime, lowering operational costs, and improving sustainability with low power consumption and minimal environmental impact.
How has MMD’s journey and innovations shaped its impact on mining and other industries?
MMD began in 1978 and initially focused on designing and building mineral processing equipment for the UK underground coal mining sector. Our breakthrough was the Twin Shaft Mineral Sizer, which stood out for its resilience and compact design. Over the years, this innovation revolutionised material handling and processing across global mining activities. To enhance its performance in tough underground environments, we developed a customised gearbox that ensures the remarkable reliability and efficiency that Sizers are known for.
While coal was our primary focus, the Sizer’s unique capabilities soon gained recognition in other industries, such as cement, metals, energy, precious stones, and waste management. Our Sizer technology addresses challenges like space constraints by integrating seamlessly into existing setups, reducing downtime, lowering operational costs, optimising power usage, and supporting sustainability goals. It helps minimise dust, controls emissions, and reduces environmental impact, aligning with global efforts to combat greenhouse gases.
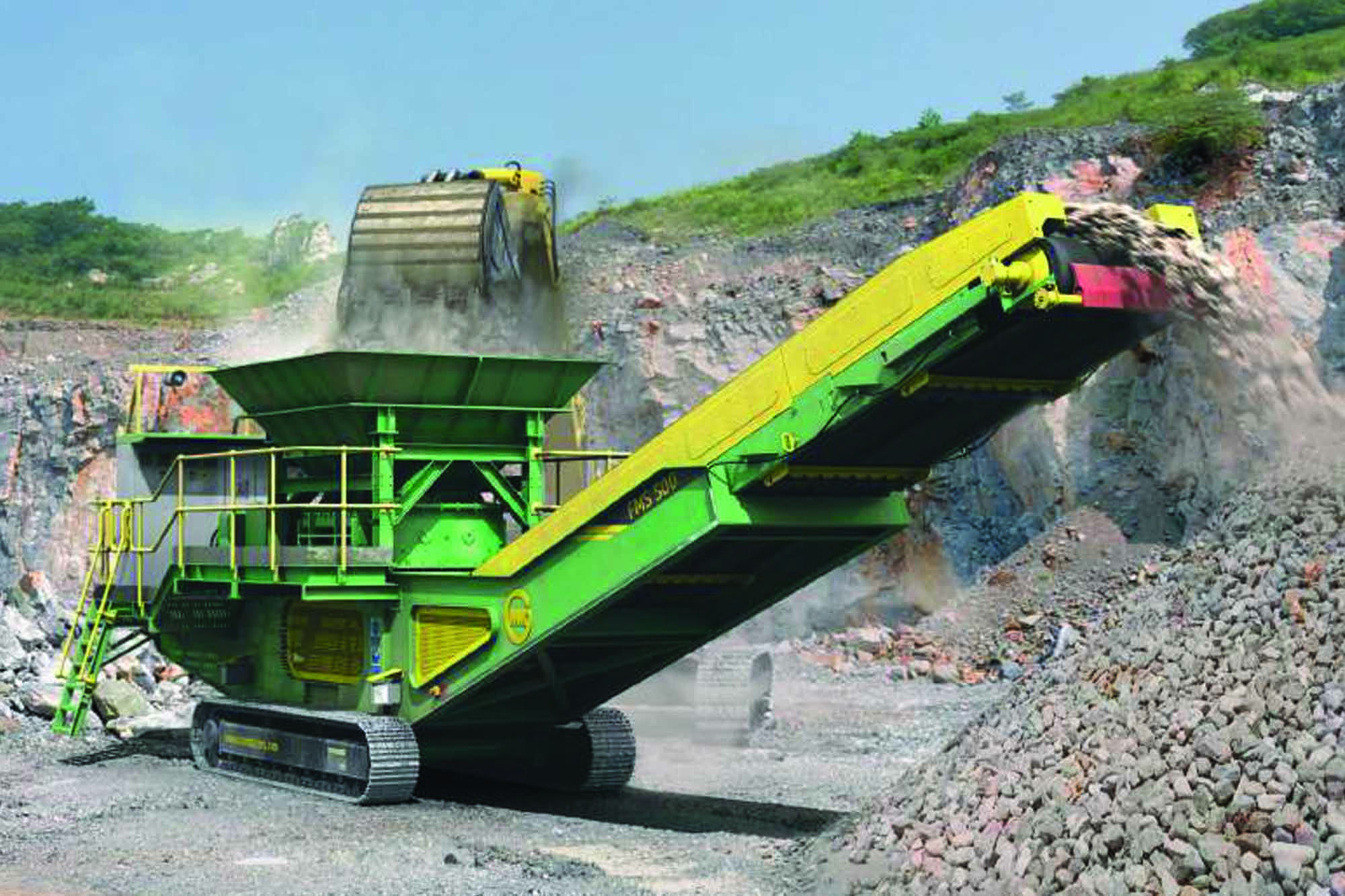
How does MMD address the growing demand for versatile extraction systems in modern mining processes?
At MMD, we prioritise adaptability to meet the evolving demands of modern mining processes. Our Sizer range is highly versatile, integrating various transport and mounting solutions to handle diverse extraction needs. For instance, wheeled units are ideal for smaller Sizers in constrained environments, while Track Modular Units, powered by diesel or electricity, offer a flexible solution for larger operations. Additionally, transportable modular setups allow seamless relocation and compatibility with different transport modes, ensuring operators can tailor the system to their specific requirements.
Our Fully Mobile IPSC system takes adaptability further by combining mining shovel flexibility with conveyor cost-efficiency. Processing material directly on the mine face removes the need for haul trucks, streamlining operations and enhancing production capacity.
What makes the Fully Mobile IPSC solution a game-changer in mining operations?
The Fully Mobile IPSC redefines mining efficiency by enabling in-pit material processing without haul trucks. This innovation processes material directly at the mine face, reducing operational complexity and wear on conveyor systems while boosting throughput. The system is designed for performance and reliability with a 175m³ hopper for direct feed, an adjustable MMD Apron Plate Feeder for precise tonnage control, and a discharge conveyor for optimised material placement.
Its compact, modular design ensures easy relocation and maintenance, while its robust build withstands harsh conditions and steep grades of up to 10%. With automation and remote operation capabilities, the IPSC enhances safety, simplifies management, and delivers unmatched flexibility, making it a cornerstone of modern, large-scale mining operations.
How does MMD help clients meet their ESG commitments with products like Fixed Sizer Stations and In-Pit Sizing and Conveying solutions?
We are committed to fostering an environmental culture in our communities, including responsible use of natural resources, emission reduction, and waste reduction. We aim to improve efficiency and employ greener energy sources in our business and products. Working with our suppliers and customers, we combine our expert knowledge with new energy-efficient technology, enabling us to build products and processes that decrease our clients’ carbon footprint.
How do MMD’s Apron Plate Feeders improve material handling efficiency and reduce downtime in challenging material conditions?
Designed to withstand impact loads and abrasive materials, they are frequently installed beneath tipping points, where their combination of dependability and durability has been shown to provide many years of trouble-free operation with minimal maintenance. The apron plates, attached to the chain, are composed of specifically rolled pieces and come in different widths to accommodate the largest volume of material that may need to be processed. These plates have overlapping edges to prevent spillage between them, and they are attached to the chains using bolts positioned between the grousers to protect the bolt heads from damage caused by the material being transported. The reduction of impact energy is important. The conveyor plates absorb the impact force, deforming within their elastic limit. The impact rails subsequently transmit the dissipated forces to the main frame construction.
How does MMD use automation and digital technologies in the Fully Mobile Surge Loader™ and Bulk Ore Sorting Systems to enhance efficiency?
The Fully Mobile Surge Loader uses cutting-edge 3D camera technology and RFID sensors to swiftly and efficiently guide trucks into position. Sensors also allow for automated start/stop delivery of material, boosting the fill factor for each vehicle. Another significant advantage is the Fully Mobile Surge Loader’s ability to load trucks with a specific desired payload precisely. These capabilities particularly piqued the customer’s interest, as they had spent the last ten years developing and implementing driverless truck fleets. Using mine automation software, a single operator may remotely deploy the Surge Loader, with instant remote control and real-time data relayed to the shovel.
Can you share examples of how your service contracts, support, and repair services help clients maximise equipment performance and lifespan?
We provide tailored service contracts to meet each customer’s specific demands, increasing availability by adopting preventative maintenance schedules and systems. Using our understanding of your equipment, we can cost-effectively restore your machine to its original state while maximising your return on investment. We have performed this type of exercise for all of our existing customers.
For more information, visit: https://www.mmdsizers.com/
Cookie Consent
We use cookies to personalize your experience. By continuing to visit this website you agree to our Terms & Conditions, Privacy Policy and Cookie Policy.