Abhijeet N Gawde, Head of Business Development & Marketing, Godrej Construction, discusses how Godrej Construction aligns with the government’s infrastructure strategies, emphasising the role of recycling in meeting the increasing demand for construction raw materials.
Could you share insights into how Godrej Construction’s services, including sustainable construction materials and environmental engineering solutions, align with the theme “Building Bharat 2024”?
Environmental stewardship is at the core of our operations. We have implemented eco-friendly production processes and energy-efficient technologies to minimise our carbon footprint. We adhere to stringent waste management protocols, recycling water and other materials to reduce waste.
The Godrej TUFF brand offers a breakthrough range of customised and environmentally conscious products in construction materials. Godrej Construction (GC) has received the ‘Green Pro’ certificate from the Indian Green Building Council (IGBC) for their RMC products such as Enviro TUFF, Xtra TUFF, Easy TUFF and other construction materials such as TUFF Blocks AAC, Recycled Concrete Blocks & Pavers making them beneficial for use in Green Buildings.
Enviro TUFF is an eco-friendly concrete mix produced by blending industrial by-products like recycled Fly Ash or Grounded Granulated Blast Furnace Slag (GGBS), which helps lower a project’s carbon footprint and improves its Green Building Rating.
Our 4 RMC plants in the Mumbai-MMR & Pune region have been commended with the ‘Green Pro’ certification by the Indian Green Building Council (IGBC), and we are the first in the RMC industry to receive this certification.
Godrej Construction has deployed Circular Economy design principles of ‘Recover, Recycle and Rebuild’ for recycling concrete debris to produce prefabricated concrete products such as building blocks, pavers, culverts, ducts, and other customised precast concrete products. Godrej Construction has set up an automated Recycled Concrete Materials (RCM) manufacturing plant at Vikhroli, Mumbai. This industrial plant manufactures concrete blocks for walls and pavers using concrete debris recycled from demolished concrete structures from building and infrastructure projects, which would otherwise end up in overflowing city landfills. By implementing circular economy principles, we have recycled over 30,000 metric tonnes of concrete debris so far.
In August 2023, GC was awarded the prestigious ‘Pioneer in Excellence Prize’ at the 9th International Best Practice Competition 2023. The event, organised by the Centre for Organisational Excellence Research, New Zealand, in partnership with the European Foundation of Quality Management EFQM, has recognised GC for its best practices in various categories.
GC’s commitment towards sustainable development, demonstrated through the practice of ‘Adopting Circular Economy Principles for Recycling Concrete Debris to Produce Precast Products’, has earned a prestigious 5-star rating.
With the government’s recent strategy for boosting infrastructure projects through the ambitious National Infrastructure Pipeline and Gati Shakti Master Plan, the demand for construction raw materials is expected to increase significantly. A large part of this upcoming demand for raw materials can be met by recycling and reuse of the C&D waste.
Urban infrastructure project sites need to collaborate with the C&D waste recycling plants within the city to manage C&D waste generated effectively. Technical problems around reusing recycled products should be solved through coordination with Project Management Consultants and relevant stakeholders working on the project to identify potential applications for recycled products. The government mandate to use recycled products in infrastructure projects will increase the number of project-based C&D waste recycling facilities.
Godrej Construction is one of the first in the RMC industry to switch to 100% green energy. Our RMC and Recycled Concrete Materials (RCM) plants in Vikhroli West, Mumbai, are powered by 100% Green Energy. Similarly, the common areas within Godrej IT Park – 02 GBD, Grade A+ Commercial building at Vikhroli, Mumbai, are also powered by 100 percent Green Energy.
Recently, the Godrej IT Park – 02 GBD, Grade A+, LEED Platinum rated by IGBC Commercial Office building at Vikhroli, Mumbai, won the National Award for Excellence in the Energy Management 2023 – Building Sector, Excellent Energy Efficient Unit, by the CII (Confederation of Indian Industry).
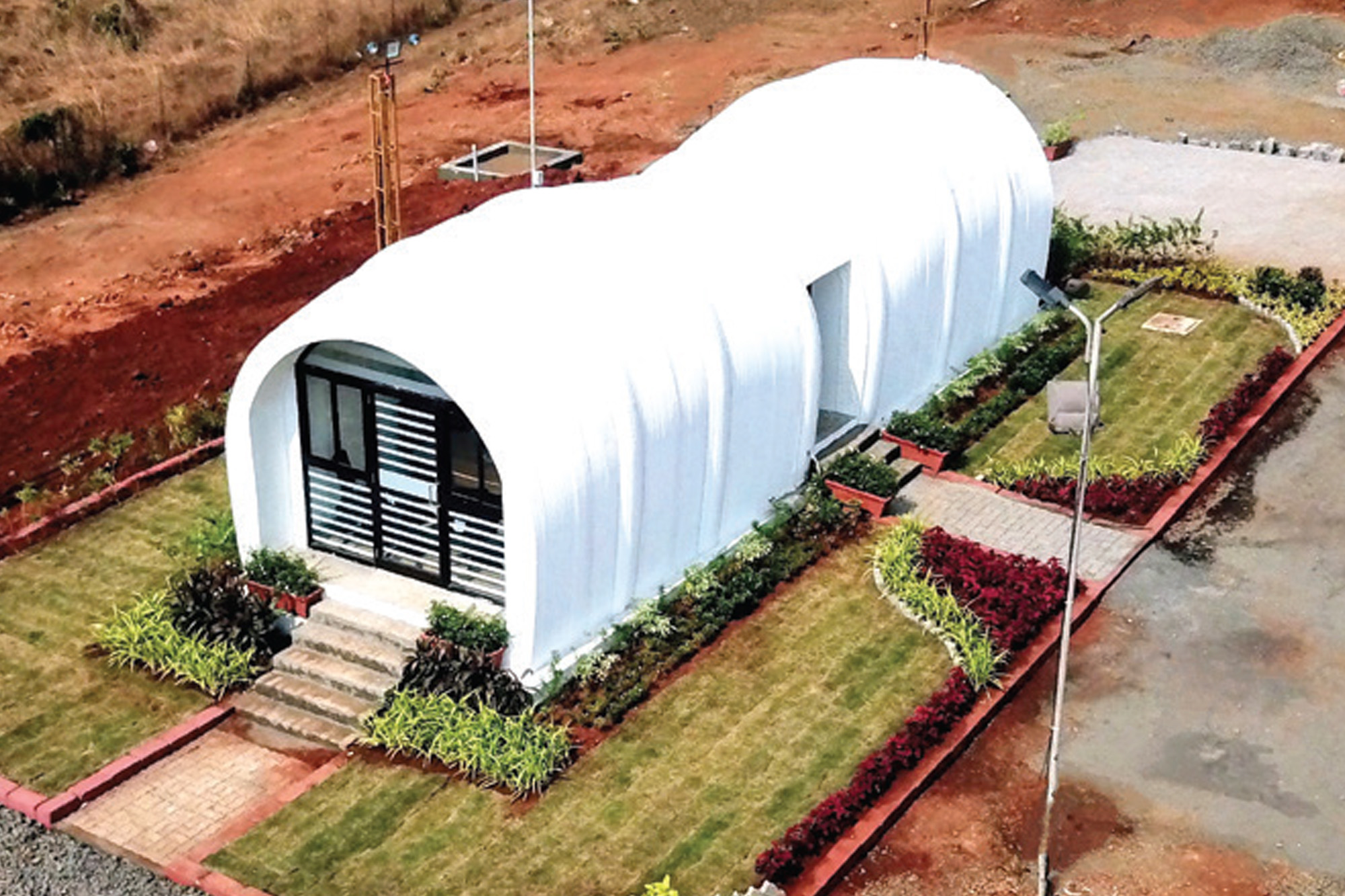
Godrej Construction adopts a lean manufacturing culture. How does this culture contribute to eliminating waste, creating better value, and ensuring faster delivery?
Godrej Construction (GC) started its Lean journey in 2011 by becoming one of the first Charter Member companies of ILCE, where it got exposure to Lean practices by collaborating with many like-minded leading Construction companies such as Shapoorji, L&T, Afcons, Tata, Arcop, URC, etc and IIT-M as its knowledge partner. For GC, it has been a steady, progressive journey with increasing exposure to the Lean philosophy by implementing lean tools at project sites to initialising lean culture across the organisation by involving its cross-functional teams of projects, design, engineering, procurement, and safety across projects.
Integrating Lean Construction techniques has significantly contributed to the successful execution and commissioning of our projects at GC. This approach has fostered improved stakeholder relationships, facilitated a smoother process flow for efficient project delivery, and enabled better monitoring and control through a “pull” mechanism. Additionally, it has allowed for early identification of potential delays, constraints, and non-value-adding activities, resulting in a superior customer experience, enhanced employee and partner satisfaction, and promoted an inclusive culture. The implementation of waste minimisation, 5S practices, reduced rework, and enhanced safety through technology further underscores the positive impact of Lean Construction on our business operations.
Looking ahead, GC is committed to reinforcing the Lean Culture in our business operations through various initiatives. These include the integration of Lean principles in the Conceptual Design stage of projects through collaboration with our Supply Chain, providing 100 training to all GC employees with Lean Certification programs through NPTEL & CII, executing Lean Transformation Projects, driving Lean in Innovation by reducing Customer Complaints, and improving efficiency at all sites through a robust network of Lean Champions. These initiatives aim not only to sustain the positive outcomes achieved through Lean Construction but also to enhance our overall operational effectiveness continually.
How does Godrej Construction leverage technological innovations in construction projects, such as automation or smart technologies?
Construction is the biggest industry in the world. As per McKinsey research, the ecosystem represents 13 percent of global GDP, but construction has seen a meagre productivity growth of 1 per cent annually for the past two decades. Time and cost overruns are the norm. Digitalisation is lower than in nearly any other industry. Regular time and budget overruns hamper customer satisfaction. As per the analysis done by McKinsey, it is found that construction projects typically take 20 per cent longer to finish than scheduled.
Godrej Construction recently took up an innovative project to drive a culture towards integrating project planning and delivery to speed up the construction of an office project.
With this objective, Godrej Construction unveiled ‘The Cocoon’, a 48 sq.m—3D printed office at Khalapur, which was installed and fully functional in under 40 hours. The structure, printed at the Godrej & Boyce Campus in Vikhroli, Mumbai, using innovative 3D Construction Printing (3DCP) Technology, was installed and made fully functional within an impressive 40-hour timeframe. This structure, ‘The Cocoon,’, was created as prefabricated modules using innovative 3D Construction Printing (3DCP) Technology.
The modular office is characterised by its namesake, and the unique structure incorporates advanced engineering techniques integrated with a modular construction process. The design of ‘The Cocoon’ is one organic continuum where the wall and ceiling are not separate components but merge. The office is thoughtfully designed to explore the potential of 3DCP technology, showcasing design flexibility through an unconventional curvilinear elliptical design. The entire layout is column-free, offering maximum usable office space, installed with a prefabricated toilet unit.
The project construction included complete installation of 3D printed modules, civil works, waterproofing, flooring, external & internal painting, electrical works, lighting, AC installation, plumbing, drainage & sanitation fixtures, office furniture and landscaping in under 40 hours.
The office was created using a sustainable concrete mix design comprising 20% Recycled Concrete Aggregates (RCA) sourced from concrete waste debris, recycled at the Godrej & Boyce Recycled Recycled Concrete Materials manufacturing plant at Vikhroli, Mumbai.
Thus demonstrating the speed at which the construction processes can be completed while ensuring sustainability. This achievement marks a significant stride forward in construction practices, emphasising cost-efficiency, sustainability, time effectiveness, and innovation that redefine industry standards.
Construction of ‘The Cocoon’ is enabled through effective team collaboration integrated with good project planning using tools like Building Information Modelling (BIM), Lean Construction methods and 3D Construction Printing.
Cookie Consent
We use cookies to personalize your experience. By continuing to visit this website you agree to our Terms & Conditions, Privacy Policy and Cookie Policy.